Manufacturing involves assembling a product, but costs, time, and quality are also important. All of these depend on the bill of materials (BOM), which lists the raw materials (parts, components) needed to create the final product.
Using a BOM helps improve supply chain efficiency, minimizes production errors, and helps manage resources effectively, serving as the vital connection between design and delivering the final product to the customer.
With this article, you will get to know the meaning of BOM, its types, and obtain free templates to prepare BOM right away. We will also discuss the various software you can choose from to create BOM. So let’s get started.
- What is a Bill of Materials (BOM)?
- Why is BOM Important?
- Who Should Use the Bill of Materials Format?
- Types of Bills of Materials
- Benefits of BOM for Your Business
- Example of Bill of Materials
- Free Bill of Materials Templates
- How to make BOM? Step‑By‑Step Instructions Using Kladana
- Bill of Materials Software
- Frequently Asked Questions on Bill of Materials
💻 Free Webinar Recording Available!
Recently, we hosted the webinar Automation for Manufacturing Companies: Where to Begin, featuring Aleksandra Brovchuk, Kladana’s Director in India, and Uday Sharma, Senior Customer Support Executive.
They shared the insights on efficiently managing inventory, warehousing, sales, and production — all within a single app, without requiring expensive implementations or specialized skills.
Key topics covered included:
- 6 common production management challenges and solutions
- 5 steps to seamlessly implement manufacturing software
- How Kladana ERP can benefit manufacturing companies
Receive webinar recording, presentation slides, a promo code for an extended 30‑day trial, and additional content via email for free.
What is a Bill of Materials (BOM)?
A Bill of Materials (BOM) is a comprehensive inventory list that forms the backbone of a manufacturing unit. It includes details of all the materials, components, and assemblies used to create a final product. This means that every component, subassembly, and raw material required to bring a product to life is included in the BOM.
Also, it is about more than what goes into your product. Ideally, a BOM will also include details of how much of each item is needed so that you have enough to complete the job without wasting anything. Moreover, a BOM is also necessary for compliance since industry regulations play a major role in maintaining efficient and cost-effective operations.
Read‑alikes
Top 23 Manufacturing Management Software in 2024
Managing Production in a Small Manufacturing Company: Planning, Control, and Profit Calculation
Full Guide to MRP Solutions: Core Features, Advantages and Pitfalls
Why is BOM Important?
BOM serves as a foundation for undertaking successful product manufacturing since it acts as a central reference point. Throughout the product life cycle, it guides everyone in the product department on how much each component is required, where to source it, and how it fits within the larger assembly.
Manufacturers are prone to inefficiencies, increased costs, and potential supply chain disruptions with precise BOM management.
Here’s why BOM is essential:
- Streamlines Inventory Management: A clear bill of materials helps manufacturers manage inventory more effectively, reducing waste and avoiding shortages.
- Supply Chain Resilience: Manufacturers can leverage BOM to identify alternative components, reducing their dependence on a single supplier.
- Cost Control: With BOM inventory management, you get a transparent view of material costs and can calculate the exact costs of materials and components to budget your manufacturing.
- Enhances Communication: BOM ensures that all teams involved in the production process are aligned so that there are no misunderstandings and delays.
- Improves Supply Chain Efficiency: Detailed BOM paves the way for better supplier coordination to make all the necessary components available on time.
- New Product Development: Leverage BOM to speed up the introduction of new products using the existing components.
Who Should Use the Bill of Materials Format?
At its core, BOMs tend to guide the production process, but they have a larger impact beyond the assembly line. Why do we say this?
Because BOMs involve every other team in the product lifecycle wherein they can understand the product’s composition and requirements. The result is highly efficient collaboration and decision-making throughout the production.
Below are some direct users of BOMs.
- Engineers and Designers: In a typical factory setup, both professionals leverage BOMs for the product design and development phases. With BOMs, they can specify and document every material and component required to build the product.
- Production Managers: They delegate tasks to respective employees and production line workers responsible for producing the finished product as per the BOM. If they outsource production to subcontractors, BOM helps manufacture the finished products as per the specifications.
- Procurement Teams: Help procurement leads order the correct materials and components while ensuring they meet the document’s specifications.
- Inventory Controllers: They use bill of materials to track stock levels, prevent shortage, and optimize inventory management.
- Sales and Marketing Professionals: Managers and executives of both these teams use BOM to understand product variations, accurately quote prices, and accentuate key features to customers.
- Cost Analysts: These professionals calculate the total cost of the materials and components using BOMs, which feed the budgeting and pricing strategies.
- Quality Assurance Teams: The QA teams often access the BOM to check whether the final product meets all specifications and quality standards.
Types of Bills of Materials
Different types of BOMs are available to suit the specific requirements of different stages in the product lifecycle and across various departments. Knowing and understanding these different types of BOMs helps leverage them to their full potential and optimize product development, manufacturing, sales, and support.
Let’s explore different types of BOMs in detail.
Engineering BOM (EBOM)
The Engineering BOM is like a product’s blueprint that defines the design and structure of the finished product. EBOM is often based on a detailed CAD (computer-aided design) drawing, making it an essential BOM in the product design phase.
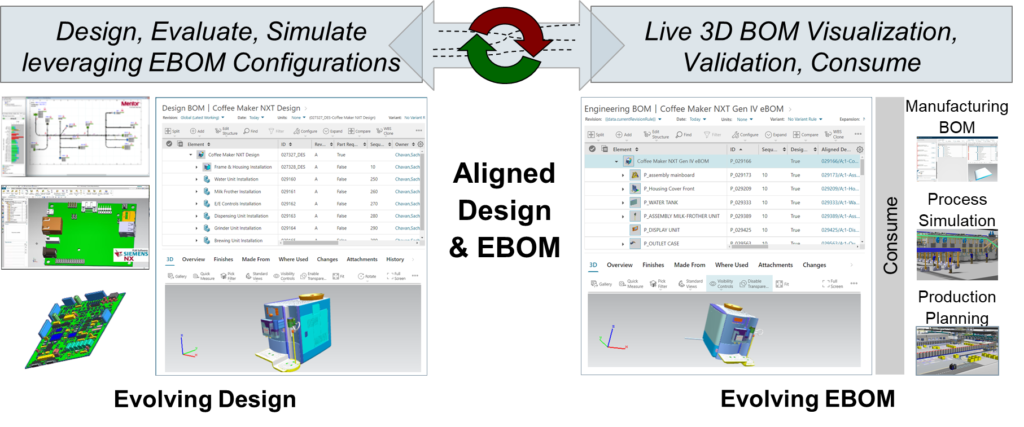
EBOMs are intended to help engineers and designers outline exactly what components are needed as a product goes through its lifecycle. During this time, multiple EBOMs are created to reflect design changes and improvements.
Manufacturing BOM (MBOM)
MBOM contains a list of all the parts, assemblies, and materials necessary in an entire production lifecycle — from manufacturing a product to packaging sent to the customer. This is a critical bill that requires the use of manufacturing management software for production managers and assembly teams. It ensures that everything is accounted for during manufacturing.
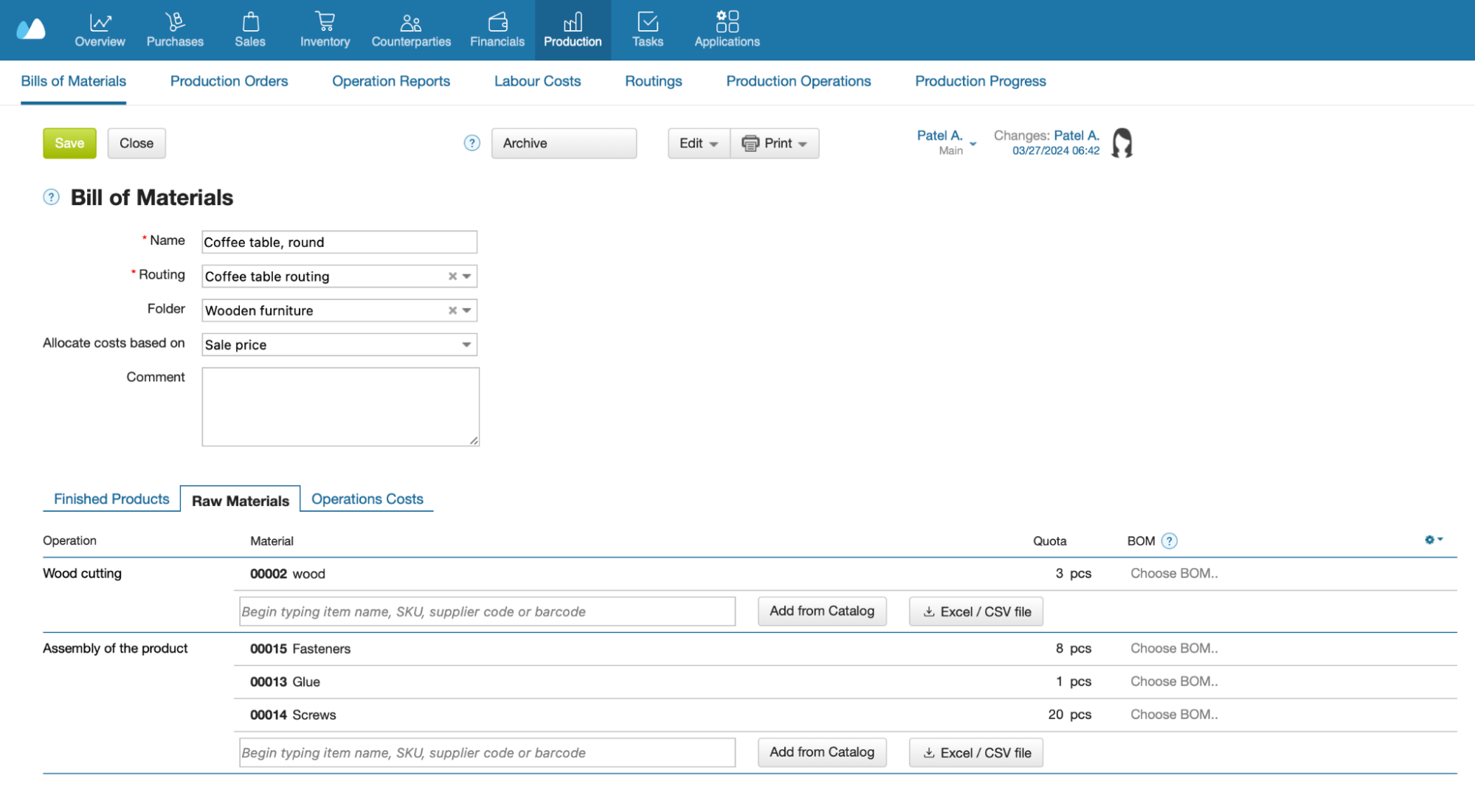
Configurable BOM (cBOM)
This BOM is particularly useful if a product has multiple iterations to manufacture and assemble (for instance, different colors, sizes, or features). It lets you define a base model and quickly create variations based on customer preferences to streamline the ordering and production process.
Modular BOM
You’d go with a modular BOM if your business needs to produce complex products with numerous subassemblies. This BOM helps break down the product into manageable chunks, making it easier to track changes and updates without reworking the entire BOM every time.
Sales BOM (SBOM)
The Sales BOM is tailored to specific customer orders and outlines the components and materials required to fulfill a particular sales order, including any special packaging or customization details. It is a necessary BOM for sales teams to help ensure that customer-specific requirements are met accurately and efficiently.
Service BOM
The Service BOM is the go-to document when repairing or servicing a product. It holds details of all the parts, components, and instructions required for maintenance and repairs. Service teams can use it to perform their tasks effectively since this BOM possesses details of the exact components used during repairs. In turn, this helps your teams maintain product integrity and performance.
Single‑Level BOM
The Single‑Level BOM provides a simplistic view of a product’s structure. It lists only the primary components required to build the product without diving into sub-assembly details. This BOM is highly useful for less complex products without a detailed breakdown.
Multi‑Level BOM
Unlike a single‑level BOM, a Multi‑Level BOM offers a hierarchical view of the product’s structure, including all components and subassemblies. This BOM shows the relationships between each part to provide a comprehensive understanding of how everything fits together. Hence, manufacturing units use Multi‑Level BOM to manage complex products with multiple layers of components.
We, in Kladana, offer BoMs also, including multi‑level ones.
Assembly BOM
Use assembly BOM when you need a bill highlighting a specific sub assembly within a larger product. It contains details of components and instructions required to build a particular subassembly, including the order in which components should be put together.
Businesses leverage this type of BOM to guide assembly line workers and make sure that the product is built correctly and efficiently.
Software BOM (SBOM)
An SBOM is increasingly important in today’s digital world. The SBOM will list all the software components and dependencies within a software product to help in security and vulnerability assessments.
Repair BOM
You’d choose a repair BOM to track repair operations since it features all the components and parts needed to repair a product. This also contains detailed instructions for the repair process, which are essential for maintenance teams and service departments. The end goal is to ascertain and correct the repairs being conducted efficiently.
Packaging BOM
The PackagingBOM contains the materials and components required for packaging the final product.
Template BOM
The Template BOM is a predefined BOM acting as a starting point for creating new BOMs. Businesses that manufacture similar products often use a Template BOM, which allows them to quickly generate BOMs for new products by modifying an existing template.
Benefits of BOM for Your Business
Your Bill of Materials is not just a list of spare parts and machinery components but a vital asset that drives every aspect of production. In this section, we’ll delve into the major advantages of using a BOM.
Enhanced Cost Control and Budgeting
A BOM also becomes your cost‑cutting ally since it helps highlight potential savings opportunities. Like, it gives you a pause to think of and find a cheaper supplier for those screws or a more efficient material for that casing. The BOM lays it out so you can make informed choices to boost your bottom line.
Optimized Inventory Management
Use BOM to maintain optimal inventory levels. It helps accurately specify the quantities needed, reducing the risk of stockouts or overstocking. This results in an improved bill of materials inventory management that helps control costs.
Streamlined Production Processes
BOM provides a detailed map of the production process, ensuring that every step is laid out. This will help drive clarity and minimize errors, rework, and frustrating production bottlenecks that may cost time and money.
Improved Supply Chain Resilience
Use BOM as your alert system, warning your supply chain by pinpointing potential trouble spots before they become a full‑blown crisis. BOMs can flag single‑source dependencies, allowing you to find alternative suppliers or parts so you’re not left high and dry if something goes wrong.
Facilitates Accurate Product Lifecycle Management (PLM)
Bill of Materials shows what is in your product and highlights details on where those parts come from. It helps map a supply chain, highlighting potential bottlenecks or vulnerabilities to drive effective product lifecycle management and track every component used in a product.
Facilitated Collaboration
Let BOM be a focal point, like a common language, that helps bring together engineers, production managers, procurement teams, and quality control experts. As a result, no single department works in silo since BOM creates a shared understanding of what’s needed to bring a product to life.
Compliance and Regulatory Adherence
Manufacturing businesses must follow the rules to remain compliant. Even here, BOM comes in handy since it serves as a checklist that verifies that every component and material you use has the right certifications and meets the necessary standards.
Reduced Environmental Impact
Consumers are becoming more environmentally conscious and moving towards sustainable products. Use BOM as your green guide, which sheds light on areas where eco‑friendly alternatives might be feasible to minimize your product’s environmental impact.
Example of Bill of Materials
Now that we know what BOM is and its types, let’s examine real‑life examples of how a Bill of Materials appears.
In this, we’ll understand by example how a BOM looks and navigate through a set of main fields that form the main component of BOM.
Let’s check out some BOMs
-
A BOM for raw material where each fruit/vegetable is mentioned along with the order and inventory details.
Source: © Indzara -
Next, below is a more comprehensive BOM with different fields, including category, BOM notes, etc.
Source: © Arena Solutions
Let’s now explore some of the main fields in the BOM document.
- BOM Level: This level highlights the hierarchical position of a component within the overall product structure. It’s a table of contents in the BOM that helps navigate its various levels of complexity.
- Part Number: This unique identifier for each component helps ensure precision and avoids confusion when dealing with multiple parts that may look similar.
- Part Name: Suggests the component’s name, making it easy to recognize across different teams and departments.
- Procurement Type: Specifies how each part is acquired. Whether it’s purchased off‑the‑shelf or custom-made to specification.
- Reference Designators: Useful for products that have printed circuit board assemblies (PCBAs) where reference designators indicate where each part fits on the board.
- BOM Notes: A catch‑all for any additional information that doesn’t fit neatly into other categories.
- Phase: Help track the lifecycle stage of each component, be it in production, under development, or even obsolete. This will help teams manage inventory, plan new product introductions, and make informed decisions about product upgrades or obsolescence.
- Description: A concise description of the component, including its function or purpose within the product. This helps to understand the role of each component and facilitates communication across teams.
- Manufacturer/Supplier: This option lets you identify the preferred or approved source for each component. It aids procurement teams in sourcing the right parts from reliable suppliers.
- Lead Time: This section suggests the estimated time required to procure or manufacture each component, which is crucial for production planning and scheduling.
- Cost: Shows the unit cost of each component, enabling cost estimation, budgeting, and analysis of the product’s overall cost structure.
- Revision: This tracker tracks the BOM’s version or revision history, helping to easily identify changes so that everyone works with the latest information.
- Custom Fields: Depending on the specific industry or product, BOMs can be customized with additional fields to capture relevant data like material specifications, regulatory compliance information, or environmental impact data.
Learn how to run a manufacturing business in Kladana. Plan your production operations, manage supplies and inventory, calculate cost of goods, and monitor employees activity.
Free Bill of Materials Templates
To help you get started with preparing the Bill of Materials, we’ve compiled some formats.
Choose your preferred format and download or make a copy of the BOM template. Only in this case you’ll be able to edit it.
BOM Template in Excel (.xls) Format
Free download BOM template that helps with raw material inventory management in Excel format. You can paste your company logo, enter details of the bill, and edit it according to your branding style.
Single Level BOM Template
Multi Level BOM Template
BOM Template in MS Word (.dotx) Format
Click the link below to download the Free MS Word Bill of Material template. Use it to edit and enter the details in the shared BOM.
BOM Template in PDF (.pdf) Format
Below is the free BOM template in PDF for the download. You can use it to enter the necessary details as required.
BOM Template in Google Sheets
This is the link for you to access the free BOM template in Google Docs format.
Single Level BOM Template
Multi Level BOM Template
BOM Template in Google Docs
Straightaway started editing this free bill of materials (BOM) template in Google Docs. Just log in to Google Docs and start preparing BOM.
How to make BOM? Step‑By‑Step Instructions Using Kladana
Let’s now drill down some of the key steps involved in creating a Bill of Materials with the help of Kladana.
Step1: Navigate to the Production > BOM
Login to Kladana, and from the top main menu, select Production.

A sub‑menu will open. From there, choose Bill of Materials.
Step 2: Create a BOM
Next, you’ll see an option to start creating BOM.
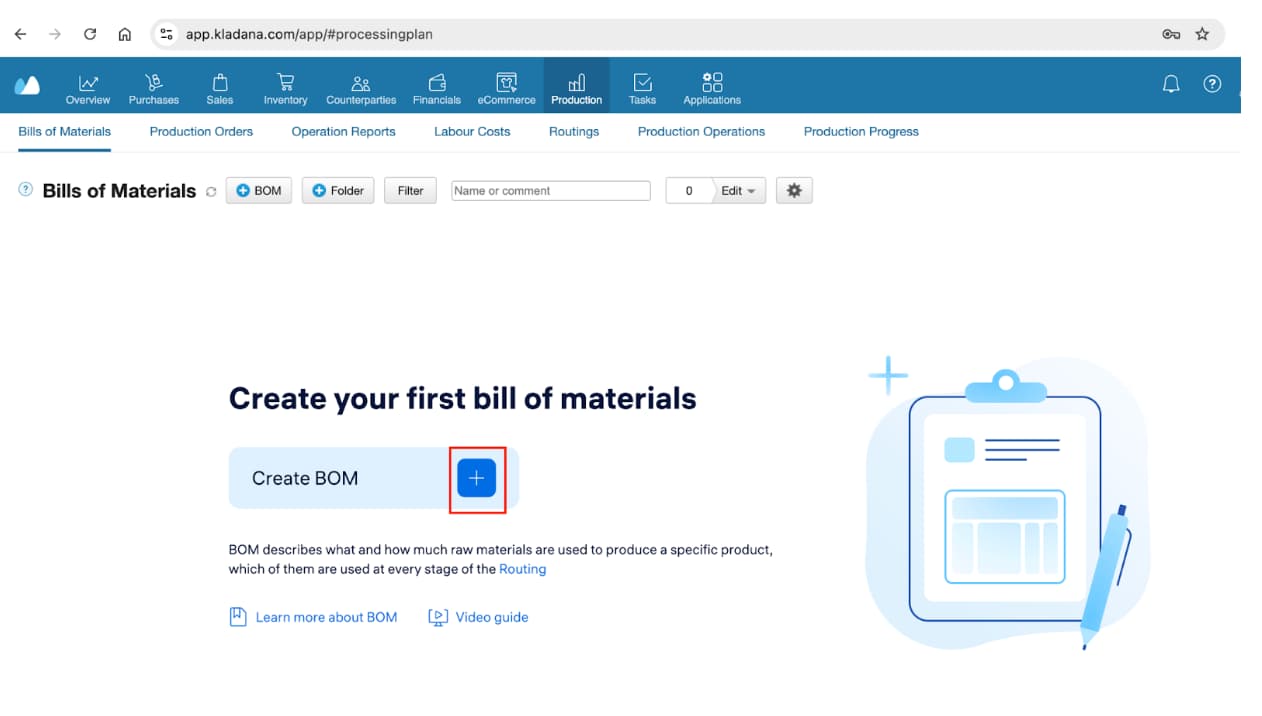
Click the ‘+’ sign to enter BOM build mode.
Step 3: Add Details
Enter the name of the BOM, select routing, and choose the BOM folder. Routing is the sequence of production operations that must be completed to produce a finished product. You can also opt to add a comment on that particular BOM.
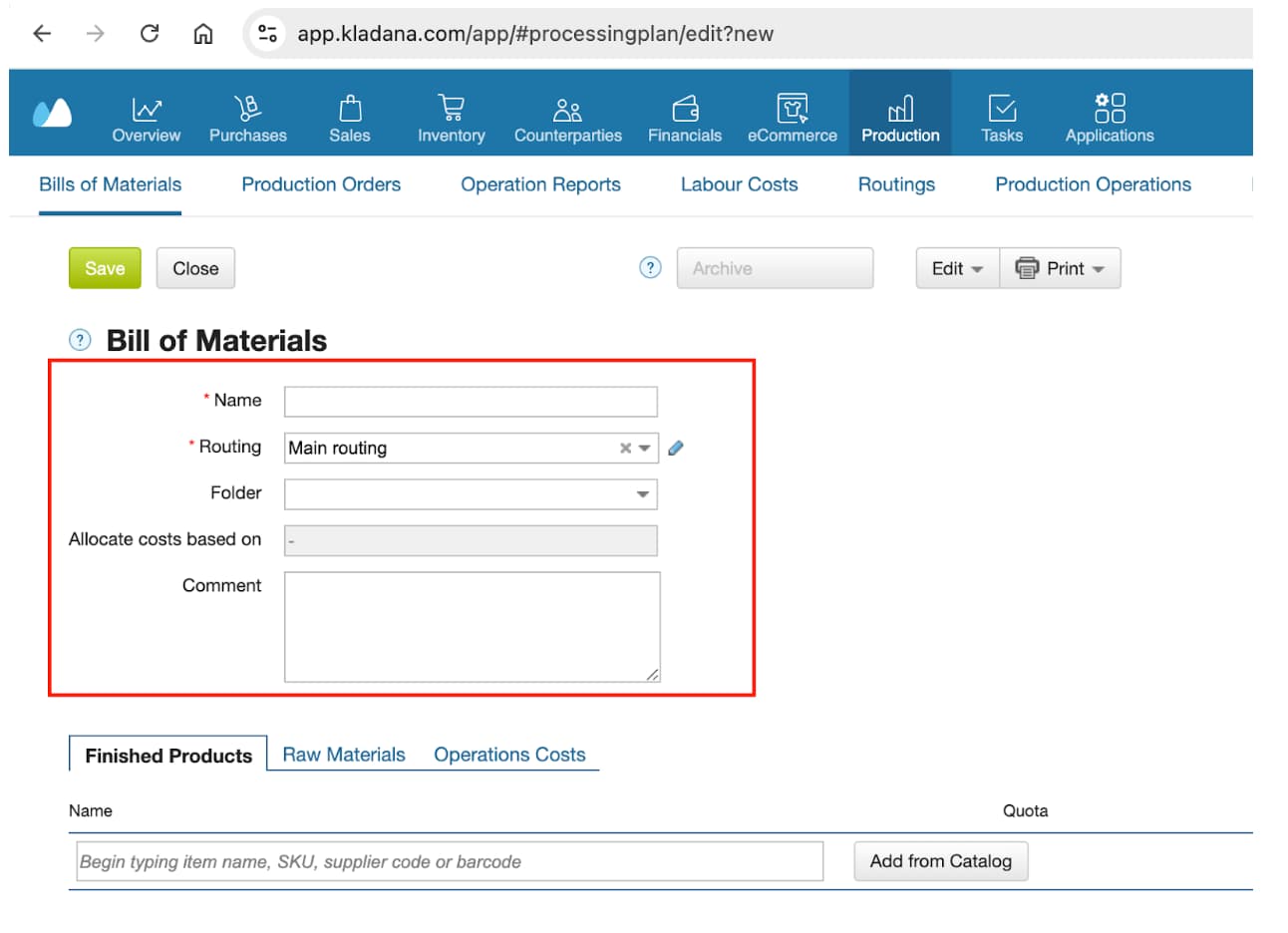
Step 4: Choose Expenditure Type
So, is the BOM for finished products, raw materials, or operations costs like machine maintenance? Each of the options will require you to add details as follows.
-
Finished Products
Choose this, and you’ll be able to search for the finished products for which BOM needs to be generated.
Also, you can choose the Add from Catalog option if you need to add a product that is not entered in the inventory.
-
Raw Materials
Add raw materials that are needed for finished goods production.
Here, you can again choose to navigate and add from the catalog or import from an external Excel/CSV file.
-
Operations Cost
In order to keep track of operational costs, use this option and add cost for operations and labor while mentioning the standard hour.
Step 5: Save the BOM
Lastly, save the BOM you created after entering the necessary details.
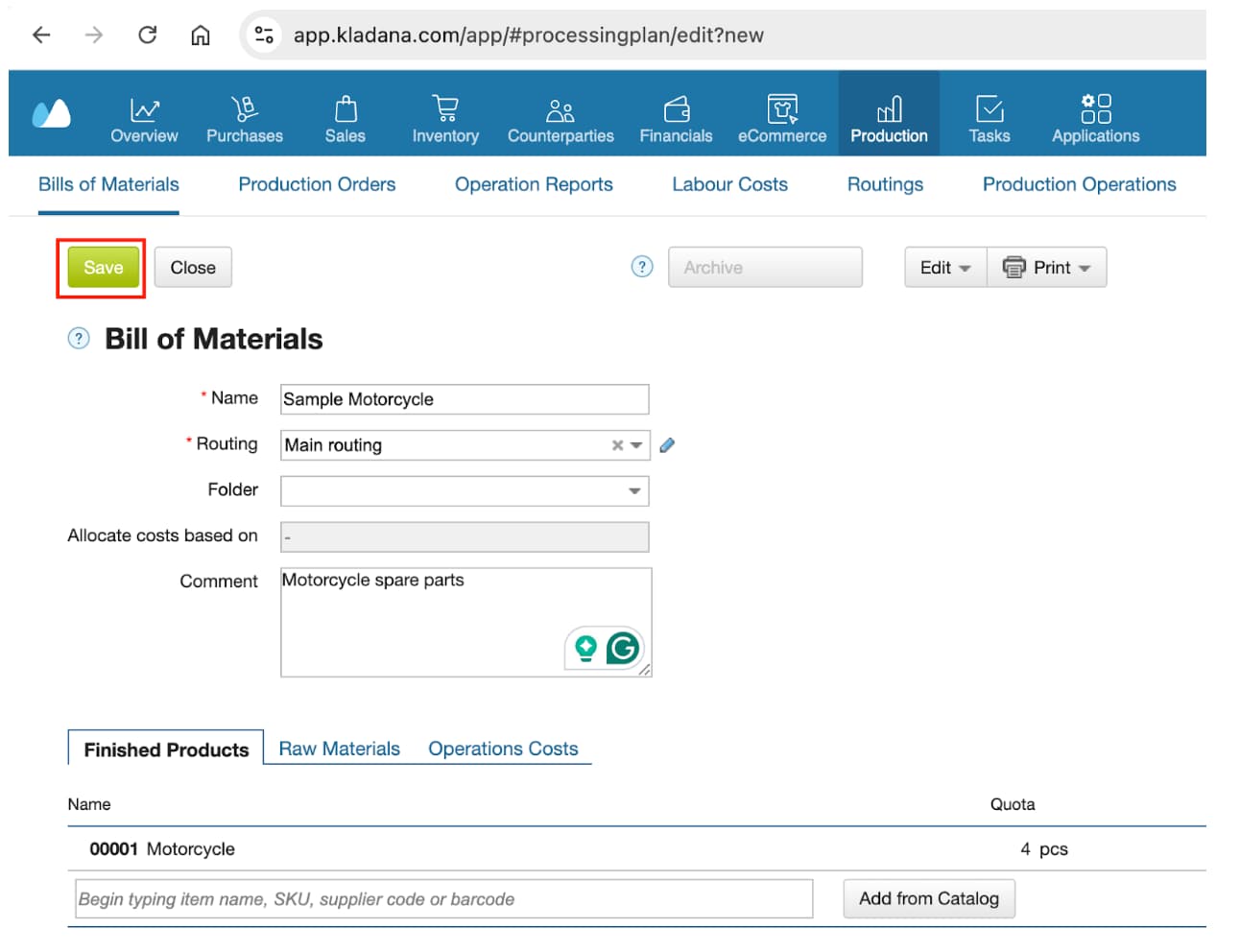
Click on the Save button, and you should be able to see the text: BOM created.
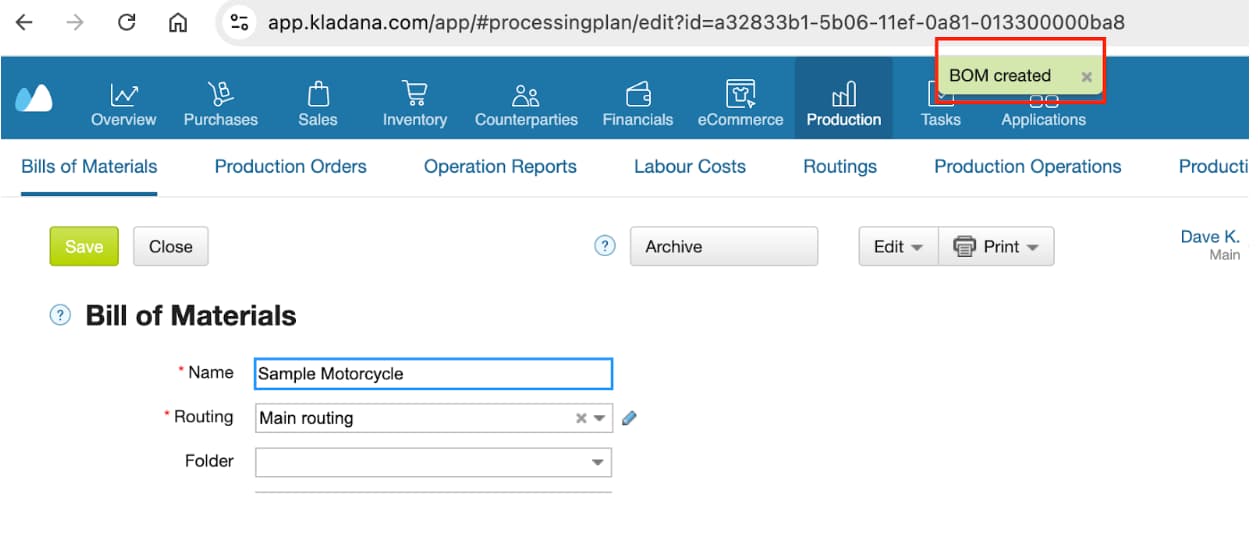
Step 6. Check The BOM Entry
Finally, you can click on the close option, and you’ll then be able to see the entry you created in a BOM.
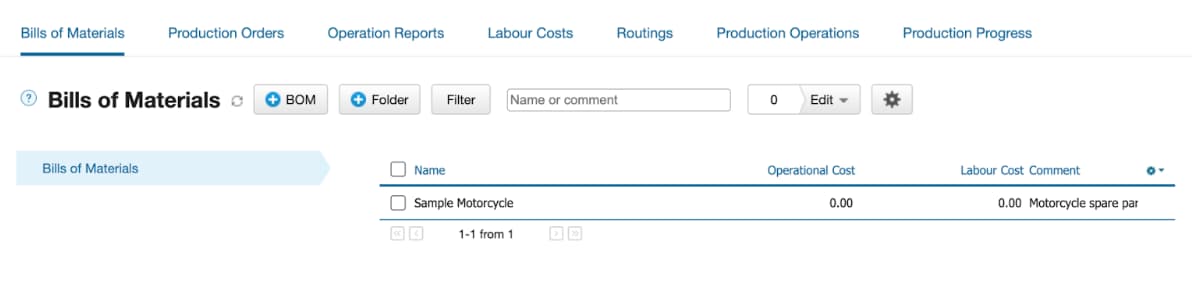
Moreover, you can also choose the Filter and Edit buttons to find and bulk edit your BOM, respectively.
To explore Kladana in‑depth, browse through our video tutorials and streamline your operations:
Use Kladana to prepare and track your BOM, helping you streamline production, minimize downtime, and reduce costs.
We have our own BOM template. Register in Kladana, then go to Production → BoM → Print → Template Settings → BoM Download
Bill of Materials Software
From the above example, we learned how to use the software Kladana to create a BOM. Also, there are other software programs that you can use to create BOM.
Here’s a quick overview comparing the available BOM software with Kladana, which should help you make the right choice.
Software | Features | Ratings | Pricing (USA) | Ideal for Business Size |
Kladana |
|
5/5 |
Starts at $563/year |
Small to Medium Businesses |
Arena PLM |
|
4.3/5 |
Custom pricing |
Medium to Large Enterprises |
OpenBOM |
|
4.1/5 |
$900/Year /month (per user) |
Small to Medium Businesses |
Odoo MRP |
|
4.2/5 |
Starts at $300/year (per user) |
Small to Large Enterprises |
Upchain (By Autodesk) |
|
4.0/5 |
Custom pricing |
Medium to Large Enterprises |
Sage 100cloud |
|
4.2/5 |
Custom pricing |
Small to Medium Businesses |
MRPeasy |
|
4.5/5 |
Starts at $828/year (per user) |
Small to Medium Businesses |
Fishbowl Manufacturing |
|
4.2/5 |
Custom Pricing |
Small to Medium Businesses |
SAP BOM Management |
|
4.2/5 |
Custom Pricing |
Large Enterprises |
When choosing the right software to help you create BOM, it is ideal to understand your business needs, size, and scope of further scalability.
Try Out the Easiest Manufacturing Process Management Software
→ Manage multi‑level BOM with ease
→ Create production orders straight from BOM
→ Outsource sub‑contracts to vendors seamlessly
→ Access cloud software without downloads
→ Forever free plan for basic features
Frequently Asked Questions on Bill of Materials
Having various questions when introducing your first or a new inventory management technique is normal. Here are some of the most common BOM questions you may have.
Can a BOM be used for service and maintenance?
Yes, you can use a service BOM that specifically lists the components, parts, and instructions required for servicing or repairing a product. This helps maintenance teams identify the correct components and perform effective repairs.
How does a BOM help new product development?
A BOM can expedite new product development by allowing the reuse of existing components or subassemblies from previous products, saving time and resources.
Can a BOM help in cost reduction?
Definitely! With BOM, you get transparency into material costs, which allows for the analysis of component pricing. In turn, this reveals opportunities for cost reduction through supplier negotiations, material substitutions, or design optimizations.
Is a BOM only applicable to physical products?
No, BOMs are also applicable to software products. A Software BOM (SBOM) lists the software components, libraries, and dependencies within a software product that help in security assessments and license compliance.
Can I use BOM for service and maintenance?
Definitely! You can use a service BOM that possess the ability to list all components, parts, and instructions needed to serve or repair a product. This help maintenance teams identify the correct components and perform effective repairs.
How often should I update BOM?
You shall update BOMs whenever there is a change to the product design, materials, or manufacturing process so that they are accurate and reflect the current state of the product.
How does a BOM help new product development?
A BOM can expedite new product development as it enables reuse of existing components or subassemblies from previous products, resulting in time and resource saving.
What are some common challenges in BOM management?
It becomes difficult to maintain the accuracy and consistency of BOMs across different versions. You need to manage these changes effectively to ensure data integrity as production evolves.
How often should I update BOM?
A BOM will need an update in case of a change in the product design, materials, or manufacturing process so as to accurately reflect the current state of the product.
How does a BOM contribute to product compliance and regulatory requirements?
With BOM, you can track all the materials and components that are used in the product. You can use these details to showcase compliance with industry regulations like environmental standards, etc. to avoid potential legal issues and penalties.