If you are in the middle of choosing proper production management software, go directly to our top 23 solutions. Use the comparison table to find what is best for you. In case you want to learn more about the pitfalls of manufacturing software implementation & usage, hidden costs in the pricing plans, and other vital data, read this article.
- Why do Businesses Need Manufacturing Software?
- How Does it Work?
- What Are the 6 Benefits of Manufacturing Software?
- What 6 Industries Use Manufacturing Software Mainly?
- What Are the 6 Main Types of Manufacturing Software?
- How Much Does it Cost?
- Top 23 Manufacturing Management Software 2025 — Compare All Features
- Best Production Management Solutions
- Frequently Asked Questions on Manufacturing Software
💻 Free Webinar Recording Available!
Recently, we hosted the webinar Automation for Manufacturing Companies: Where to Begin, featuring Aleksandra Brovchuk, Kladana’s Director in India, and Uday Sharma, Senior Customer Support Executive.
They shared the insights on efficiently managing inventory, warehousing, sales, and production — all within a single app, without requiring expensive implementations or specialized skills.
Key topics covered included:
- 6 common production management challenges and solutions
- 5 steps to seamlessly implement manufacturing software
- How Kladana ERP can benefit manufacturing companies
Receive webinar recording, presentation slides, a promo code for an extended 30‑day trial, and additional content via email for free.
Why do Businesses Need Manufacturing Software?
Manufacturing software allows entrepreneurs to digitize & automate production routines. Say, a beginner manufacturer launches their production. While purchasing raw materials and creating BOMs, they use Excel sheets and print them for the managers. If some printouts are lost, or fields are incorrectly filled in, the mistakes are unavoidable.
While executing a production order, thorough calculations are not being done, and stage completion is not being marked. So, nobody knows how much finished goods were actually produced, what the amount of scrap & by-products is, who performed particular production operations, and what the unit cost is.
Overall, a startup manufacturing company can exist without proper software only at the very beginning. Later, all the processes must be managed in the cloud, and manual labour must be minimized in order to avoid crucial mistakes.
An average manufacturing solution covers the following day-to-day routines:
- Planning & purchasing — inventory & warehousing modules are a must
- Execution — BOMs, production operations, routings, production orders & reports, WIP, scheduling
- Analytics — operational, labour costs & the unit cost, profitability, employee productivity
- Quality check — for engineers to control the quality of produced items
- Equipment maintenance & tooling
How Does it Work?
As a rule, manufacturing software is ERP with a production module. A large variety of non-production modules enable entrepreneurs to build a complex manufacturing ecosystem:
- Inventory — for procurement & supplies
- CRM — for working with customers & suppliers
- Sales & integrations with ecommerce platform — for D2C brands who sell produced goods on their own
- Accounting & billing — for the visibility of profit & losses
- HR — for employee payments & management
What Are the 6 Benefits of Manufacturing Software?
No advantage comes alone, it’s always followed by pitfalls.
Benefits | Drawbacks |
✅ Total visibility. Not a single process can be missed. All raw materials up to a tiny cog will be recorded. All actions performed by employees will be easily seen. |
❌ Typically, manufacturing software doesn’t offer free plans. So, you need to be ready to pay a decent price — an approximate range of prices can be found below. |
✅ Increased productivity & speed. When employees don’t need to look for random printouts or fill in Excel sheets, production runs smoothly according to the set procedures. |
❌ Manufacturing software is not an easy thing to do. You’ll have to rearrange all the processes from scratch. You also have to ensure that your employees are ready for changes and they get everything right. |
✅ Profitability. One can get the unit cost, and easily calculate the sale price. Later, interactive dashboards can show the real profit and even forecasts. |
❌ In case you decide to switch to another manufacturing software, it may be challenging to migrate the databases without any loss. |
✅ Scalability. When your company grows, you can choose a more expensive plan to increase the number of users, modules, and integrations available. |
|
✅ Simplified decision-making. Whenever you need to cut costs, extend the product range, or make some other vital decisions, you can use reports to ensure you’re making the right choice. |
|
✅ Low risk level. With manufacturing software, you won’t suddenly run out of raw materials, overpay employees’ wages, or sell finished underpriced goods. |
What 6 Industries Use Manufacturing Software Mainly?
According to Grand View Research, the most common are the following:
- Aerospace & defense
- Consumer goods
- Chemicals
- Pharmaceuticals & medical equipment
- Automotive
- Food & beverage
These industries’ production processes are the most complicated. Any mistake can lead to bad outcomes connected with security & health. That’s why advanced manufacturing software is required by these industries.
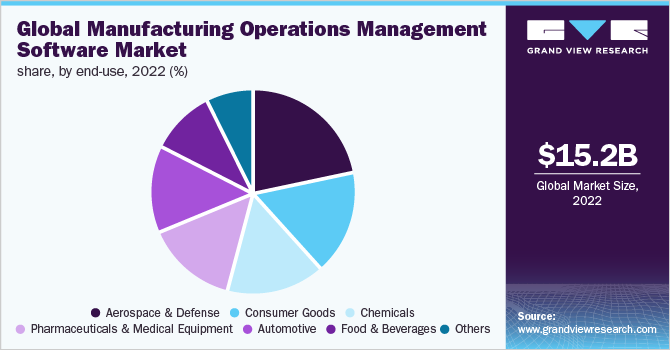
What Are the 6 Main Types of Manufacturing Software?
MRP, MES, PLM, CAD, and EAM — let’s explore what these abbreviations stand for.
ERP Software with a Production Module
It’s the most sought-after type of software with inventory, CRM & sales modules at hand.
MRP
MRP (Material Requirements Planning) is focused on procurement, supplies, and forecasts. MRP systems usually have automated solutions for raw materials purchase, finished goods shipment, etc.
MES
MES (Manufacturing Execution Systems) is focused on management and real-time monitoring of all production stages.
PLM
PLM (Product Lifecycle Management) is about item parts, production papers, quality check routines, etc.
CAD
CAD (Computer-Aided Design) is utilized to create technical item designs and to transfer them into BOMs.
EAM
EAM (Enterprise Asset Management) is used for equipment maintenance & tooling.
How Much Does it Cost?
The plans of most affordable software start from $500–600 annually. The average cost of manufacturing software starts from $1,000 –4,300 annually. The most expensive solutions have plans up to $35,000 annually.
Mind that plenty of software don’t disclose pricing publicly. You can either learn it during the demo, or it’ll be custom-calculated. As a rule, such solutions are quite pricey.
What Are the Hidden Costs?
Say, you’ve chosen the software with reasonable pricing, and the monthly payment is somewhat of what you are eager to spend. Later you realize that you need to add an extra user, and you have to pay additional money. Then, you need an ecommerce integration, and it turns out to be extra-chargeable. So, your initial sum can even double. While choosing the software, the pricing plans must be transparent, without any hidden lines.
Also, unscrupulous developers may not inform you that the software implementation & employee training are not included in the plan and that they are costly enough. And you will suddenly need to spend a lump sum that wasn’t planned or restrain from using any solution in order to keep your business.
Pay attention to the customization tools — whether they are sufficient for your business and whether they are included in your plan. Think about scalability in advance and the way you can upgrade your plan without huge losses.
Top 23 Manufacturing Management Software 2025 — Compare All Features
We’ve compared different production management solutions according to 18 features and made a chart that consists of 23 optimal software. Mind that we sought apps for frugal entrepreneurs, so the low price was the main criterion.
The following information is based on companies’ sources: websites, help centers, social media, and support teams’ replies. The data is valid on February 14, 2024.
Software Name | Production Planning | MRP | Expenses & Profit | Additional Features | Price (Yearly) | Deployment | Overall Score | ||||||||||||
BOMs | Orders | Reports | Operation Costs | Labour Costs | Unit Cost | WIP | Partial Production | Batches | Assignees | Ecommerce | Subcontractors | By-Products & Scrap | Cloud | Desktop | Mobile | ||||
✅ |
✅ |
✅ |
✅ |
✅ |
✅ |
✅ |
✅ |
✅ |
✅ |
✅ |
✅ |
✅ |
✅ |
$559–1,105 |
✅ |
❌ |
❌ |
⭐⭐⭐⭐⭐ |
|
✅ |
✅ |
✅ |
✅ |
✅ |
✅ |
✅ |
✅ |
❌ |
✅ |
✅ |
✅ |
✅ |
✅ |
$600+ |
✅ |
❌ |
❌ |
⭐⭐⭐⭐ |
|
✅ |
✅ |
✅ |
✅ |
❌ |
✅ |
✅ |
❌ |
❌ |
✅ |
✅ |
✅ |
✅ |
✅ |
$540–1,630 |
✅ |
❌ |
✅ |
⭐⭐⭐⭐ |
|
✅ |
✅ |
❌ |
✅ |
❌ |
❌ |
✅ |
✅ |
✅ |
❌ |
✅ |
✅ |
✅ |
✅ |
$360–440 |
✅ |
❌ |
✅ |
⭐⭐⭐⭐ |
|
✅ |
✅ |
✅ |
✅ |
✅ |
✅ |
✅ |
✅ |
❌ |
❌ |
✅ |
✅ |
✅ |
✅ |
$150–230 |
✅ |
❌ |
❌ |
⭐⭐⭐⭐ |
|
✅ |
✅ |
✅ |
✅ |
✅ |
✅ |
✅ |
✅ |
✅ |
✅ |
✅ |
❌ |
✅ |
✅ |
$600–4,300 |
✅ |
❌ |
❌ |
⭐⭐⭐ |
|
✅ |
✅ |
✅ |
✅ |
✅ |
✅ |
✅ |
✅ |
✅ |
✅ |
✅ |
✅ |
✅ |
✅ |
$2,130 –21,500 |
✅ |
❌ |
❌ |
⭐⭐⭐ |
|
✅ |
✅ |
❌ |
✅ |
❌ |
❌ |
✅ |
❌ |
✅ |
❌ |
✅ |
✅ |
✅ |
❌ |
$600–4,300 |
✅ |
❌ |
✅ |
⭐⭐⭐ |
|
✅ |
✅ |
✅ |
✅ |
✅ |
✅ |
✅ |
✅ |
❌ |
✅ |
✅ |
✅ |
✅ |
✅ |
No data |
✅ |
❌ |
❌ |
⭐⭐⭐ |
|
✅ |
✅ |
✅ |
✅ |
✅ |
✅ |
✅ |
✅ |
❌ |
✅ |
✅ |
✅ |
❌ |
✅ |
No data |
✅ |
❌ |
❌ |
⭐⭐⭐ |
|
✅ |
✅ |
✅ |
✅ |
✅ |
✅ |
✅ |
✅ |
✅ |
✅ |
✅ |
✅ |
✅ |
❌ |
No data |
✅ |
❌ |
❌ |
⭐⭐⭐ |
|
✅ |
✅ |
✅ |
✅ |
❌ |
❌ |
❌ |
✅ |
❌ |
❌ |
✅ |
✅ |
✅ |
❌ |
$1,000+ |
✅ |
❌ |
❌ |
⭐⭐ |
|
✅ |
✅ |
✅ |
✅ |
✅ |
✅ |
✅ |
✅ |
❌ |
✅ |
✅ |
✅ |
✅ |
✅ |
$21,500–34,600+ |
✅ |
❌ |
✅ |
⭐⭐ |
|
✅ |
✅ |
✅ |
✅ |
❌ |
✅ |
✅ |
❌ |
✅ |
✅ |
✅ |
✅ |
❌ |
❌ |
$5,100+ |
✅ |
❌ |
✅ |
⭐⭐ |
|
✅ |
✅ |
✅ |
✅ |
✅ |
✅ |
✅ |
❌ |
✅ |
✅ |
❌ |
✅ |
✅ |
✅ |
$3,800–11,000+ |
✅ |
❌ |
❌ |
⭐⭐ |
|
✅ |
✅ |
✅ |
❌ |
✅ |
✅ |
✅ |
❌ |
✅ |
❌ |
✅ |
✅ |
✅ |
❌ |
$1,650–15,600+ |
✅ |
✅ |
✅ |
⭐⭐ |
|
✅ |
✅ |
✅ |
✅ |
✅ |
✅ |
✅ |
✅ |
❌ |
✅ |
❌ |
✅ |
❌ |
✅ |
No data |
✅ |
❌ |
❌ |
⭐⭐ |
|
✅ |
✅ |
✅ |
✅ |
❌ |
❌ |
❌ |
✅ |
❌ |
✅ |
✅ |
❌ |
✅ |
✅ |
No data |
✅ |
❌ |
✅ |
⭐⭐ |
|
✅ |
✅ |
❌ |
✅ |
✅ |
✅ |
✅ |
❌ |
❌ |
❌ |
✅ |
✅ |
❌ |
✅ |
No data |
✅ |
❌ |
❌ |
⭐⭐ |
|
✅ |
✅ |
✅ |
✅ |
✅ |
✅ |
✅ |
✅ |
❌ |
✅ |
✅ |
✅ |
❌ |
✅ |
$7,800+ |
✅ |
❌ |
✅ |
⭐⭐ |
|
✅ |
✅ |
✅ |
✅ |
✅ |
✅ |
✅ |
✅ |
❌ |
✅ |
✅ |
✅ |
❌ |
✅ |
No data |
✅ |
❌ |
✅ |
⭐⭐ |
|
✅ |
✅ |
✅ |
✅ |
✅ |
✅ |
✅ |
✅ |
❌ |
✅ |
✅ |
✅ |
❌ |
✅ |
No data |
✅ |
❌ |
❌ |
⭐⭐ |
|
✅ |
✅ |
✅ |
✅ |
✅ |
✅ |
✅ |
❌ |
❌ |
❌ |
✅ |
✅ |
✅ |
❌ |
No data |
✅ |
❌ |
❌ |
⭐⭐ |
Best Production Management Solutions
Overall, the most affordable production management software are Kladana, Odoo, ERP Next, MRPeasy, Expand ERP, and ERPAG. Those whose main customers are manufacturers are Kladana, Tranzact, Katana, MRPeasy, ERPAG, Fulcrum, Epicor, Global Shop Solutions, and Genius ERP.
The solutions with mobile apps are the following: Deskera, Fishbowl, MRPeasy, inFlow, Expand ERP, Plex, ProShop, Prodsmart, and ERPAG (Android). As to the other features, their content varies from one app to another.
Kladana
Cloud composite manufacturing software with an MRP module suitable for D2C businesses, and small & medium-sized manufacturers. Kladana helps one to control all the production stages starting from a single cog to ready-to-use machinery.
Using Kladana, one can boost their manufacturing startup or develop an existing business: plan & purchase supplies, calculate costs & profit, create BOMs, complete production orders, and sell finished goods online. All these can be done in one app due to its multiple features, API, and integration with Shopify.
Kladana is not a newcomer in the industry. Its story began 17 years ago, and now, the software is expanding to different markets, and working on new features. In case of any second thoughts & doubts, one can try a free 14-day trial, and then choose a proper plan. The production module is an option that can be purchased for $43 a month or $358 a year in the Growth, Business, and Business Plus plans.
The first steps of onboarding can be completed within 15 minutes. All features can be mastered with the help of a personal manager, support team, emails, videos & tutorials in the Help Center.
There are a lot of manufacturers among Kladana clients. Read case stories to learn more:
- «Space» Lemonade Manufacturing: 1,500 Bottles are Moved from one Warehouse to Another in Two Clicks
- How to Create a Clothing Brand and Increase Turnover from 145 Lakh Rupees up to 260 Lakh Rupees in a Year
- How to turn a loss-making manufacturing into a profitable one
Pros | Cons |
✅ Affordable — from $67 a month, discounts up to 25% with a yearly plan |
❌ No desktop or mobile versions |
✅ All core production planning features |
|
✅ MRP |
|
✅ All types of costs: operation, labour & unit cost |
|
✅ Plenty of additional features: partial manufacturing, Work-in-Progerss (WIP), subcontracts, etc. |
|
✅ Online Order App & Shopify and WooCommerce integrations for direct sales |
|
✅ Free 14-day trial |
|
✅ User-friendly interface & easy onboarding |
|
✅ Detailed analytics and reports |
Available Plans with the Production Module
-
Growth
$67/monthly
$559/annually
Good for a start: 2+ users, 2 companies, 0.5+ GB of data storage. Unlimited warehouses, items, counterparties, and transactions. All production management features, including production orders, multi-level BOMs, expenses calculation, MTO, work orders, subcontractor management, WIP, etc. All manufacturing features can be found on the pricing page.
Barcoding, CRM, custom fields, custom print templates, and Online Order App are also included. Automation via workflows is an available option.
-
Business
$92/monthly
$770/annually
The most popular plan: 5+ users, 5 companies, 2+ GB of data storage. All features of the Growth plan plus user access rights, and unlimited support and onboarding.
-
Business Plus
$132/monthly
$1,105/annually
Suitable for a big company: 10+ users, unlimited companies, 10+ GB of data storage. All features of the Business plan are included plus workflows.
ERPNext
Smart cloud-based production ERP software.
Pros | Cons |
✅ Affordable — from $50 a month |
❌ No phone support for SMEs |
✅ Manufacturing scheduling |
❌ No partial manufacturing |
✅ Production analytics |
|
✅ Workstations, shop floor management connected to the manufacturing |
|
✅ Integrations with Amazon, Shopify, Stripe, PayPal, etc. |
|
✅ Modern user-friendly interface |
|
✅ Comprehensive reports enable one to make data-driven decisions |
Available Plans
-
Small Business
$50/monthly
Unlimited users, managed hosting -
Enterprise
Price is set custom
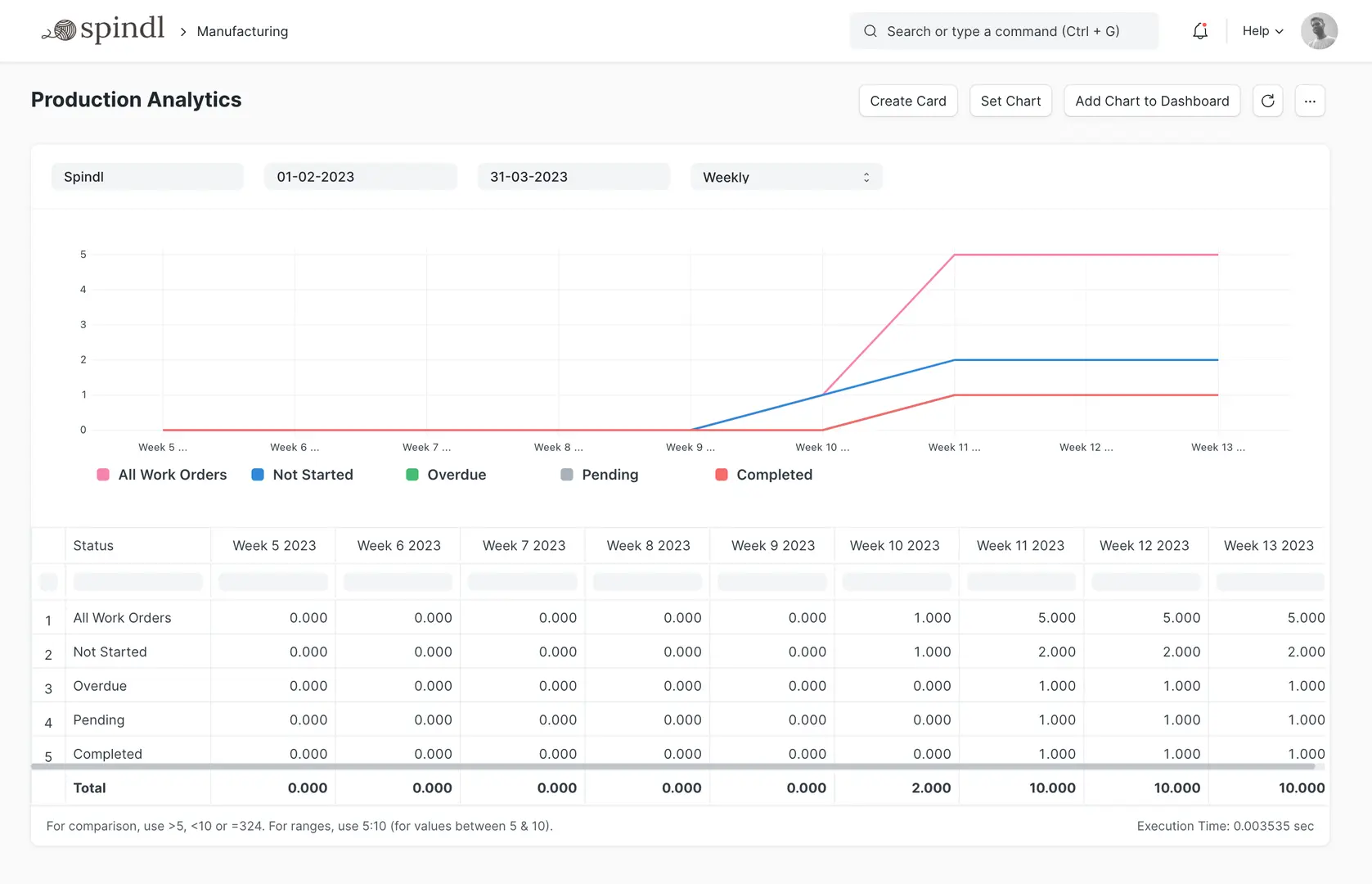
MRPeasy
AI-powered MRP software for SMEs. MRPeasy is a company with a 23-year history. It started with web app development and later started making easy-to-handle solutions for small manufacturers.
Pros | Cons |
✅ Relatively affordable — from $45 (per user) a month |
❌ Not all features are available — operation costs, WIP & partial manufacturing |
✅ Production statistics |
|
✅ Material requirements forecast |
|
✅ Production scheduling with a calendar |
|
✅ Free 30-day trial |
|
✅ Workstations, equipment utilization & multi-site production |
|
✅ Suitable for multiple industries: marine, biotechnology, textile, paper, etc. |
|
✅ Integrations with Amazon, HubSpot, Salesforce, etc. |
Available Plans
-
Starter
$50 (per user)/monthly
$540 (per user)/annually
Main functions & integrations -
Professional
$70 (per user)/monthly
$760 (per user)/annually
Professional functions -
Enterprise
$100 (per user)/monthly
$1,100 (per user)/annually
Enterprise functions -
Unlimited
$150 (per user)/monthly
$1,630 (per user)/annually
Full package with no limits
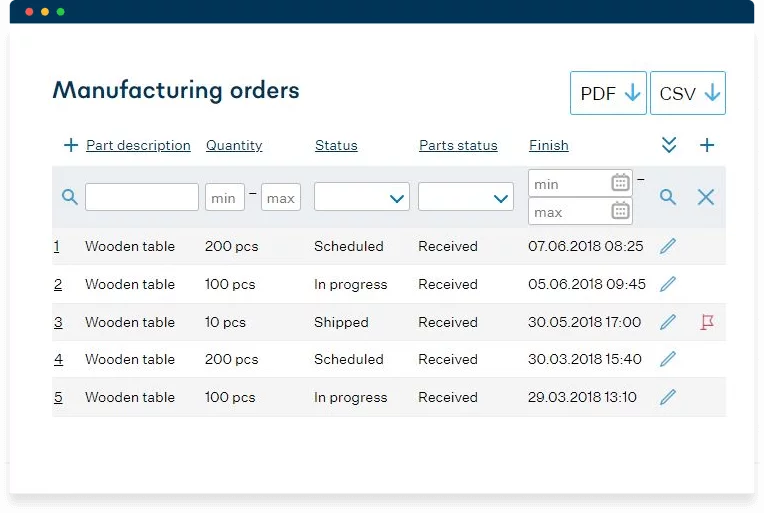
Expand ERP
ERP system for manufacturers in the mid-market segment. Suitable for multi-site production along with subcontractors. A company with a 28-year history that has been creating apps for various business purposes.
Pros | Cons |
✅ Relatively affordable — from $30 (per concurrent user per month)/annual payment |
❌ Not all features are available: comprehensive operation reports, batch, operation & labour costs |
✅ One production order can be divided into a few ones |
❌ No discounts for yearly plans |
✅ Discrete and process manufacturing |
|
✅ Operation stages due dates |
|
✅ Quality check, machine tracking |
|
✅ Free iOS & Android apps |
|
✅ Integrations with Shopify, Flipkart, WhatsApp & Shiprocket |
One Production Plan
Expand
$30 (per concurrent user per month)/annual payment
$36 (per concurrent user per month)/quarterly payment
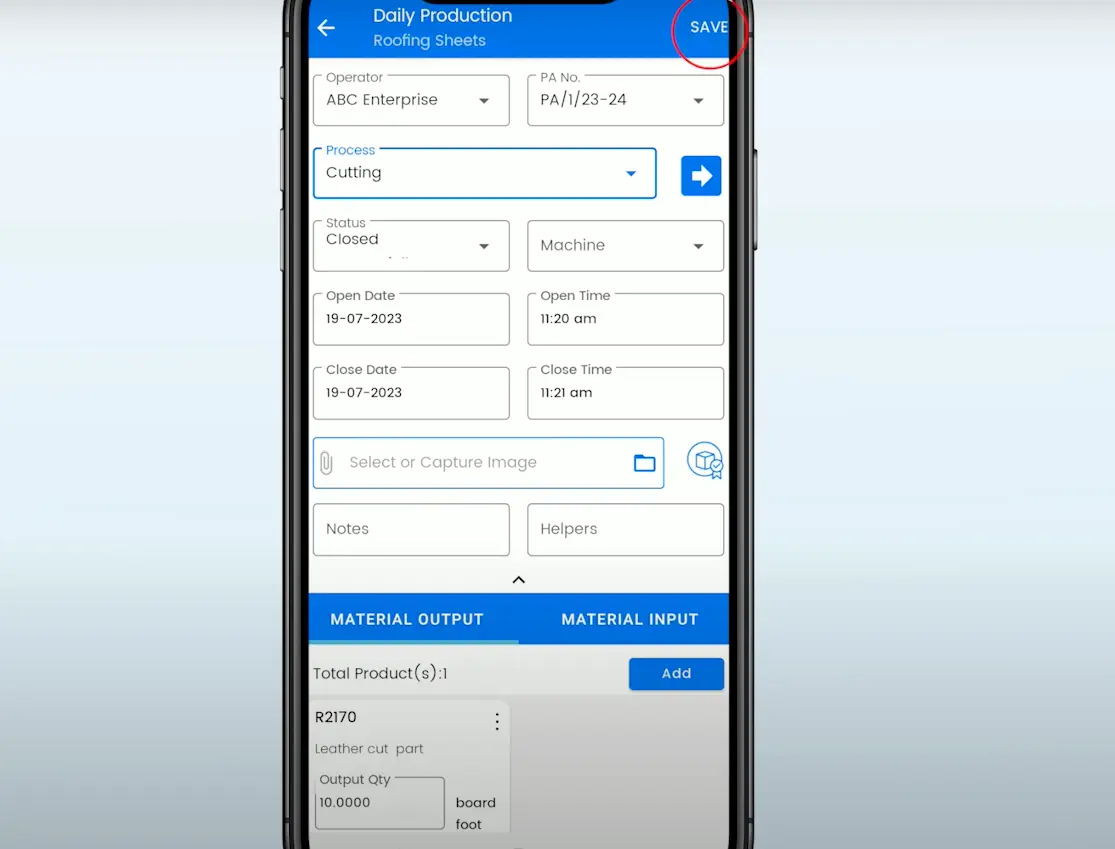
Read‑alikes
Full Guide to MRP Solutions: Core Features, Advantages and Pitfalls
Managing Production in a Small Manufacturing Company: Planning, Control, and Profit Calculation
Odoo
Out-of-the-box manufacturing software that meets the needs of businesses of various sizes and from different industries. Odoo Manufacturing module is a part of a large Odoo ecosystem with 30+ applications helping entrepreneurs run their businesses.
Pros | Cons |
✅ Affordable — from $13 per user a month |
❌ You can use only one app for free. Say, you choose Manufacturing. Then Marketing, Sales, HR, and Finance will be unavailable |
✅ Master production scheduling, demand forecast |
|
✅ Product Lifecycle Management (PLM), maintenance, worksheets |
|
✅ Quality control: fail tests & photos |
|
✅ Printers, barcode scanners & other devices connection |
|
✅ Automatic time-tracking |
Available Plans
-
Free
1 app (Manufacturing), unlimited users -
Standard
$16 (per user)/monthly
$150(per user)/annually
All apps, unlimited users, Odoo Online -
Custom
$25 (per user)/monthly
$230 (per user)/monthly
All apps, unlimited users, multi-company, external API, Odoo Online, Odoo
On-premise
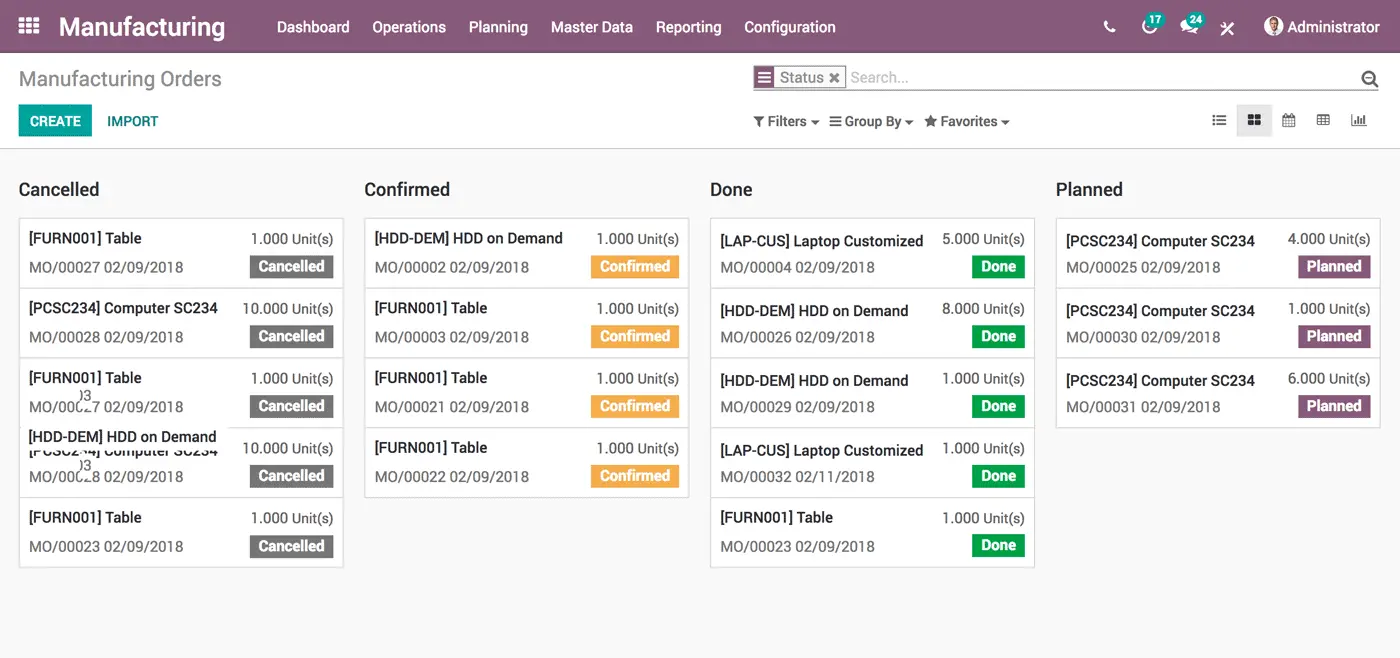
Tranzact
Tranzact sets itself up as MRP, ERP & production management software for Indian manufacturers. Tranzact enables a make-to-order production process: one can plan the resources, execute production stages, and test ready-made goods.
Pros | Cons |
✅ An evident choice for those who produce items |
❌ Expensive — from $50 a month |
✅ Finished goods testing is available after which items can pass the test, be rejected, or need repair |
❌ Only quarterly or annual payments, no monthly payment is available |
✅ Has an extensive set of production features |
❌ Add-ons are extrachargeable: barcoding, accounting, customizations, etc. |
✅ Forecasting & reporting, including real-time MRP reports |
❌ Isn’t suitable for D2C companies as there are no integrations with ecommerce platforms for product sales |
✅ Support is available even for the free plan |
|
✅ 7-day implementation is promised |
Available Plans
-
Small Plan
$560/annually
Up to 5 users
Multi‑level Bill of Material
Single‑step production
BOM Costing -
Medium Plan
$360/quarterly
$1,430/annually
Up to 10 users
Multi-step production
Subcontracting
Production costing -
Enterprise Plan
$1,050/quarterly
$4,300/annually
10+ users
Batch tracking & barcoding
Customized reports
IP Whitelisting
Mind that add-ons are extra-chargeable:
- paid implementation — $290
- accounting — $145/annually
- barcoding — $300/annually
- e-invoicing— $145/annually
- system customizations — $145/annually.

Katana
Katana MRP is designed for SMEs who want to optimize their production routines seamlessly — the user-friendly interface enables that. The software was founded in 2017.
Pros | Cons |
✅ Make-to-order & make-to-stock workflows |
❌ Expensive — from $180 a month |
✅ Subassemblies are available |
|
✅ Resource planning allows to avoid bottlenecks in the procurement process |
|
✅ Production deadlines |
|
✅ Integrations with Shopify, Amazon, eBay, HubSpot, Zapier, etc. |
|
✅ Free templates, spreadsheet, guides & SKU generator |
|
✅ Free 14-day trial |
Available Plans
-
Starter
$200/monthly
$2,130/annually
1 inventory location
1,200 sales orders per year -
Standard
$400/monthly
$4,275/annually
3 inventory locations
6,000 sales orders per year -
Professional
$900/monthly
$9,530/annually
10 inventory locations
18,000 sales orders per year -
Professional Plus
$2,000/monthly
$21,460/annually
Unlimited inventory locations
40,000 sales orders per year
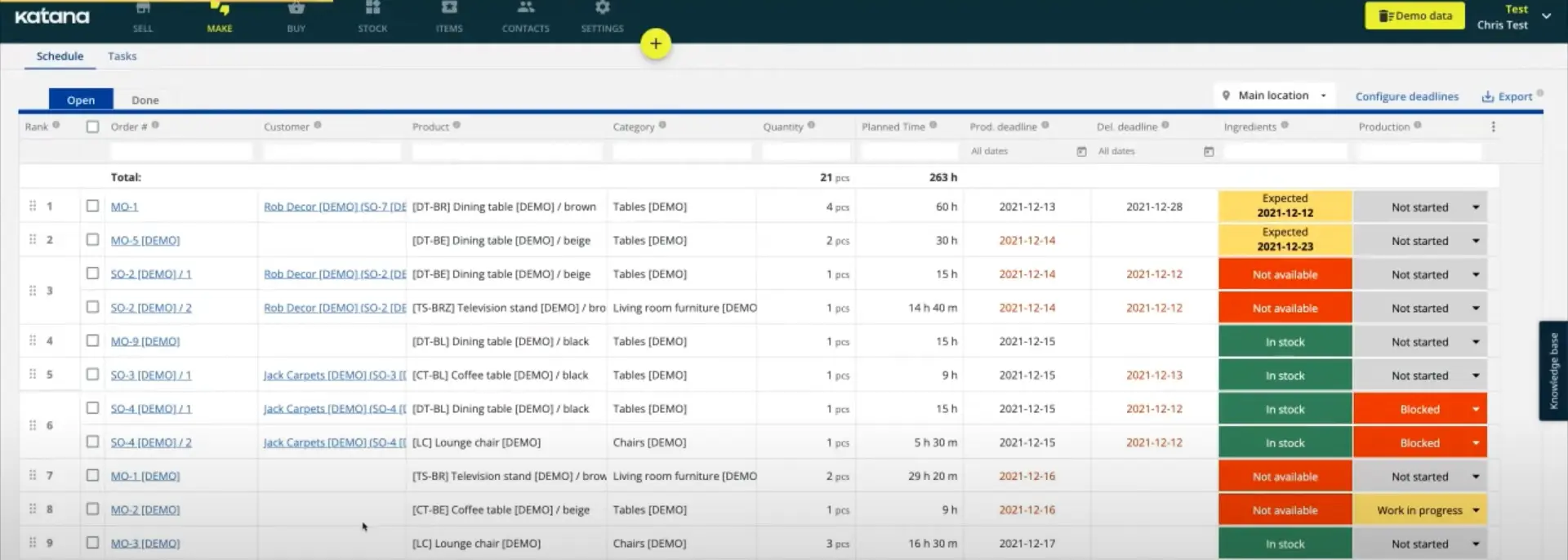
ERPAG
Cloud-based MRP solution & end-to-end production software.
Pros | Cons |
✅ Affordable — from $50 a month |
❌ Not all basic features are available: comprehensive data-driven operation reports, labour & operation costs, WIP, batches & scrap counting |
✅ Parts (subassemblies) manufacturing is available |
❌ No iOS mobile app |
✅ Time-tracking is available |
|
✅ Machines tracking & management |
|
✅ Solutions for various industries: food, medical devices, oil & gas manufacturing, etc. |
|
✅ Integrations with Woo, Shopify, Xero, etc. |
|
✅ 15-day free trial |
|
✅ Mobile app for Android |
Available Plans
Basic
$50/monthly
All modules, including manufacturing
Professional
$100/monthly
Live support
Customization
Advanced
$200/monthly
Customer portal
Automation
Smart API
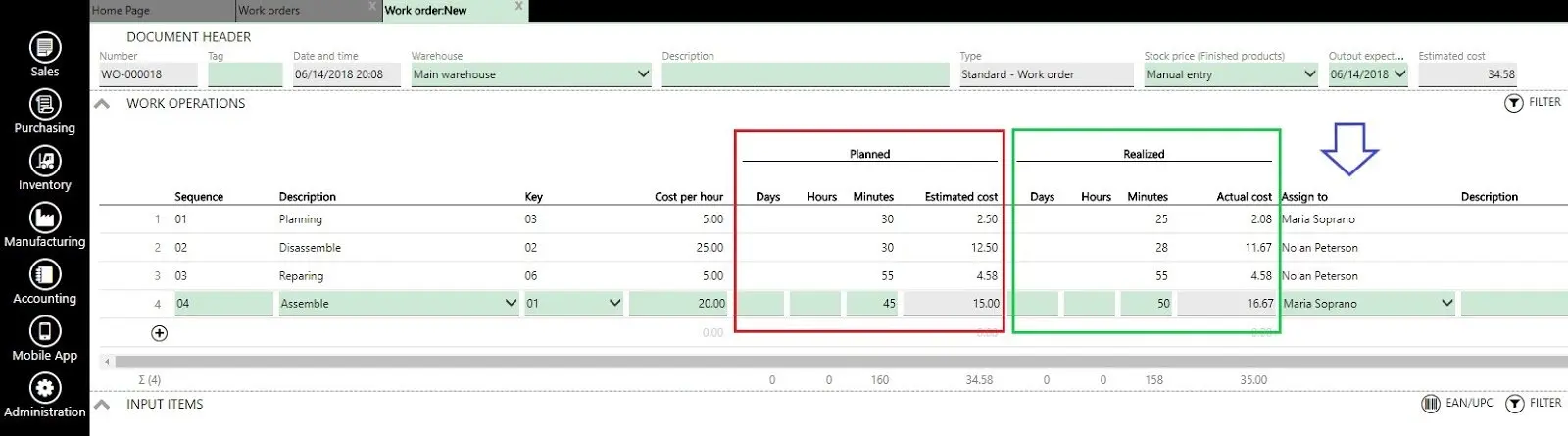
Acumatica
Multi-site cloud-based production software that provides all popular manufacturing methodologies: engineer-to-order, make-to-order, make-to-stock, etc. Acumatica has a 15-year history.
Pros | Cons |
✅ Discrete and batch process production |
❌ Prices are not disclosed publicly |
✅ Provides a large variety of manufacturing management features |
|
✅ Production scheduling, engineering change control |
|
✅ Machine maintenance & tooling |
|
✅ Integrations with Shopify, ShipStation, PayPal, etc. |
|
✅ An entrepreneur can choose where to store their data — on a public cloud or a private one |
|
✅ Plans with unlimited users |
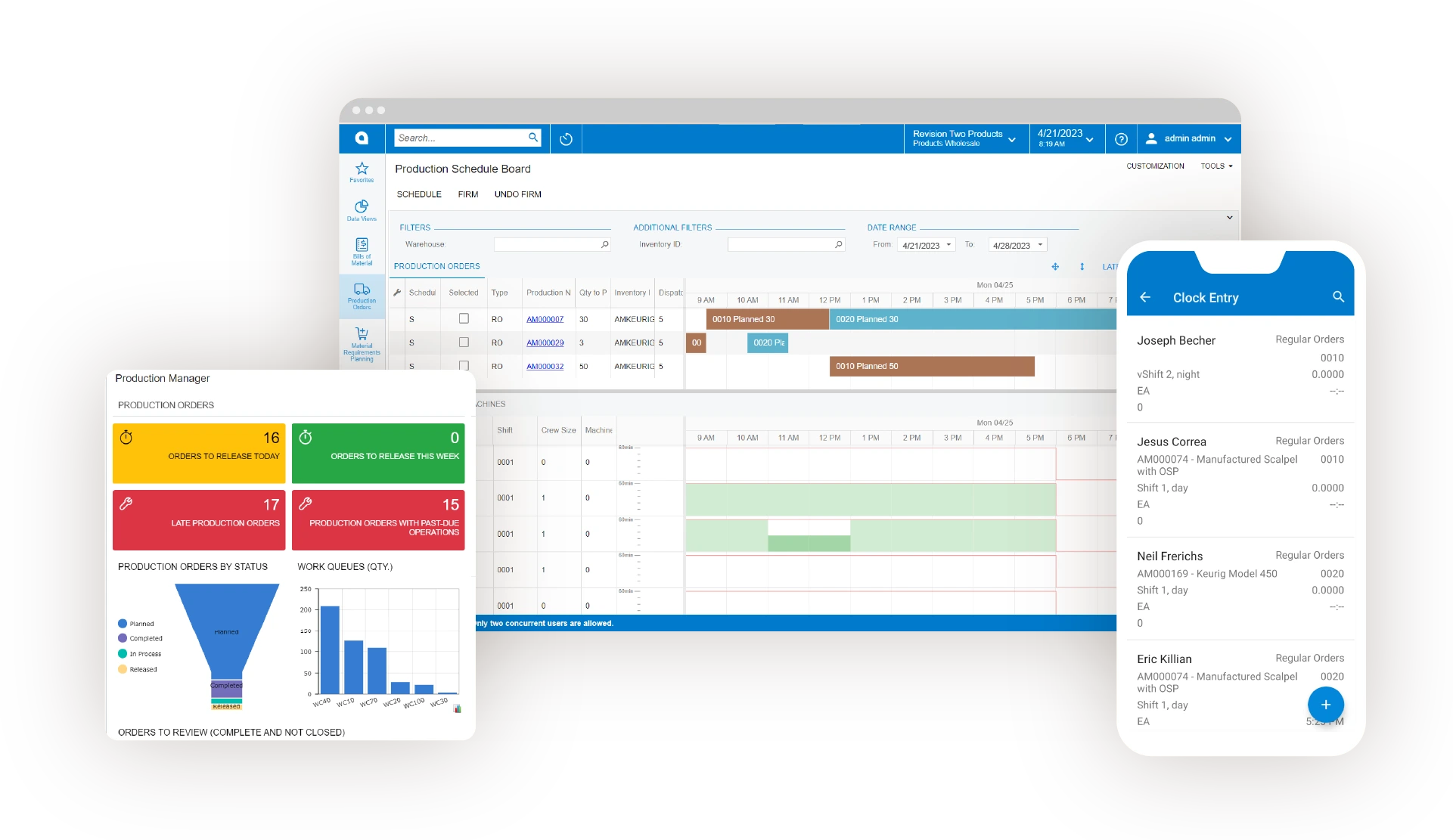
Fulcrum
The main idea of Falcrum is to connect one’s shop with production management for better decision-making. Also, the easy-to-handle software pays attention to the visual data: blueprints, 3D models, assembly instructions, etc.
Pros | Cons |
✅ Contemporary user-friendly interface |
❌ Price plans are not publicly disclosed |
✅ Almost all basic features are available |
|
✅ Production operations progress tracking |
|
✅ Quality checks |
|
✅ Interactive education |
|
✅ Integrations with ShipStation, Salesforce, HubSpot, etc. |
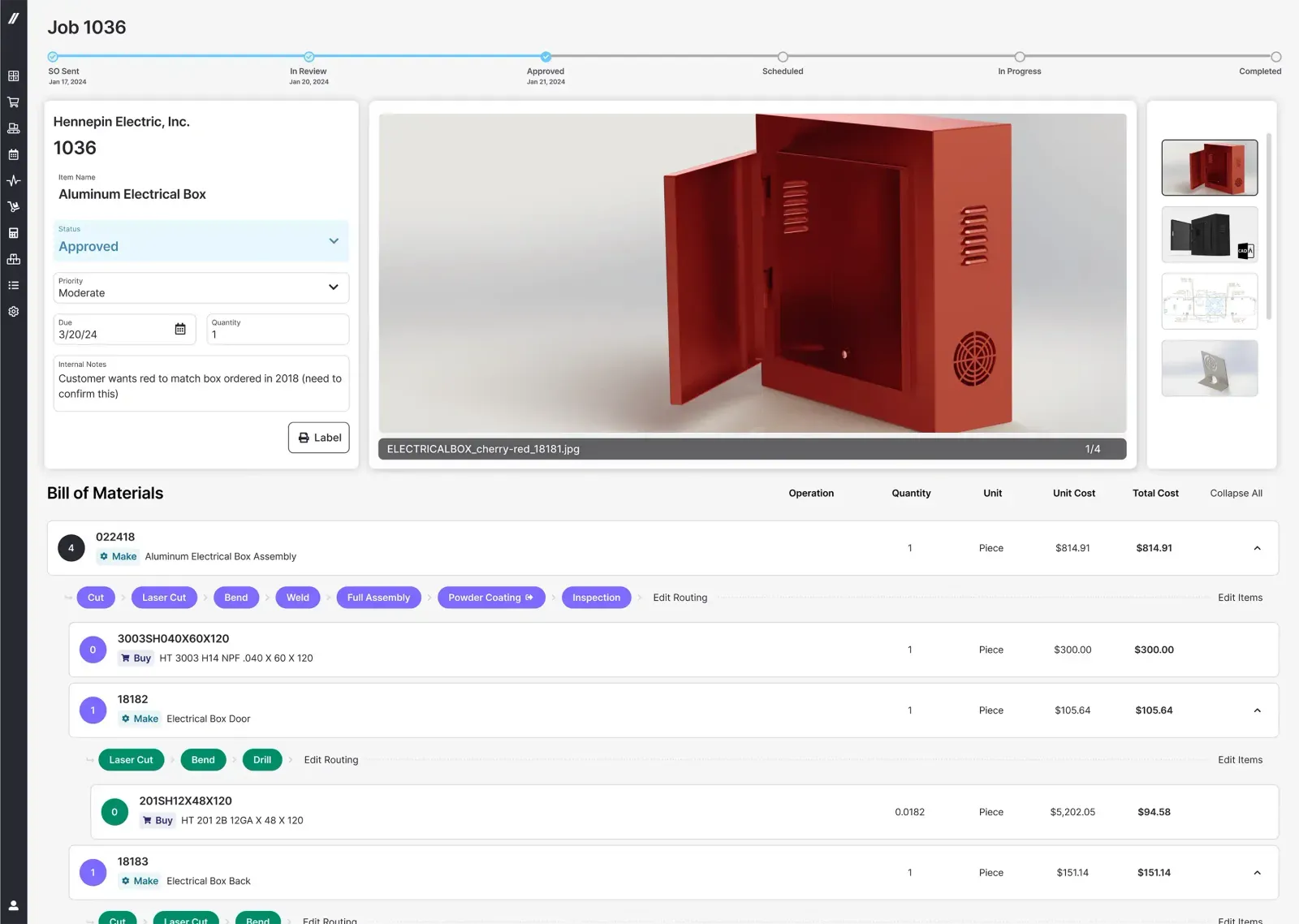
Oracle NetSuite
NetSuite for Manufacturing is a module in the large Oracle NetSuite ecosystem.
Pros | Cons |
✅ Multi-location planning & DRP (distribution requirement planning) |
❌ Pricing is not disclosed publicly |
✅ Shop floor control |
❌ Isn’t suitable for small businesses, is designed rather for large-scale companies that hit the Forbes Cloud 100 list |
✅ Quality management |
|
✅ MES |
|
✅ All basic features are available |
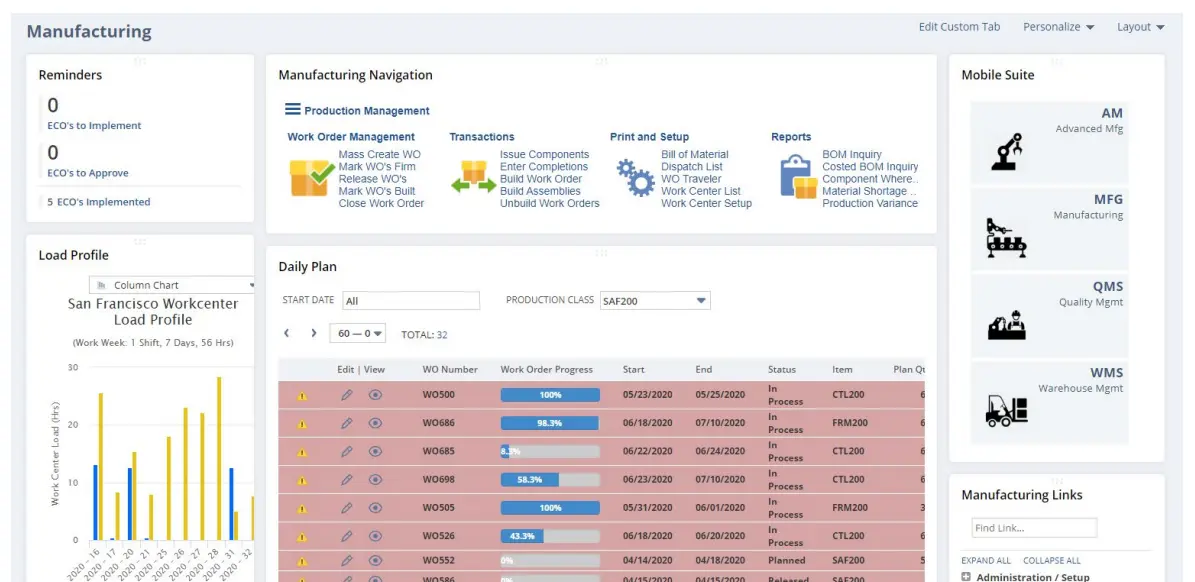
BizAutomation
MRP focused on growing SMBs. BizAutomation calls itself a «customer advocate» because they claim that they don’t have hidden features, all the processes are transparent, and even the price plan is the only one.
Pros | Cons |
✅ Production demand planning is included |
❌ Expensive — from $80 (per user) a month |
✅ Production scheduling |
❌ Not all basic features are available or work only through the ERP integrations |
✅ WIP progress bar is available |
|
✅ Quality check |
|
✅ A finished good can be disassembled |
One Plan
$80 (per user)/monthly
Mind that add-ons are extra-chargeable:
- ecommerce platform — $200 (per site)/monthly
- ecommerce integration (e.g. Amazon) — $200 (per integration)/monthly
- other add-ons are in the pipeline
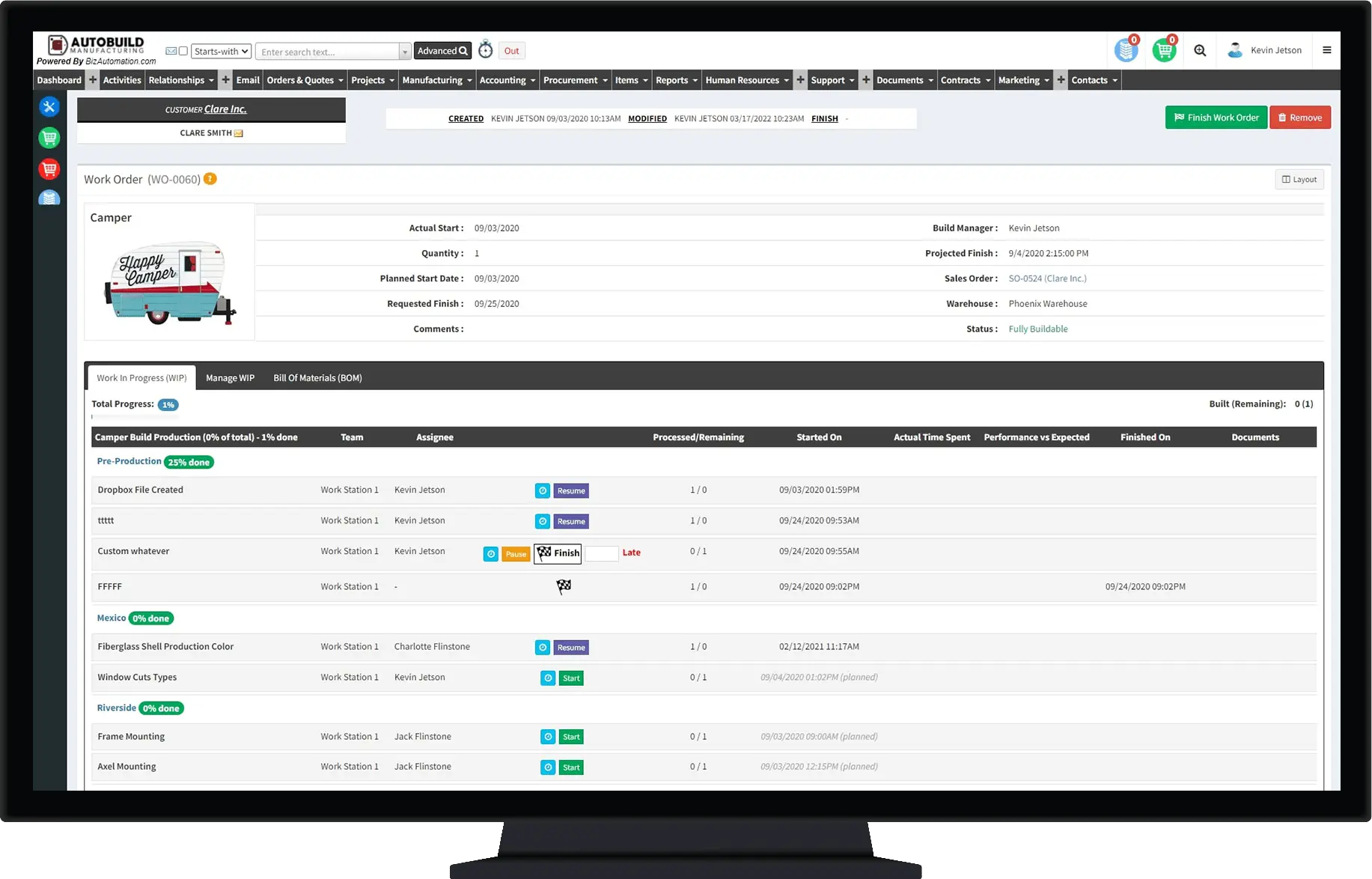
Relevant Case Stories
Artisanté: How to Streamline Chocolate & Coffee Manufacturing Management in Half a Year
Cura Pharmaceuticals Manufacturing: Increased Data Accuracy & Business Workflows in 6 Months
Unicorn Natural Products Manufacturing: a Journey from Spreadsheets to ERP
Deskera
The engineer-to-order MRP software that enhances productivity & visibility. Despite its high cost, Deskera is considered to be an industry-leading company that has been on the market for 15 years already. Deskera’s positioning is a growth business partner rather than simply a software provider.
Pros | Cons |
✅ Demand forecasting helps reduce waste |
❌ Extremely expensive — from $1,800 a month |
✅ Machine management & maintenance |
❌ No tool for partial manufacturing |
✅ Solutions for various industries: apparel, beauty, healthcare, etc. |
|
✅ Integrations with Amazon, Shopify, FedEx, Woo, etc. |
|
✅ A free mobile app with limited features can be used |
|
✅ Onboarding & training take a few hours, as promised |
Available Plans
-
Growth
From $1,800/monthly
5 users, work orders, multi-level BOMs, manufacturing reports, yield calculations -
Mid Market
From $2,900/monthly
10 users, demand forecasting, contract production, manufacturing scheduling, quality checks -
Enterprise
Custom price
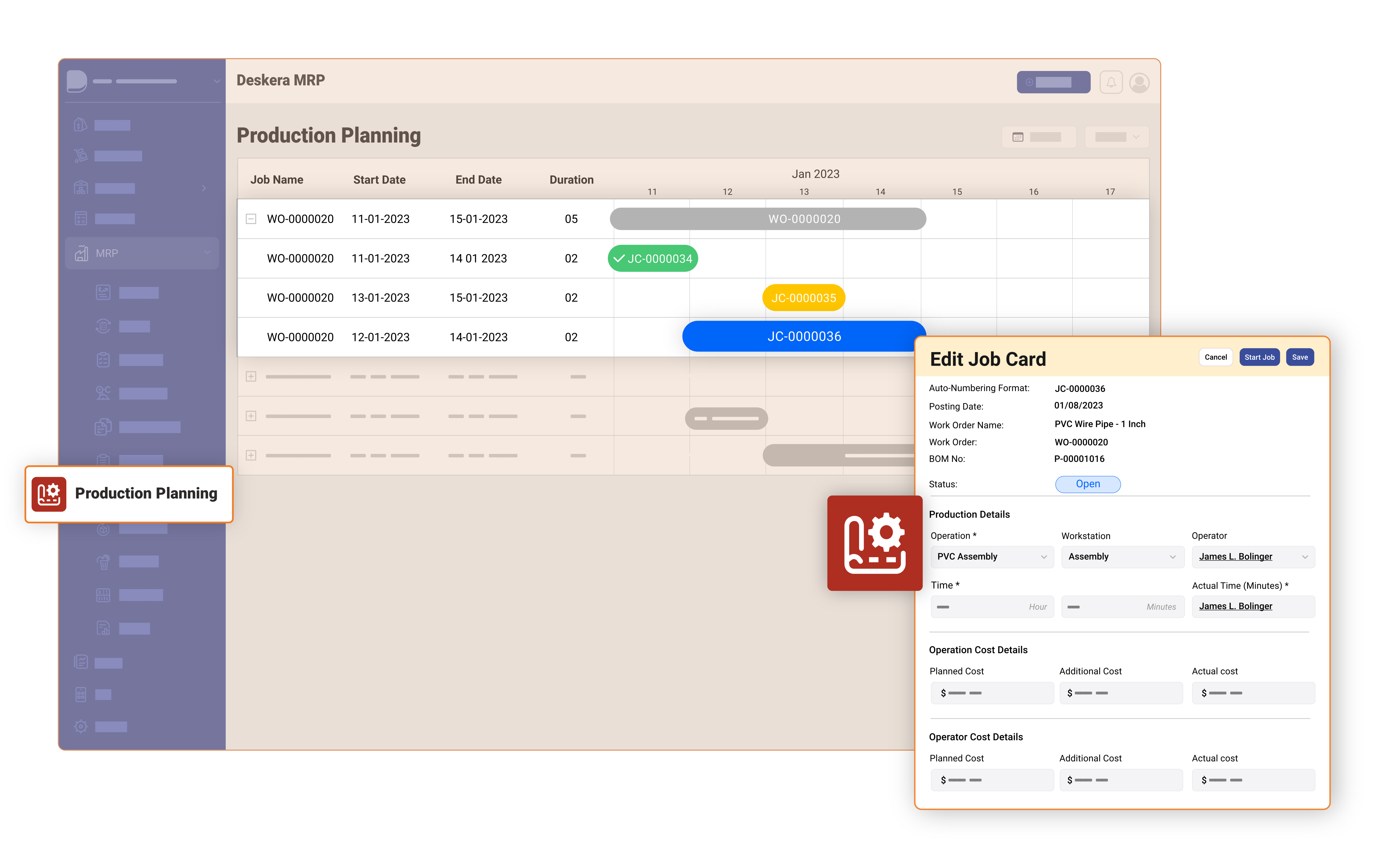
Fishbowl
Complex all-in-one manufacturing management platform.
Pros | Cons |
✅ Customizable complex, multi-level, and staged bill-of-materials |
❌ Expensive — from $430 a month |
✅ Subassemblies are available |
❌ Outdated interface |
✅ Production scheduling taking into account the season |
❌ Not all features are available: scrap counting, WIP, subcontractors & operation costs |
✅ Workstations & manufacturing jobs |
|
✅ Mobile app |
|
✅ 8-week training & certification |
|
✅ Free BOM template |
Fishbowl Advanced
From $430/monthly
From $5,100/annually
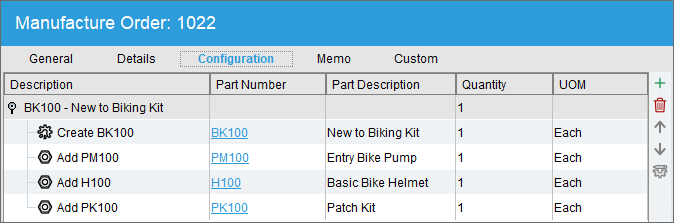
Unleashed
BOM software that streamlines one’s production, and increases efficiency in day-to-day manufacturing operations. Flexible & cohesive solution focused on MRP & BOMs. Unleashed is software with a 10-year history suitable as for startups, as for large-scale enterprises.
Pros | Cons |
✅ Auto-assembled products, disassembly, kitsets, bundles & batches |
❌ Expensive — from $320 a month |
✅ Multi-level BOMS |
❌ Some features are not available |
✅ Precise profit margins |
|
✅ Subassemblies |
|
✅ Integrations with Amazon, Shopify, Woo, Lightspeed, etc. |
|
✅ Free 14-day trial |
|
✅ Unleashes Academy educates existing & to-be customers |
Available Plans
-
Mid-sized businesses
$350/monthly
$3,800/annually
3 users -
Scaling businesses
$650/monthly
$7,150/annually
8 users -
Emerging enterprises
$1,000/monthly
$11,000/annually
20 users
Mind that add-ons are extra-chargeable:
- ecommerce hub — from $25/monthly
- B2B ecommerce — from $130/monthly or from $1,400/annually
- and other add-ons connected with inventory management, storage, etc.
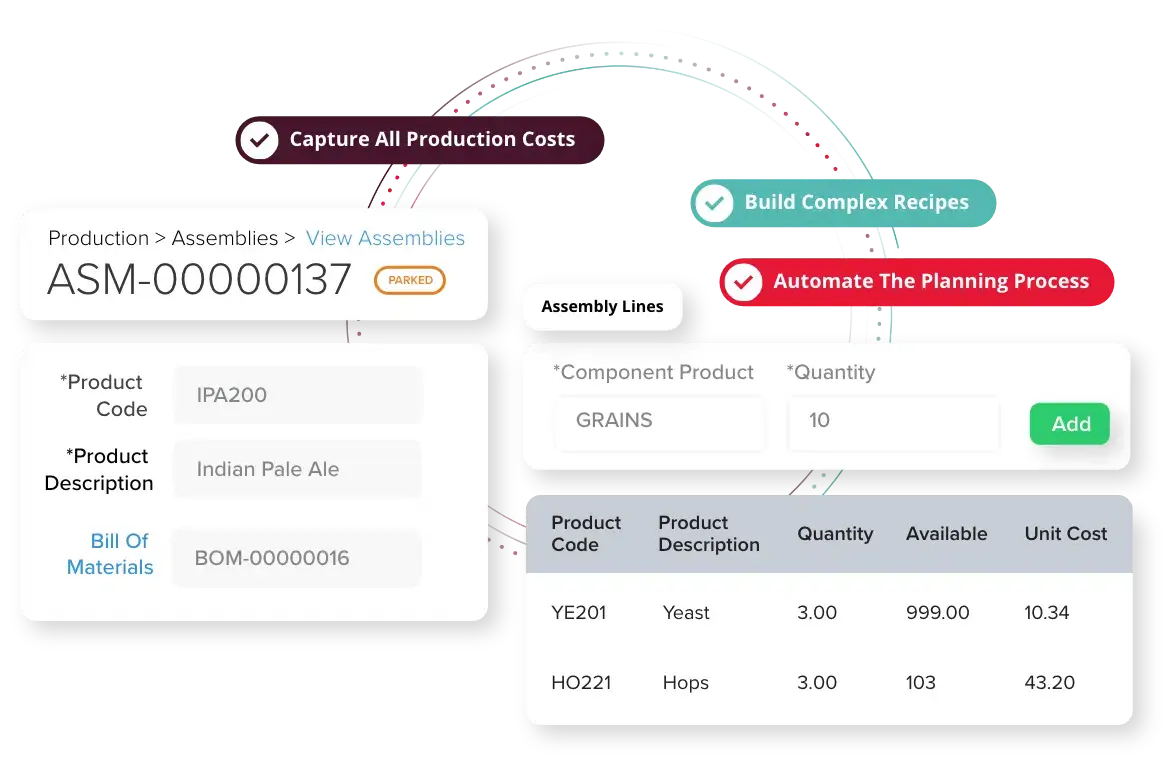
inFlow
All-in-one production management software that helps one reduce manual labour on day-to-day operations. inFlow has been in business for 12 years. The mission is to support solo businesspeople & SMEs from various industries. Also, they build a community of entrepreneurs.
Pros | Cons |
✅ Production orders prioritization & scheduling due to deadlines |
❌ Expensive — from $140 a month |
✅ Subassemblies & auto-assembly |
❌ Not all basic features are available: WIP, MRP, batches & scrap |
✅ Cloud, desktop & mobile apps |
❌ Supports payment for customers from US and Canada only |
✅ Free 14-day trial |
|
✅ B2B portal for online sales which works as a showroom |
|
✅ Integrations with Amazon, Etsy, Xero, Walmart, etc. |
|
✅ Contemporary user-friendly interface |
Available Plans
-
Entrepreneur
$160/monthly
$1,640/annually
2 users, 1 location, 1 integration, 2 hours setup assistance -
Small Business
$350/monthly
$3,450/annually
5 users, unlimited locations, 2 integrations, 4 hours of setup assistance, B2B portal -
Mid-Size
$675/monthly
$6,800/annually
10 users, unlimited locations, 3 integrations, 6 hours of setup assistance, B2B portal pro -
Enterprise
$1,560/monthly
$15,560/annually
25 users, unlimited locations, 4 integrations, 10 hours of setup assistance, premium database
Mind that add-ons are extra-chargeable:
- Serial numbers — $30–$100/monthly
- Advanced access rights — $50/monthly
- API access — $50–70/monthly
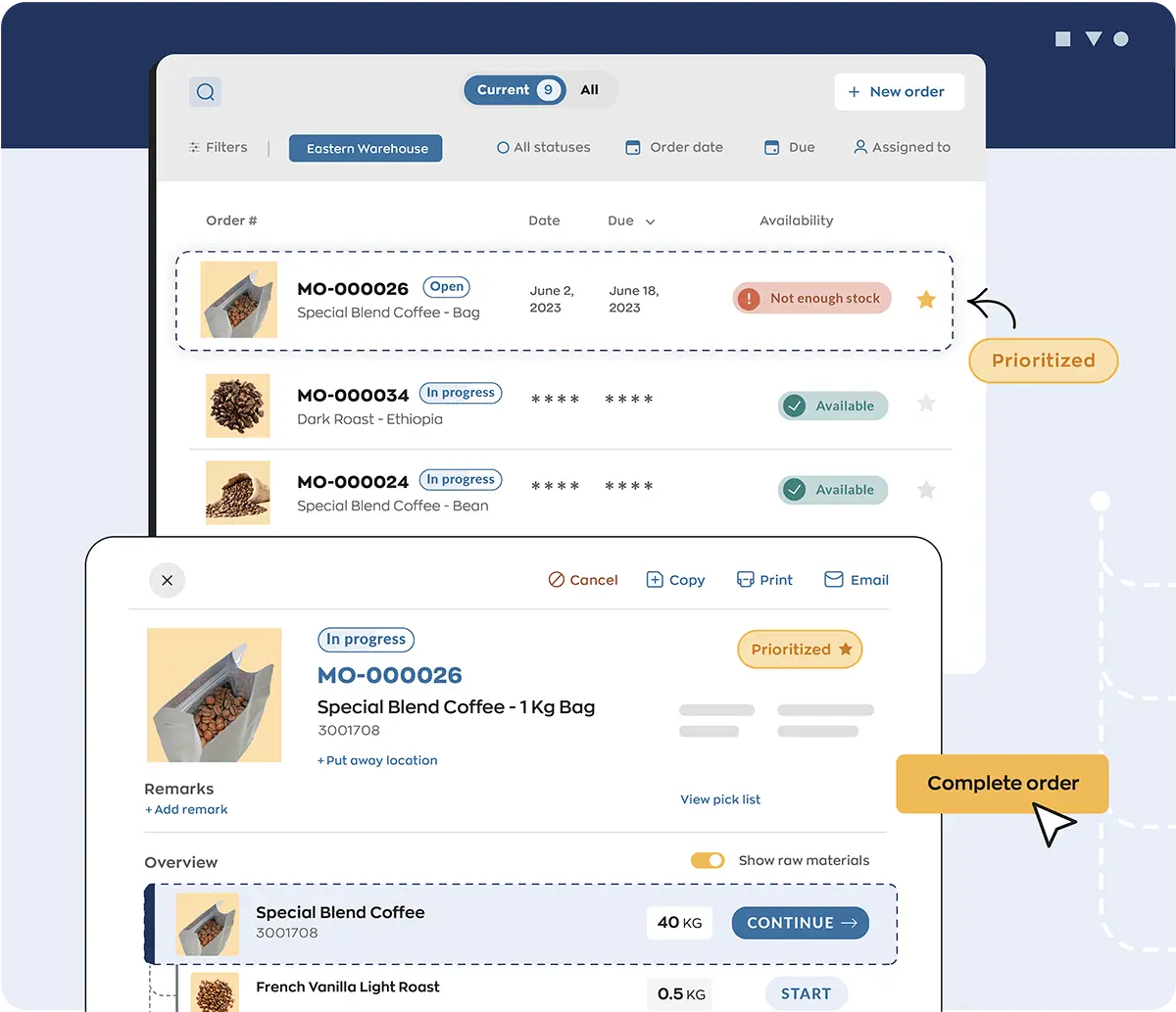
PACT ERP
End-to-end ERP software with a manufacturing module. PACT ERP has been developing solutions for SMEs for the last 25 years.
Pros | Cons |
✅ Focus on accurate profit margin calculations, and all direct & indirect expenses connected to the production process |
❌ Prices are not publicly disclosed |
✅ Equipment tracking |
❌ No info on the actual interface, only the sales team can share it during a demo which seems suspicious enough |
✅ Seasonal demands forecast |
❌ Not all features are available |
✅ Multi-level BOMs |
|
✅ Shortfall Reports |
|
✅ Batch-wise consumption analysis |
Plex
The manufacturing execution system enables visibility and helps control the entire production cycle. 30 years of experience, 20 of which are in the cloud format make Plex one of the leaders in the market.
Pros | Cons |
✅ Control Panel for running production, maintenance, analytics, etc. |
❌ Prices are not disclosed publicly |
✅ Digital Kanban production scheduling |
❌ Many vital features are missing |
✅ Tools purchase & control |
|
✅ Quality Management System |
|
✅ Smart Manufacturing Platform |
|
✅ Chesksheet |
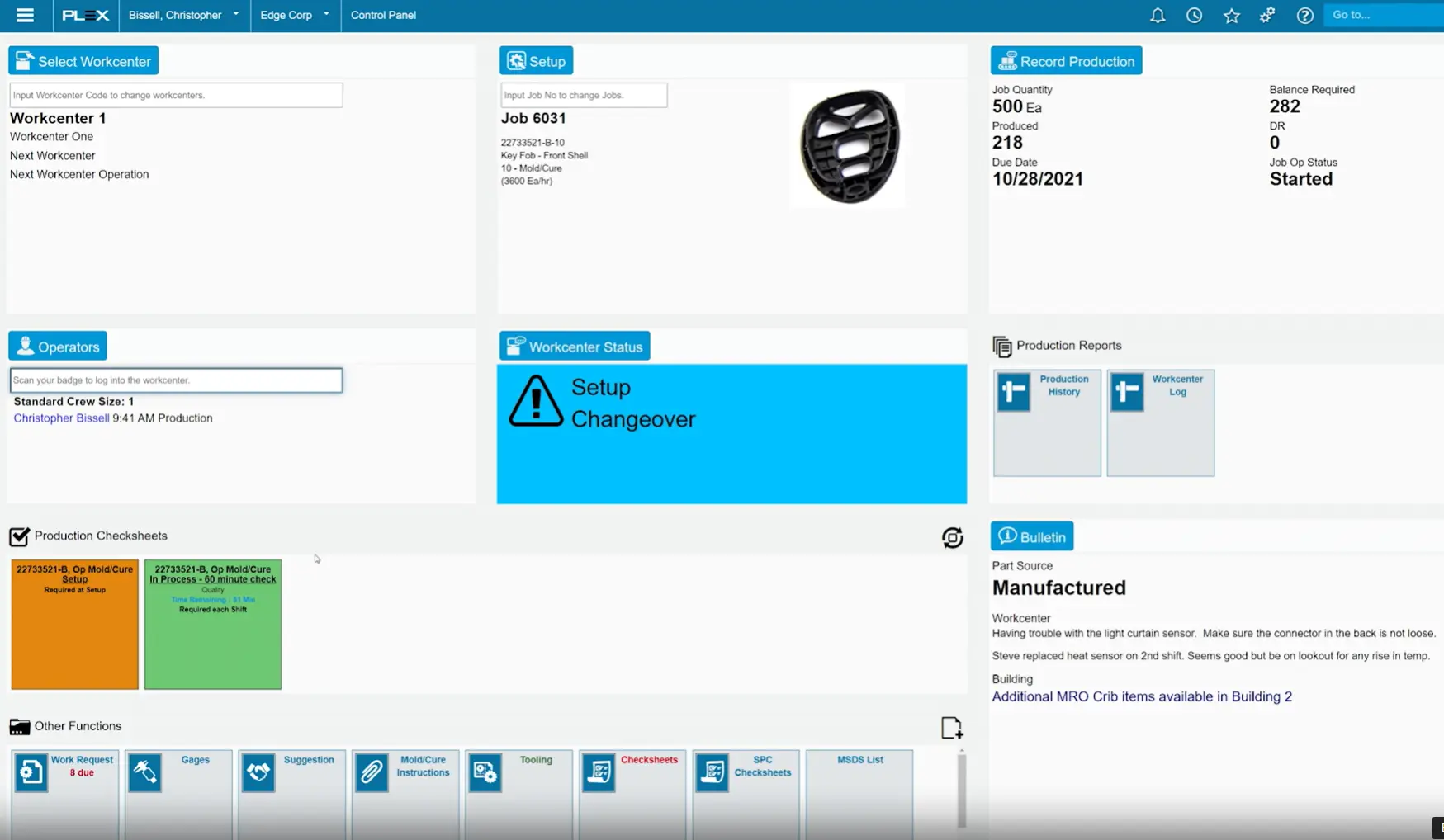
Epicor
Manufacturing execution software (MES) with a focus on a smart factory transformation. Epicor is one of the market dinosaurs (in a positive way) with a 50-year history. The software focuses on industry-based solutions.
Pros | Cons |
✅ Energy consumption monitoring, machine capacity planning |
❌ Plans are not publicly disclosed |
✅ Kanban scheduling |
❌ The interface doesn’t seem to be user-friendly |
✅ Quality control |
❌ A lot of crucial features are missing |
✅ Real-time shop floor visibility |
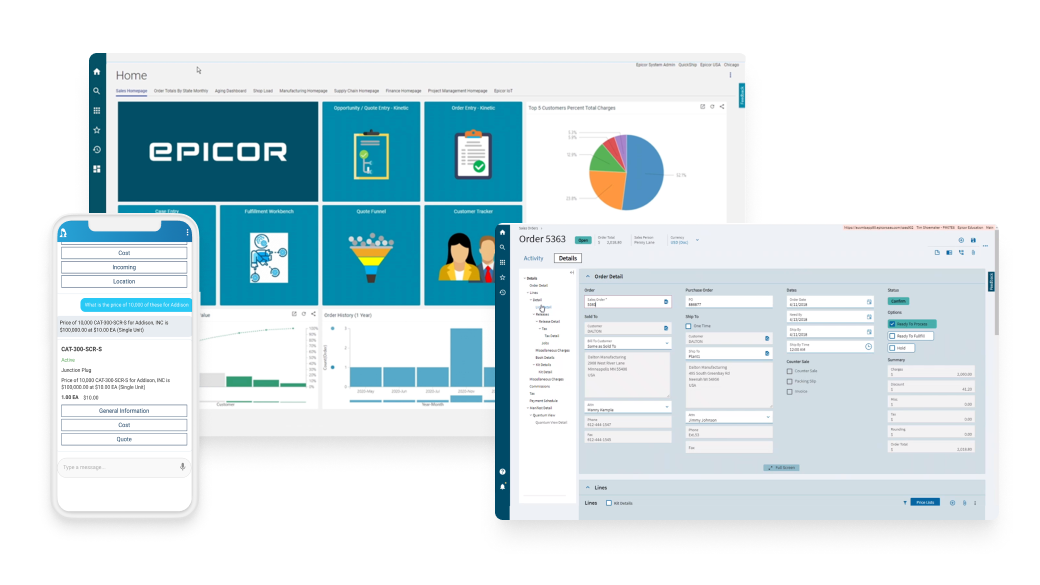
ProShop
30-year-old ERP with a MES (manufacturing execution system) module.
Pros | Cons |
✅ In-depth estimates |
❌ Expensive — from $650 a month |
✅ Work order scheduling |
❌ Outdated interface |
✅ Equipment module & tooling enable asset management |
|
✅ COTS (Components Off The Shelf) & fixtures |
|
✅ Time clock lets employees record clock-ins & clock-outs, and time-tracking is also available |
Price is set custom
From $650/monthly
7–8 users
Mind that there is a minimum 12-month contract.
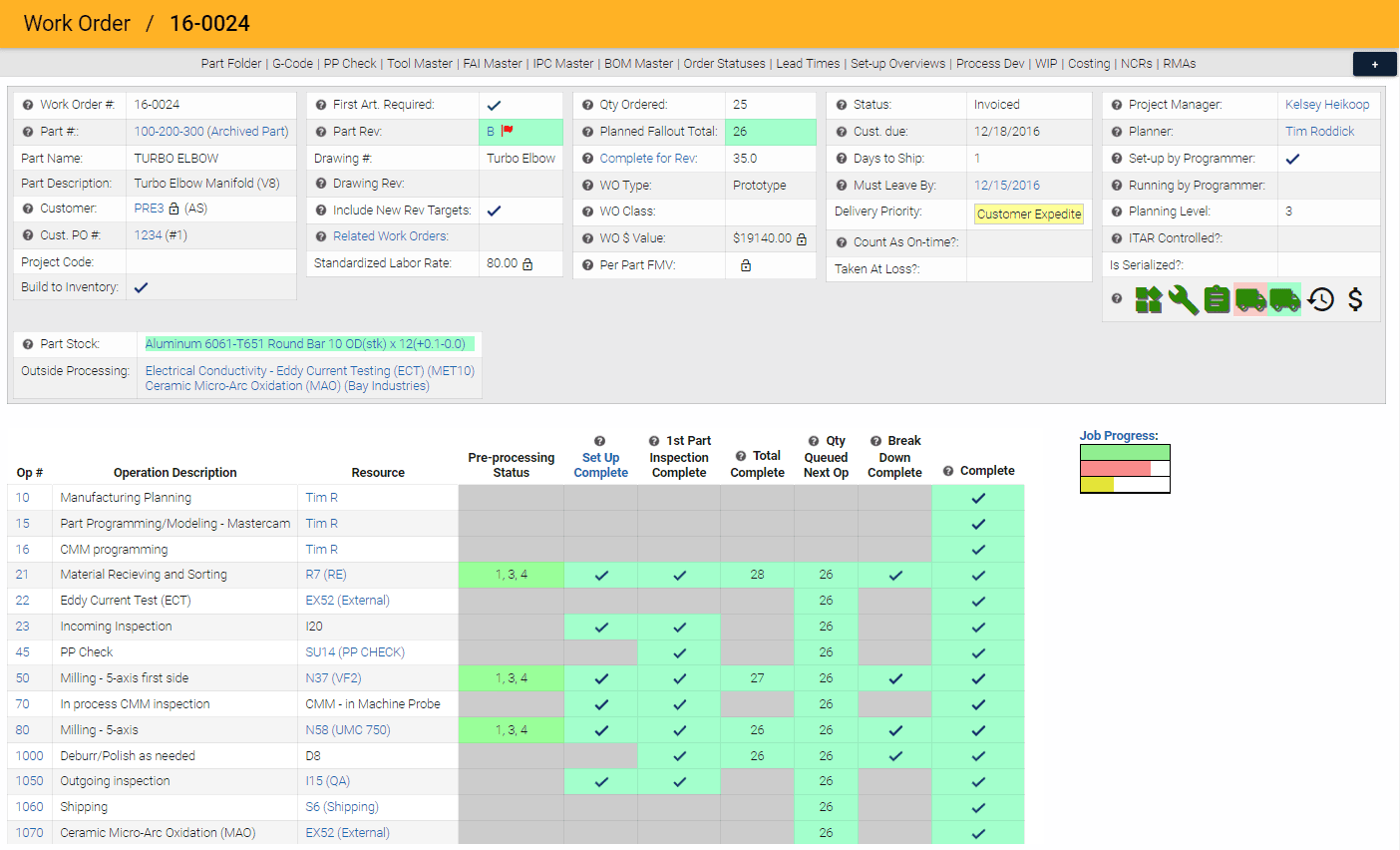
Prodsmart
Manufacturing management and production floor tracking solution that enables real-time production visibility.
Pros | Cons |
✅ Quality tracking & analytics |
❌ Some features are missing |
✅ Production orders auto-scheduling |
❌ Outdated interface |
✅ Equipment management, maintenance management |
|
✅ Free 14-day trial |
|
✅ Mobile apps for iOS & Android |
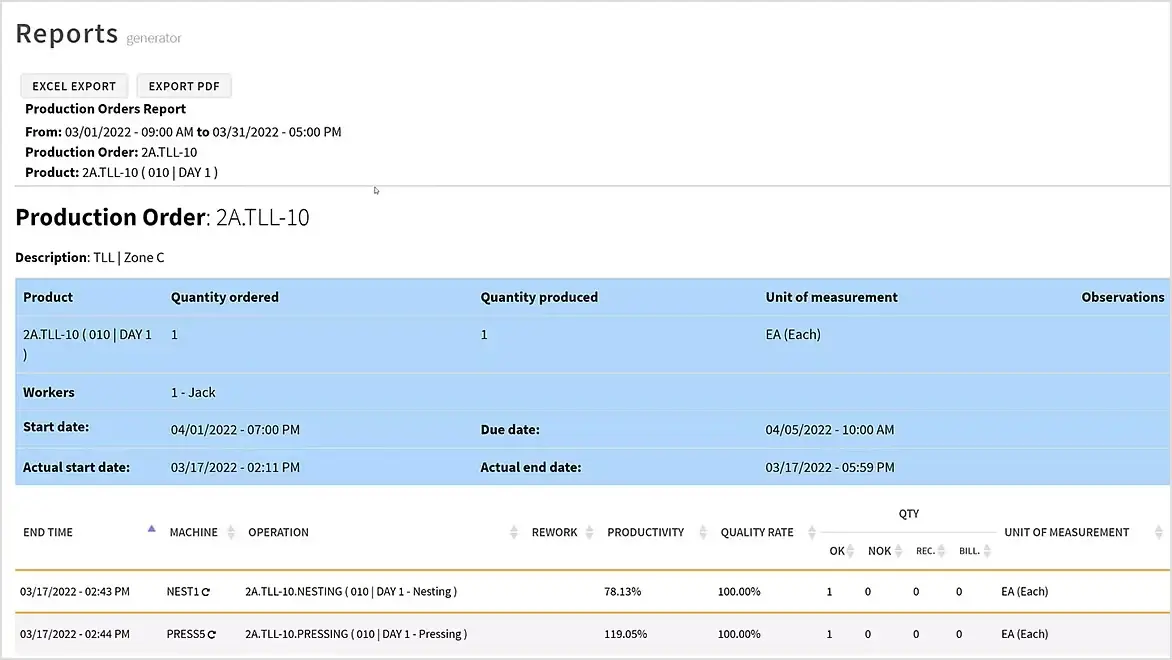
Global Shop Solutions
ERP software with a production module that helps simplify one’s manufacturing routines. Suitable for businesses with $10M‑1B in revenue and 20‑1,000 employees. Global Shop Solutions is a family business that is nearly 50 years old.
Pros | Cons |
✅ Scheduling, Shop floor data collection, quality check, tooling |
❌ Prices are not publicly disclosed, however, according to the target audience portrait, pricing is presumably high |
✅ Machines & equipment maintenance, engineering revisions |
❌ Outdated interface |
✅ Workcenters, workgroups |
❌ Not all features are available |
✅ Offers solutions for different industries: rubber, truck, concrete, electric vehicles, etc. |
|
✅ Integrations with FedEx, Magento, Woo, HubSpot, etc. |
|
✅ Additional resources: ERP training, manufacturing health test, Learning management system |
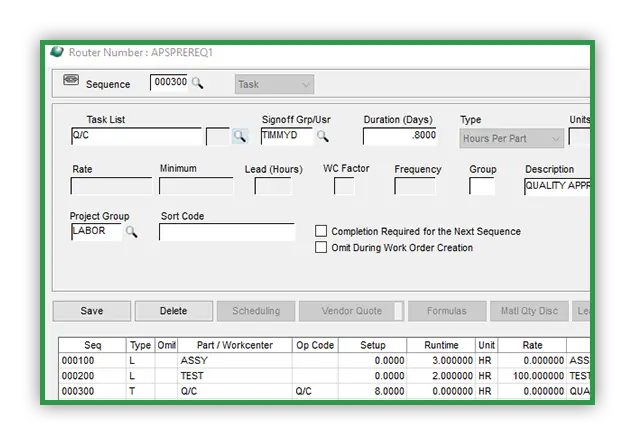
Genius ERP
A company from Quebec with 33 years of experience in manufacturing. The vast majority of Genius ERP customers are small & mid-sized companies. The software is said to be created and developed by manufacturing experts, mechanical engineers, and accountants.
Pros | Cons |
✅ Planning, execution & engineering |
❌ Pricing isn’t publicly disclosed |
✅ CAD designs can be transferred into BOMs |
❌ Some core features are missing |
✅ Integrations with Autodesk, Microsoft, Avalara, FedEx, etc. |
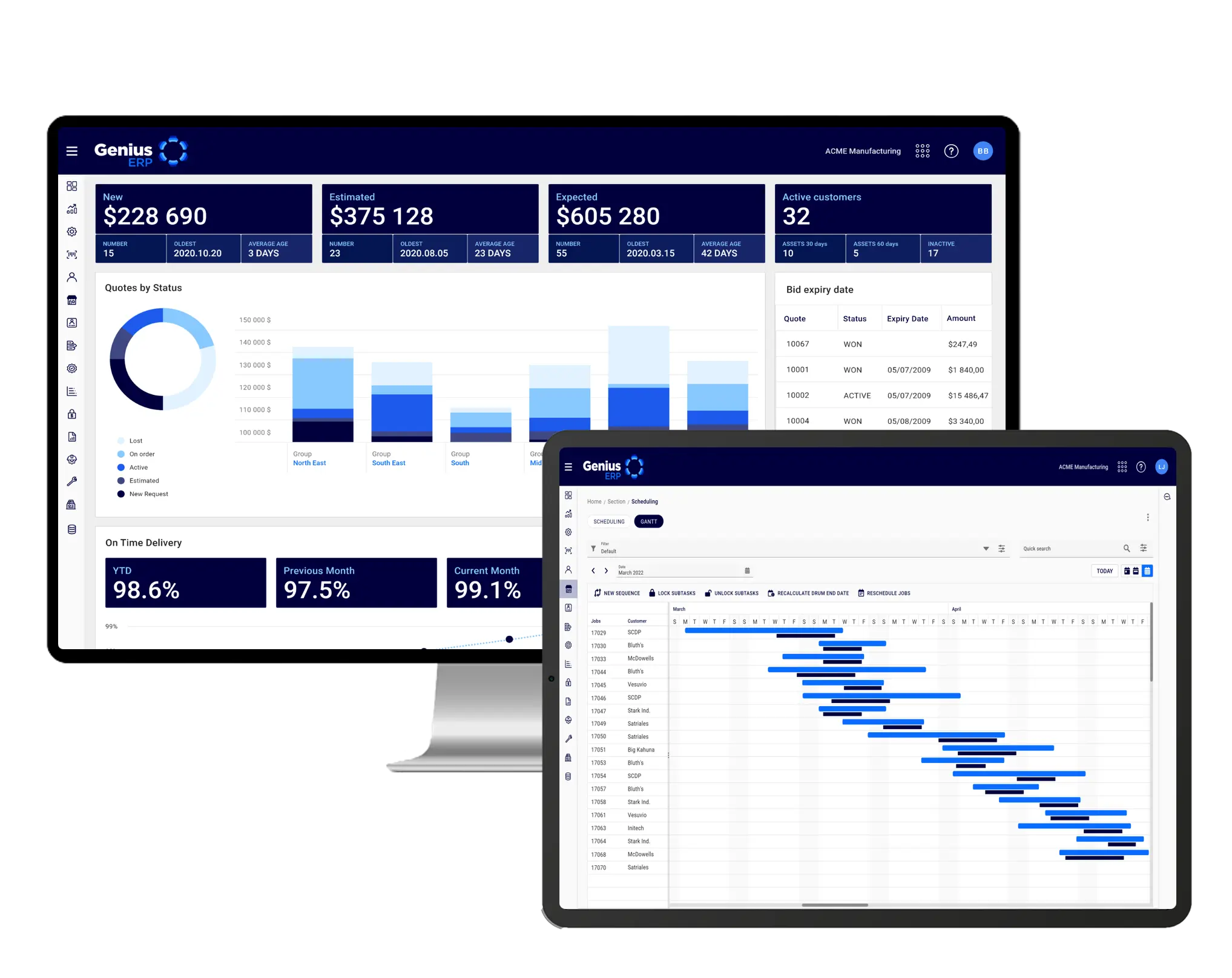
Frequently Asked Questions on Manufacturing Software
Prior to choosing manufacturing software, it’s advisable to learn the answers to common questions regarding these solutions.
How does manufacturing software work?
Manufacturing software streamlines and automates the production process. It integrates various operational functions like inventory management, order processing, production planning, and quality control. This allows for real‑time tracking of the manufacturing lifecycle, from raw materials to finished goods.
What are the 5 types of software used in manufacturing?
- ERP (Enterprise Resource Planning) for overall business management;
- MES (Manufacturing Execution Systems) for production control;
- PLM (Product Lifecycle Management) for product development and innovation;
- SCM (Supply Chain Management) for managing logistics and supply chains;
- CAD/CAM (Computer‑Aided Design/Computer‑Aided Manufacturing) for product design and manufacturing.
How to choose the best software for manufacturing business?
Identify your specific needs and challenges first. Consider scalability, compatibility with existing systems, and the software’s ability to integrate various manufacturing processes. Look for software with a user‑friendly interface, robust support, and training resources. Prioritize solutions that offer customization and can grow with your business.
What are typical manufacturing software features?
Key features include inventory management, production scheduling, quality control, maintenance management, and analytics for performance tracking. Other common functionalities are product lifecycle management, supply chain management, and customer relationship management (CRM) integration.
What is production management in ERP?
Production management in ERP involves overseeing all aspects of the manufacturing process within an integrated system. It coordinates raw material procurement, production scheduling, process optimization, and product delivery. This module ensures efficient production flow, aligning manufacturing operations with business objectives and customer demands.
What is MTO software?
MTO software, short for Made‑to‑Order software, is specialized in supporting businesses that produce goods only after receiving a customer’s order. This type of software helps manage custom orders, ensuring materials, production schedules, and delivery timelines are aligned with specific customer demands.