A parcel shipped to the wrong address. A batch of 1,000 T-shirts of the wrong colour stored in a warehouse as a result of confusion during receiving. Finished goods mixed up with raw materials. A label containing a retail price instead of a wholesale one. Employees looking up a particular variant of a product in a storeroom in a hurry without a clue if this product is on hand at all. All these are entrepreneurs’ nightmares that can come true if they neglect barcodes.
In this article, we’re going to tell how barcodes can be handy in your business, what the costs are, how to choose the right barcode inventory system — we’ve got 12 solutions, — and how to implement such a system in your company.
- Top 12 Barcode Inventory Software in 2025
- What is a Barcode?
- How does a Barcode work?
- What are the Pros & Cons of Barcode Usage?
- How Barcoding Appeared?
- What is a Barcode Inventory System?
- Is it Costly to Implement a Barcode Inventory System?
- What Factors to Consider while Choosing a Barcode Scanning System?
- What are the Core Features of Barcode Inventory Software?
- How to Implement a Barcode Inventory System in your Business?
- Frequently Asked Questions on Barcode Inventory Software
Top 12 Barcode Inventory Software in 2025
We analyzed the best software for barcode inventory management according to 16 parameters and created a handy table that can help you make an optimal choice.
The following information is based on companies’ sources: websites, help centers, social media, and support teams’ replies. The data is valid on February 13, 2024.
Software Name | Affordable | Supports | Types of Barcodes | |||||||||||||
Generation | Autogeneration | Import | Print Forms | Label Editor | Bundles & Batches | Scanning | Assets Tracking | EAN‑13 | EAN‑8 | Code‑39 | Code‑128 | UPC | QR Code | Data Matrix | ||
✅ |
✅ |
✅ |
✅ |
✅ |
✅ |
✅ |
✅ |
❌ |
✅ |
✅ |
❌ |
✅ |
✅ |
❌ |
❌ |
|
Zoho |
❌ |
✅ |
❌ |
❌ |
✅ |
✅ |
✅ |
✅ |
❌ |
✅ |
✅ |
✅ |
✅ |
✅ |
✅ |
✅ |
❌ |
✅ |
❌ |
✅ |
✅ |
❌ |
✅ |
✅ |
❌ |
❌ |
❌ |
❌ |
✅ |
❌ |
❌ |
❌ |
|
❌ |
✅ |
✅ |
❌ |
✅ |
❌ |
❌ |
✅ |
✅ |
✅ |
✅ |
✅ |
✅ |
✅ |
✅ |
✅ |
|
❌ |
✅ |
❌ |
❌ |
✅ |
✅ |
✅ |
✅ |
✅ |
✅ |
✅ |
✅ |
✅ |
✅ |
✅ |
✅ |
|
✅ |
✅ |
❌ |
❌ |
❌ |
❌ |
❌ |
✅ |
❌ |
✅ |
❌ |
✅ |
❌ |
✅ |
❌ |
❌ |
|
❌ |
✅ |
✅ |
✅ |
✅ |
✅ |
✅ |
✅ |
❌ |
✅ |
✅ |
✅ |
✅ |
✅ |
✅ |
✅ |
|
❌ |
✅ |
❌ |
✅ |
✅ |
✅ |
✅ |
✅ |
✅ |
❌ |
❌ |
❌ |
❌ |
❌ |
✅ |
❌ |
|
❌ |
✅ |
✅ |
✅ |
✅ |
✅ |
✅ |
✅ |
✅ |
✅ |
❌ |
✅ |
✅ |
✅ |
✅ |
❌ |
|
❌ |
✅ |
✅ |
✅ |
✅ |
✅ |
✅ |
✅ |
❌ |
✅ |
✅ |
✅ |
✅ |
✅ |
❌ |
❌ |
|
❌ |
✅ |
✅ |
❌ |
✅ |
❌ |
✅ |
✅ |
❌ |
✅ |
✅ |
❌ |
✅ |
✅ |
✅ |
❌ |
|
✅ |
✅ |
✅ |
❌ |
✅ |
❌ |
❌ |
✅ |
❌ |
✅ |
✅ |
✅ |
✅ |
✅ |
❌ |
❌ |
Kladana
A cloud-based software for inventory, sales, and production management with a 17-year-old history. It’s a reasonable solution for small & medium-sized businesses — wholesalers, distributors, and manufacturers. There is a free 14-day trial & a free price plan.
Kladana is easy to master — it takes 15 minutes only for a quick start. Kladana provides entrepreneurs with stable work, 1–3 onboarding sessions, and support with 5–15 minutes for a reply. One can use API to enable useful integrations. Also, we have integrations with accounting, e-commerce, and CRM solutions.
Pros | Cons |
✅ Affordable — from $60 a year (barcoding is available on Free plan) |
❌ Not suitable for large-scale businesses |
✅ Supports all main types of barcodes: EAN-13, EAN-8, Code-128 & UPC |
❌ Doesn’t support assets tracking |
✅ Barcodes generation, autogeneration, manual addition & .xsl files import |
❌ Doesn’t support 2D barcodes |
✅ Barcodes for products with variants, raw materials, finished goods, bundles, packaging & services |
|
✅ Numerous barcodes for one item |
|
✅ Thermal labels and price tags print forms to download, print, or send via email |
|
✅ Labels custom editing — you can you can set an item’s weight, picture, serial number, employees performed production operations, washing mode icons, etc. |
|
✅ Scanning (KBW) during receiving, shipment, transfer, and inventory counts |
Zoho
A complex tool for business management that has been on the market for 25 years. Zoho provides users with CRM & multiple mobile apps. The company is keen on privacy data. Barcodes are used for inventory tracking & document identification.
Pros | Cons |
✅ Has a label editor where you can add some fields |
❌ Expensive — from $130 a month (barcode generation, and batches & serial numbers tracking are available starting from Premium Plan) |
✅ Barcodes generation, autogeneration, manual addition & .xsl files import |
❌ Barcoding is a beta feature meaning there are limitations: barcodes for bundles can’t be printed or customized |
✅ Adding an item with a barcode in a sales & purchase order, an invoice, or a bill |
❌ Isn’t suitable for manufacturers |
❌ Doesn’t provide import |
|
❌ Doesn’t support autogeneration |
|
❌ Doesn’t provide asset tracking |
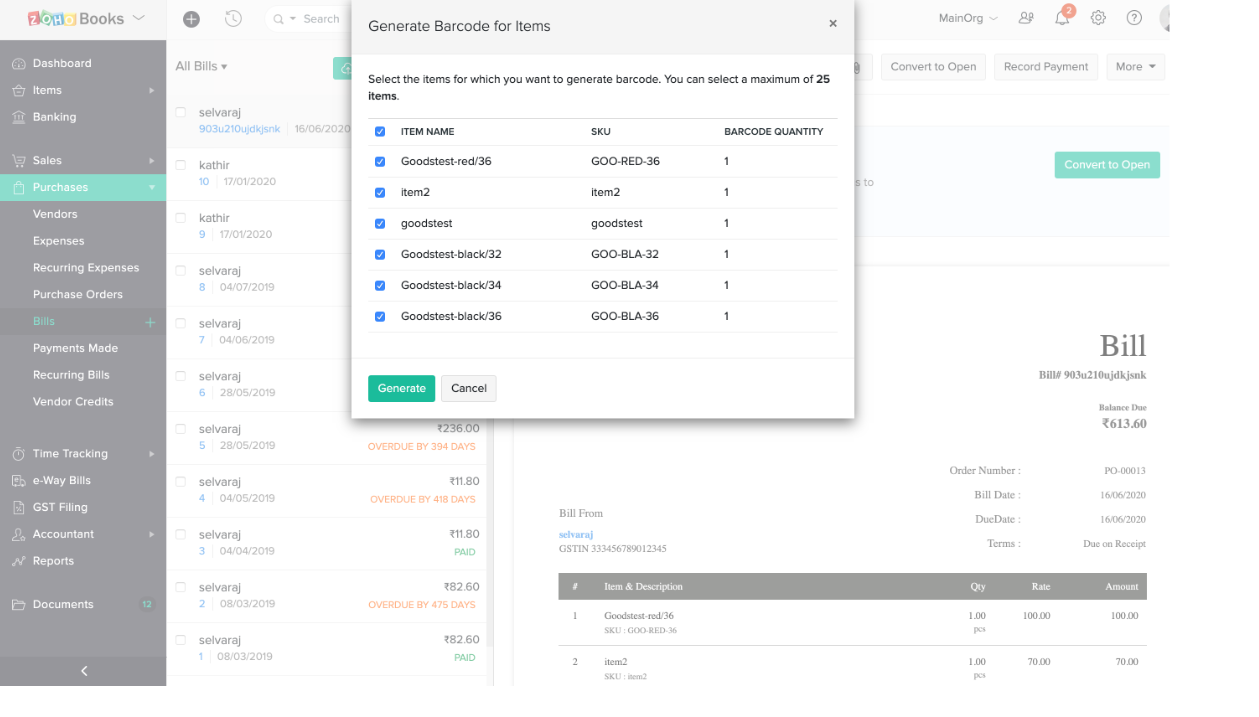
TranZact
Software designed for production management. Targeted at SME. Offers integration with Tally & Excel.
Pros | Cons |
✅ Barcode tracking system designs exactly for the need of manufacturers |
❌ Expensive — from $360 a month (barcoding and batch tracking are available only at Enterprise Plan) |
✅ Barcodes for items & batches |
❌ Isn’t suitable for large-scale businesses |
✅ Barcode reports indicating the available products with barcodes |
❌ Isn’t initially designed for wholesalers or distributors |
❌ Doesn’t support assets tracking |
|
❌ Doesn’t provide autogeneration |
|
❌ Doesn’t have full label editor |
|
❌ Supports Code-128 barcodes only |
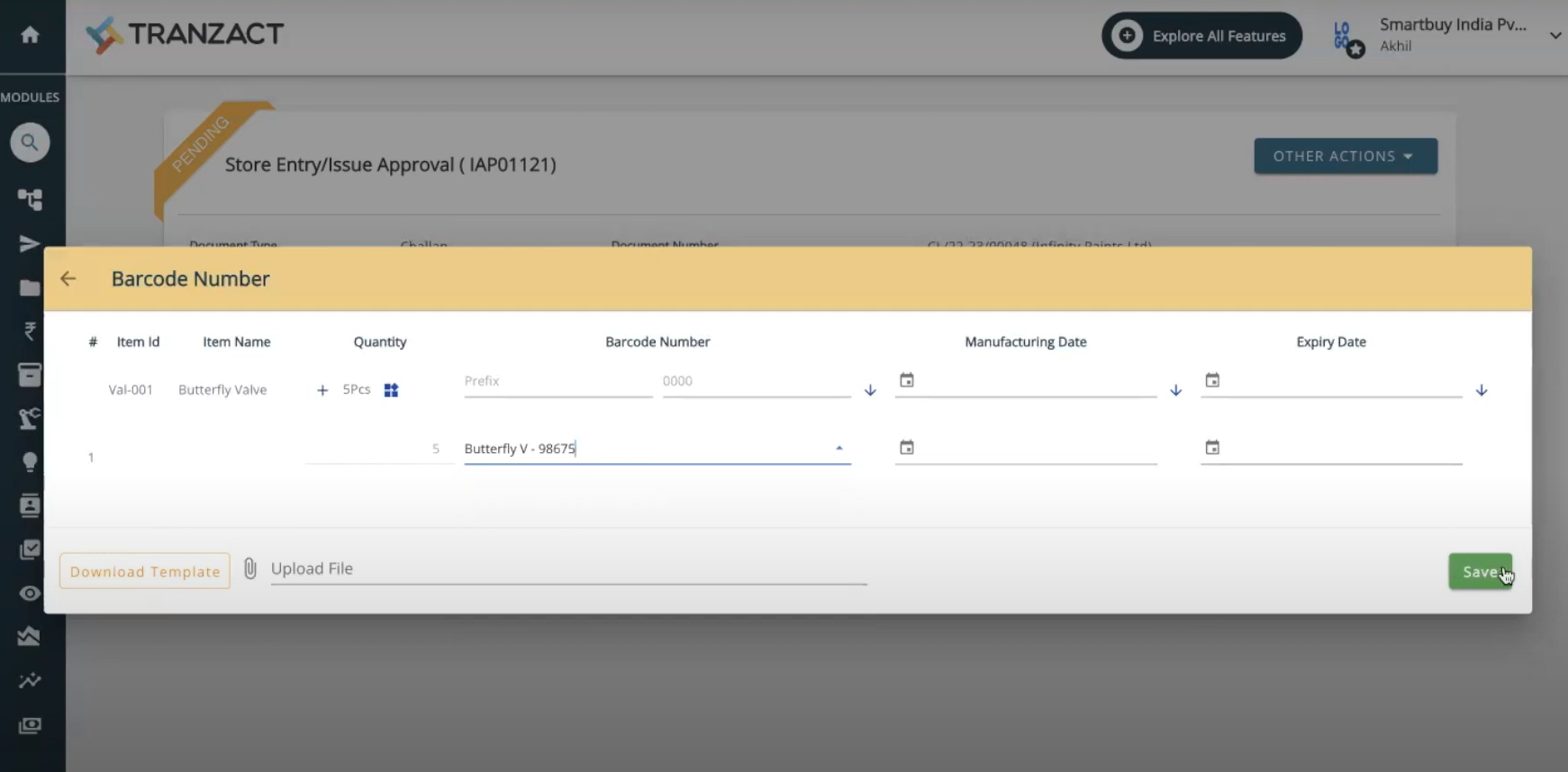
Deskera
Cloud software for managing production and warehouse operations. It is also helpful for accounting and HR management. Moreover, Deskera provides CRM and has integrations with 2,000+ applications.
Pros | Cons |
✅ Suitable for manufacturing — factory workers can generate barcodes for finished products |
❌ Expensive — from $1,000 a month |
✅ Barcodes creation for products, parts, or components |
❌ No import option |
✅ Inventory track with barcodes — the good’s location, the on-hand number, the date of production & sale |
❌ Doesn’t support bundles |
✅ Autogeneration & assets tracking is available |
❌ Doesn’t have a label editor |
✅ Barcode scanning provides automated billing processes & smooth shipment |
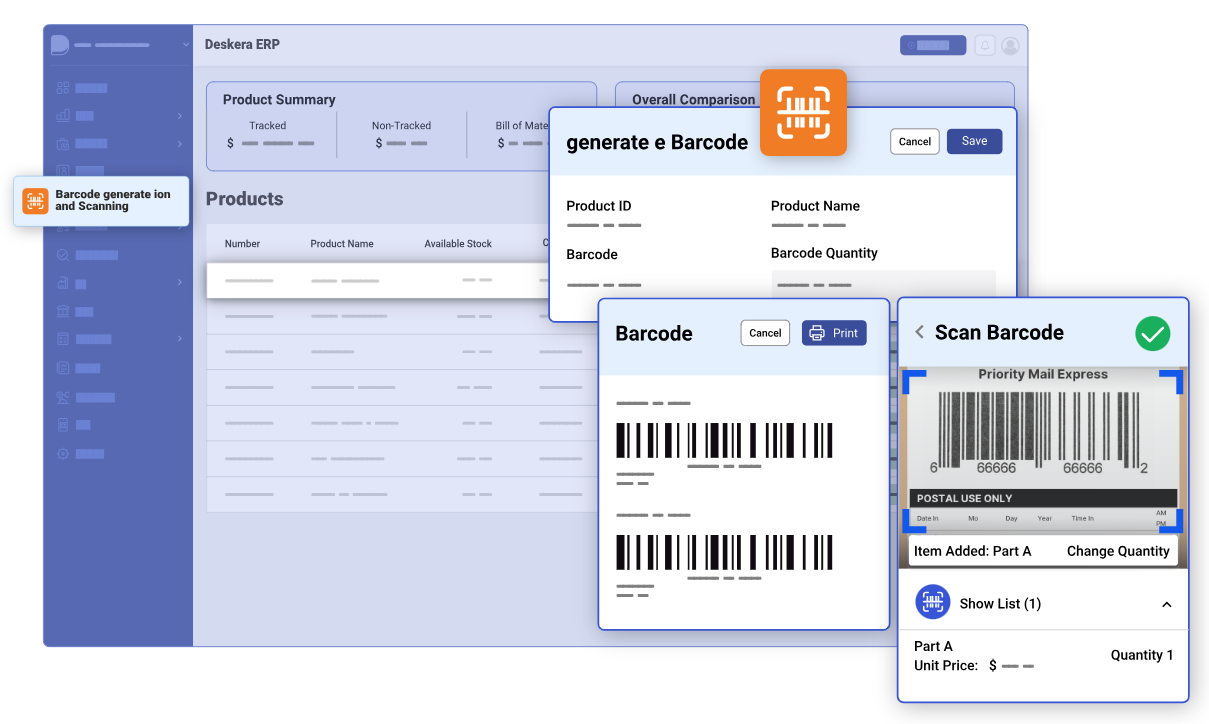
Read‑alikes
Free Inventory Management Software: Top 20 Solutions for Small Businesses
Inventory Management Guide for Beginners: Techniques, Challenges, Best Practices, and Trends
Inventory Counting: Step‑by‑Step Guide on How to Conduct and Access the Results
Inventory Management in Excel: Free Template and a Step‑by‑Step Guide
Sortly
Inventory management tool with a user-friendly interface. Barcoding helps track goods in stock, items in and out, supplies, and raw materials. It connects scanned goods to main info such as SKU, quantity, price, and location.
Moreover, Sortly offers custom solutions for various industries & API for integrations.
Pros | Cons |
✅ Support as in-app, as external scanners |
❌ Expensive — from $60 a month (barcode scanning and generation is available starting from Ultra plan) |
✅ Handy for managing assets: vehicles, tools, equipment, machinery, etc. |
❌ No autogeneration |
✅ Solution for different domains: education, jewelry, medicine, construction, etc. |
❌ No Excel files import |
✅ Supports QR codes as well as 1D barcodes |
|
✅ Offline mobile access for using Sortly in the field |
|
✅ Label editor: while printing barcodes, you can choose paper size & label size, include some item info (price, serial number, expiry date) & logo |
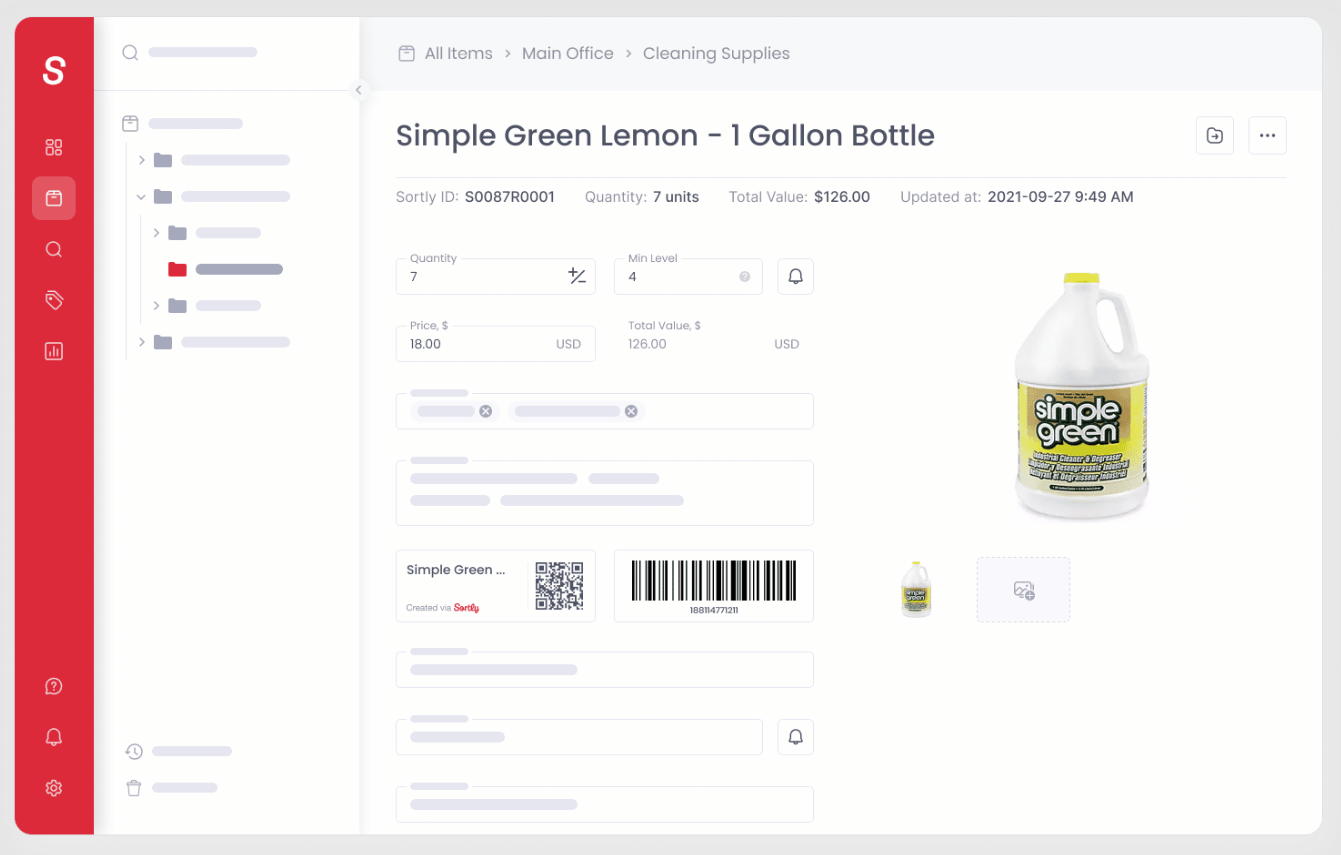
Vyapar
Billing & inventory management software with a barcode scanning solution helps to avoid long queues of customers at billing counters and keep accurate stock. Accounting and GST invoicing are big advantages of Vyapar.
Pros | Cons |
✅ Affordable — from $7 a month (a few free features are available fir the Android app only) |
❌ Suitable for retail rather than wholesale or distribution |
✅ Supports barcodes for inventory control and billing |
❌ Isn’t suitable for manufacturing |
✅ Saves time at billing counters: purchased goods can be scanned within seconds |
❌ You can’t perform any actions with barcodes rather than scanning & generation: there is no autogeneration, import, label editor, print forms, etc. |
✅ Suitable for online & offline retail stores |
❌ Supports limited types of barcodes |
✅ Support in-app and external scanners |
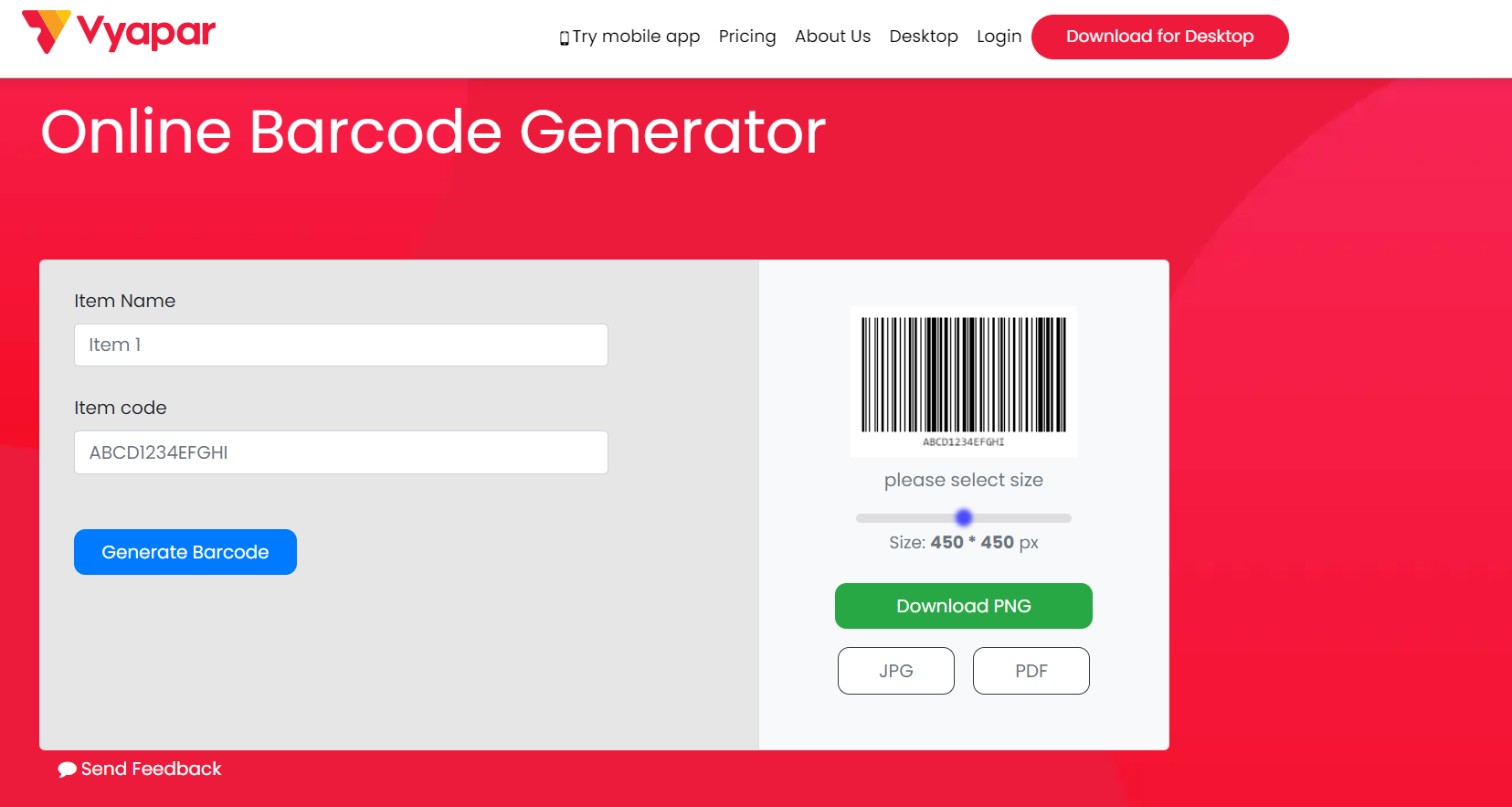
Katana
Cloud manufacturing software helps control production, inventory, and accounting. Enable fast and error-proof barcode tracking. Supports integrations with CRM, e-commerce, reports, and other tools. Provides API for custom integrations.
Pros | Cons |
✅ Designed precisely for manufacturers: use barcoding for raw materials and finished goods recording |
❌ Expensive — from $360 a month (barcode scanning is available starting from Standard plan) |
✅ Provides various barcode options: supplier item codes, internal barcodes for inventory & production management, and registered barcodes for retail |
❌ Isn’t suitable for wholesalers and distributors |
✅ Full label editor where you can customize a label according to your needs |
❌ No assets tracking |
✅ Multiple scanning devices options: USB & Bluetooth scanners, and mobile gadgets |
|
✅ Suitable for goods receiving and stocktakes, supports pick lists for accuracy |
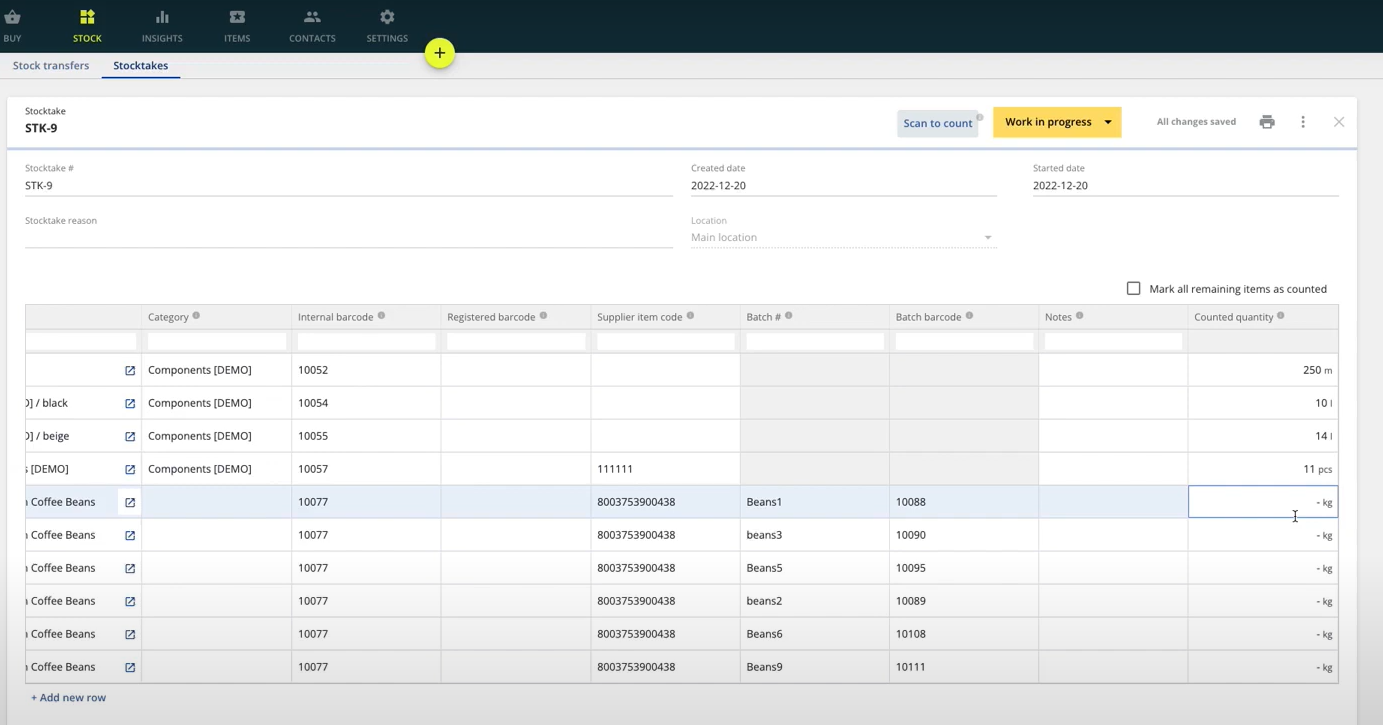
EZOffice
Asset-driven management software. One of the company products — EZOfficeInventory — enables entrepreneurs to process business operations, manage a team, and track equipment. Scan-based audits and stock reports are available too.
Pros | Cons |
✅ Focus on various assets (items, tools, equipment, locations) tracing, including usage, maintenance expenses, and depreciation |
❌ Expensive — from $35 a month (mind that bundles and packaging are available starting from Advanced plan which is more pricey) |
✅ Solutions for various industries: healthcare, education, construction, sports, events, etc. |
❌ Generates QR codes only |
✅ Availability to use a third-party scanner or EZOfficeI mobile application |
❌ No auto generation |
✅ Label editor where you can customize the layout and design. But as to barcodes, you must generate them on your own. |
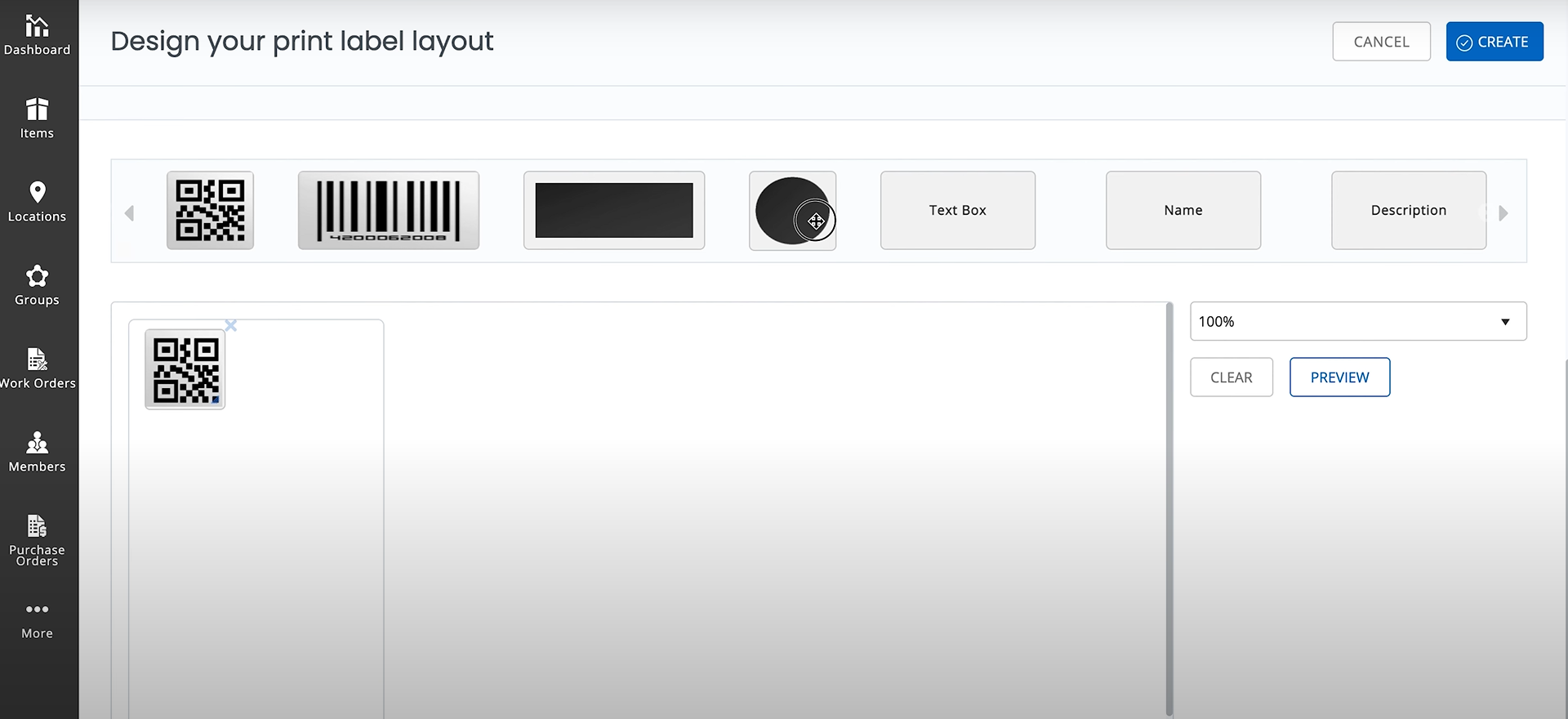
inFlow
Inventory software for managing stock and orders. Helps pick, pack, and ship orders from any device. The main focus is on the label editor.
One of the core features is working with B2B customers — inFlow can take online orders from them. Also, inFlow offers useful tools for manufacturers.
Pros | Cons |
✅ Suitable for manufacturers, wholesalers, and distributors |
❌ Expensive — from $90 a month (serial numbers are extra-chargeable) |
✅ Provides a comprehensive label editor where you can customize the design and content of a label |
❌ Doesn’t support EAN-8 and Data Matrix codes |
✅ Smart scanning via a mobile phone or any other external device |
|
✅ Scanning for picking up, receiving, picking, transfers, and stock adjustment |
|
✅ Assets tracking: equipment and supplies |
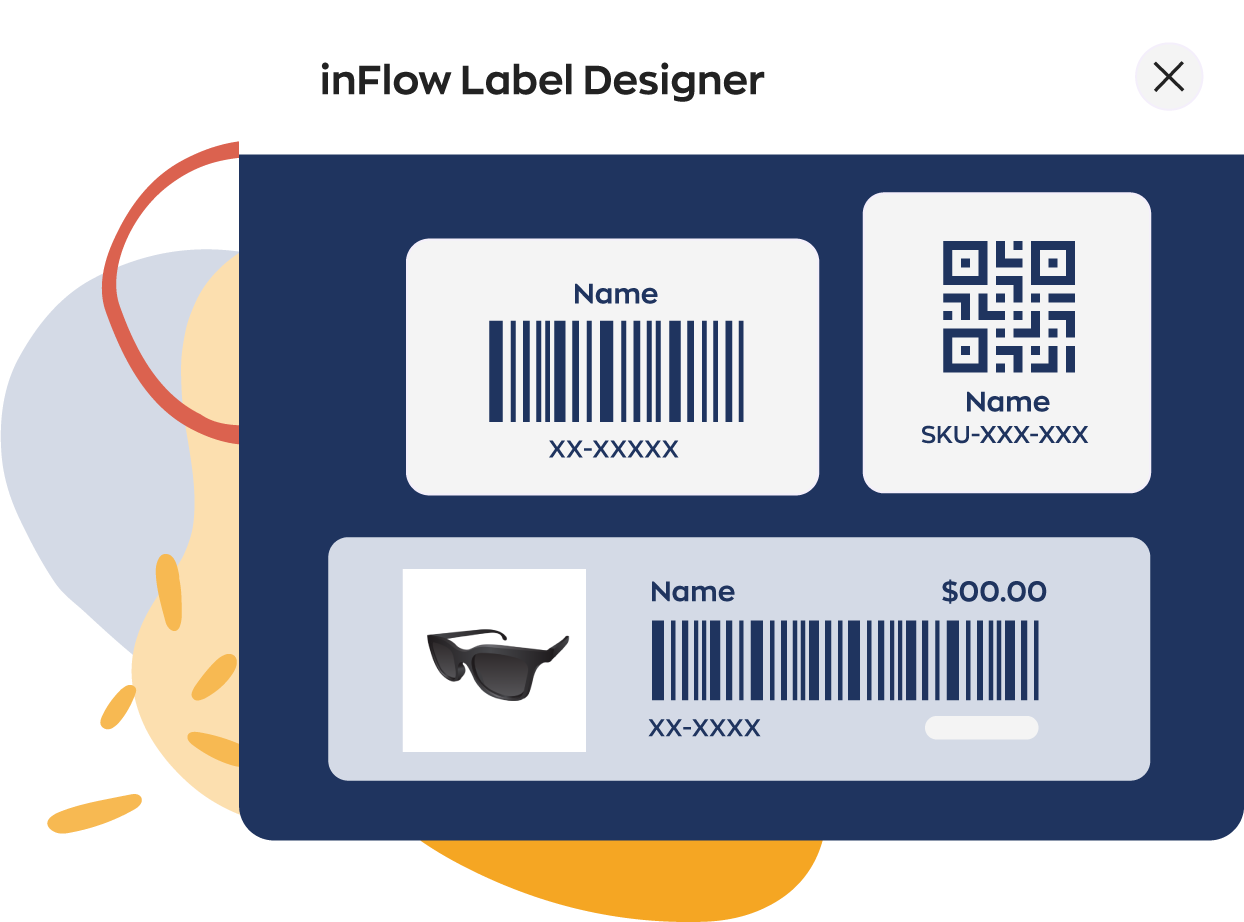
HandiFox
Inventory tracking & sales management software for small and medium businesses. Barcodes in HandiFox can be used for sales orders and invoices, and to pick and pack ordered items. The software provides tools for manufacturing and accounting.
Pros | Cons |
✅ Label editor for customization |
❌ Expensive — from $40 a month (serial numbers are available starting from Pro Plan which is quite pricey) |
✅ Scanning via a smartphone or a Bluetooth-enabled scanner |
❌ Doesn’t allow tracking assets |
✅ Barcoding for inventory counting, transfers, purchases, and sales |
❌ Doesn’t work with 2D barcodes |
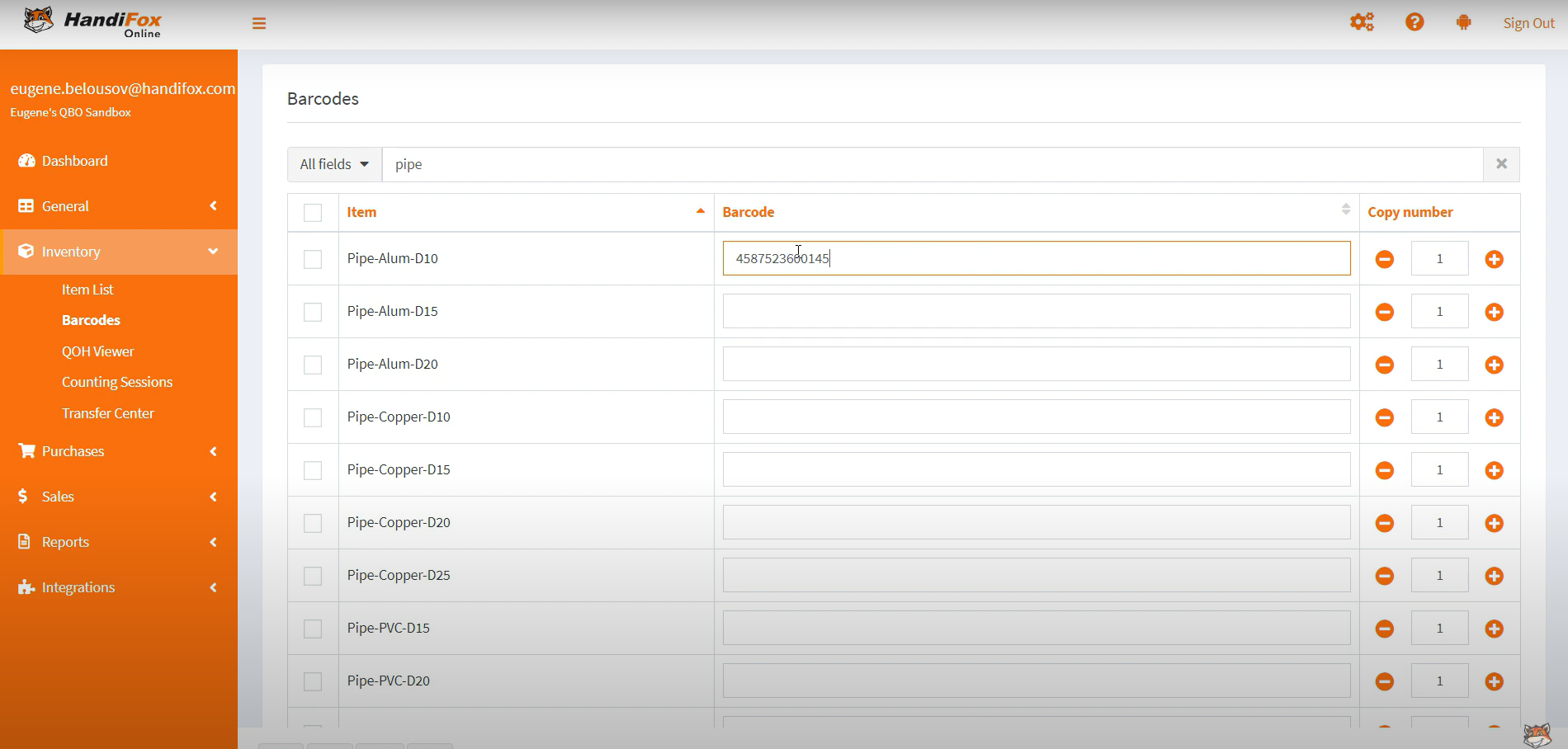
Mintsoft
Order fulfillment software for online retailers, warehouses, and third-party logistics companies. Helps one’s employees to pick, pack and manage stock with ease. Provides 150+ integrations.
Pros | Cons |
✅ Mobile barcode scanner with bulk batch picking, multi-tote & single tote |
❌ Expensive — from $420 a month (mobile barcode scanning is available starting from Medium plan) |
✅ Suitable for wholesalers and distributors |
❌ Isn’t suitable for manufacturers |
✅ Autogeneration & print forms are available |
❌ Doesn’t support import |
❌ Doesn’t have a label editor |
|
❌ Doesn’t support many types of barcodes |
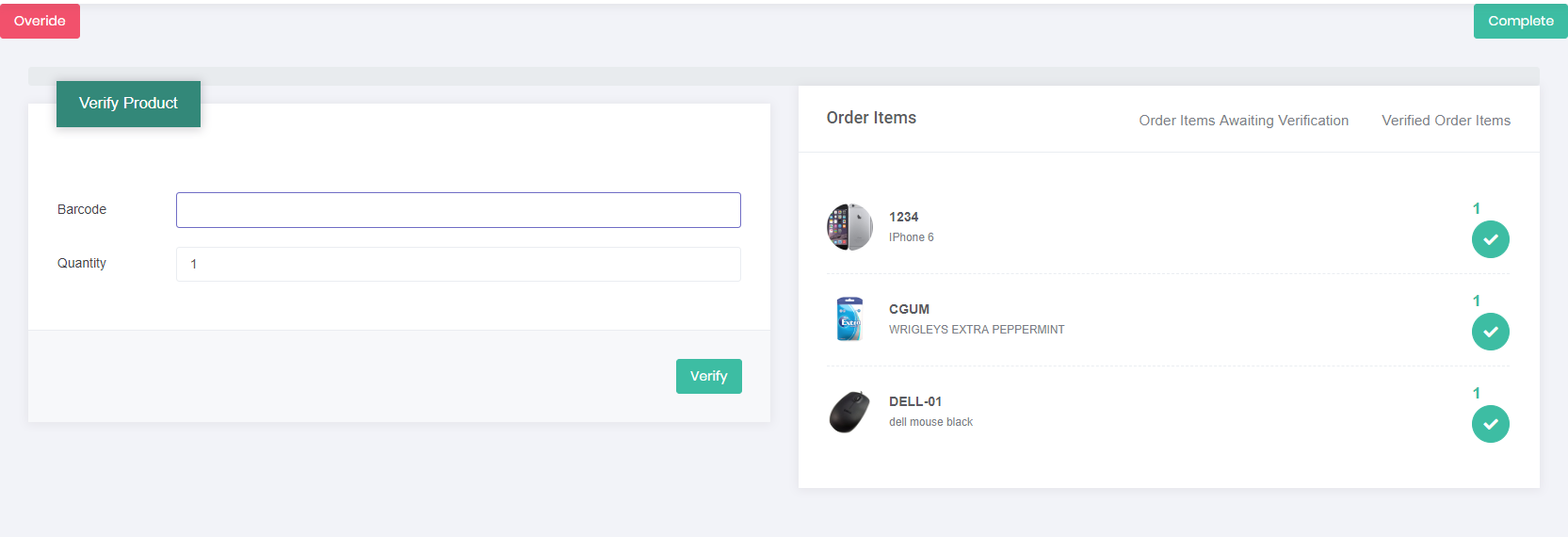
Salesbinder
Inventory software system for any company purchasing and selling products. Helps generate and scan barcodes to deal with sales & purchase orders, and invoices.
Pros | Cons |
✅ Affordable — from $10 a month (barcoding is available on Free plan) |
Isn’t suitable for manufacturers |
✅ Can automatically display barcodes on documents |
❌ Provides generation, autogeneration, and printing of barcodes for documents only (e.g. packing lists), not for goods or packaging |
✅ Supports main types of barcodes for scanning |
❌ Doesn’t have a label editor |
❌ Doesn’t support Excel import |
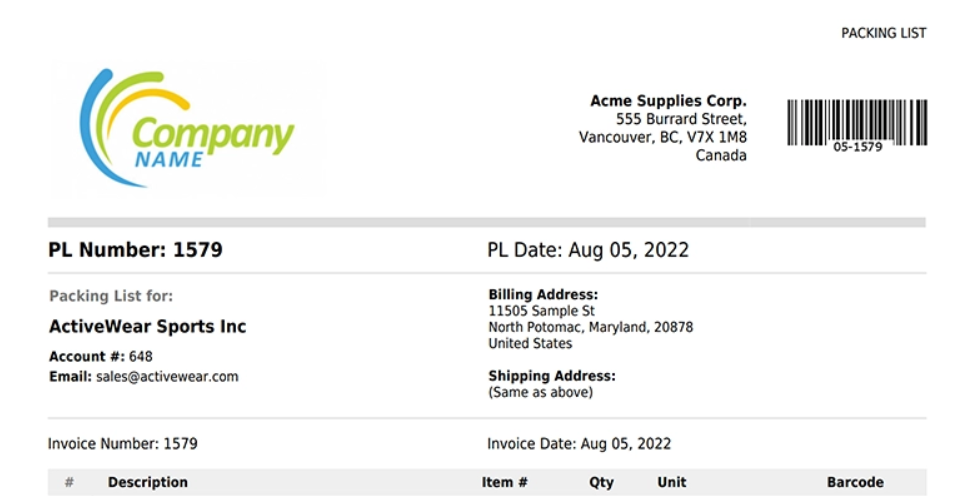
What is a Barcode?
Visually, a barcode is a combination of lines, spaces, digits, and letters. A QR code consists of dots, squares, and other symbols. A barcode represents a digital code containing information about a product, packaging, document, or location. The data is usually the following: price, currency, weight, size, colour, etc.
Barcoded can be scanned via hardware (scanning devices) or software (smartphones & tablets). Barcodes can be generated via various platforms including Kladana and other solutions.
How does a Barcode work?
All the lines, digits, and dots of barcodes represent a unique cipher that can be scanned. Thus a person gets some data regarding the exact object containing a barcode. In wholesale and manufacturing business, this info is extremely helpful to keep inventory in order to conduct inventory counting, receiving, and shipment.
To put it simply, a barcode is a digital ID card belonging to an object. Without this ID card, there would be chaos, disorder, and multiple mistakes in shops, warehouses, and production facilities.
What’s the Difference between UPC & SKU?
UPC is an abbreviation for Universal Product Code, as SKU is Stock Keeping Unit. They both are barcodes but exist for various purposes. In short, UPC is for contacts with external counterparties (customers & suppliers), and SKU is for internal usage (warehouse storage, transfers, stock-taking, etc.).
UPC barcodes are maintained by GS1 organization. If manufacturers wish to sell their goods using UPCs, they register with GS1. Afterward, they are assigned a company prefix. A product number and a check digit follow this prefix.
SKUs are used by wholesalers, distributors, and retailers, They can be created manually or via software. SKUs may contain various info: size, colour, material, manufacturing date, washing modes icons, etc.
What’s the Difference between 1D & 2D Barcode Types?
Typically, 1D barcodes are used for storing data on items, and 2D barcodes are commonly utilized on packaging and documents.
1D Barcodes
They keep basic data on a product and consist of lines, spaces, digits, and letters. Let’s take a look at examples of the most widely-spread 1D barcodes.
Barcode | Description | Sample |
EAN‑13 |
European article number consists of 13 digits. One of the most commonly used barcodes in retail and at the points of sale. |
|
EAN‑8 |
A shortened version of EAN-13 that consists of 8 digits. The first two digits identify the country, the next five ones indicate the product, and the final digit is a check number. EAN-8 is used on small goods to save space on packaging: e.g. candies, and chewing gums. |
|
Code‑128 |
This barcode gained popularity due to the versatile info it can indicate. It’s usually used for warehouse management: storage, purchasing, and shipping. It can encode digits, letters, and control characters such as Tab, Enter. |
|
Code-39 |
Widely spread in the automotive and pharmacy industries. It can consist of 43 characters maximum. |
|
Code‑93 |
A more secure and compact version of Code-39. |
|
UPC‑A |
Universal Product Code is mostly commonly used in the USA and Canada in grocery stores and retail chains. It consists of 12 digits. The first digit indicates the item code: a product, a coupon, or a weighted good. The next five digits indicate the manufacturer’s number, the following five ones index a product number, and a check digit is the last one. |
|
UPC‑E |
A shortened version of UPC-A. It’s used for small products. UPC-E consists of 6 digits. |
|
Samples are provided by Matthews Australasia, Cognex, Accusoft, and ActiveBarcode.
2D Barcodes
They keep extensive data on packaging, a document, or a product and can link to a website, video, audio, an image, or other media content. 2D barcodes consist of dots, squares, rectangles, and other shapes. Let’s take a look at examples of the most widely-spread 2D barcodes.
Code | Description | Sample |
QR Code |
Quick Response code is a well-known type of 2D barcodes. Usually, it opens a website, an app, or a menu and can be scanned with a smartphone camera. It can consist of 7,000 characters. |
|
Data Matrix |
It’s often used for electronic & jewelry parts, food & beverage packaging, and printed media. Also, it’s utilized in the aerospace, pharmaceutical, and automotive industry. Data Matrix can consist of 2,300 characters. |
|
MaxiCode |
It’s most commonly used for packaging and shipping. MaxiCode can consist of 90 characters. |
|
Aztec |
It’s used in the travel domain for airline tickets and in hospitals. It owes its name to its resemblance to the Aztec pyramids. Aztec can consist of 3,800 characters. |
|
PDF417 |
It’s used in manufacturing, the transport industry, and for ID documents. PDF417 can consist of 800 characters. |
|
Samples are provided by Matthews Australasia, Cognex, and Softmatic.
What are the Pros & Cons of Barcode Usage?
Benefits | Disadvantages |
✅ Accurate inventory that is always in order: when every item has its identification number, you get a full picture of your stock instead of approximate info stored on random Excel sheets, pieces of paper, and mental notes. |
❌ Setup time. You need to spend enough effort and time to select a suitable barcode inventory system, implement it in your company, and educate your employees to use it. However, you have to do it only once. |
✅ Reduced human-made mistakes. Manual data entries inevitably cause recurring errors that can bring about troubles with sales, supplies, and production. |
❌ Initial costs. While keeping inventory in order may save you money in the future, the vast majority of barcode inventory systems are not free and you’ll have to pay from $7 up to $100 a month. And don’t forget that you have to purchase hardware for scanning and printers to print thermal labels and price tags. |
✅ Saved time. Manual inventory counting causes mistakes and hours or even days spent. While scanning barcodes and calculating items digitally, you save time of your employees for other important tasks. |
❌ Equipment maintenance. Hardware must be checked regularly and repaired if needed. As to the software, malfunction or errors may occur from time to time. |
✅ Reduced losses caused by mistakes and theft. |
|
✅ Real-time reports and immediate changes that streamline business growth without a postponed effect. |
How Barcoding Appeared?
Barcodes were invented in 1948 by two American students. They wanted to improve inventory management for a supermarket chain. Inspired by Morse code, students drew concentric circles in the sand.
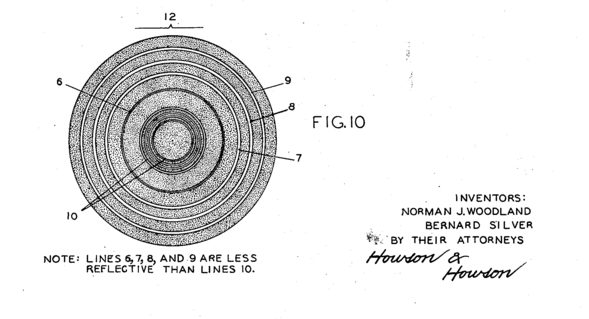
In 1961, linear barcodes were used for the first time by American Railroads to identify cars in motion, and then for full inventory control. In 1973, the Committee on Uniform Grocery Product Core recommended using barcodes on most goods in the USA. A year later, the first scanning system was invented in Ohio, and a pack of Wrigley’s gum became the first product whose UPC barcode was commercially scanned.
Laser scanners appeared in 1986, and QR codes — in 1999 in Japan. In 2005, airlines started printing barcodes on passengers’ boarding passes.
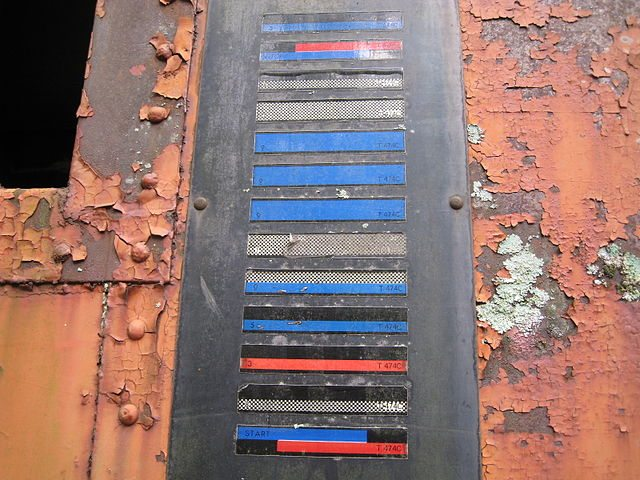
What is a Barcode Inventory System?
A barcode inventory system is a system that uses 1D and 2D barcodes and barcode scanners for inventory management and item tracking. The combination of hardware and software barcoding components is used to automate business processes. Thus entrepreneurs can be aware of the product’s location, quantity, price, variants, etc.
Barcode inventory systems are used in manufacturing, warehouse management, shipping, receiving, inventory counting, and for asset tracking.
What Software and Hardware Components are Included in a Barcode Inventory System?
Barcode generators, mobile scanners, label templates, serial number trackers, and inventory management solutions comprise barcoding software. In terms of hardware, stationary and handheld scanners, thermal label printers, and thermal paper are common components of barcoding technology.
Software Components
- Barcode generator. There are plenty of free tools available. However, it will take you a long time to generate barcodes for all goods and to record them in Excel sheets. Using the software, you can generate barcodes automatically.
- Mobile barcode scanner. Thus you can scan barcodes using your smartphone or tablet. The drawback is that such systems are not always precise, and mistakes occur.
- Standard and customized label templates. Again, you can use free tools but mostly they don’t allow you to add custom fields and make necessary amendments. Using proper software, you can design ideal labels on your own.
- Serial number tracker. This will help you indicate an item not only with a barcode but also with a unique serial number.
- Inventory management software. Generating and scanning barcodes isn’t all. In order to have full control of your stock, you need complex inventory management software that provides barcoding features.
Hardware Components
Stationary scanner It’s usually used in supermarkets to check out customers. |
|
Hand-held scanner It’ll be easier for your employees to hold such compact devices during stock-taking, shipment, receiving, etc. In order to be completely mobile, use wireless devices. However, one shouldn’t forget to charge them. USB scanners don’t need to be charged but employees lack portability. |
|
Thermal label printer and thermal paper Handy to print thermal labels and price tags. |
|
Pictures are provided by Zebra.
Is it Costly to Implement a Barcode Inventory System?
If you want to avoid expenses on software, you’ll still need to buy hardware. A hand-held scanner costs $25–120, a stationary one — $120+, a thermal label printer — $120–250, and thermal paper — about $0.5 per roll.
As to a barcode inventory system, you’ll find precise prices in Top 12 Barcode Inventory Software in 2025 section. In general, the most affordable solutions would cost you from $7–10 per month, the average price is $40–120, and the most expensive solutions cost up to $1,000. If you select a yearly subscription, it’ll be cheaper than a monthly one.
What Factors to Consider while Choosing a Barcode Scanning System?
- Business goals. Ponder what you need barcoding for: to conduct inventory counting quicker, to reduce costs and losses, to avoid recurring mistakes, or to manage manufacturing.
- Business tasks to solve. Haven decided on purposes, and think of certain tasks. To generate & scan barcodes, and to print thermal labels — are these features enough? Or maybe you need barcodes to be autogenerated and thermal labels customized to your needs?
- Financial capacity. Consider how much you are eager to spend on hardware. If you hesitate regarding software, you can start with free tools or free trial software periods — about a fortnight.
- Setup time. Reflex in time your team and you need to opt for a platform, implement it, and learn how to use it.
What are the Core Features of Barcode Inventory Software?
- Barcode generation and scanning. Make sure that software supports all the types of 1D or 2D barcodes you need and is able to generate and autogenerate them.
- Label customizing. If you want to add your own fields such as colour, size, and logo you need a label editor option.
- Quick and simple info import is required. If you want to smoothly upload Excel files containing items with barcodes, you need this feature.
- Access for several users. If you are going to grant access to your employees, look for a platform with plans supporting good synchronization of actions made by a few users at a time. Also, you should be able to set up roles and allow and deny certain actions to particular users.
- Cloud-based application. Thus all necessary information will be stored in the cloud. You won’t lose significant files.
How to Implement a Barcode Inventory System in your Business?
Step 1. Decide a type of barcode you need for your business. This will also help you choose the proper software which supports the necessary types. Consider what you are going to use barcodes for (finished goods, raw materials, products with variants, packaging, location) and information that has to be included in barcode data (price, currency, logo, size, manufacturing date). See the description and examples of the types.
Step 2. Select proper software and hardware based on your budget, time, and other resources.
Step 3. Create a roadmap with a timeline — decide what actions with what deadlines and who is going to do in order to start using barcoding for your business. If you use hardware only, ensure to generate a bunch of barcodes and put them into your inventory Excel sheet.
If you use software, import your items, generate barcodes for products and bundles, and apply necessary settings as autogeneration. Customize your labels, and print relevant thermal labels, price tags, and documents containing barcodes.
Step 4. When you finish testing your barcode system, educate your employees.
Step 5. After some time, assess how your new system is functioning. Did you meet your initial goals? Do you lack some features? Would you like to change something? Conduct such revisions on a regular basis to check if everything works smoothly.
Learn more about the barcode inventory system for manufacturers and wholesalers in Kladana.
Import, generate, and autogenerate GTIN, EAN-13, EAN-8, Code-128 & UPC barcodes. Scan barcodes, design custom thermal labels, and print them.
All this together with a comprehensive inventory, warehouse, and production management system at an affordable price starting from $60 a month.
Frequently Asked Questions on Barcode Inventory Software
Let’s focus on common questions people usually ask about barcoding and inventory management software.
What is a barcode?
A barcode is a method of representing data in a visual, machine‑readable form. Typically, barcodes represent data by varying the spacings and widths of parallel lines, or sometimes patterns of squares or dots. This data can then be scanned and interpreted by barcode readers to retrieve the information encoded within such as product type, size, and manufacturer.
How do you track inventory with a barcode?
Tracking inventory with a barcode involves assigning a unique barcode to each item or SKU in your inventory. When items are received, sold, or moved, their barcodes are scanned using a barcode scanner. This updates the inventory levels in a database or inventory management system in real time, allowing for accurate tracking of stock quantities, locations, and movements.
How do I create a barcode for my inventory?
To create a barcode for your inventory, first, decide on the type of barcode format (e.g., UPC, EAN, QR code) that best suits your needs. Then, use barcode generation software or online tools to generate barcodes for your items. Each item or SKU will need a unique code that corresponds to its information in your inventory system. Print these barcodes on labels and affix them to the respective items.
What is the best barcode for inventory management?
The best barcode for inventory management depends on your specific needs. For most retail and inventory purposes, UPC (Universal Product Code) and EAN (European Article Number) barcodes are widely used for their universality and efficiency. For more complex needs or larger amounts of data like batch numbers or expiration dates, QR codes may be preferred.
What is the barcode inventory system?
A barcode inventory system is a technology‑based method that uses barcodes to identify, track, and manage inventory levels. It involves scanning barcodes to record the movement of inventory through receiving, storing, and selling, helping businesses maintain accurate stock counts.
How to choose the best barcode inventory system?
Choosing the best barcode inventory system involves evaluating your business’s specific inventory needs, the volume of transactions, the complexity of your inventory, and your budget. Look for systems that integrate well with your existing operations, offer scalability, and provide robust reporting and tracking features. Consider also the system’s ease of use and the quality of customer support. Also, evaluate user reviews and cost‑effectiveness.
How to implement a barcode system for inventory?
Implementing a barcode system for inventory involves several steps:
- Choose the right barcode format and inventory software;
- Generate and print barcode labels for your inventory items;
- Input information on these barcodes into the inventory system;
- Train staff on how to use barcode scanners and the inventory software;
- Start scanning to record inventory data;
- Set up regular processes for scanning items during transactions and stock movements to maintain accurate data;
- Continuously monitor and refine the process for efficiency.
What are the best practices for barcode inventory systems?
Best practices for barcode inventory systems include:
- Ensure all items are clearly labeled with barcodes that are easy to scan;
- Keep your barcode database updated with accurate product information;
- Train staff thoroughly on the correct procedures for scanning and handling items;
- Perform regular audits and cycle counts to verify the accuracy of the inventory data;
- Utilize the data collected through the barcode system for analytics and decision‑making;
- Use high‑quality labels and printers to ensure barcodes are scannable.
What is the future of barcode inventory systems?
The future of barcode inventory systems may involve more advanced technologies like RFID (Radio Frequency Identification), which allows for non‑line‑of‑sight scanning and can handle multiple scans simultaneously, improving efficiency. Integration with AI and machine learning could provide predictive analytics for inventory management. Additionally, improvements in mobile technology and apps may further streamline inventory management processes, making them more accessible and cost-effective for businesses of all sizes.