ABC analysis, a powerful inventory classification technique, helps prioritize stock by dividing it into three categories based on value and impact. This method enables SMBs to focus on their most important items, optimize resources, and reduce inefficiencies. When integrated with cloud‑based ERP systems, ABC analysis can be automated, making inventory control smarter, more efficient, and aligned with long‑term business growth.
What is ABC Inventory Analysis?
ABC analysis is a strategic inventory management technique that classifies stock into three categories based on its value to the business. This approach helps companies prioritize their efforts on the items that have the greatest impact on inventory value, leading to more efficient use of resources. Items are grouped into three categories: A, B, and C. Category A consists of high‑value products that generate the most revenue. Category B includes moderately valuable items, while Category C covers low‑value stock. By understanding these classifications, businesses can allocate their time, money, and attention where it matters most.
For small and medium‑sized businesses (SMBs), this method is particularly beneficial, as it simplifies inventory management and supports informed decision‑making. Rather than treating every item equally, ABC analysis encourages a targeted approach, helping businesses avoid overstocking low‑priority items and understocking critical ones. Integrated into an ERP system, this process can be automated, allowing for real‑time tracking and adjustment.
The A, B, and C Categories Explained
- Category A: These are the high‑value items, typically making up 70‑80% of total inventory value but only around 10‑20% of the total stock. Managing this category closely is essential to maintain profitability.
- Category B: This includes mid‑range value items that represent about 15‑25% of inventory value and require moderate attention to ensure they don’t become bottlenecks in operations.
- Category C: Low‑value items that make up the bulk of stock (around 50‑60%) but contribute only a small percentage to the overall value (about 5%). They require minimal oversight but need to be replenished frequently.
Why ABC Analysis Matters for SMEs
Implementing ABC analysis allows SMEs to optimize their resources by focusing on high‑value items that significantly impact revenue. This method supports efficient stock control, reducing excess inventory of low‑value items and freeing up capital.
For SMEs operating with limited budgets, ABC analysis also aids in better decision‑making by highlighting where investment in stock should be concentrated. Integrated with ERP systems, this approach can be automated, providing real‑time insights that help businesses respond faster to changing demand, minimize waste, and improve overall profitability.
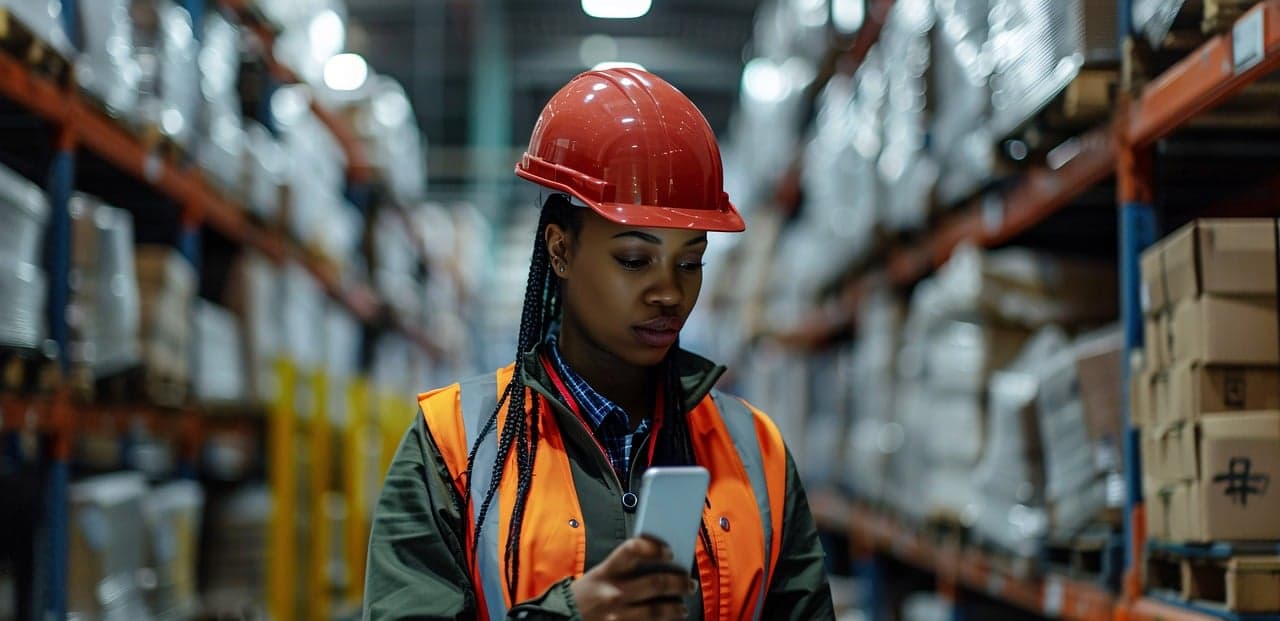
How ABC Analysis Optimizes Inventory Management for SMEs
ABC analysis offers small and medium‑sized businesses (SMBs) a powerful way to streamline inventory management. By focusing on high‑value items, businesses can significantly reduce costs and improve stock forecasting. Instead of spreading resources thinly across all products, SMBs can strategically manage inventory, ensuring that critical items are always available, while low‑priority items don’t accumulate unnecessarily. This targeted approach minimizes waste, optimizes resource use, and enhances overall inventory control.
Improved Inventory Control
ABC analysis provides a structured way to manage inventory levels by focusing attention on the most valuable items. It enables SMBs to:
- Prioritize stock replenishment for high‑value products (Category A)
- Maintain optimal stock levels for moderately valuable items (Category B)
- Reduce excessive attention on low‑priority items (Category C)
Resource Allocation and Optimization
With ABC analysis, SMBs can allocate their resources—time, staff, and capital—more efficiently:
- Focus on high‑profit, high‑impact items
- Avoid tying up resources in lower‑value stock
- Improve cash flow by balancing inventory levels with demand
Minimizing Stockouts and Overstocking
By classifying inventory, SMBs can better manage stock availability, ensuring they avoid:
- Stockouts of critical, high‑demand items
- Overstocking of low‑value products that could lead to unnecessary storage costs
Implementing ABC Analysis with ERP Systems
Integrating ABC analysis with ERP systems automates inventory management and provides real‑time insights for SMBs. ERP software simplifies tracking and classification, ensuring accuracy and efficiency in stock control. With the power of real‑time data, businesses can make better decisions, allocate resources effectively, and streamline inventory processes.
The Role of ERP in ABC Inventory Management
ERP systems enhance ABC inventory management by:
- Automating inventory tracking and classification
- Generating real‑time reports on stock levels and value
- Simplifying decision‑making with up‑to‑date data
Cloud‑Based ERP Solutions for SMBs
Cloud‑based ERP solutions are ideal for SMBs due to their:
- Affordability, without needing large IT investments
- Flexibility to scale with business growth
- Remote access, allowing inventory management from anywhere
Automating ABC Analysis with ERP Software
Automation through ERP software:
- Reduces human errors in inventory classification
- Speeds up the ABC analysis process
- Ensures ongoing accuracy in stock management without manual intervention
Read‑alikes
ERP Inventory Management: 12 Benefits for Your Business in Full Guide
MRP vs ERP: A Comprehensive Guide to Business Management Solutions
Top 20 ERP Software for SMEs in India and Across the World 2025
ERP Software Boom: «It’s Becoming a Single Point of Assembly of All Business Processes»
Best Practices for ABC Inventory Management
Implementing ABC analysis effectively requires thoughtful strategies and ongoing attention. For small and medium‑sized businesses, the following best practices can ensure that ABC inventory management maximizes efficiency and supports growth.
Regularly Review and Update Classifications
Business dynamics change, and so should your ABC classifications. Periodically review and update these classifications to align with:
Key Factors to Monitor | Impact on ABC Classifications |
Evolving customer demand |
Shifts products between A, B, and C categories |
Supplier cost changes |
Impacts high‑value items and reordering strategies |
Market condition changes |
Affects stock prioritization based on profitability |
By keeping the classifications up‑to‑date, SMBs can ensure they continue to optimize resources effectively and respond to market shifts with agility.
Use Data‑Driven Insights for Decision‑Making
Leverage data analytics from your ERP system to:
Benefits of Data‑Driven Decisions | Example Actions |
Identify stock movement trends |
Adjust reorder points based on demand fluctuations |
Historical and real‑time analysis |
Set optimal stock levels and prevent overstocking |
Predictive analytics |
Phase out underperforming products efficiently |
Data‑driven insights allow for more accurate and efficient inventory management, reducing excess stock and improving cash flow.
Collaborate Across Departments
Involve multiple departments in the ABC analysis process, such as:
Department | Contribution to ABC Analysis |
Purchasing |
Ensures critical stock levels are maintained |
Sales |
Provides insight into customer demand trends |
Finance |
Aligns inventory strategy with overall business goals |
Cross‑departmental collaboration ensures that everyone is aligned with inventory management goals, leading to more coordinated and successful outcomes. This holistic approach enhances decision‑making and improves long‑term inventory control.
Benefits of ABC Analysis for SMB Growth
ABC inventory management offers significant advantages for small and medium‑sized businesses, driving growth through improved resource utilization and operational efficiency.
Cost Savings and Efficiency Gains
Implementing ABC analysis helps SMBs optimize inventory management by focusing resources on high‑value items. This targeted approach reduces excess inventory costs, minimizes waste, and improves cash flow. According to studies, businesses using ABC analysis can reduce inventory costs by 10‑30%. By allocating attention and resources to the most critical items, SMBs can achieve significant cost savings and operational efficiency.
Enhanced Customer Satisfaction
Maintaining optimal stock levels of high‑priority items ensures that customer demand is consistently met. ABC analysis allows SMBs to prioritize the availability of items that matter most to their customers, leading to fewer stockouts and faster order fulfillment. A well‑managed inventory directly impacts customer satisfaction, which is essential for business retention and growth. Studies show that businesses with better stock control experience up to a 20% increase in customer satisfaction.
Scalability and Long‑Term Business Growth
ABC analysis also supports scalable inventory practices. As SMBs grow, they can continue refining their inventory strategy by adjusting their focus on A, B, and C categories. This flexibility allows for sustainable business growth, ensuring efficient inventory management as operations expand. By leveraging data‑driven insights, SMBs can scale their inventory operations smoothly, enhancing long‑term business success.
Get started with cloud‑based solutions by choosing Kladana — an ERP tailored for small and medium‑sized businesses. Now is the time to take full control of your inventory, sales, and manufacturing processes.
Frequently Asked Questions on ABC Analysis
ABC inventory analysis can significantly improve inventory management for small and medium‑sized businesses. Below are answers to some common questions SMBs may have about implementing this method.
What is ABC inventory analysis?
ABC inventory analysis classifies inventory into three categories based on their value and contribution to overall stock. Category A includes high‑value items that make up a large percentage of sales, Category B represents moderate‑value items, and Category C consists of low‑value items.
How does ABC analysis benefit small businesses?
ABC analysis helps small businesses reduce costs, improve inventory accuracy, and allocate resources efficiently. By focusing on high‑value items, businesses can improve stock management and cash flow while minimizing excess stock and wastage.
What types of businesses should use ABC analysis?
Any business with a diverse inventory can benefit from ABC analysis. It’s especially useful for SMBs looking to optimize stock levels and streamline their inventory management process.
How can ABC analysis prevent stockouts?
By prioritizing high‑value items in Category A, ABC analysis ensures that critical products are consistently stocked, reducing the risk of stockouts and improving customer satisfaction.
Can ABC analysis be automated?
Yes, ABC analysis can be automated using ERP systems, which streamline classification and provide real‑time insights for better decision‑making.
Is ABC analysis suitable for seasonal businesses?
ABC analysis can be adjusted for seasonal demand by revisiting and reclassifying items before peak periods, ensuring inventory remains optimized year‑round.
How often should I review my ABC classifications?
ABC classifications should be reviewed at least once a year to ensure they accurately reflect changes in product value and demand.
What challenges should I expect when implementing ABC analysis?
Challenges include potential misclassification and the cost of implementing technology. These can be addressed by using accurate data and automating the process with ERP systems.
What is the role of ERP in ABC inventory management?
ERP systems automate ABC analysis by tracking inventory levels, automating classifications, and generating reports, which helps businesses stay informed and proactive.
Can ABC analysis help reduce costs?
Yes, by ensuring optimal stock levels and reducing wastage, ABC analysis can lead to significant cost savings over time.