Imagine walking into a massive warehouse, rows upon rows of shelves stretching endlessly in every direction. Each shelf is crammed with products waiting to be shipped, but somewhere in this labyrinth, there’s a hidden problem: a surplus of obsolete items gathering dust and critical parts missing from their designated spots. This isn’t a scene from a dystopian novel; it’s the reality many businesses face when inventory control goes wrong.
In 2013, one of the world’s retail giants — Target, experienced a highly publicized inventory nightmare. As they expanded into Canada, their stores were plagued by empty shelves and overstocked backrooms. The disastrous rollout highlighted a crucial lesson: poor inventory control can cripple even the most successful companies.
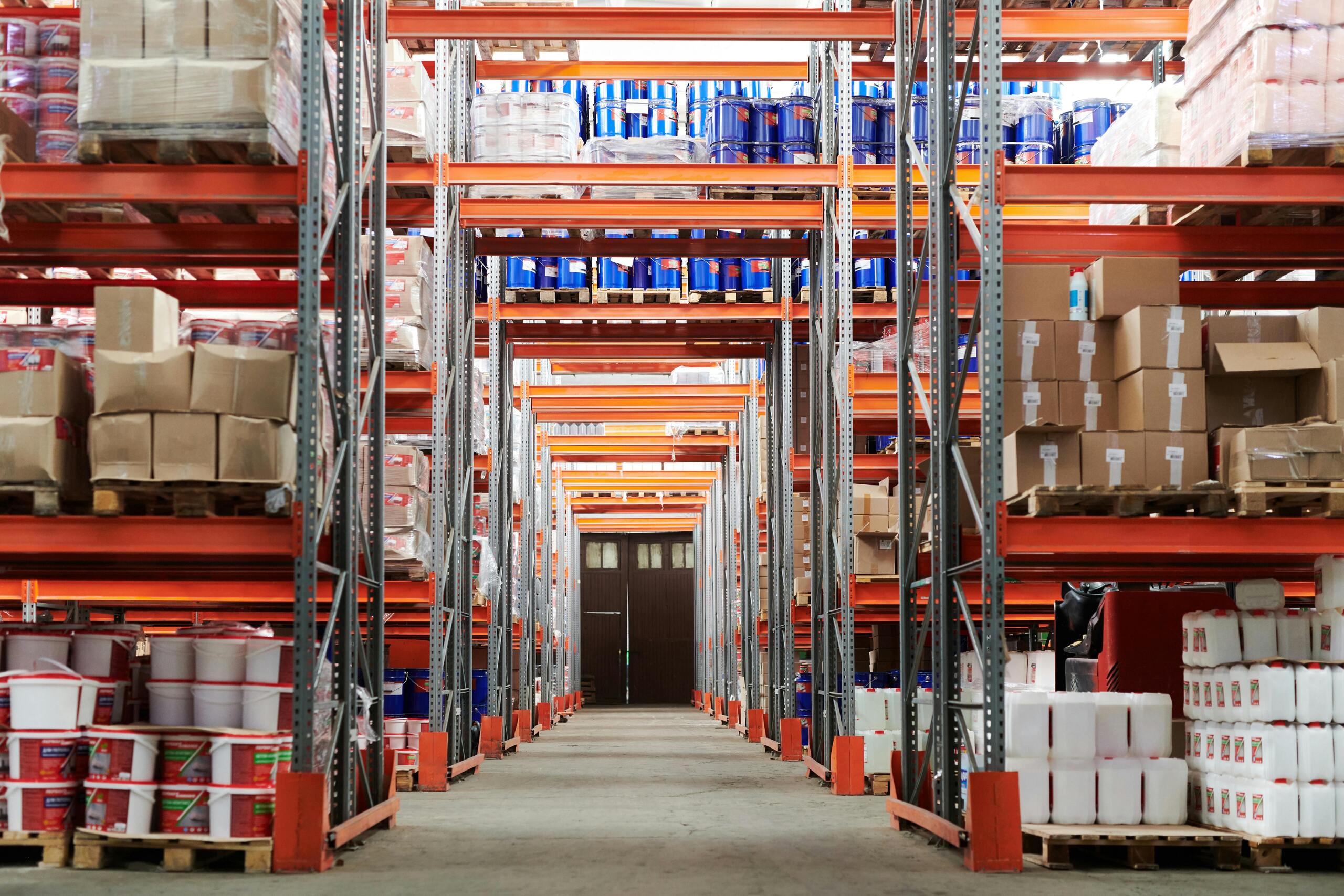
Effective inventory control is not just about counting what’s in stock; it’s a sophisticated dance of anticipating demand, minimizing waste, and ensuring every cog in the supply chain works seamlessly. It’s the difference between a thriving business and one drowning in inefficiencies. In this article, we dive into the essential elements of inventory control, uncover the common hurdles businesses encounter when implementing these systems, and offer expert tips for selecting the perfect inventory control software.
- What Is Inventory Control?
- Importance of Inventory Control
- Inventory Control vs. Inventory Management: Key Differences
- Inventory Control Key Elements
- Inventory Control Challenges
- Inventory Control Systems
- How to Implement Inventory Control?
- Choosing the Right Inventory Control Software
- Future Trends in Inventory Control
- Frequently Asked Questions on Inventory Control
What Is Inventory Control?
Inventory control refers to the systematic approach to managing and regulating the stock of goods in a business. Its primary aim is to ensure that the right amount of inventory is available at the right time to meet customer demand while minimizing costs associated with holding inventory.
Key concepts of inventory control include maintaining optimal inventory levels, understanding reorder points, implementing effective tracking systems, and employing certain techniques. These concepts help businesses avoid overstocking or stockouts, improve cash flow, and enhance overall operational efficiency. By leveraging reliable inventory control methods, companies can achieve a balanced, cost-effective inventory system that supports their strategic goals.
🎯 Ready to build inventory control from scratch?
Our free inventory checklist helps structure your processes even with basic software. From catalogue setup to internal audits — it’s the starter kit you didn’t know you needed.
Fill out the form to receive it + free 30‑day Kladana trial (instead of 14).
Importance of Inventory Control
Inventory control is a critical component of successful business operations, particularly in industries where managing the balance between supply and demand is essential. It refers to overseeing and managing the flow of goods into and out of a company’s inventory.
Businesses can reduce their inventory costs by 10% only by eliminating overstocking and understocking (according to MYOS, German financing provider).
Effective inventory control ensures that a company has the right amount of inventory on hand at any given time, avoiding stockouts that can result in lost sales or overstocking that ties up valuable capital. Here are the most paramount reasons why inventory control plays a vital role in business processes:
Reason 1. Customer Satisfaction
Inventory control ensures businesses have the right amount of inventory to fulfill customer orders promptly, leading to higher satisfaction and loyalty.
Reason 2. Cost Management
Proper inventory control prevents overstocking, which ties up capital, and stockouts, which lead to rush orders and increased costs.
Reason 3. Cash Flow Optimization
By optimizing inventory levels, businesses free up the funds that can be used for other purposes, improving liquidity and financial stability.
Reason 4. Risk Mitigation
Monitoring inventory levels helps anticipate changes in demand and minimize the impact of unforeseen events, reducing the risk of stockouts and overstocking.
Reason 5. Operational Efficiency
Effective inventory control streamlines operations, ensuring resources are used efficiently and reducing waste.
I used to sell 80 beauty care goods on marketplaces. I tried to utilize Excel sheets, but inevitably made crucial mistakes. Then I realized that I could process no more than 20 goods manually.
After six months of using Kladana, I started selling 300 goods, and the turnover almost tripled. I also analyze what goods are the most and the least profitable ones.
Reason 6. Improved Decision-Making
Inventory data can provide valuable insights into sales trends and demand patterns, helping businesses make informed decisions about purchasing and production.
Kladana helped us to automate routine processes. As soon as we started using this solution, we immediately organized our warehouses. With several warehouses in different cities, our turnover grew, leading us to purchase more products. However, the large volumes resulted in significant losses. We didn’t know the exact location of raw materials, the precise quantity of remaining goods, or how much needed to be purchased. Now, we finally see and understand everything clearly.
Reason 7. Competitive Advantage
Businesses with efficient inventory control are better positioned to meet customer demand and respond to market changes, giving them a competitive potential.
🚀 Moving from spreadsheets to pro‑level control?
Use our free checklist to set your priorities — and get a free month of Kladana. No hidden fees, no credit card. Just actionable help for smarter control.
Inventory Control vs. Inventory Management: Key Differences
Inventory control and inventory management, though often used interchangeably, serve distinct roles within a business’s operations. Inventory control focuses on the regulation and handling of stock that is already in storage, ensuring that the right amount of inventory is maintained to meet current demand without overstocking or understocking. This involves meticulous tracking, auditing, and the application of various techniques to categorize stock based on its importance and turnover rates.
On the other hand, inventory management encompasses a broader scope, including the planning, ordering, and oversight of inventory from the point of procurement to the sale. It integrates forecasting, supply chain coordination, and strategic decision-making to optimize the entire lifecycle of inventory.
Effective inventory management ensures that inventory control methods and processes are aligned with the company’s overall business strategy, enhancing efficiency, reducing costs, and improving customer satisfaction.
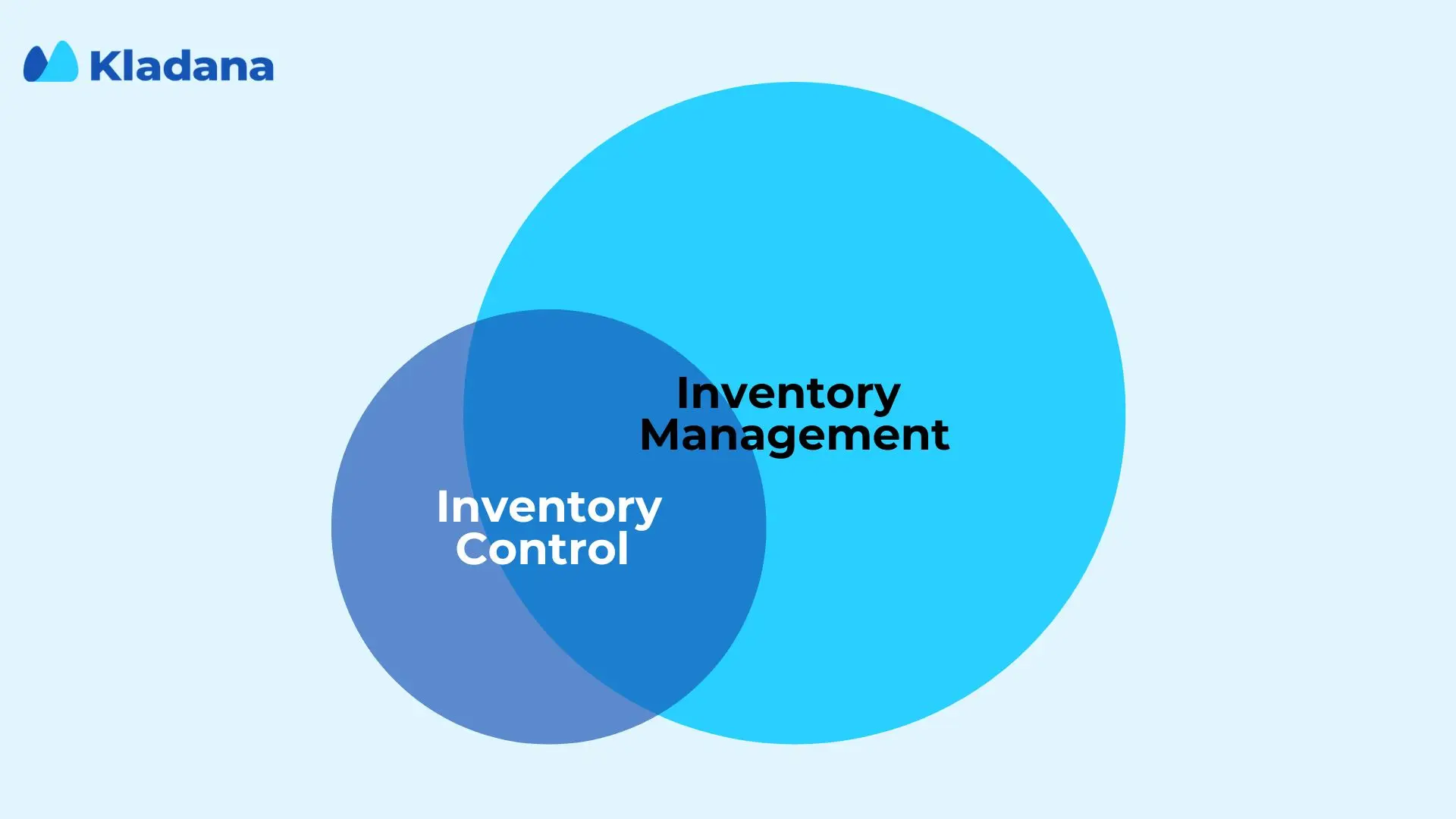
6 Inventory Control Key Elements
Effective inventory control is not just about keeping track of stock; it is a strategic component crucial for the seamless operation and financial health of a business. By maintaining the right inventory balance, companies can meet customer demands promptly, reduce unnecessary costs, and optimize their supply chain processes. Here are the essential components that form the backbone of an effective inventory control system:
Element 1. Accurate Demand Forecasting
Anticipate customer needs and adjust inventory levels accordingly to reduce the risk of overstocking or stockouts.
Element 2. Efficient Inventory Tracking Systems
Utilize advanced software solutions to provide real-time visibility into stock levels, locations, and movements, enabling better decision-making and faster response to market changes.
Element 3. Regular Stock Audits
Verify the accuracy of inventory records, identify discrepancies, and prevent losses due to theft, damage, or mismanagement.
Element 4. Managing All Stock Items
Maintain comprehensive records and organization of all stock items, ensuring easy access and efficient management of inventory.
Element 5. Timely Purchasing
Implement a well-planned purchasing strategy to ensure timely stock replenishment, avoiding delays that can disrupt operations and affect customer satisfaction.
Element 6. Regular Analyzing and Reporting
Conduct ongoing analysis and generate reports to track inventory performance, identify trends, and make informed decisions to optimize inventory management strategies.
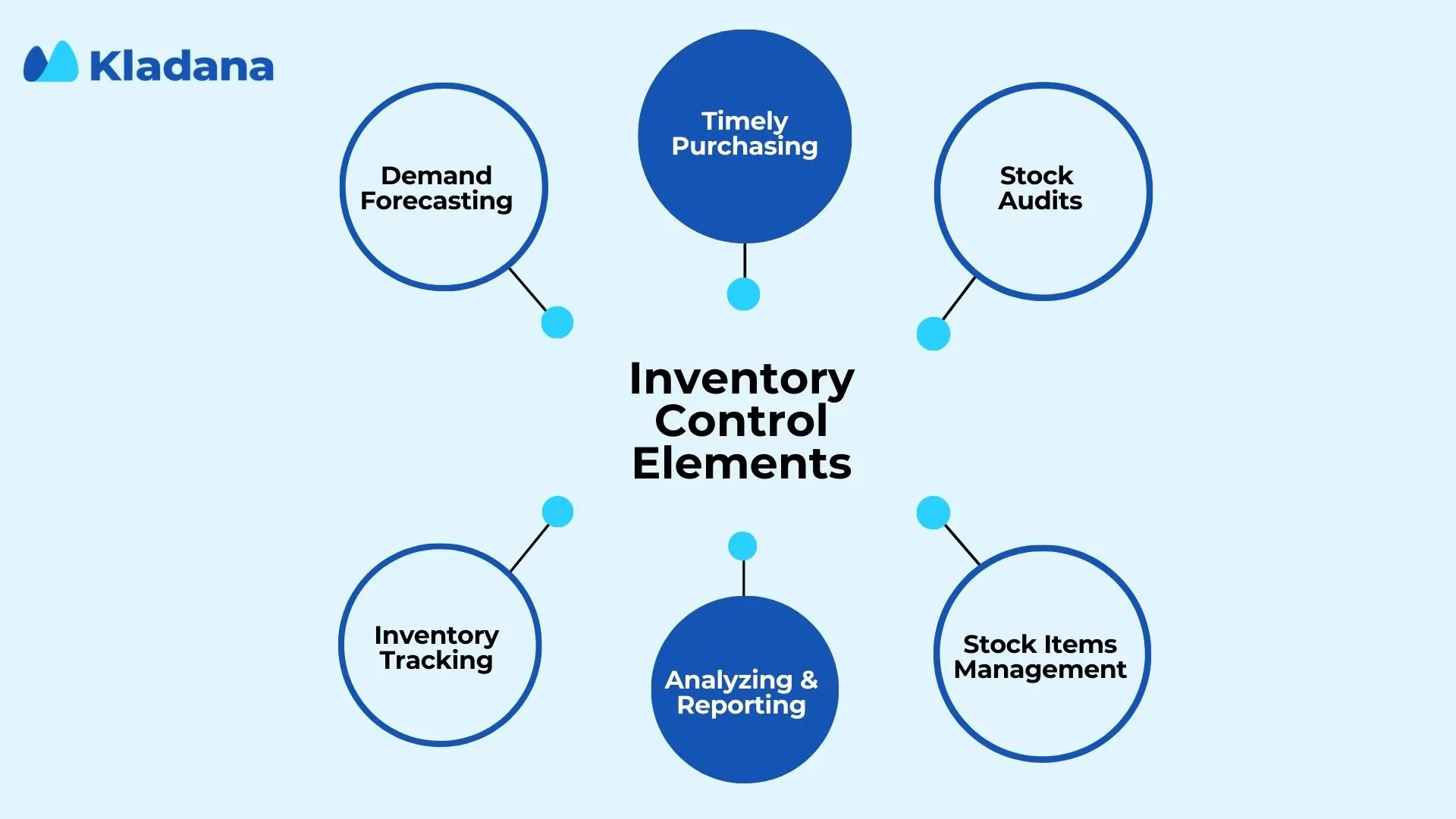
10 Inventory Control Challenges
Inventory control is a multifaceted process that poses several intricate challenges for businesses, particularly those operating within complex supply chains. These challenges demand meticulous attention and strategic management to ensure operational efficiency and financial stability. Here are some key challenges:
Challenge 1. Accurate Inventory Records
Maintaining precise inventory records is essential but can be challenging due to the dynamic nature of inventory movement. Inaccuracies can lead to stockouts, overstocking, or misallocation of resources, impacting customer satisfaction and profitability.
Challenge 2. Demand Forecasting
Factors such as seasonality, market trends, and consumer behavior make accurate forecasting challenging. Inaccurate forecasts can result in excess inventory or stockouts, both of which can incur significant costs.
According to a 2023 Kearney, global management consulting company, study, excess inventory created by demand surges during the pandemic is a disaster worth more than $250 billion in the USA alone. Globally, U.S. Census data suggests that excess inventory is in the trillions of dollars.
Challenge 3. Inventory Theft and Shrinkage
Protecting inventory from theft and shrinkage is a constant challenge for businesses. Theft can occur internally or externally, and without proper security measures and stock controls in place, businesses can suffer substantial financial losses.
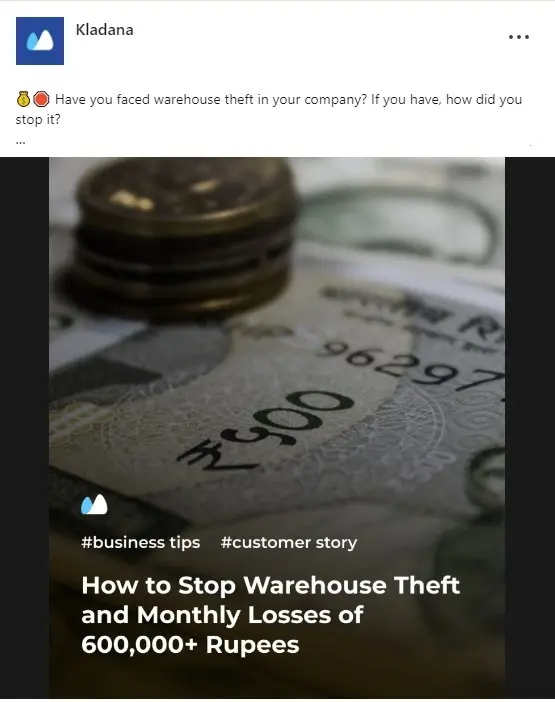
Challenge 4. Supplier Management
Managing multiple suppliers, lead times, and quality control can be challenging, requiring robust supplier management practices.
Only 6% of companies claim to have complete visibility into their supply chain, while 69% lack full visibility (Zippia, career guidance platform).
Challenge 5. Technology Integration
Implementing and integrating inventory management technologies, such as inventory tracking systems or warehouse management systems, can be complex and costly. However, these technologies are crucial for improving inventory visibility and streamlining operations.
Challenge 6. Inventory Optimization
Balancing inventory levels to meet customer demand while minimizing carrying costs is a constant challenge. Without proper optimization strategies, businesses risk tying up capital in excess inventory or facing stockouts, impacting their bottom line.
Challenge 7. Proneness to Errors
Inventory management is susceptible to various errors, including data entry mistakes, miscounts, and miscalculations. These errors can lead to inaccuracies in inventory records, impacting decision-making and operational efficiency.
Challenge 8. Achieving Real-time Visibility
Achieving real-time visibility can be challenging, especially for businesses with complex supply chains and disparate systems.
Challenge 9. Accurate Tracking
Tracking inventory movement accurately, from receipt to storage to fulfillment, is essential for ensuring inventory accuracy. However, manual tracking processes are prone to errors and can be time-consuming, highlighting the need for automated tracking solutions.
According to Peoplevox, Ecommerce WMS, around 34% of companies have faced instances where they accidentally sold an out-of-stock item, causing delays in fulfilling orders.
Challenge 10. Reducing Costs
Balancing inventory levels to meet demand while minimizing costs requires careful planning and effective inventory management strategies.
Inventory Control Systems
There is no ideal universal system for inventory control. For some types of businesses, manual control systems that have been in place for centuries are still suitable. However, for large enterprises that use a wide range of raw materials and semi-finished products for production, relying on paper and pencil poses a significant risk. In such cases, implementing high-tech software is ideal. Below, we will explore the main types of inventory control systems.
Manual System
This system of inventory control involves tracking inventory levels by hand. This method is labor-intensive and prone to errors but can be cost-effective for small businesses with low inventory turnover.
Pros | Cons |
Cost-effective for small businesses, simple to implement and understand |
Labor-intensive, prone to errors, limited scalability |
Stock Cards
Stock cards, also known as bin cards, are physical cards that record the quantity of each item in stock. They are updated manually with each transaction, providing a real-time view of inventory levels for a specific item.
Pros | Cons |
Provides a real-time view of inventory levels for a specific item, simple to use |
Requires manual updating, can be time-consuming, prone to errors, no remote access |
Spreadsheets
Spreadsheets, such as Microsoft Excel or Google Sheets, can be used to track inventory levels. They offer more flexibility than stock cards and can be automated to some extent, but they are still prone to errors and may not scale well for large inventories.
Pros | Cons |
More flexible than stock cards, can be automated to some extent, widely available |
May not scale well for large inventories, lack of real-time updates |
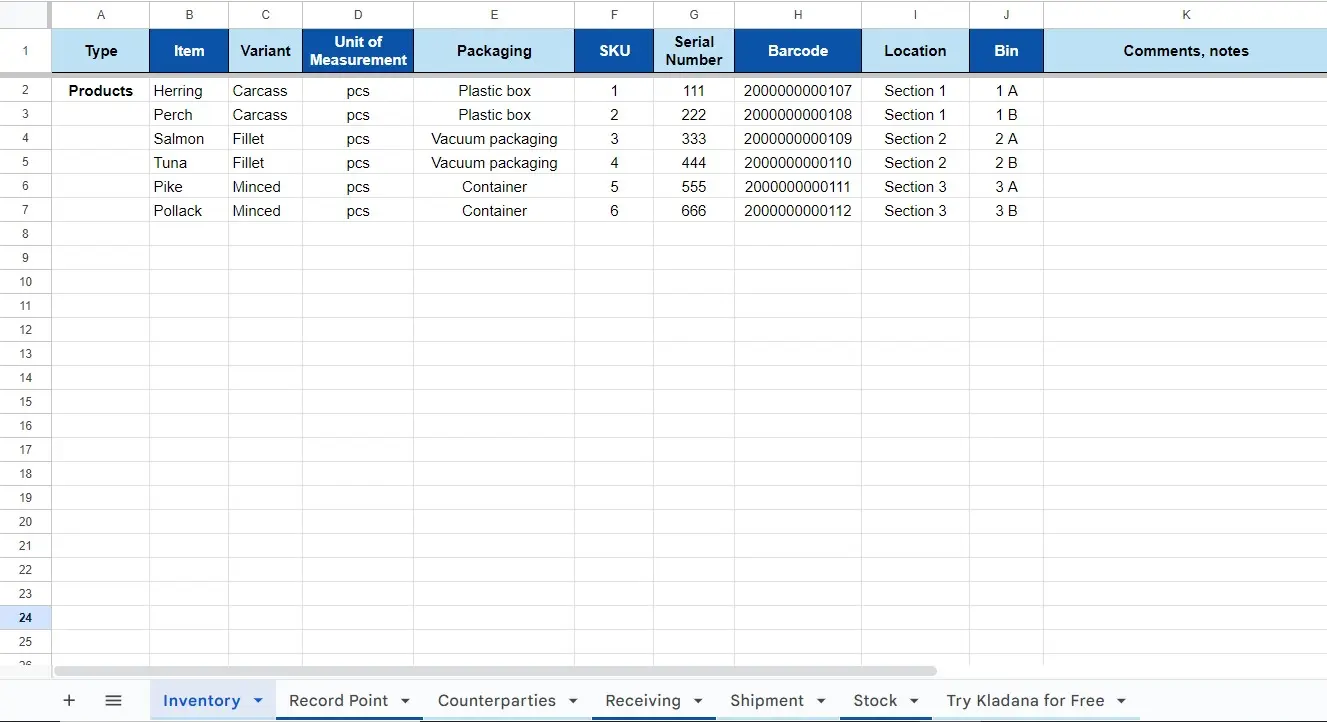
If you choose Excel for stock management and prefer not to start from scratch, read the guide and try our free Excel inventory template.
Cloud Software
Inventory management software, such as ERP systems or specialized inventory control software, offers the most advanced solution. These systems can track and manage stock levels in real-time, automate reordering processes, and generate detailed reports. While more expensive than manual systems or spreadsheets, these stock control systems can significantly improve efficiency and accuracy in inventory management.
Pros | Cons |
Real-time tracking of inventory levels, automation of reordering processes, detailed reporting, automated planning |
More expensive than manual systems or spreadsheets, may require training to use effectively |
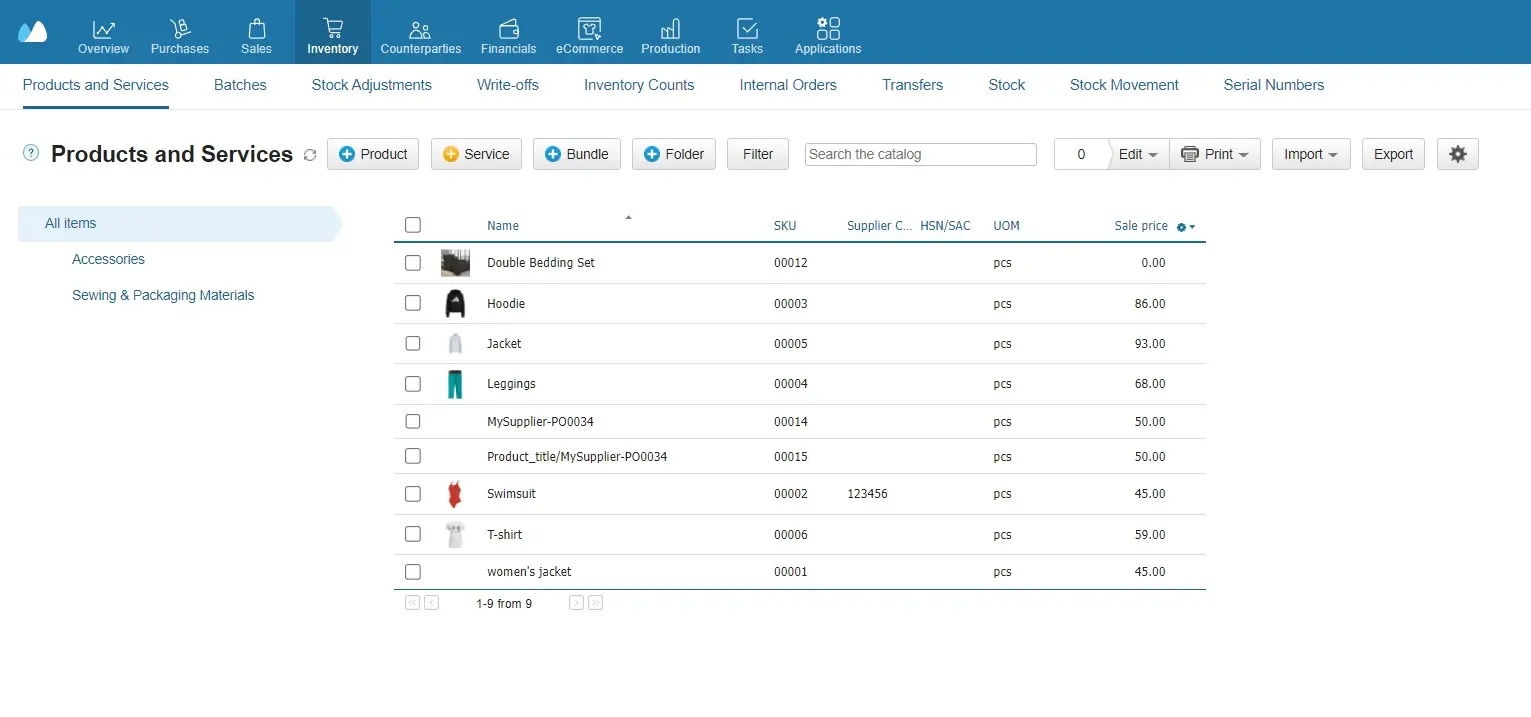
How to Implement Inventory Control?
We’ve already covered the basic elements, benefits, and challenges that make inventory control what it is today. However, if you are new to building inventory control in your business, this information may not be enough for you. In this section, you will find a description of the basic steps that will guide you on your way.
Assess Current State of Inventory Control
Begin by evaluating your current inventory control practices. Identify strengths, weaknesses, and areas needing improvement.
Set Clear Goals
Define what you want to achieve with your inventory control system. Goals may include reducing excess stock, improving order accuracy, and minimizing holding costs.
Classify Inventory
You may use ABC analysis to categorize inventory based on importance. This helps prioritize which items need more attention and resources.
Choose and Implement New Inventory Control System
Weigh the pros and cons of different systems and determine which one is optimal at the current stage.
Establish Reorder Points
Determine reorder points for each item to ensure timely restocking and prevent stockouts. Use historical sales data and lead times to set accurate reorder levels.
Regular Audits and Cycle Counts
Conduct regular inventory audits and cycle counts to verify physical stock against records. This helps identify discrepancies and maintain accuracy.
Train Staff
Ensure your team is well-trained in using the inventory control system and understands its importance. Regular training sessions can keep everyone updated on best practices.
Monitor and Adjust
Continuously monitor the performance of your inventory control system. Analyze key metrics like turnover rates and holding costs, and make necessary adjustments to improve efficiency.
Choosing the Right Inventory Control Software
Selecting the right inventory control software is akin to finding the perfect puzzle piece for your business operations. It’s a decision that requires thoughtful consideration and a deep understanding of your company’s unique needs. Here are key factors to contemplate when embarking on this quest:
9 Key Factors | Considerations |
Scalability |
Ensure the software can accommodate your business growth, handling increased products and orders |
Integration |
Look for seamless integration with existing systems, minimizing disruptions and data discrepancies |
Features |
Identify must-have features like barcode scanning, batch tracking, and demand forecasting |
User-Friendliness |
Opt for intuitive software with a user-friendly interface, reducing training time for your team |
Reporting and Analytics |
Prioritize software that offers robust reporting and analytics for informed decision-making |
Mobile Accessibility |
Choose software with mobile capabilities for remote inventory management and real-time updates |
Compliance |
Ensure the software complies with relevant regulations, such as traceability and tax requirements |
Cost |
Consider both initial investment and ongoing costs, aligning with your budgetary constraints |
Customer Support |
Select a vendor known for reliable customer support, providing assistance when you need it |
Future Trends in Inventory Control
As technology continues to advance at an unprecedented pace, the future of inventory management is being shaped by groundbreaking developments that promise to revolutionize the way companies operate.
These trends are not only enhancing efficiency and accuracy but also paving the way for more intelligent, responsive, and environmentally conscious inventory practices. In this context, exploring the future trends of inventory control reveals how these innovations are poised to redefine the industry.
Use of Automated Guided Vehicles and Automated Mobile Robots
As customer demand for rapid deliveries intensifies, businesses are exploring innovative solutions to enhance efficiency. Among these, Automated Guided Vehicles (AGVs) and Automated Mobile Robots (AMRs) are becoming indispensable for warehouse operations. AGVs navigate warehouse floors using magnetic strips or wires, following predetermined paths. AMRs represent a new generation of «collaborative robots» that navigate autonomously using advanced sensors similar to those in self-driving cars.
Both AGVs and AMRs significantly cut down the time required to move items within a warehouse, allowing human employees to focus on other tasks and expedite order fulfillment. Additionally, AMRs, due to their lack of reliance on infrastructure such as guiding wires, are cost-effective and straightforward to implement, making them an attractive option for modern warehouses.
Trying Distributed Inventory
Decentralizing inventory by spreading it across various warehouses can cut down on transportation expenses and enhance delivery efficiency—provided the right products are placed in optimal locations and shipments are dispatched from the nearest warehouse to the customer. Typically, managing a larger number of smaller warehouses, rather than a few large ones, enables more precise control over inventory.
Achieving this requires robust data analysis to understand the geographic distribution of orders in relation to inventory locations. It also demands the flexibility to establish distribution centers strategically based on this data and the technology to guide suppliers in effectively dividing shipments.
The Role of Artificial Intelligence and Machine Learning
One of the most significant advancements in inventory control is the integration of artificial intelligence (AI) and machine learning (ML) algorithms. These technologies allow businesses to analyze vast amounts of data to predict demand more accurately, optimize inventory levels, and automate replenishment processes. AI and ML also enable dynamic pricing strategies based on real-time market conditions and customer behavior, leading to improved profitability and customer satisfaction.
The Impact of the Internet of Things on Inventory Management
The Internet of Things (IoT) has revolutionized inventory management by enabling real-time tracking and monitoring of inventory levels. IoT devices, such as RFID tags and sensors, provide accurate data on the location, condition, and movement of inventory items throughout the supply chain. This visibility helps businesses reduce stockouts, prevent overstocking, and improve overall operational efficiency.
Sustainable Inventory Practices
Sustainability is becoming increasingly important in inventory management. Businesses are adopting practices such as lean inventory management, which focuses on reducing waste and optimizing processes to minimize environmental impact. Additionally, there is a growing trend towards implementing circular economy principles, where products and materials are recycled or repurposed to extend their lifecycle. These sustainable inventory practices not only benefit the environment but also enhance brand reputation and appeal to eco‑conscious consumers.
Inventory Control, Minus the Headaches
Track what you have, where it is, and when to reorder — all in one place. No more guesswork, no more stockouts.
Frequently Asked Questions on Inventory Control
To create your own inventory control starter pack, we recommend that you find answers to typical questions.
What is inventory control?
Inventory control is the process of managing and overseeing the storage, ordering, and use of materials and products to ensure an optimal balance between supply and demand, minimizing costs while maximizing efficiency and customer satisfaction.
What is the difference between inventory control and inventory management?
Inventory control focuses on maintaining optimal stock levels to prevent overstocking or stockouts, ensuring efficient storage and accurate records. Inventory management encompasses the broader process of overseeing the entire inventory cycle, from ordering and storing to using and selling inventory.
Why is inventory control important for businesses?
Effective inventory control helps businesses minimize costs, improve cash flow, and meet customer demand promptly. It reduces the risk of excess inventory, obsolescence, and stockouts, leading to better financial health and customer satisfaction.
What are the key features to look for in inventory control systems?
Essential features include real-time tracking, barcode technology, demand forecasting tools, integration capabilities with other business systems, automated reordering, and comprehensive reporting and analytics.
What role does demand forecasting play in inventory control?
Demand forecasting is crucial in inventory control as it predicts future sales trends, helping businesses to maintain optimal stock levels, reduce excess inventory, and avoid stockouts, thereby enhancing customer satisfaction and operational efficiency.
How do manual and automated inventory control systems differ?
Manual systems rely on human input and physical records, making them prone to errors and time-consuming. Automated systems use software and technology like barcode scanners and RFID to streamline processes, improve accuracy, and provide real-time data.
What are the consequences of poor inventory control?
Poor inventory control can lead to overstocking, stockouts, increased carrying costs, lost sales, decreased customer satisfaction, and ultimately, reduced profitability. It can also cause operational inefficiencies and affect the overall business performance.
What are the benefits of using AI and machine learning in inventory management?
AI and machine learning can enhance demand forecasting accuracy, optimize stock levels, identify trends, automate routine tasks, and provide actionable insights for better decision-making, ultimately improving efficiency and reducing costs.
How does IoT impact inventory management?
IoT enables real-time tracking of inventory through connected devices, enhancing visibility and control over the supply chain. It improves accuracy, reduces losses, and provides data for predictive maintenance and better demand forecasting.
Read-alikes
Inventory Management Guide for Beginners: Techniques, Challenges, Best Practices, and Trends
Inventory Management in Excel: Free Template and a Step‑by‑Step Guide
Inventory Counting: Step‑by‑Step Guide on How to Conduct and Access the Results
ERP Inventory Management: 12 Benefits for Your Business in Full Guide