Managing inventory across multiple locations can be complex, but it’s crucial for small and medium businesses aiming to streamline operations and improve efficiency. Without real-time visibility and accurate tracking, inventory mismanagement can lead to costly errors like stockouts, overstocking, and delayed deliveries.
In this guide, we’ll explore how businesses can simplify multi-location inventory management by leveraging cloud-based ERP systems and automation, ensuring seamless control over stock, and enhancing decision-making across all locations. Let’s dive into practical strategies for efficient multi-location stock management.
- Understanding Multi-Location Inventory Management
- The Role of Cloud-Based ERP in Simplifying Multi-Location Inventory
- Best Practices for Multi-Location Inventory Management
- Overcoming Common Pitfalls in Multi-Location Inventory Management
- Frequently Asked Questions on Multi-location Inventory Management
Understanding Multi-Location Inventory Management
For small and medium-sized businesses (SMEs), managing inventory across multiple locations is an essential yet challenging task. Multi-location inventory management refers to the coordination of stock levels across different warehouses, stores, or distribution centers.
This ensures that stock levels are balanced, and customer demands are met without delay or surplus. Efficient inventory management across locations prevents stockouts, overstocking, and logistical inefficiencies, allowing SMEs to operate with greater agility and precision.
What is Multi-Location Inventory Management?
Multi-location inventory management is the process of overseeing inventory across various locations — whether physical stores, warehouses, or fulfillment centers. By centralizing control of these inventories through cloud-based ERP systems, businesses can monitor stock levels in real-time, track stock movement, and ensure smooth supply chains. For SMEs, it’s a way to streamline stock control while optimizing storage and distribution across diverse regions.
Key Challenges Faced by SMEs in Multi-Location Inventory Management
SMEs encounter several hurdles in managing inventory across different locations:
- Stock discrepancies: Inconsistent stock counts between locations lead to inaccuracies.
- Oversupply or undersupply: Balancing stock levels without overstocking or running out of products.
- Demand forecasting: Predicting demand accurately for multiple regions can be difficult.
- Coordination of shipments: Moving stock between locations can be inefficient without proper tracking.
By understanding these challenges, SMEs can begin to implement solutions that simplify their multi-location inventory systems. We’ll consider the topic of overcoming this and other challenges later in this article.
The Role of Cloud-Based ERP in Simplifying Multi-Location Inventory
Cloud-based ERP systems play a pivotal role in streamlining multi-location inventory processes for small and medium-sized businesses (SMEs). These solutions can enhance operational efficiency, reduce errors, and provide businesses with the tools needed to respond swiftly to market changes. This not only improves the management of stock across different locations but also enables SMEs to maintain a competitive edge in a dynamic business environment.
Benefits of Cloud-Based ERP for Inventory Control
Utilizing cloud-based ERP software for inventory management offers numerous advantages:
Benefit | Description |
Real-Time Data Access |
Users can access up-to-date stock levels and inventory information from anywhere at any time. |
Automation of Processes |
Automated reordering and tracking reduce manual workload, minimizing human errors. |
Scalability |
Cloud-based systems can easily scale with business growth, accommodating increased inventory needs. |
Cost-Effectiveness |
Lower infrastructure costs compared to traditional on-premise systems, ideal for SMEs. |
How Cloud-Based ERP Enhances Visibility and Control
Cloud-based ERP systems provide unprecedented visibility into inventory levels across multiple locations. With real-time tracking capabilities, businesses can monitor stock levels, manage orders, and identify discrepancies promptly. This enhanced visibility helps improve inventory accuracy, ensuring that each location has the right amount of stock to meet customer demands.
Furthermore, centralized reporting tools allow decision-makers to analyze data trends and make informed inventory management decisions, significantly enhancing overall control over operations.
Streamline Your Inventory Control with Kladana!
With Kladana, you can:
- Gain a comprehensive view of your warehouse, from overall stock to individual items
- Set up alerts for tasks that need immediate attention
- Track batch expiration dates and monitor raw materials and semi-finished goods
- Maintain optimal stock levels, avoiding shortages and excess inventory
- Conduct regular inventory checks to ensure accuracy.
Best Practices for Multi-Location Inventory Management
Effectively managing inventory across multiple locations requires a strategic approach that combines technology and best practices. Small and medium-sized businesses (SMEs) can optimize their inventory management processes by implementing the following key strategies, ensuring a smoother operation and better resource allocation.
Centralizing Inventory Data
Centralizing inventory data is crucial for maintaining consistency and transparency. By using a cloud-based ERP system, SMEs can ensure that all locations are updated in real-time, providing a single source of truth for inventory levels.
Automating Stock Replenishment
Automated stock replenishment significantly reduces human error and ensures adequate stock levels across all locations. By utilizing inventory management software that triggers automatic reordering based on predefined thresholds, SMEs can maintain optimal stock levels without manual intervention.
Implementing Real-Time Inventory Tracking Solutions
Real-time inventory tracking is vital for maintaining stock accuracy and avoiding understocking or overstocking. By employing barcode scanning and RFID technology, SMEs can monitor stock movements as they occur.
Standardizing Processes Across Locations
Standardizing inventory management processes across all locations is essential for ensuring consistency and efficiency. By developing uniform procedures for stock receiving, storage, and distribution, SMEs can minimize confusion and enhance training for new employees.
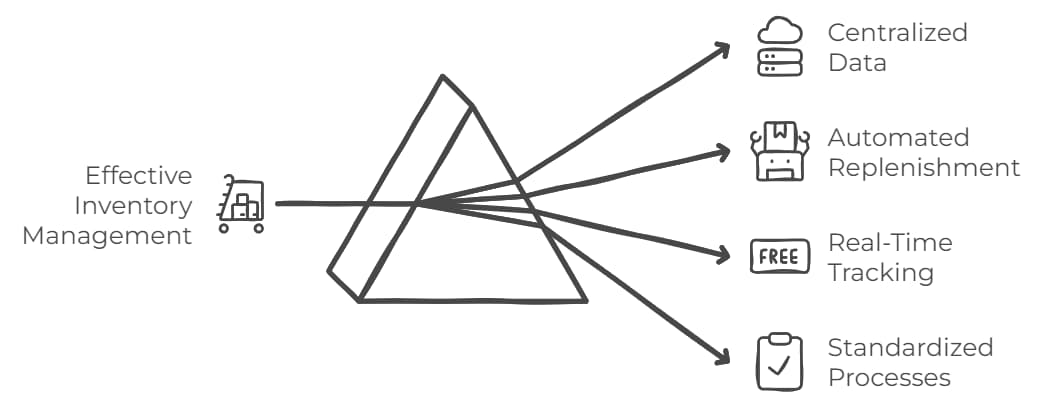
Overcoming Common Pitfalls in Multi-Location Inventory Management
Managing inventory across multiple locations can be challenging for small and medium-sized enterprises (SMEs), often leading to costly mistakes. Understanding common pitfalls and how to avoid them can enhance operational efficiency and customer satisfaction.
Inconsistent Stock Levels
Inconsistent stock levels across different locations can result in lost sales or excessive overstocking. This discrepancy often arises from poor inventory tracking or failure to communicate stock movements effectively. To mitigate this issue, SMEs should:
- Implement centralized inventory management software that provides real-time visibility across all locations.
- Regularly audit stock levels to identify discrepancies and adjust accordingly.
- Set up automated alerts for low stock to facilitate timely replenishment.
By ensuring consistent stock levels, businesses can enhance customer satisfaction and reduce waste.
Lack of Real-Time Data Access
A lack of real-time data can severely hinder decision-making and lead to inefficient inventory management practices. Without up-to-date information on stock levels and sales trends, businesses may struggle to respond to customer demands or market shifts. To overcome this challenge:
- Adopt cloud-based ERP systems that provide real-time data access to all stakeholders.
- Utilize mobile inventory management solutions to allow team members to update stock levels instantly.
- Train staff on the importance of data accuracy, emphasizing the role of real-time information in decision-making.
Poor Communication Between Locations
Clear communication between various locations is essential for effective inventory management. Miscommunication can lead to misunderstandings regarding stock availability and demand forecasts. To enhance communication:
- Establish regular check-in meetings between location managers to discuss inventory needs and challenges.
- Use collaborative tools for sharing inventory data, ensuring all team members are informed of stock changes.
- Create a shared inventory dashboard to provide all locations with a unified view of stock levels and trends.
Neglecting Employee Training
Failing to adequately train employees on inventory management practices can lead to costly errors. Staff must understand the processes and technologies in place to effectively manage inventory. To address this issue:
- Provide ongoing training sessions to ensure all employees are up to date on best practices.
- Develop clear documentation outlining procedures for inventory management.
- Encourage cross-training between locations to foster a culture of collaboration and knowledge sharing.
Ignoring Demand Forecasting
Ignoring demand forecasting can result in stock imbalances, affecting sales and customer satisfaction. Accurate forecasting is crucial for maintaining optimal inventory levels. To improve forecasting:
- Analyze historical sales data to identify trends and seasonal fluctuations.
- Leverage advanced analytics tools to improve forecasting accuracy.
- Engage in regular market research to adapt to changing consumer preferences.
Read‑alikes
15 Key Inventory Management Techniques: How to Choose the Best One
ERP Inventory Management: 12 Benefits for Your Business in Full Guide
Frequently Asked Questions on Multi-location Inventory Management
Managing multi-location inventory presents unique challenges for small and medium-sized enterprises (SMEs). Below are answers to some of the most common questions regarding this critical aspect of inventory management.
What is multi-location inventory management and why is it important?
Multi-location inventory management refers to the strategies and processes involved in tracking and managing inventory across different warehouses or retail locations. For SMEs, effective multi-location inventory management is crucial as it ensures that stock levels are optimized, reduces the risk of stockouts or overstocking, and enhances customer satisfaction. With efficient management, businesses can respond more effectively to market demands and streamline their operations.
How can cloud-based ERP software help manage inventory across multiple locations?
Cloud-based ERP systems facilitate multi-location inventory management by providing a centralized platform for real-time data access and automation. These systems allow SMEs to monitor stock levels across all locations simultaneously, automate inventory replenishment processes, and ensure accurate reporting. As a result, businesses can respond quickly to inventory fluctuations and maintain optimal stock levels.
What are the biggest challenges in managing inventory across multiple locations?
Key challenges in multi-location inventory management include inconsistent stock levels, poor communication between locations, and limited access to real-time data. Inconsistent stock levels can lead to lost sales, while inadequate communication can result in mismanagement. Additionally, without real-time data, decision-making may suffer, impacting overall inventory efficiency.
How does real-time inventory tracking work in a multi-location setup?
Real-time inventory tracking utilizes advanced technologies such as barcode scanning and RFID to keep inventory data synchronized across all locations. When a product is sold or moved, the system automatically updates stock levels in real time. This immediate feedback allows businesses to make informed decisions regarding restocking and resource allocation, thus maintaining accurate inventory levels.
How can SMEs prevent overstocking or understocking at various locations?
To prevent overstocking or understocking, SMEs should implement automated stock replenishment systems and accurate demand forecasting techniques. Automated systems monitor stock levels and trigger replenishment orders when thresholds are reached. Accurate forecasting based on historical sales data and market trends helps ensure that inventory levels align with customer demand.
What are the benefits of having a centralized inventory management system?
A centralized inventory management system consolidates data from all locations, providing a comprehensive view of stock levels and movements. This centralization improves accuracy, reduces discrepancies, and enhances visibility. By having a single source of truth, SMEs can streamline their inventory management processes, making it easier to identify trends and make data-driven decisions.
What key features should I look for when choosing inventory management software for SMEs?
When selecting inventory management software, SMEs should prioritize features such as scalability, automation, real-time tracking, and multi-channel integration. A user-friendly interface and robust reporting capabilities are also essential, enabling businesses to manage their inventory efficiently and adapt to growth.
How can automation improve multi-location inventory management?
Automation streamlines operations by minimizing human errors and enhancing efficiency in inventory management. Automated systems can handle tasks such as stock monitoring, order processing, and reporting, allowing employees to focus on more strategic initiatives. By reducing manual input, businesses can maintain more accurate inventory records and improve overall operational productivity.
What are some best practices for managing warehouses across multiple locations?
Best practices for managing warehouses across multiple locations include:
- Implementing standardized processes for inventory handling to ensure consistency.
- Utilizing technology such as automated tracking systems to enhance accuracy.
- Conducting regular audits to verify stock levels and address discrepancies.
- Fostering open communication between locations to share insights and strategies.
By adhering to these best practices, SMEs can effectively manage their inventory across multiple locations, driving operational efficiency and customer satisfaction.
How can training improve staff efficiency in multi-location inventory management?
Training plays a crucial role in enhancing staff efficiency by ensuring that employees understand the inventory management systems and best practices in place. Providing regular training sessions helps staff stay updated on technology and procedures, leading to more accurate inventory handling and reduced errors. This investment in employee education ultimately contributes to smoother operations and improved inventory performance across all locations.