Imagine running a flash sale, which triggers an unexpected surge of orders. Your system says enough stock is on hand, but in reality, half of those items are already gone. Customers rush in, placing orders, but you scramble to buy goods at higher prices, slashing your profit margin just to save your brand’s image.
But is this situation totally avoidable? The answer is yes.
A well-structured inventory management process could flag rising demand early, help you plan reorders, and protect your bottom line. Managing inventory ensures that the right stock is available at the right time and in the right quantity without tying up excess capital.
Whether in retail, manufacturing, or distribution, businesses that refine their inventory processes can reduce waste, improve cash flow, and enhance customer satisfaction.
Let’s find out more about the objectives of inventory management and how it increases profits and operational agility.
- What is Inventory Management?
- Key Objectives of Inventory Management
- Goals of Inventory Management
- Objectives of Inventory Control
- Best Practices for Effective Inventory Management
- Challenges in Inventory Management and How to Overcome Them
- Invest in a Robust ERP Solution to Manage Your Inventory
- FAQs on Objectives of Inventory Management
What is Inventory Management?
Inventory management is a system for organizing the handling of goods from procurement to final sale. This process involves tracking stock levels, forecasting demands, and optimizing order fulfillment to maintain a delicate balance between supply and demand.
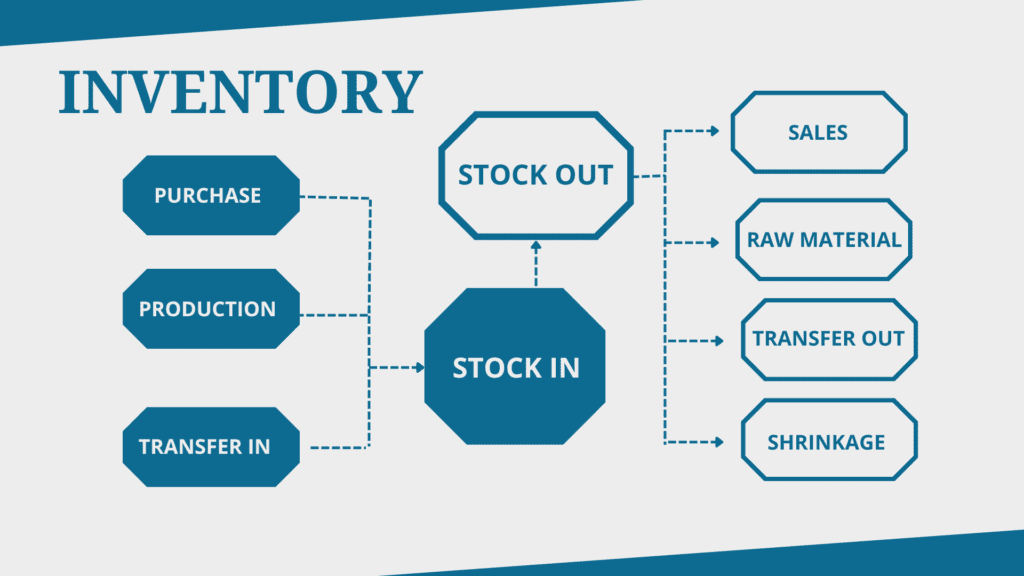
That said, inventory management is different from inventory control based on the other scope, focus, and goals:
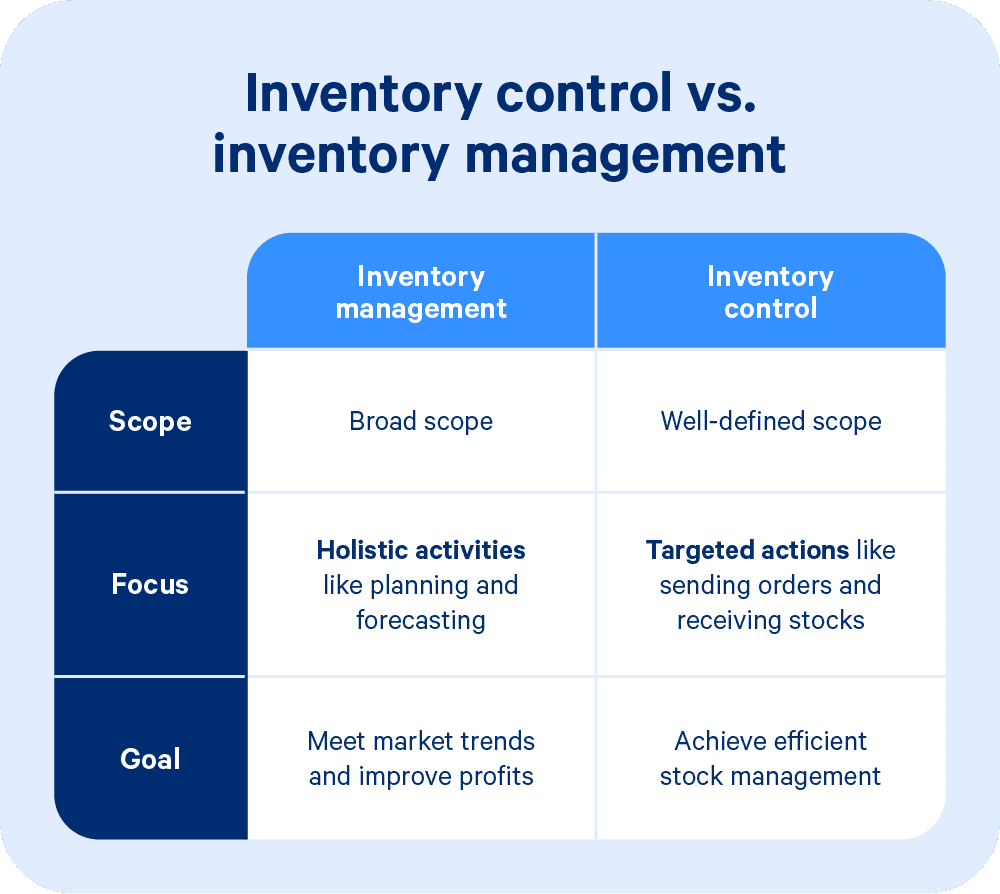
Inventory Management: A strategic process of forecasting demand, optimizing stock levels, and ensuring timely replenishment. It encompasses supplier coordination, cash flow planning, and efficiency improvements.
Inventory Control: A subset of inventory management that involves monitoring stock movement, preventing discrepancies, and maintaining accuracy through tracking systems like RFID, barcodes, and automated records.
A company can have good inventory control but still struggle with poor inventory management if forecasting and procurement decisions are flawed.
Both must work in sync to prevent operational bottlenecks.
Key Objectives of Inventory Management
Objectives in inventory management are the measurable outcomes that your business should aim for. They usually revolve around profitability, efficiency, and customer satisfaction.
A lack of clear objectives for inventory management can cause businesses to risk overstocking, stockouts, and financial mismanagement.
Below are some of the major inventory management objectives you should know about:
Ensuring Product Availability
The idea behind implementing inventory management is to make sure you don’t run out of stock at the wrong time. It can mean lost revenue, customer dissatisfaction, and damaged brand reputation.
So, maintain safety stock through real-time inventory tracking and implement automated reorder systems to prevent disruptions.
For example, Amazon’s fulfillment centers leverage predictive analytics to monitor demand patterns. During peak sales periods, like Black Friday, their system ensures high-demand products are stocked at warehouses closest to key markets.
Optimizing Inventory Costs
Inventory cost optimization involves finding ways to reduce holding and ordering costs. Balancing inventory expenses requires strategic ordering cycles, lean stocking models, and supplier negotiations.
Holding too much stock increases storage, insurance, and depreciation costs, while frequent ordering raises logistics expenses and procurement inefficiencies.
Zara, a global fashion retailer, optimizes costs using a fast-turnaround inventory model. Instead of overstocking seasonal items, it relies on a high-frequency, limited-stock replenishment strategy.
This approach reduces warehouse space needs while keeping fresh designs flowing. Zara’s ability to adapt order volume based on demand trends helps it maintain profitability while reducing unnecessary inventory expenses.
Minimizing Wastage and Obsolescence
Think about ways you can prevent losses due to expired or outdated stock. Inventory waste occurs when goods expire, become outdated, or degrade due to poor storage conditions.
You can implement strategies like First-In, First-Out (FIFO), demand forecasting, and inventory rotation to minimize losses.
A prime example is McDonald’s, where perishable ingredients must be carefully managed to prevent food waste. Their system tracks sales data to adjust ingredient restocking schedules, ensuring that older stock is used first while maintaining freshness. Any excess stock is redirected to outlets with higher demand, reducing spoilage.
Enhancing Supply Chain Efficiency
To ensure a smooth supply chain, you’ll need to streamline order processing and warehouse management. This will result in efficient order processing, warehouse optimization, and seamless coordination between suppliers and distributors. A mismanaged supply chain leads to delays, lost sales, and increased operational costs.
Walmart sets the gold standard in supply chain efficiency by leveraging RFID technology, real-time inventory tracking, and cross-docking warehouses. These systems allow trucks to unload and reload stock without prolonged storage, significantly cutting holding costs. Orders are processed automatically based on point-of-sale data, ensuring products reach stores precisely when needed.
Improving Cash Flow Management
Balancing inventory investment with operational needs is challenging because inventory spending directly impacts cash flow. If too much capital is invested in unsold stock, businesses struggle with liquidity issues. To balance investments, companies must adopt lean inventory models, negotiate better payment terms, and track inventory turnover rates.
Retailers like Costco focus on high inventory turnover, selling bulk products at lower margins to ensure fast-moving stock that keeps cash flow steady.
Enhancing Customer Satisfaction
Another major objective of inventory management is to ensure that products are delivered on time and that service levels are maintained. Meeting customer expectations hinges on accurate order fulfillment, quick delivery, and stock availability. Delays and backorders frustrate customers, leading to lost loyalty and negative reviews.
Nike ensures customer satisfaction by employing omnichannel inventory management. Their system integrates online and in-store inventory, allowing customers to check availability before purchasing. If a product is out of stock at one store, they offer ship-from-store fulfillment, sourcing the item from another location.
Goals of Inventory Management
Businesses set inventory targets based on sales patterns, lead times, and cost considerations. They use tools like demand forecasting, historical data, and seasonal trends to determine reorder points and safety stock levels.
Aligning inventory with business objectives means balancing cost efficiency with service quality. If a company prioritizes fast delivery, it might hold extra stock near key markets.
For instance, you can set a goal to reduce the cost then the just-in-time (JIT) approach minimizes excess inventory while maintaining supply continuity. Effective inventory strategies directly contribute to profitability and competitive advantage.
Objectives of Inventory Control
Inventory control ensures stock accuracy and prevents financial losses from shrinkage, overstocking, or understocking.
Without strong control mechanisms, businesses face issues like theft, misplacement, or supply chain inefficiencies.
Inventory Tracking and Monitoring Systems
Barcode scanning, RFID, cloud-based ERP systems, and plenty of other methods can be implemented to track the inventory.
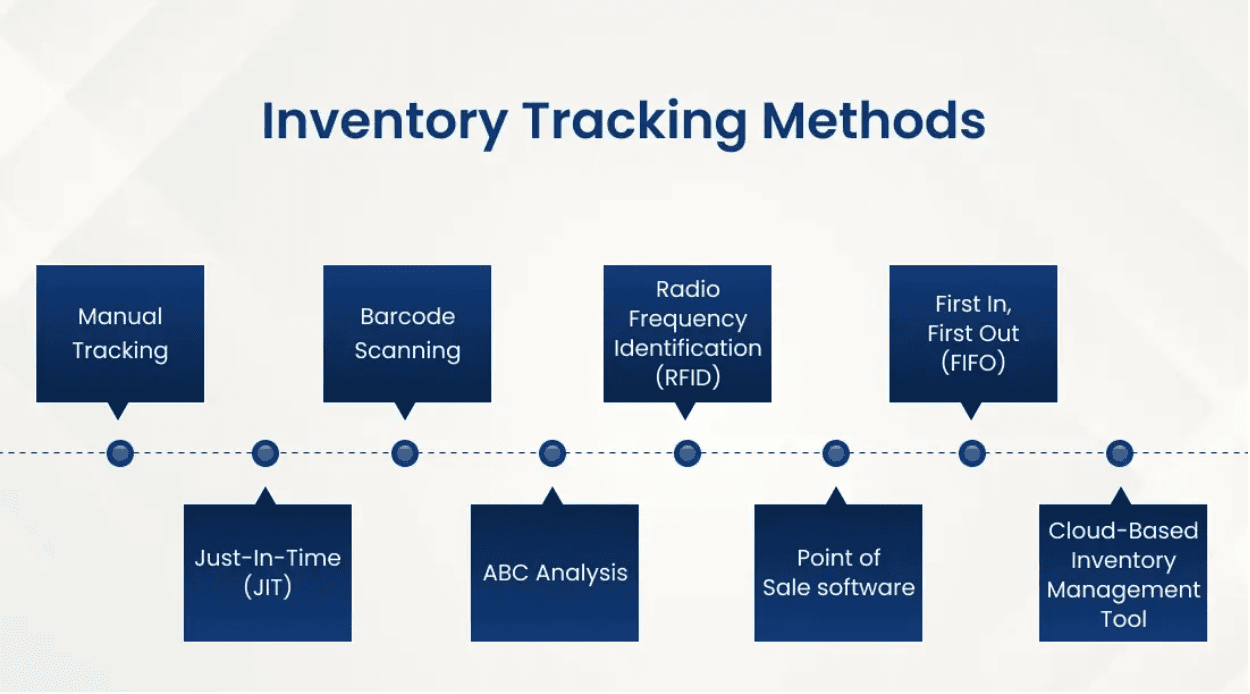
The goal is to leverage real-time tracking of stock movement, which will reduce the chances of human errors and increase visibility.
Techniques to Control Stock Levels and Prevent Overstocking
Companies use ABC analysis to categorize inventory based on value, cycle counting for continuous stock verification, and reorder point strategies to maintain optimal levels. These methods prevent excessive stock accumulation while ensuring demand is met efficiently.
Best Practices for Effective Inventory Management
Strong inventory practices prevent inefficiencies, improve profit margins, and ensure smooth operations. Businesses using structured approaches reduce errors and enhance productivity.
Utilizing Technology and Automation
Automation in inventory management involves using software and integrated systems to streamline stock control, order processing, and warehouse operations. Businesses that manage stocks use it to minimize human intervention, reduce errors, and improve efficiency.
If your business wants to start leveraging automation, consider cloud-based inventory management software like Kladana. Its intelligent demand forecasting, automated stock tracking, workflow automation, and real-time reporting ensure that businesses maintain accurate inventory levels, minimize stock discrepancies, and streamline operations.
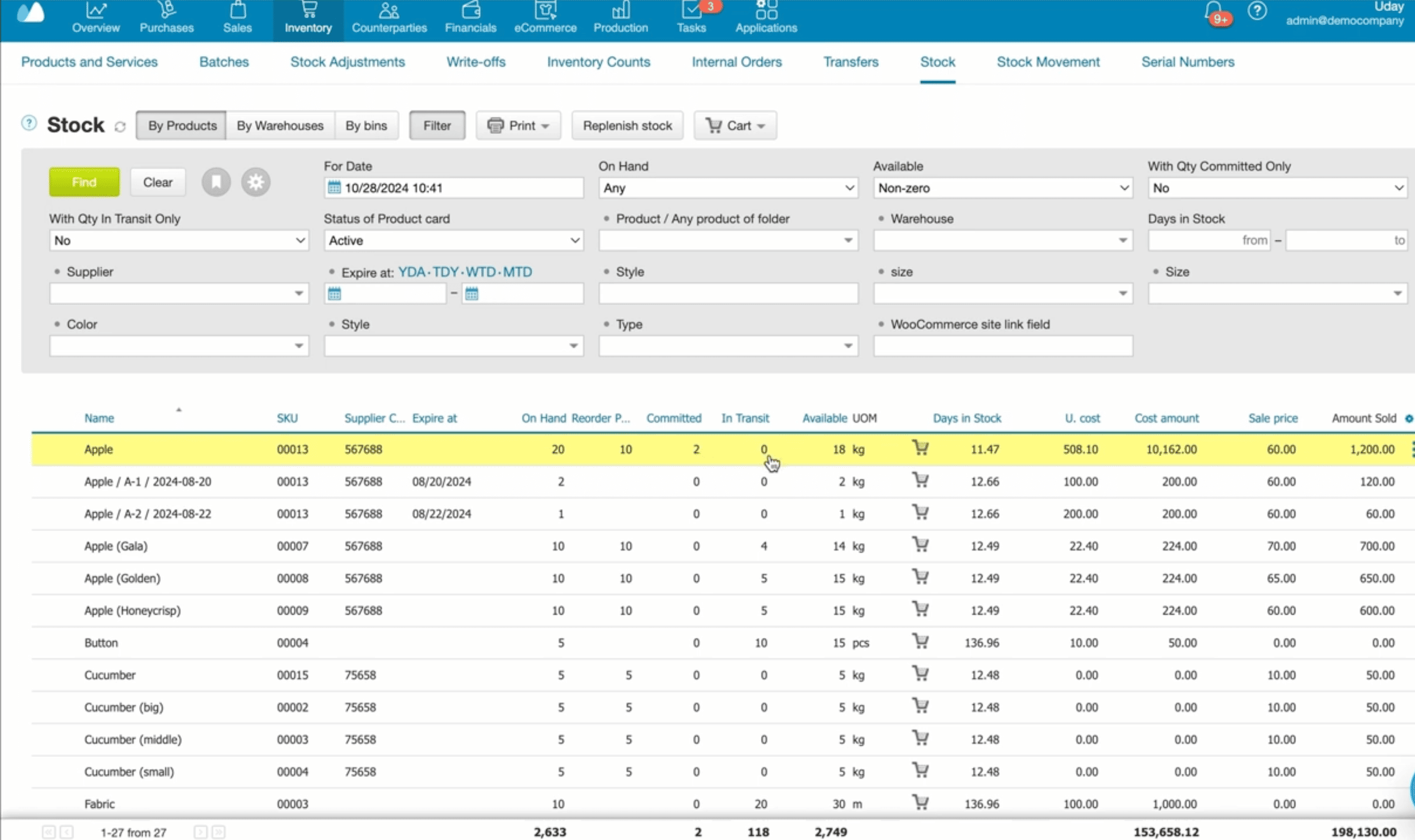
Kladana helps to eliminate manual errors and optimize inventory workflows, thereby reducing inefficiencies, speeding up order processing, and enhancing overall business productivity.
How Kladana Can Optimize Your Inventory Operations
✅ Enhanced Accuracy: Automates tracking to reduce errors and maintain precise stock levels.
✅ Cost Savings: Minimizes overstock and storage expenses by optimizing inventory.
✅ Improved Efficiency: Streamlines inventory processes, saving time and reducing manual labor.
✅ Real-Time Visibility: Provides up-to-date insights into stock status for informed decision-making.
✅ Better Customer Satisfaction: Ensures product availability, leading to timely deliveries and happier customers.
Implementing Just-in-Time (JIT) Inventory
JIT minimizes excess stock by ordering only when needed. This strategy works well for companies with reliable suppliers and predictable demand.
Conducting Regular Audits and Demand Forecasting
Periodic stock checks prevent discrepancies, while advanced forecasting tools analyze sales trends to adjust inventory levels accordingly.
Challenges in Inventory Management and How to Overcome Them
Inventory problems don’t just eat away at profits — they create delays, frustrated customers, and a logistical mess that’s tough to untangle.
Whether it’s misplaced stock, supplier hiccups, or outdated products clogging up space, these issues are the difference between a well-oiled machine and a business constantly putting out fires. Let’s understand the major challenges and solutions to fix them.
Stock Discrepancies
Have you ever received an inventory report stating that you have 500 units in stock, but when you checked, there were only 470? That’s a stock discrepancy.
Human errors, theft, miscounts, packaging errors, supplier misdeliveries — all of it messes up stock accuracy. It’s a nightmare when you’re running tight on space, and every unit counts.
Strategy to fix it: Barcode scanning + RFID tracking
Manual entries are a disaster waiting to happen. Implement a real-time inventory system that tracks every movement — purchases, returns, transfers — without human error.
Major businesses in retail e-commerce, such as Zara and Nike, use RFID to keep shelves stocked with 99% accuracy.
Supplier Delays
A supplier tells you they’ll deliver in three days, but it turns into three weeks — and now you’ve got empty shelves, upset customers, and a backlog of orders.
Sound familiar? Supplier delays hit businesses hard, especially when there’s zero backup plan.
Strategy to fix it: Diversify your suppliers. Never depend on just one.
Build relationships with multiple vendors so that if one supplier drops the ball, another can pick it up. Also, negotiate penalty clauses for late deliveries so vendors stay accountable.
Overstocking & Dead Stock
Too much stock might sound like a good problem, but it’s capital sitting idle. Excess inventory means high storage costs, waste, and markdowns that eat into your margins.
And if products expire or become obsolete, then it’s the money that goes straight down the drain.
Strategy to fix it: Use demand forecasting tools
These tools analyze buying patterns so you don’t over-order. Implement just-in-time (JIT) inventory, so stock arrives right when you need it — not months ahead.
Poor Warehouse Organization
Your team wastes hours searching for products. Orders take forever to process. Shipments get delayed because items aren’t where they should be. If your warehouse isn’t optimized, you’re bleeding time and money.
Strategy to fix it: Zone-based warehouse organization
Store your best-selling products in easily accessible areas. Use a barcode tracking system to track their location instantly. Make your warehouse work for you, not against you.
Invest in a Robust ERP Solution to Manage Your Inventory
For just $60 per year, Kladana ERP equips trade, e-commerce, and manufacturing businesses with the tools they need to streamline operations.
Kladana ERP: Powerful, Affordable, and Easy to Use
Here’s what you get:
✅ Fast support response (5–15 minutes on workdays)
✅ Up to 3 personalized onboarding sessions
✅ Unlimited API access
✅ Seamless integrations
✅ Automated tasks and reminders
✅ Cash flow gap prevention
✅ Strong data security
Kladana is packed with features yet simple to use. Get started in just 15 minutes with a 14-day free trial. No credit card required!
FAQs on Objectives of Inventory Management
It’s time to address some common questions around inventory management.
What are the primary objectives of inventory management?
To balance stock availability, minimize costs, improve cash flow, and enhance customer satisfaction.
How does inventory management impact profitability?
Efficient stock handling reduces waste, prevents overstocking, and ensures timely sales, leading to better margins.
What are the key challenges in inventory control?
Common issues include inaccurate tracking, supplier delays, overstocking, and stock shrinkage.
How can businesses improve inventory accuracy?
By integrating real-time tracking, conducting regular audits, and refining demand forecasting models.
Why is inventory optimization critical for growth?
It prevents cash flow issues, ensures smooth operations, and supports scaling by maintaining efficiency.
What role does technology play in modern inventory management?
Technology automates stock tracking, order processing, and warehouse operations to reduce errors and improve supply chain efficiency.
How does demand forecasting help in inventory management?
Enables anticipate stock demands, prevents stockouts and overstocking, and optimizes procurement cycles for better cash flow management.
What are the different types of inventory management systems?
It mainly includes perpetual inventory systems (which track inventory in real time using automation and software) and periodic inventory systems (which count stock manually at set intervals).
How can businesses reduce inventory carrying costs?
By optimizing stock levels, implementing just-in-time (JIT) inventory, negotiating better supplier terms, and automating inventory control that minimizes excess storage and handling costs.
How can small businesses effectively manage inventory?
Inventory software like Kladana helps set reorder points, perform regular stock audits, and implement efficient stock rotation methods like FIFO (First-In, First-Out) to prevent losses.
List of Resources
- Amazon AWS — Amazon Customer Fulfillment Increased Productivity and Reduced Unplanned Equipment Downtime Using Amazon Monitron
- SCM Globe — Zara Clothing Company Supply Chain
- SupplyChain Digital — Nike — an omnichannel inventory management cautionary tale
- Dfrieght — Costco Supply Chain: Efficiency, Innovation, and Sustainability for Optimal Operations
- Kcode — How Walmart Uses RFID Technology to Save Millions