Managing raw material inventory efficiently can be the difference between smooth production and costly delays. For instance, if a company produces cosmetics, managing the inventory of ingredients like essential oils, pigments, and emulsifiers ensures that products meet quality standards and are delivered on time.
Tracking raw materials inventory — whether via ERPs or MRPs, Excel templates, or dedicated inventory apps — helps businesses monitor stock levels, control costs, and avoid production delays. Understanding raw material inventory, including tracking methods, formulas, and challenges, enables companies to maintain efficiency while minimizing costs, resulting in a stronger bottom line.
- What Is Raw Materials Inventory Management?
- Raw Materials Inventory Management Basic Strategies
- Raw Materials Inventory Management Dangers and Challenges
- How to Calculate Raw Materials Inventory?
- Raw Materials Inventory Management by ERP and MRP Solutions
- Raw Materials Inventory Management for eCommerce Businesses
- Frequently Asked Questions on Raw Materials Inventory Management
What Is Raw Materials Inventory Management?
Raw materials inventory management involves tracking, storing, and replenishing the inventory of raw materials in ways that optimize production efficiency and control costs.
Companies use various methods and software tools to streamline the management of raw materials, ensuring that production schedules run smoothly and that storage costs remain manageable.
What Are Raw Materials?
Raw materials are unprocessed resources used in production to create finished products. They include items like metals, wood, chemicals, and fabrics, which are essential in industries from manufacturing to construction. Proper management of raw materials ensures that production runs without interruptions due to stock shortages, while avoiding excess inventory that ties up capital and storage space.
Raw Materials Inventory Examples
The inventory of raw materials includes both direct and indirect materials.
-
Direct raw materials are the core items that become part of the finished product. For instance:
- Metals used in automotive and machinery manufacturing
- Lumber for furniture and construction
- Fabrics in the clothing industry
-
Indirect raw materials are essential for production but don’t become part of the final product. Examples include:
- Cleaning supplies used to maintain equipment in a factory
- Lubricants for machinery in a manufacturing plant
- Packaging materials for shipping finished goods
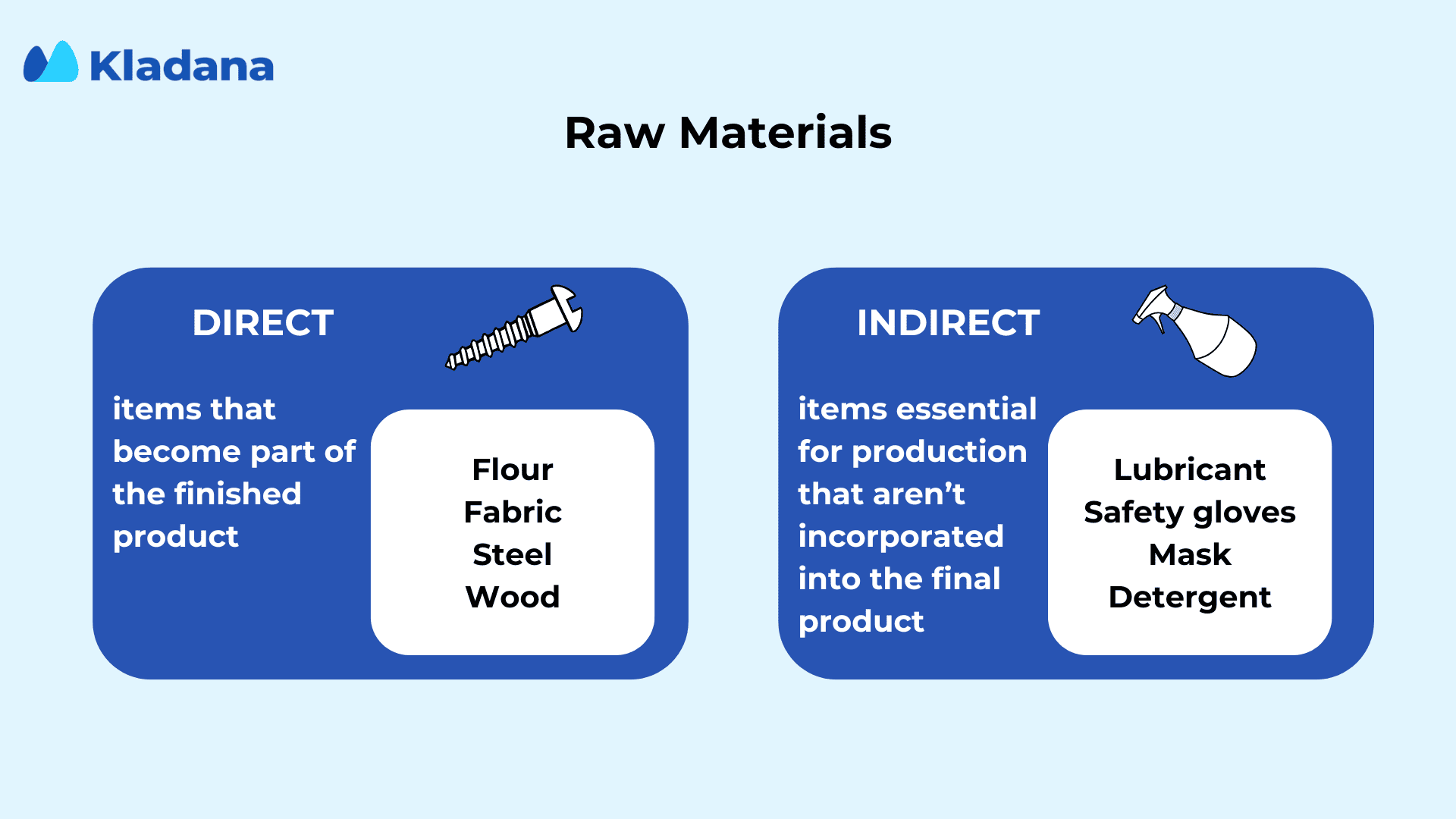
Why Is It Important to Manage Raw Materials Inventory?
Effective raw materials inventory management offers key benefits that contribute to the operational success of a business:
- Prevents production delays by ensuring essential materials are always available.
- Controls holding costs by keeping inventory levels optimized, and avoiding excessive stock.
- Improves cash flow through efficient purchasing practices that prevent overbuying.
- Supports quality control by making it easier to monitor the condition and turnover of materials.
- Increases efficiency by streamlining storage and reducing time spent searching for materials.
- Enhances customer satisfaction by minimizing delays in production, and ensuring timely delivery of finished products.
Get organized with detailed product records, batch monitoring, fast stock reporting, and precise inventory cost tracking.
- Manage various product options and pricing
- Create barcodes and print custom labels
- Sell items by unit or in bulk: kilos, packs, sacks, and more
- Monitor stock levels with comprehensive real-time insights
Raw Materials Inventory Management Basic Strategies
With the right strategies, businesses can ensure that stock levels are aligned with demand, preventing both shortages and overstock situations. Here are key approaches to enhance raw materials inventory management:
Track Raw Materials with Inventory Software
Using inventory management software simplifies the process of monitoring stock levels. A raw material management system can provide real-time updates, making it easier to forecast needs and streamline procurement.
Implement a Raw Material Inventory Formula
To calculate inventory levels effectively, use a raw material inventory formula. It helps determine the optimal stock quantity, balancing supply and demand. Regular use of this formula helps maintain a steady flow of materials without overstocking.
Utilize a Raw Material Inventory Excel Template
For businesses not ready to invest in advanced software, raw material inventory management Excel spreadsheets can be a simple and free solution. Tracking raw materials in Excel provides a clear overview of stock levels, purchase history, and reordering points, helping to avoid shortages.
Quality Control for Raw Materials
Quality control in raw materials is essential for ensuring that the materials used in manufacturing meet the required standards. Implementing quality control techniques for raw materials reduces defects in the final products and minimizes waste.
Raw Materials Procurement Strategy
The strategy of procurement of raw materials directly affects inventory levels. By developing a clear procurement process, businesses can ensure a consistent supply of raw materials while minimizing the risk of excess inventory.
Barcode System
Adopting a barcode system for raw materials inventory enhances accuracy and speeds up stocktaking. Barcode scanning allows businesses to quickly track raw materials as they are received, stored, or used in production, providing real-time data on inventory levels and reducing the risk of human error.
Just-in-Time Approach
The just-in-time (JIT) inventory approach helps companies minimize raw material inventory by ordering only the materials needed for production in a given period. This strategy reduces storage costs and eliminates the risks associated with overstocking, allowing businesses to operate more efficiently and with greater cash flow flexibility.
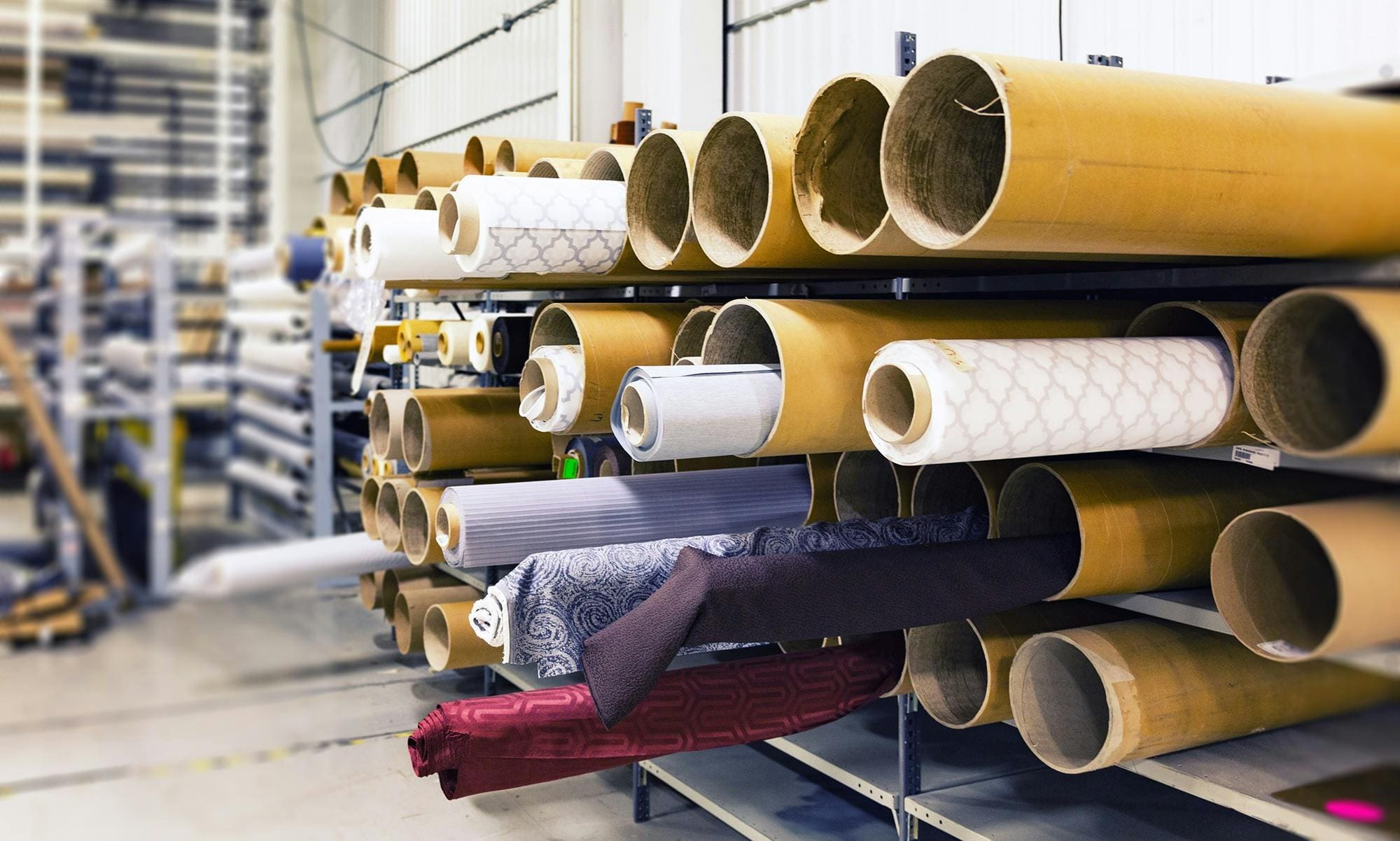
Raw Materials Inventory Management Dangers and Challenges
Effective raw materials inventory management has a potential to keep production processes smooth and cost-effective, but it comes with various challenges. Here are some of the primary issues businesses face with raw materials inventory:
Overstocking or Understocking
Maintaining the right inventory levels is crucial to avoid tying up capital in unused raw materials or, on the contrary, halting production due to shortages. Calculating the ideal levels often requires accurate formulas or an efficient raw materials inventory system.
Inventory Tracking and Accuracy
Without a strong raw material tracking system, errors in tracking inventory quantities and locations can lead to discrepancies. Using raw material inventory management software, such as ERP or MRP solutions, can enhance accuracy and streamline the tracking.
Reliance on Suppliers
Many companies rely on a limited number of suppliers, making them vulnerable to delays, price fluctuations, or quality inconsistencies. Building an efficient raw material procurement process and diversifying suppliers can help mitigate this risk.
Quality Control Issues
The quality control of raw materials is critical, as poor-quality raw materials can impact the end product’s reliability and customer satisfaction. Quality control techniques for raw materials should be implemented across all stages of the procurement and storage processes.
Storage and Handling
Storing raw materials improperly or using inadequate raw material handling systems can lead to spoilage, especially with perishable, fragile, or sensitive items. Proper storage practices are necessary to minimize waste and ensure materials are production-ready.
Inventory Space Limits
Limited storage space can restrict the amount of raw material inventory a business can keep on hand, which may ruin production schedules or lead to higher costs in case of frequent replenishments.
Inventory Turnover
High raw material inventory turnover rates may indicate efficient use of materials, while lower turnover can signal issues with production flow or demand forecasting. Monitoring the turnover ratio can help optimize stock levels and prevent unnecessary costs.
How to Calculate Raw Materials Inventory?
Calculating raw materials inventory involves understanding several key metrics that help in effective inventory planning and cost control: Ending Raw Materials Inventory, Beginning Raw Materials Inventory, Raw Materials Inventory Turnover, Average Raw Materials Inventory, and Cost of Goods Sold (COGS). Each metric provides insight into material flow, costs, and overall efficiency. Here’s an introduction to these key metrics and their importance in raw materials inventory management.
Ending Raw Materials Inventory shows the remaining stock at the end of a period. It helps businesses evaluate material consumption and anticipate future needs.
Beginning Raw Materials Inventory represents the inventory available at the start of a period. It’s essential for calculating inventory turnover and planning purchases.
Raw Materials Inventory Turnover measures how often inventory is used within a given period, indicating the efficiency of material usage.
Average Raw Materials Inventory offers a view of inventory levels over a period, providing a baseline for assessing turnover. It is calculated by averaging the Beginning and Ending Raw Materials Inventory:
Cost of Goods Sold (COGS) is the total cost incurred in production, directly linked to the consumption of raw materials. COGS provides insight into material costs relative to production, which helps in calculating inventory turnover ratios and assessing profitability.
These metrics are essential in managing raw materials efficiently, ensuring the company maintains enough stock for production while minimizing excess inventory.
Ending Raw Materials Inventory = Beginning Raw Materials Inventory + Purchases − Cost of Materials Used
Suppose a company begins the month with a Beginning Raw Materials Inventory of $10,000. During the month, it purchases an additional $8,000 in raw materials and uses $12,000 worth of raw materials in production.
Using these values:
Ending Inventory = 10,000 + 8,000 − 12,000 = 18,000 − 12,000 = 6,000
So, the Ending Raw Materials Inventory for this period would be $6,000. This figure then rolls over as the Beginning Inventory for the next period, ensuring continuity in inventory records.
How to Calculate Beginning Raw Materials Inventory?
Beginning Raw Materials Inventory is often calculated at the start of an accounting period or new cycle and is based on the Ending Raw Materials Inventory from the previous period. To ensure accurate tracking, record the Ending Inventory at the end of each period, which then serves as the Beginning Inventory for the next cycle.
Beginning Raw Materials Inventory = (COGS + Ending Raw Materials Inventory) − Raw Materials Inventory Purchased
Suppose a company has:
- Cost of Goods Sold (COGS) = $50,000
- Ending Raw Materials Inventory = $15,000
- Raw Materials Inventory Purchased = $40,000
Using these values:
Beginning Inventory = (50,000 + 15,000) − 40,000 = 65,000 − 40,000 = 25,000
So, the Beginning Raw Materials Inventory for this period is $25,000.
How to Calculate Raw Materials Inventory Turnover?
The Raw Materials Inventory Turnover formula is:
Raw materials inventory turnover = COGS / Average Raw Materials Inventory
Suppose a company has:
- Beginning Inventory = $25,000
- Ending Inventory = $15,000
- Cost of Goods Sold (COGS) = $50,000
First, calculate Average Raw Materials Inventory:
Average Raw Materials Inventory = (25,000 + 15,000) / 2 = 40,000 / 2 = 20,000
Then, use this in the turnover formula:
Raw Materials Inventory Turnover = 50,000 / 20,000 = 2.5
This result means the company turns over its raw materials inventory 2.5 times during the period, indicating the frequency with which inventory is used relative to COGS.
Raw Materials Inventory Management by ERP and MRP Solutions
Although raw material inventory can be managed in Excel or Google Sheets, specialized solutions will give you much faster results and save you from many common mistakes. Using ERP and MRP systems for managing raw materials can simplify tracking, improve visibility, and support timely decision-making.
ERP (Enterprise Resource Planning) and MRP (Material Requirements Planning) software solutions each offer unique benefits for controlling raw material inventory, with ERP providing broader integration across business functions and MRP focusing on manufacturing and production needs.
Using ERP Systems for Raw Materials Inventory Management
ERP systems bring a comprehensive approach to managing raw material inventory by integrating it with other critical functions such as procurement, finance, and sales. With ERP software, businesses gain real-time visibility into their raw material stock, helping prevent shortages or overstock situations.
Features like inventory tracking, raw material inventory formula calculations, and automated purchase orders support smooth replenishment and efficient resource allocation. ERP systems can also centralize data on raw materials, allowing businesses to track quality control for raw materials and align inventory levels with demand forecasts. This integration of raw material management within ERP systems ultimately enables businesses to make data-driven decisions and streamline operations across the supply chain.
Leveraging MRP Systems for Raw Material Inventory Control
MRP systems are designed specifically for manufacturing, offering targeted tools to calculate, track, and forecast raw material needs. By analyzing factors like production schedules and lead times, MRP software helps businesses avoid delays due to insufficient inventory of raw materials. This software can also provide insights through raw material inventory turnover ratios, ensuring that materials move through the system efficiently.
Additionally, MRPs and some ERPS support timely raw material procurement processes by automating reorder points and generating purchase orders based on current stock levels and forecasted demand. The result is a more organized raw material store management system, reducing waste and maintaining optimal levels for production.
Read‑alikes
Stock Control: Methods, Systems and Definitions
Barcoding for Manufacturing: Importance, 8 Paramount Benefits, and Step‑by‑Step Implementation Guide
Inventory Counting: Step‑by‑Step Guide on How to Conduct and Access the Results
ERP Inventory Management: 12 Benefits for Your Business in Full Guide
Raw Materials Inventory Management for eCommerce Businesses
Like any manufacturing business, eCommerce related to the production of goods depends largely on competent inventory control of raw materials. Each type of raw material here also goes through a chain of transformations before contributing to the final product.
If you know what and when happens to raw materials at each stage of this path, you can avoid problems associated with temporary losses in production, undersupply, overstocking, and loss of product quality at different stages of its readiness. Adequate inventory control of raw materials can help improve the efficiency of processes, and, ultimately, save money.
Why it is Important to Track Raw Materials in eCommerce
Tracking raw materials inventory is crucial for eCommerce businesses to meet customer demands and prevent production delays. Without an effective inventory of raw materials, businesses risk stockouts that disrupt production or, conversely, excess inventory that ties up capital and increases storage costs.
Raw material inventory tracking is especially important in eCommerce, where order volume may fluctuate seasonally or based on promotional campaigns. By actively monitoring raw materials, businesses can adjust purchasing to match demand, minimizing waste and improving production timelines. Quality control is another key benefit. By tracking raw materials, companies can ensure that only high-quality materials are used, which enhances the overall product quality.
Best Strategies for Raw Materials Inventory Management for eCommerce
Effective raw material management in eCommerce relies on a combination of accurate data and smart systems. A few core strategies include:
Implementing a Raw Materials Inventory Management System
Using raw material management software, eCommerce businesses can automate inventory tracking, monitor stock levels, and set reorder points to avoid shortages.
Using Inventory Management Formulas
Calculating metrics such as raw material turnover ratio and average raw material inventory formula allows businesses to analyze how efficiently they use their inventory and identify areas for improvement.
Adopting Quality Control for Raw Materials
Ensuring the quality of raw materials is essential for product integrity. A raw materials inventory system that includes quality checks can help maintain high standards and prevent costly recalls or customer dissatisfaction.
Optimizing Raw Material Procurement
Effective procurement processes ensure that materials are available just when they are needed, reducing both excess inventory and stockouts. This can be achieved by coordinating closely with suppliers and maintaining a consistent procurement schedule.
Utilizing Inventory Management Templates and Spreadsheets
For micro businesses with few products and a short list of raw material positions or those in the early stages, raw materials inventory management Excel templates offer an easy way to track stock without investing in more complex software.
Introducing Barcode System
Assigning unique barcodes to each type of raw material makes tracking dramatically easier. To get a complete, real-time view of raw materials it’s enough just to scan the barcode at each stage of movement, such as:
- upon receipt at the warehouse,
- upon transfer to a different warehouse,
- upon write-off,
- upon transition to the production stage.
Additionally, in case of defects, claims, or returns of finished products, business owners can always trace the raw materials back to their specific batch, enabling informed decisions on the next steps.
Basic Advantages of Accurate Raw Material Inventory Tracking for eCommerce Businesses
Accurate raw material inventory tracking brings several advantages to eCommerce businesses, including:
Cost Savings
With precise tracking, companies can prevent overstocking and understocking, both of which lead to unnecessary expenses. Proper raw material inventory levels reduce storage costs and improve cash flow.
Enhanced Production Efficiency
Knowing exactly what raw materials are available helps production teams plan better, leading to fewer interruptions and delays in the manufacturing process. This results in faster order fulfillment and increased customer satisfaction.
Better Decision-Making
Access to accurate inventory data allows managers to make informed decisions regarding purchasing, production schedules, and product launches. It also helps in forecasting future inventory needs, based on historical data and seasonal trends, ensuring that the business is always prepared for demand changes.
With these strategies in place, eCommerce businesses can streamline the control of raw materials, improve quality assurance, and enhance their overall profitability. Whether using software or templates, tracking raw material inventory accurately is an essential practice for sustainable growth.
Frequently Asked Questions on Raw Materials Inventory Management
In this section, we address some of the most common questions related to raw materials inventory management. Whether you’re looking to deepen your understanding or seeking effective strategies, these FAQs provide valuable insights for owners and managers of small and medium-sized businesses.
What is raw materials inventory?
Raw materials inventory refers to the stock of basic materials that are used in the production process to create finished goods. These materials can include anything from metals and plastics to chemicals and textiles. In the context of production, raw materials inventory plays a crucial role, as it directly affects the ability of a business to meet demand and maintain operational efficiency. Proper management of this inventory type ensures that production lines run smoothly, minimizing delays caused by material shortages while also reducing excess stock that can lead to increased holding costs.
How do you manage raw material inventory?
Effective management of raw material inventory involves several strategic approaches. First, establishing accurate forecasting methods can help predict demand, allowing businesses to maintain optimal stock levels. Implementing a robust inventory tracking system is also vital; this could include barcode systems or inventory management software that monitors stock levels in real time. Additionally, regular audits and cycle counting can help identify discrepancies and ensure data accuracy. Finally, fostering strong relationships with suppliers can enhance procurement processes, ensuring timely delivery of materials.
How can an ERP system help in managing raw materials inventory?
An ERP system can significantly enhance raw materials inventory management by providing a centralized platform for tracking and analyzing inventory data. With features such as real-time inventory monitoring, businesses can gain visibility into stock levels, enabling them to make informed decisions regarding ordering and procurement. An ERP system also streamlines processes by integrating inventory management with other business functions like purchasing, production, and sales. This integration helps prevent stockouts and reduces excess inventory, ultimately leading to improved operational efficiency and cost savings.
How can Excel be used for raw materials inventory management?
Spreadsheets can serve as a powerful tool for raw materials inventory management. Users can create customized templates to track inventory levels, orders, and supplier information. By leveraging Excel formulas, businesses can calculate metrics such as average inventory and turnover ratios. Setting up a simple dashboard in Excel allows for quick visualization of inventory trends, making it easier to identify when to reorder materials or assess excess stock levels.
What are the common challenges in raw materials inventory management?
Common challenges in raw materials inventory management include inaccurate demand forecasting, which can lead to either surplus stock or shortages, impacting production schedules. Poor visibility of inventory levels often results from outdated tracking methods, making it difficult to respond to changes in demand. Implementing automated systems can mitigate these issues. Additionally, managing supplier relationships can be challenging; delays or quality issues from suppliers can disrupt the entire production process. Regular communication and performance evaluation of suppliers can help alleviate these concerns.
What is the raw materials inventory turnover ratio?
The raw materials inventory turnover ratio measures how efficiently a business utilizes its raw materials inventory. Calculated by dividing the cost of goods sold (COGS) by the average raw materials inventory, this ratio indicates how many times inventory is sold or used over a specific period. A high turnover ratio suggests effective inventory management, while a low ratio may signal overstocking or weak sales, highlighting the need for improvement.
How do I calculate raw materials inventory?
Calculating raw materials inventory involves a straightforward process. Begin by determining the beginning inventory value at the start of the period. Next, add any purchases made during the period to this value. Finally, subtract the ending inventory value, which can be obtained through a physical count of inventory management software. This formula provides the total raw materials inventory for the specified period, allowing businesses to assess their inventory management effectiveness.
What are the best practices for managing raw materials?
Best practices for managing raw materials inventory include implementing just-in-time (JIT) inventory practices, which minimize stock levels and reduce holding costs. Regular training for staff on inventory management software ensures efficient usage of technology. Additionally, establishing a clear inventory policy that outlines procedures for receiving, storing, and tracking raw materials can enhance accountability and accuracy. Frequent supplier evaluations also contribute to maintaining quality and ensuring timely deliveries.
How do quality control measures impact raw materials inventory?
Quality control measures are integral to effective raw materials inventory management. Implementing strict quality standards helps ensure that materials meet production requirements, reducing waste and rework costs. Regular inspections and testing of raw materials prevent defective goods from entering the production line, safeguarding the final product’s quality. By maintaining high-quality standards, businesses can enhance their reputation and customer satisfaction while minimizing the costs associated with managing raw materials inventory.
What is the significance of procurement in raw materials management?
Procurement plays a pivotal role in raw materials management, influencing both inventory levels and production schedules. An effective procurement process ensures that materials are sourced from reliable suppliers at the best possible prices, reducing costs and maintaining quality. Establishing clear communication channels with suppliers allows businesses to respond quickly to changes in demand or supply chain disruptions, ensuring that raw materials are available when needed. Ultimately, effective procurement contributes significantly to the overall efficiency of raw materials inventory management, impacting a business’s bottom line.