Food suppliers everywhere scramble to keep up with growing orders and shifting consumer tastes. Many even juggle older processes that soak up time and allow plenty of room for mistakes.
A closer look at stats shows how the tide is turning: analysts at the Business Wire predict the global food automation sector will reach around $15.1 billion by 2030, spurred by the need for stronger output and consistent quality.
Sure, robotic arms technology gets plenty of attention. However, other forms of food and beverage automation, such as software platforms, sensors, and data analytics, also contribute to improving production lines.
Consistent product quality, faster output, and real-time insights are a few gains of this automation. So, businesses needing a smoother ride often lean toward food manufacturing automation or automation in the food and beverage industry to streamline everything from raw material intake to final packaging.
It is safe to see it as a path to slash expenses and maintain freshness, which matters a lot in today’s world. Especially when faster results, better hygiene, and more stable workflows are key business goals.
A combination of technology and thoughtful planning can bring those goals within reach.
Read on to find out what’s in store.
Challenges in the Food Manufacturing Industry
First up — the challenges that manufacturing companies face. They confront different hurdles, like unpredictable labor supplies and tighter regulations. Shoppers expect new flavors and fast service, while owners struggle with overhead and safety rules shifting quickly.
Some plants even have trouble balancing speed with high hygiene standards. Below, we’re highlighting some of the major challenges in the food manufacturing industry.
Common issues
First, let’s explore some of the highly possible issues that require a proactive approach to address them head-on.
Labor shortages
Labor shortages can strike at any moment. Some regions struggle to find skilled workers to run equipment, while others scuffle with fast turnover and repeated training cycles. Turnover and unfilled positions slow production, especially during peak seasons, while training requirements for new employees drain time and resources.
Product consistency
Customers value items that look and taste the same every time. Manual processes sometimes lead to small differences in color or texture. For example, slight variations in temperature or ingredient measurements can derail taste, aroma, or texture, hampering your brand’s image.
Safety requirements
Inspections for contaminants or pathogens grow more thorough every year. Teams relying on manual checks struggle with record-keeping and timely interventions.
Growing demand for faster production
Another key challenge in the food manufacturing business is catering to growing business demands.
Here’s how it affects:
- Retailers expect quick turnaround to keep shelves stocked. Delays in fulfilling large orders mean losing business to more modernized rivals.
- Price-sensitive markets put pressure on operators to cut costs without sacrificing quality.
Additional Sub-Challenges
There are a few other small challenges that can impact your business, such as —
- Inventory Oversight: Large variations in raw materials and packaging supplies may result in overstock or spoilage if they are not well-tracked
- Compliance Complexity: Different markets apply unique rules on labeling, nutritional facts, and sanitation. Plants with old systems may get trapped in paperwork
Role of Automation in Food Manufacturing
Battling the challenges we discussed and more requires pivoting to automation. An automated approach brings fresh energy and speed to day-to-day food manufacturing processing operations.
Many plant owners adopt conveyor systems or software-based solutions that track ingredients from arrival to final dispatch.
You also have modern systems that run continuously, lower waste, and help analyze the product flow more closely.
With the greater role automation plays in food production, you’ll see improvements in labor expenses, consistent flavor and texture, and minimized downtime due to quick error detection. Ultimately, it all leads to manufacturing food products that maintain uniform taste, color, and packaging, making them more attractive to buyers.
Benefits of adopting automation for food manufacturing
Gains go far beyond the product quality and profitability when you adopt automation in the food manufacturing business.
Software platforms such as ERP or MRP tie together order management, raw material checks, and financial data.
A system like Kladana’s Food & Beverage ERP can capture and present data in one location and help operators see patterns in cost overruns or inventory gaps.
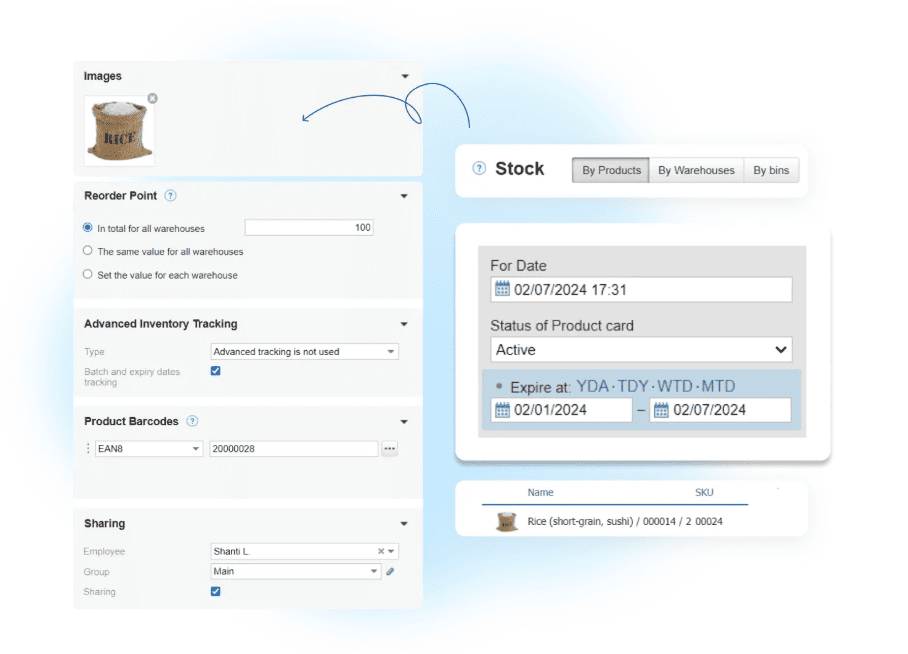
Below, we’re highlighting the same:
- Faster Throughput: Automation enables the use of equipment programmed for high-speed operations, which pushes more units per hour.
- Cost Reduction: There’ll be fewer people handling tasks to cut overhead, and standardized processes — ultimately reducing misfires or spoilage.
- Quality Consistency: You’ll benefit from automated checks to maintain uniform color, shape, and taste across massive batches.
- Scalability: Plants scale up by adding more hardware or modules, which is simpler than overhauling the entire layout.
Types of Automation
There are several types of food manufacturing automation to choose from. It all depends on what you want to focus on. Is it packaging, manufacturing, supply chain, etc.?
Below, we’re starting with a few of those.
- ERP and MRP Solutions: Tools like Kladana ERP gather sales, stock, and financial data under one umbrella so that you don’t have to juggle multiple spreadsheets.
- Machine Vision: Smart cameras detect imperfections in fruits, dough texture, or packaging seals to help you improve food quality control automation.
- Robotics in Food Manufacturing: Robotic arms, pick-and-place gadgets, and collaborative robots (cobots) handle repetitive tasks.
- Sensors and IoT: Devices measure temperature, humidity, and more, keeping staff informed through real-time dashboards. It’s a common approach in food processing automation to prevent spoilage.
A glance at the table below can help identify the type of automation in the food industry and its impact area (s):
Automation Type | Usage | Impact Area |
ERP and MRP Solutions |
Gather sales, stock, and financial data under one roof. |
Production management, cost tracking, and smoother inventory control |
Machine Vision |
Employs smart cameras to detect defects, shape variations, or package issues in real time. |
Faster quality checks, reduced waste, consistent brand standards |
Robotics in Food Manufacturing |
Uses robotic arms and pick-and-place systems for repetitive or heavy tasks. |
Lower labor costs, steady production speed, and improved safety for human workers |
Sensors and IoT |
Monitors temperature, humidity, and other factors through real-time dashboards. |
Food safety, early detection of issues, efficient environment control, and data flow |
Companies Who Adopted Kladana’s ERP Automation in Food Manufacturing
Owners who adopt automated processes often point to tangible results. Plenty of business owners have already leaped.
So, if you’re interested, we’ve covered a few practical results that matter when evaluating food automation.
Unicorn Natural Products
This one is a facility run by Unicorn Natural Products, an Indian manufacturer of spices and plant extracts. They moved from spreadsheets to specialized software and reported fewer data mismatches and quicker cycle times.
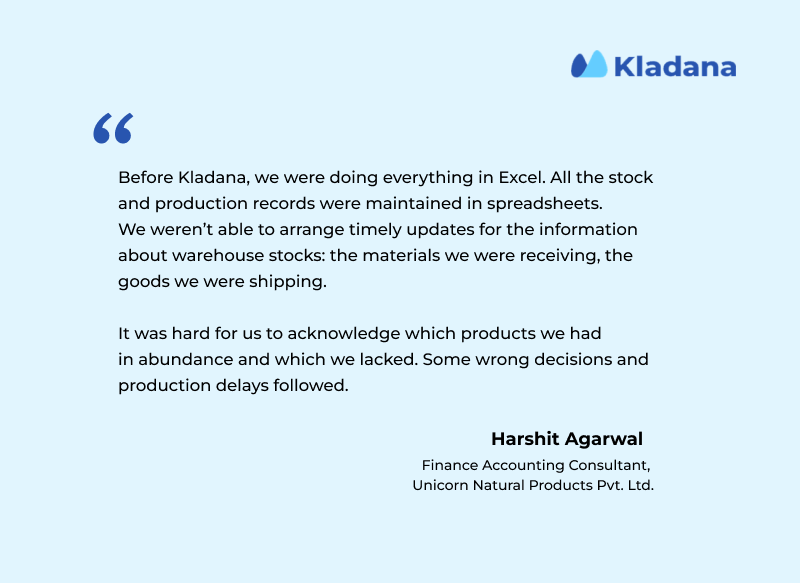
Since all inventory management involved batch details entered only once, there was an immediate drop in manual errors.
R&A Artisanal Foods
Next is the R&A Artisanal Foods, a small chocolate and coffee operation that integrated production tracking and order management. As a result, they gained clarity on daily stock, output, and raw material usage.
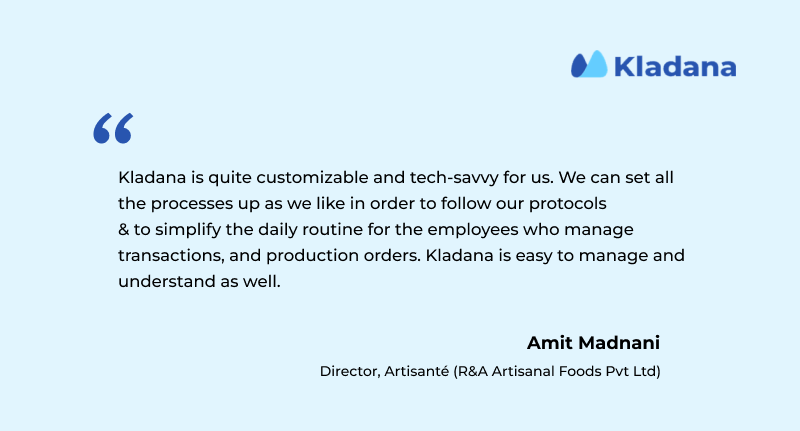
Also, their workers no longer flipped through handwritten logs or spreadsheets — instead, they leveraged real-time data to identify when cocoa beans or coffee grounds needed restocking.
Space
One brand of lemonade, Space, installed technology that reduced manual labor costs by a factor of 18 compared to older setups.
They adopted sensors and timers to maintain precise carbonation levels, saving effort and trimming energy bills.
More Ryadom
Another venture, More Ryadom, which focuses on oysters, saw its annual revenue climb to $230,000 a year after shifting to a more organized digital system — Kladana. We helped them automate packaging routines, which helped maintain consistent freshness in a product that spoils easily.
These examples show that relying on digital solutions, mechanized lines, or a combination of both benefits both large-scale and niche producers. Ultimately, regardless of the operations’ size, you are expected to see fewer logjams and production errors after deploying automation food strategies.
Invest in Kladana as Your Food Manufacturing Automation Software
Key benefits our ERP offers:
✅ Comprehensive inventory management — Monitor raw materials, work-in-progress, and finished goods in one unified system.
✅ Batch tracking & quality control — Ensure product quality with batch tracking and quality checks during receiving.
✅ Expiry date monitoring — Reduce waste by tracking expiry dates and implementing timely write-offs.
✅ Automated reorder alerts — Set reorder points and receive low-stock notifications to maintain optimal inventory levels.
✅ Precise production planning — Create Bills of Materials (BOMs), launch production orders, and calculate unit costs for accurate pricing.
✅ Multi-channel sales management — Handle sales across field operations, wholesale, and online platforms seamlessly.
✅ Insightful reporting & analytics — Analyze sales, profits, and stock movements to make informed business decisions.
Kladana simplifies your food and beverage manufacturing processes, enhancing efficiency and profitability.
Start your 14-day free trial today. No credit card required!
The Future of Food Industry Automation
Developments in robotics, data analytics, and sensor networks promise to shake up how items get processed, packaged, and shipped. Such recent advances hint at a big shift in food and beverage industrial automation.
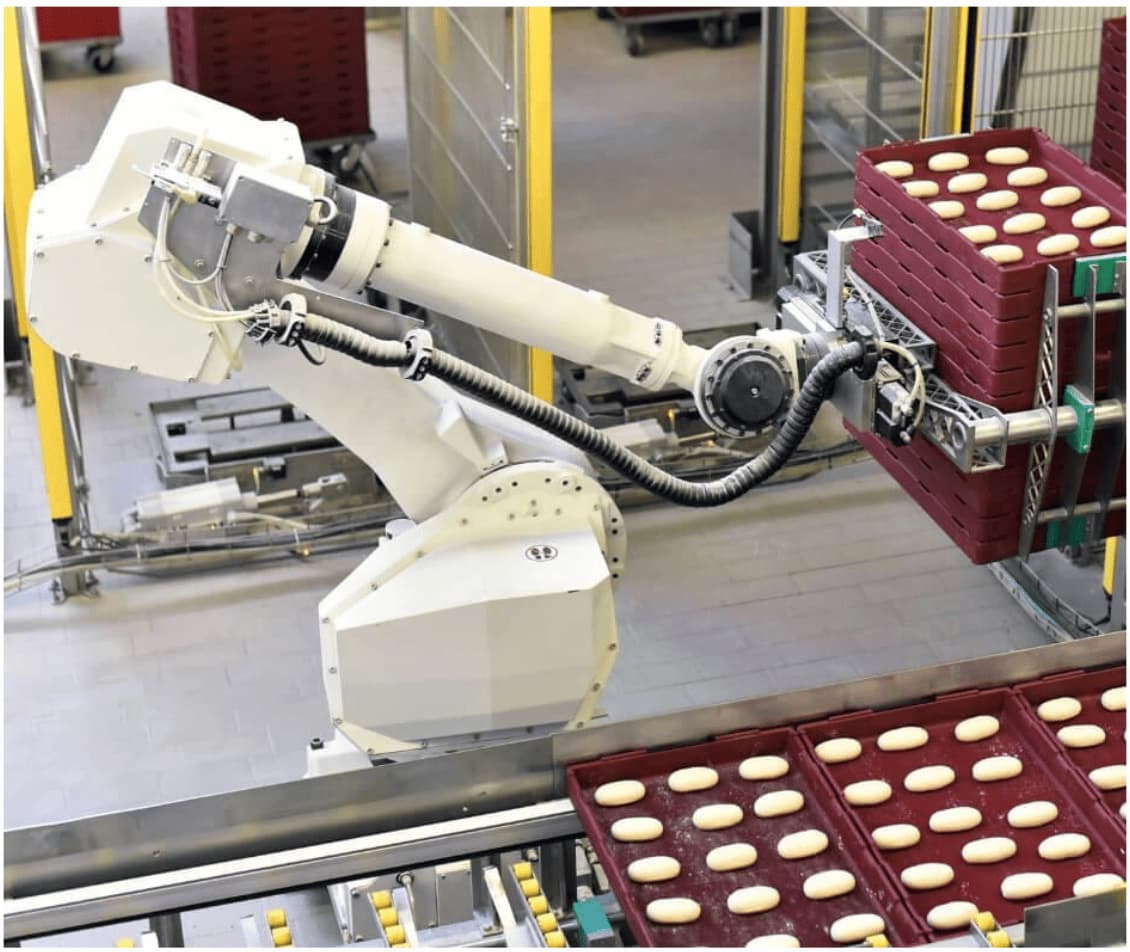
Factories aim to connect every step, from receiving raw ingredients to final shipping, through smart devices and data-sharing platforms.
These new technologies that stand out include:
AI-Driven Sorting and Machine Learning for Food Production
AI-driven sorting equipment can detect bruised apples or discolored vegetables faster than human eyes. That approach cuts waste and keeps only the best produce moving forward. A strong focus is placed on AI solutions that recognize anomalies in texture or color.
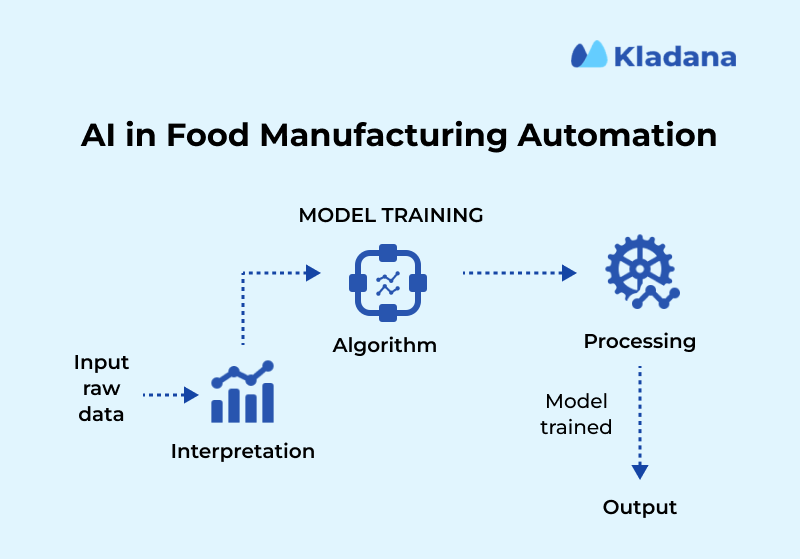
Food safety authorities set tight guidelines, so quick detection of possible hazards avoids contamination. Some businesses experiment with collaborative robots — known as cobots — that work closely with people, handling repetitive tasks or heavy loads.
Predictive maintenance also steps into the picture, since sensors detect machine wear before serious breakdowns occur. Operators swap out faulty parts on a planned schedule, leading to fewer last-minute halts.
- Cameras equipped with artificial intelligence spot mold, color defects, or bruising on produce
- Machine learning models learn from historical data, flagging small issues before they become large-scale recalls
- Helps reduce food waste and maintain product uniformity
Predictive Maintenance
Data analytics continues to gain ground. Smart factories gather volumes of information on temperature, production speed, worker hours, and consumer demand.
Algorithms spot patterns, forecast upcoming inventory needs, and highlight ways to trim costs.
- Sensors on motors, gearboxes, or conveyor belts track vibrations and temperature
- Maintenance teams get early notifications, avoiding costly breakdowns during peak periods
- Lowers disruptions and extends the life of equipment
Smart Factories and Supply Chain Automation in the Food Industry
IoT devices connect every stage, from raw ingredients in refrigerated trucks to packaging lines measuring product weight in real time.
Linking all that data was once a dream. Now it’s a pressing strategy for brand owners who want fewer returns and better compliance with industry rules.
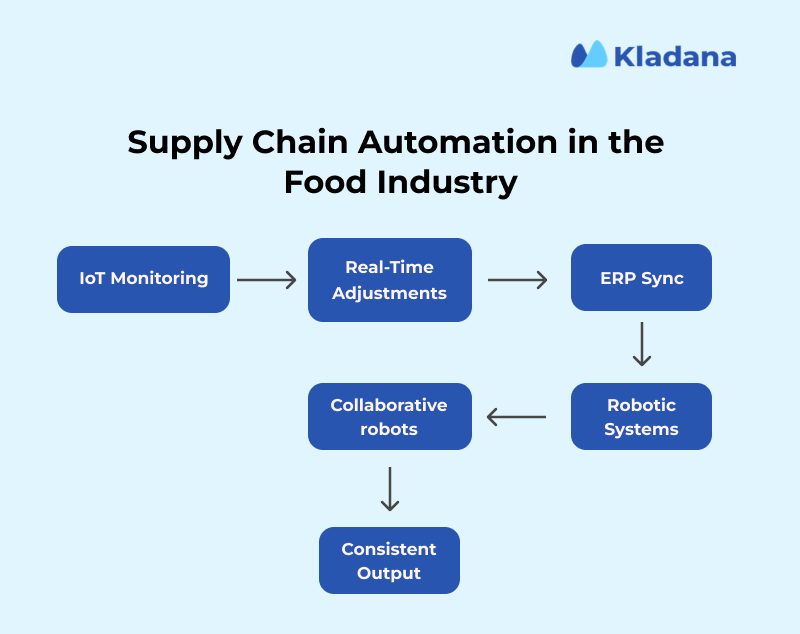
IoT devices stream real-time info on stock levels, production speed, and equipment status.
- Supervisors adjust the system instantly if a reading looks off, improving safety and efficiency.
- Machine data syncs with ERP software for streamlined ordering and shipping schedules.
- Robotic arms handle repetitive tasks like packing or stacking, freeing staff for quality checks.
- Collaborative robots (cobots) can work right beside employees, minimizing strain or injuries.
- Better throughput and fewer product defects, since robots don’t suffer from fatigue.
Challenges and Considerations When Adopting Automation
Jumping into food and beverage automation can raise several concerns, from finances to personnel shifts. It’s because adopting automated systems may overwhelm you.
Sure, large-scale installations often require infrastructure upgrades, so there’ll be a debate about short-term pain vs. long-term gains. But the success of food automation relies on thoughtful planning, realistic timelines, and open communication with teams.
Below, we’ve highlighted some of the major challenges that you may face when implementing automation in food manufacturing.
Initial Investment Costs
The initial cost can be too high when switching to automation. A few of the major automation costs can be —
- Robotics or specialized software might carry a high price tag
- Some facilities need building upgrades or advanced wiring, which adds to the bill
- Owners often compare leasing vs. buying for big-ticket machinery
Training Requirements
When you adopt automation, you’ll also need staff that is well-versed in the skills to use automation.
So, some of the training challenges are —
- Traditional staff feel uncomfortable with digital dashboards or machine interfaces
- Investing in conducting workshops, mentoring, and providing reference materials helps everyone keep pace.
- How to increase employee buy-in so that they see new technology as a tool for better results, not a threat to job stability
System Integration Hurdles
Your existing or conventional systems may become redundant the moment you choose the automation.
The bottlenecks on this front can be —
- Old conveyor belts or weight scales may not connect smoothly with modern IoT sensors
- Overcoming these gaps might involve new hardware or middleware solutions
- Data silos leading to missed insights that hamper decisions on the production floor
Technical Glitches
While not an immediate challenge, there’s a possibility that your newly functional automated food production solutions may face technical glitches.
Some of the areas where it can happen are —
- Sudden power loss or software bugs can freeze entire lines
- Backup servers, on-call support, and on-site tech expertise protect against extended downtimes
Regulatory and Safety Challenges
Lastly, you can’t rule out the issues that may crop up due to compliance.
The adoption of automation will need you to make sure that your newly designed systems take care of the following —
- Food safety audits demand precise tracking of temperature, ingredient sourcing, and cleanliness
- Automated clean-in-place methods must reach all surfaces and maintain consistent chemical ratios
- Overlooking a step during setup might leave hidden zones prone to contamination
Conclusion
Many sectors rely on food industry automation to meet rising demands while keeping products safe, tasty, and ready for market. Factories like yours can use a mix of blend robotics, IoT, and advanced software, which often breeze through record volumes without losing consistency.
We’ve covered the success stories of small and medium businesses that leveraged automation in the food industry. Overall, they were successful in bringing down costs, slashing errors, and boosting revenue.
Start with a solution like Kladana’s Food & Beverage ERP. It’ll serve as a great, solid digital backbone to unify food orders, inventory, and financial tracking. Plenty of choices exist, and picking the right path depends on each brand’s goals and budget.
Automate your Food Manufacturing with Kladana’s Advanced ERP Solutions
List of Resources
Businesswire — Global Food Automation Strategic Business Report 2023