Contract manufacturing and subcontracting have become essential production strategies, especially for small and medium-sized businesses aiming to streamline operations and reduce costs. Through subcontract manufacturing, businesses can assign specific tasks or processes to specialized third-party manufacturers, freeing up resources to focus on core competencies and product innovation. This outsourcing approach allows companies to reduce overhead, control inventory efficiently, and scale production to meet demand without compromising quality.
For businesses considering the benefits of contract manufacturing, understanding its various processes, key advantages, and how to select the right subcontractor is critical for achieving a successful partnership. In this guide, we explore these essential facets, highlighting practical insights that support decision-makers in optimizing their manufacturing strategy.
- What is Contract Manufacturing?
- Understanding Subcontract Manufacturing
- The Contract Manufacturing Process
- The Subcontract Manufacturing Process
- Challenges and Risks of Manufacturing Subcontracting
- Key Considerations When Choosing a Contract or Subcontract Manufacturer
- Frequently Asked Questions on Contract and Subcontract Manufacturing
What is Contract Manufacturing?
Contract manufacturing is a strategic approach where businesses delegate part or all of their production processes to specialized third-party manufacturers. This allows companies to focus on their core competencies while gaining the advantages of established manufacturing expertise.
Definition and Importance
Contract manufacturing involves a business engaging a third-party manufacturer to produce goods, partially or fully, on its behalf. By outsourcing these production tasks, companies, particularly small and medium-sized enterprises (SMEs), can lower operational costs, access advanced manufacturing technologies, and maintain focus on strategic priorities like product development or market expansion. This model is especially appealing for businesses that require high-quality outputs but may lack the resources to invest in expensive equipment or skilled labor in-house. Key benefits of contract manufacturing include:
Reduced Operational Costs: Minimizes the need for capital investment in machinery and facilities.
Access to Specialized Expertise: Provides companies with industry-specific skills and advanced technology.
Scalability: Allows flexible production adjustments based on demand without incurring additional overhead.
Focus on Core Business: Frees up resources for strategic priorities such as R&D and marketing.
Ultimately, contract manufacturing enables companies to compete effectively by optimizing resources while retaining control over their core business.
Examples of Contract Manufacturing
Contract manufacturing has a significant role across diverse sectors, supporting industries with specialized production needs. Here are examples from different industries:
Electronics: Companies often rely on contract manufacturers for tasks like circuit board assembly, which requires precise engineering.
Pharmaceuticals: Businesses outsource complex formulation, production, and packaging processes to meet quality standards efficiently.
Automotive: Contract manufacturers produce individual components like transmissions or electronics, leveraging expertise in precision and mass production.
For small and medium-sized businesses, this approach can be transformative. Rather than investing in full-scale production facilities, they can leverage experienced partners with proven manufacturing capabilities. This flexibility not only helps streamline their operations but also shortens time-to-market, enabling faster adaptation to customer needs and market changes. Through contract manufacturing, SMEs gain access to resources and skills that might otherwise be challenging or costly to acquire, positioning them to thrive in competitive markets.
Read‑alikes
Bill Of Materials (BOM): Definition, Examples, Format and Free Template
Managing Production in a Small Manufacturing Company: Planning, Control, and Profit Calculation
Full Guide to MRP Solutions: Core Features, Advantages and Pitfalls
Understanding Subcontract Manufacturing
Subcontract manufacturing is a more specific form of contract manufacturing where businesses outsource particular components, subassemblies, or processes to third-party manufacturers. This strategy allows companies to streamline production by focusing on their core activities while relying on subcontractors to handle specialized tasks.
What is Subcontract Manufacturing?
Subcontract manufacturing refers to a production model where a business hires a third-party subcontractor to carry out specific tasks that contribute to the final product. Unlike full contract manufacturing, which can involve the complete production of goods, subcontract manufacturing generally involves a more targeted approach, such as producing a part or completing a specific stage of the manufacturing process. This approach is commonly seen in industries like automotive, electronics, and textiles, where certain components require specialized skills or equipment. Subcontract manufacturing offers flexibility by allowing companies to maintain control over the overall production while outsourcing specific functions to partners with the expertise and equipment necessary for those tasks.
Key Differences Between Contract and Subcontract Manufacturing
While contract manufacturing involves outsourcing entire production processes, subcontract manufacturing is more focused on specific components or stages of production. Key differences include:
Scope: Contract manufacturing typically covers full-scale production, from sourcing raw materials to the finished product. In contrast, subcontract manufacturing is narrower in scope, often limited to individual parts or stages of the production process.
Responsibility: In contract manufacturing, the third-party manufacturer is responsible for the entire production. With subcontract manufacturing, the primary business retains overall responsibility for the product, and subcontractors handle specific tasks, such as assembly, machining, or quality testing.
By understanding these distinctions, businesses can decide whether subcontracting specific tasks or outsourcing entire production lines is the most effective strategy for their operations. Subcontract manufacturing offers more flexibility but requires careful coordination to ensure quality and timing align with the business’s overall production goals.
The Contract Manufacturing Process
The contract manufacturing process involves a series of carefully planned stages to ensure successful production, from the initial design phase to the final delivery of products. Understanding this process is key for businesses looking to outsource manufacturing, whether it’s for a single product or an ongoing production line.
Planning and Design Stage
The planning and design stage is where the foundation for successful contract manufacturing is laid. Businesses must define clear product specifications, including materials, dimensions, and functionality. These details are critical for the manufacturer to accurately produce the item. At this point, companies must also identify and select the right manufacturing partner based on their capabilities, experience, and ability to meet quality standards. The selection process typically involves evaluating potential manufacturers’ technical expertise, past performance, and capacity to scale production.
Contract Negotiation and Agreement
Once a manufacturer is selected, the next step is to negotiate and finalize the contract. This agreement outlines key terms, including the scope of work, timelines, production volumes, pricing, and any penalties for non-compliance. It also includes quality control measures, ensuring that the final product meets the agreed-upon standards. Additionally, logistics and delivery expectations are clearly defined to avoid any confusion later on. A well-drafted contract sets the tone for a successful partnership by clearly stating both parties’ roles and responsibilities, protecting both the business and the subcontract manufacturer.
Production and Quality Control
With the contract in place, production begins. The subcontract manufacturer takes responsibility for producing the goods according to the defined specifications. Throughout this phase, quality control is a priority to ensure that the final products meet both the business’s standards and regulatory requirements. Manufacturers often implement rigorous testing processes, inspections, and compliance checks to verify quality at various stages of production. This ensures that defects are minimized, and the final product is consistent with the original design.
Logistics and Delivery
The final stage in the contract manufacturing process is logistics and delivery. Once production is completed, goods must be packaged and prepared for shipping. Businesses often collaborate with third-party logistics providers to handle distribution, ensuring that products are delivered on time and in the right condition. Proper coordination between the manufacturer and logistics partners is crucial to avoid delays and ensure smooth delivery to end customers. By maintaining an efficient logistics pipeline, businesses can guarantee a seamless product rollout.
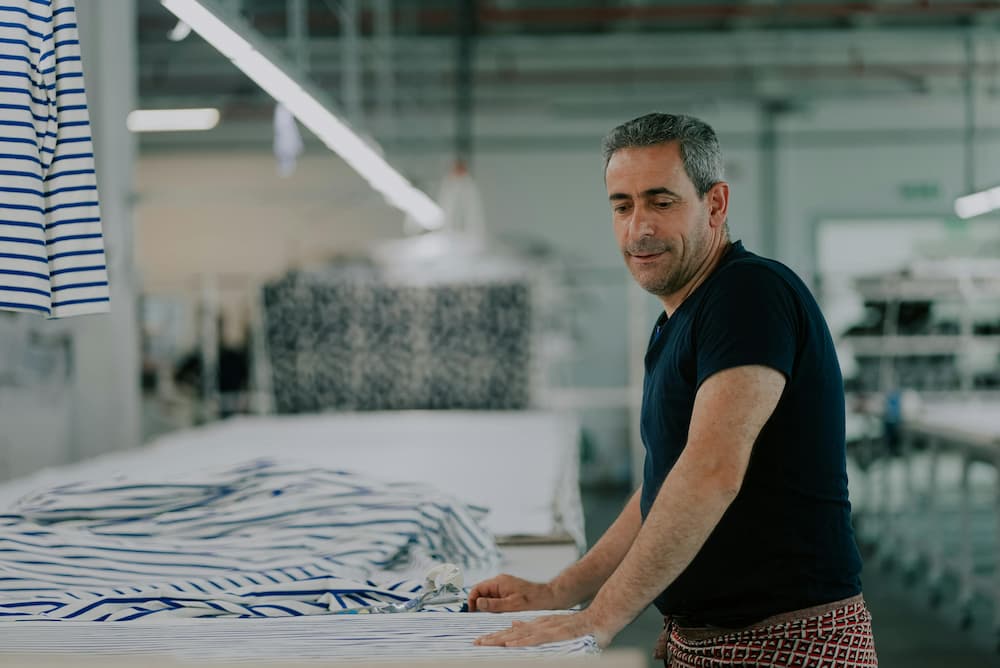
The Subcontract Manufacturing Process
Subcontract manufacturing focuses on contracting specific tasks or components of production rather than the entire manufacturing process. This allows businesses to reduce costs, leverage specialized expertise, and streamline operations. Understanding the stages of subcontract manufacturing can help companies make more informed decisions when outsourcing production tasks.
Identifying Tasks for Subcontracting
The first step in the subcontract manufacturing process is identifying which tasks or components can be outsourced. Typically, companies subcontract processes based on factors such as complexity, specialized knowledge, and cost efficiency. For instance, businesses may choose to subcontract tasks that require advanced technical expertise, like precision machining or specific assembly processes. Outsourcing these tasks helps reduce the need for in-house expertise and equipment, ultimately leading to cost savings. Companies also look for processes that are time-consuming or do not align with their core competencies, making them ideal candidates for subcontracting.
Selecting the Right Subcontractor
Choosing the right manufacturing subcontractor is vital for the success of the subcontract manufacturing process. Businesses must evaluate potential subcontractors based on experience, reputation, and production capacity. A reliable subcontractor will have a proven track record of delivering quality components on time and within budget. It is also important to assess the subcontractor’s ability to scale production and meet deadlines under varying demand levels. Transparency, communication, and the ability to meet quality standards are key factors in selecting the right partner. A thorough evaluation ensures that the subcontractor can align with the business’s production needs.
Monitoring Quality and Performance
Quality control is critical in subcontract manufacturing to ensure that outsourced tasks meet the required standards. Businesses should establish clear quality assurance protocols with the subcontractor, including inspection schedules and testing procedures. Regular performance monitoring can help identify potential issues early on, allowing for corrective actions before products are delivered. This ensures that the final output is consistent and meets the expectations of both the business and its customers.
Roles and Responsibilities of a Manufacturing Subcontractor
In the subcontract manufacturing process, the role of a manufacturing subcontractor is pivotal. Subcontractors are responsible for specific tasks within the broader production process, ensuring that the assigned work meets the required standards and deadlines. Their responsibilities extend from managing production to maintaining quality control, all while adhering to the terms of the contract with the client.
Overview of Subcontractor Duties
Manufacturing subcontractors are expected to handle a variety of tasks within the production process. Their primary duties include:
Ensuring that the product meets the required quality standards
Adhering to agreed timelines for production
Managing specific production processes assigned by the client, such as sourcing materials, operating machinery, performing quality inspections, or assembling components
Managing production challenges and resolving issues to maintain workflow
Ensuring that the final product aligns with the client’s specifications
Subcontractors must have the capacity to manage these processes efficiently, ensuring that production stays on schedule and within budget.
Communication and Reporting Requirements
Effective communication and regular reporting are crucial for the success of subcontracting relationships. Manufacturing subcontractors must maintain clear and consistent communication with the primary business, providing updates on the production progress, any potential delays, or issues that may affect delivery. Key communication tasks include:
- Submitting regular production reports
- Sharing quality inspection results
- Reporting any deviations from the agreed process or schedule
- Addressing potential challenges promptly
This level of transparency strengthens the partnership and ensures that both parties are aligned throughout the manufacturing subcontract process.
Benefits of Contract and Subcontract Manufacturing for SMEs
Small and medium-sized enterprises (SMEs) can greatly benefit from the contract and subcontract manufacturing process, which provides flexibility, cost savings, and access to specialized expertise. By choosing to outsource production, SMEs can streamline operations and focus on growing their core business.
Cost Efficiency
Outsourcing manufacturing processes offers significant cost advantages. By leveraging contract manufacturing, businesses can reduce overhead costs associated with maintaining production facilities, labor, and inventory management. Instead of investing in expensive machinery or expanding the workforce, SMEs can rely on external manufacturers to handle production. This also helps minimize the need for large inventory storage, as subcontractors often manage inventory as part of the manufacturing process. As a result, SMEs can:
- Lower operational expenses
- Avoid high initial capital investment in production equipment
- Reduce warehousing and inventory holding costs
- Eliminate the need for a large in-house workforce
These cost savings are particularly important for small businesses looking to optimize resources while maintaining competitive pricing.
Scalability
Another major benefit of outsourcing manufacturing is scalability. Contract and subcontract manufacturing allow businesses to quickly adjust their production volumes based on market demand. For SMEs experiencing fluctuations in demand, this flexibility is key to maintaining efficiency without the risk of overproduction or underproduction. Manufacturers and subcontractors typically have the capacity to scale up or down their operations with minimal lead time. This means that:
- SMEs can scale production to match seasonal demand
- Surplus production capacity can be managed by the subcontractor
- Businesses can avoid costly overproduction and underproduction scenarios
As a result, businesses have the agility to grow and adjust according to market needs, which is ideal for small businesses with fluctuating production requirements.
Access to Expertise and Technology
SMEs can also gain access to advanced technologies and skilled labor by partnering with established contract manufacturers. These external manufacturers often have specialized expertise, advanced machinery, and state-of-the-art facilities, which may be otherwise out of reach for smaller businesses. By outsourcing manufacturing, SMEs can benefit from:
Challenges and Risks of Manufacturing Subcontracting
Higher-quality products with fewer defects
Access to the latest production technologies without the need for large capital investment
Expert knowledge in specialized manufacturing processes, such as precision engineering or complex assembly
While subcontracting can provide numerous advantages to small and medium-sized enterprises (SMEs), there are challenges and risks that need careful consideration. Being aware of these potential pitfalls can help businesses manage subcontract manufacturing processes effectively and safeguard their operations.
Quality Control and Compliance Issues
One of the primary concerns with subcontract manufacturing is maintaining consistent quality and ensuring compliance with industry standards. When production is outsourced, the risk of variability in product quality increases. This can lead to defects, delays, or non-compliance with regulations, all of which can damage the brand and customer trust. To mitigate this risk, businesses can:
- Establish clear quality control standards and communicate them with the subcontractor.
- Implement regular audits and inspections at various production stages to ensure adherence to agreed-upon standards.
- Use detailed contracts that outline quality expectations and compliance with industry certifications.
By maintaining a hands-on approach and conducting thorough oversight, SMEs can reduce the risk of quality issues while keeping production on track.
Dependence on Third Parties
Another risk associated with manufacturing subcontracting is becoming too dependent on external partners. Over-reliance on a single manufacturing subcontractor can expose businesses to operational risks, especially if the subcontractor faces issues like financial instability or delays in production. To avoid this, businesses should:
- Diversify subcontractor relationships to reduce reliance on any single partner.
- Negotiate contingency plans that include backup options in case of subcontractor failure.
- Develop long-term relationships with multiple subcontractors to secure alternative production capabilities if needed.
This approach can help businesses ensure continuity of supply and mitigate risks related to subcontractor performance.
Intellectual Property and Confidentiality Risks
Outsourcing manufacturing also raises concerns about intellectual property (IP) protection and confidentiality. When sharing new product designs or proprietary processes with a subcontractor, businesses risk potential leaks or theft of sensitive information. To protect their IP, companies can:
- Include non-disclosure agreements (NDAs) and intellectual property clauses in contracts with subcontractors.
- Limit access to sensitive information by only sharing what is necessary for production.
- Consider using non-disclosure agreements and monitoring subcontractor activity to ensure confidentiality is maintained.
These measures help safeguard proprietary designs and prevent the unauthorized use or distribution of intellectual property.
Key Considerations When Choosing a Contract or Subcontract Manufacturer
Selecting the right contract or subcontract manufacturer is crucial for businesses aiming to optimize their manufacturing processes and ensure long-term success. Several factors should guide this decision-making process, from expertise and pricing models to certifications and compliance with regulations.
Evaluating Experience and Capabilities
When considering a manufacturing subcontractor or contract manufacturer, assessing their experience and capabilities is vital. A partner with a proven track record in the industry is more likely to deliver consistent quality and meet your production goals. Look for manufacturers who:
- Have a strong portfolio in your industry, demonstrating their ability to handle specific production needs.
- Offer a range of production capabilities, ensuring they can scale as your business grows.
- Are transparent about their production capacity and provide detailed information on lead times, equipment, and workforce capabilities.
A manufacturer with the right expertise will help reduce the risk of delays, quality issues, and other production-related challenges.
Cost and Pricing Models
Price is often a decisive factor in selecting a subcontract manufacturer, but it’s important to evaluate the long-term cost structure rather than focusing solely on upfront costs. Various pricing models can impact the overall cost-effectiveness of your partnership:
Fixed pricing offers predictability and works well when production volumes are consistent.
Variable pricing allows flexibility, making it ideal for fluctuating demand or custom orders.
Cost-plus pricing ensures transparency by adding a fixed percentage to the cost of materials and labor, helping both parties maintain a fair balance.
Make sure the pricing structure aligns with your financial goals and includes provisions for any potential cost increases over time.
Certifications and Compliance
It’s essential to verify that the contract or subcontract manufacturer complies with industry standards and regulatory requirements. Manufacturers should hold relevant certifications, such as ISO, that guarantee they adhere to established quality and safety protocols. Check that they comply with:
Industry-specific regulations, including environmental and safety standards.
International standards for product quality, ensuring consistent performance and reliability.
Any local or regional certifications that may apply depending on your market.
Ensuring that your manufacturing partner meets these requirements helps minimize compliance risks and ensures that the final product meets necessary quality and safety standards.
Frequently Asked Questions on Contract and Subcontract Manufacturing
This section answers common questions about contract and subcontract manufacturing, providing valuable insights for small business owners and decision-makers.
What is the difference between contract and subcontract manufacturing?
Contract manufacturing involves outsourcing the production of entire products to a manufacturer, while subcontract manufacturing focuses on outsourcing specific tasks within the production process. The difference lies in the scope of responsibility. A contract manufacturer is responsible for producing the full product, including all stages of production, whereas a subcontractor handles particular parts or processes of the production.
How do I find reliable subcontract manufacturers?
To find a dependable subcontract manufacturer, start by researching industry directories and attending trade shows. These platforms allow you to meet potential partners and assess their capabilities. Evaluate subcontract manufacturers based on their reputation, experience in your industry, and production capacity. Look for manufacturers who provide clear communication, demonstrate strong problem-solving skills, and have a proven history of meeting deadlines and quality standards.
What industries commonly use contract manufacturing?
Contract manufacturing is widely used in industries with complex, specialized production needs, including electronics, automotive, healthcare, and consumer goods. These sectors often require manufacturers with specialized knowledge and equipment, making contract manufacturing an efficient solution for meeting high standards of quality and production volume.
How can I ensure quality control in contract manufacturing?
To maintain quality control, implement regular inspections, audits, and third-party quality checks. Work closely with your contract manufacturer to establish quality standards and ensure they are met consistently. It’s also important to define specific metrics for monitoring product quality at every stage of production and address any issues quickly to avoid delays.
What are the main benefits of subcontract manufacturing?
Subcontract manufacturing offers several benefits, including significant cost savings, access to specialized expertise, and scalability. Small and medium-sized enterprises (SMEs) can particularly benefit from reduced overhead costs, as subcontracting allows them to leverage the experience and facilities of larger manufacturers without the need for substantial investment in infrastructure.
Can contract manufacturing help reduce operational costs?
Yes, contract manufacturing can help reduce operational costs by eliminating the need for in-house production facilities, inventory management, and a large workforce. It allows businesses to focus on their core competencies while outsourcing non-core activities to specialized manufacturers who can produce goods at a lower cost.
Are there risks to intellectual property in contract manufacturing?
Yes, there are risks to intellectual property (IP) when outsourcing production. Protect your IP by drafting clear contracts with confidentiality agreements and non-disclosure clauses. Ensure that your manufacturing partner has secure processes in place for handling proprietary information.
How do I negotiate a manufacturing contract?
When negotiating a manufacturing contract, focus on clear terms regarding quality standards, timelines, pricing, and penalties for non-compliance. Make sure the agreement outlines specific responsibilities, payment schedules, and dispute resolution procedures to protect both parties and ensure a smooth working relationship.
Is contract manufacturing only suitable for large businesses?
Contract manufacturing is not limited to large businesses. Small businesses can benefit from this process as well, particularly when looking to scale production without the need to invest heavily in infrastructure. Contract manufacturing allows SMEs to access advanced production capabilities while managing costs effectively.
How does contract manufacturing affect supply chain management?
Contract manufacturing can streamline supply chain management by outsourcing production processes to specialized partners. However, effective coordination is crucial to ensure timely delivery and maintain quality standards. A well-managed relationship with a contract manufacturer can simplify logistics, reduce inventory costs, and ensure smoother overall operations.