Unlocking sustained profitability in a manufacturing business takes time and effort. For that, you’ll have to continuously monitor costs and make sure that profit is consistent throughout the production line.
A recent survey by Deloitte revealed that 88% of manufacturers consider cost management a top priority. Hence, make an effort to know the costs associated with manufacturing goods. It can help understand how they contribute to expenses. In turn, you can make informed business decisions about profitability.
Once you accurately calculate the cost of goods manufactured (COGM), you can make informed decisions about pricing, budgeting, and overall financial planning.
This article explains COGM and why it matters in manufacturing. We’ll also review its formula, understand its components, and outline the key differences between COGM and the Cost of Goods Sold (COGS) for better clarity.
Let’s begin!
- What is Cost of Goods Manufactured (COGM)
- Formula to Calculate Cost of Goods Manufactured
- What is Included in COGM: Essential Cost Components
- How to Calculate Costs of Goods Manufactured: Step-by-Step
- Example of Costs of Goods Manufactured Calculation
- Calculate COGM Using Cloud ERP Software: Kladana
- Why Calculating COGM is Important for Production?
- Cost of Goods Sold vs Cost of Goods Manufactured
- Frequently Asked Questions of Cost of Goods Manufactured
What is Cost of Goods Manufactured (COGM)
Cost of Goods Manufactured (COGM) is a detailed calculation of everything it takes to produce goods. It gives a complete breakdown of the production costs by including raw materials, labor, and other expenses tied directly to manufacturing.
With COGM, you can clearly see the total investment required to turn raw inputs into finished products.
These are the key characteristics of COGM:
- Includes all direct and indirect production costs
- Focuses solely on goods completed during the period
- Help in analyzing production efficiency and cost control
- Excludes costs related to unsold or unfinished goods
- It serves as a basis for calculating the cost of goods sold (COGS)
- Useful in calculating the value of ending inventory
- Essential for determining profitability
- Help identify areas for cost optimization
Formula to Calculate Cost of Goods Manufactured
Calculating COGM requires gathering some essential information and plugging it into a simple formula.
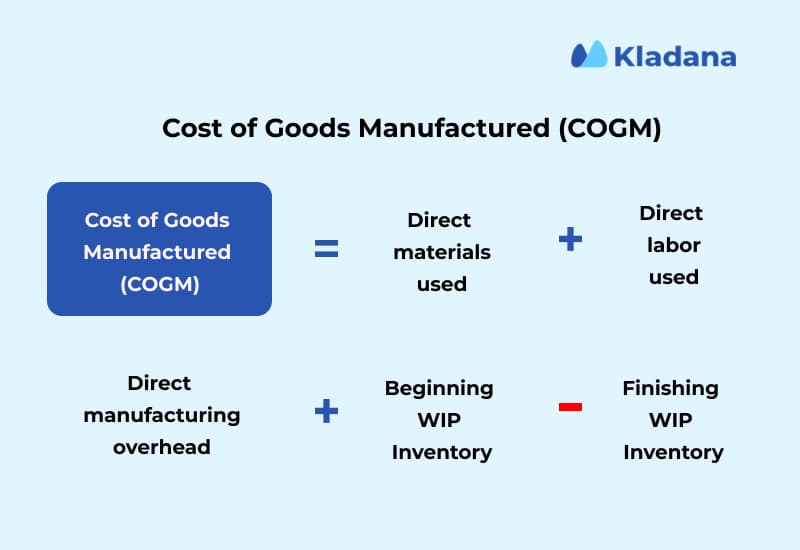
Here’s what each term means:
- Direct Materials Used = Costs of raw materials consumed during production.
- Direct Labor = Wages paid to workers directly involved in manufacturing.
- Manufacturing Overheads = Indirect costs like utilities, equipment depreciation, and factory maintenance.
- Work-in-Process Inventory = Partially completed goods at the start and end of the period.
What is Included in COGM: Essential Cost Components
Calculating COGM requires you to break down its essential components.
Each element gives clarity on how costs are accumulated from raw materials to finished goods.
Here, you’ll include everything from the obvious expenses, like raw materials, to the less obvious ones, like the cost of running the factory where your products are made.
These are the three primary cost components that make COGM.
Total Manufacturing Cost
This is where you add up all the expenses directly related to production in three main buckets:
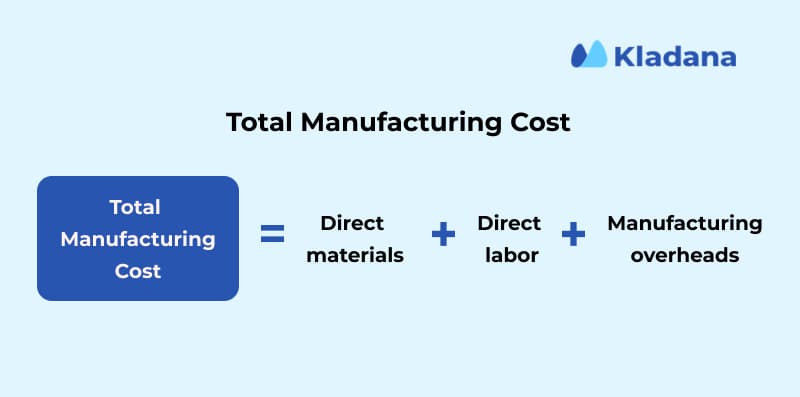
- Direct Materials: Represents the cost of raw materials consumed during production.
- Direct Labor: Covers the wages, salaries, and benefits of everyone actively involved in creating the product, including the people on the assembly line, the craftspeople in the workshop, and so on.
- Manufacturing Overhead: Involves Indirect expenses like factory utilities, equipment wear and tear, and maintenance as a part of the cost associated with running your production facility.
Work In Process Inventory (WIP)
WIP includes the value of everything that’s partially completed and still moving through your production process.
You need to factor in the value of WIP at both the beginning and end of the reporting period.
- Beginning WIP Inventory: Represents the value of any partially finished goods you had on hand at the start of the period.
- Ending WIP Inventory: Highlight the value of unfinished goods remaining at the end of the period.
Schedule of COGM
The COGM schedule gives a structured summary of everything tied together — total manufacturing costs with inventory change to arrive at the final price of goods completed.
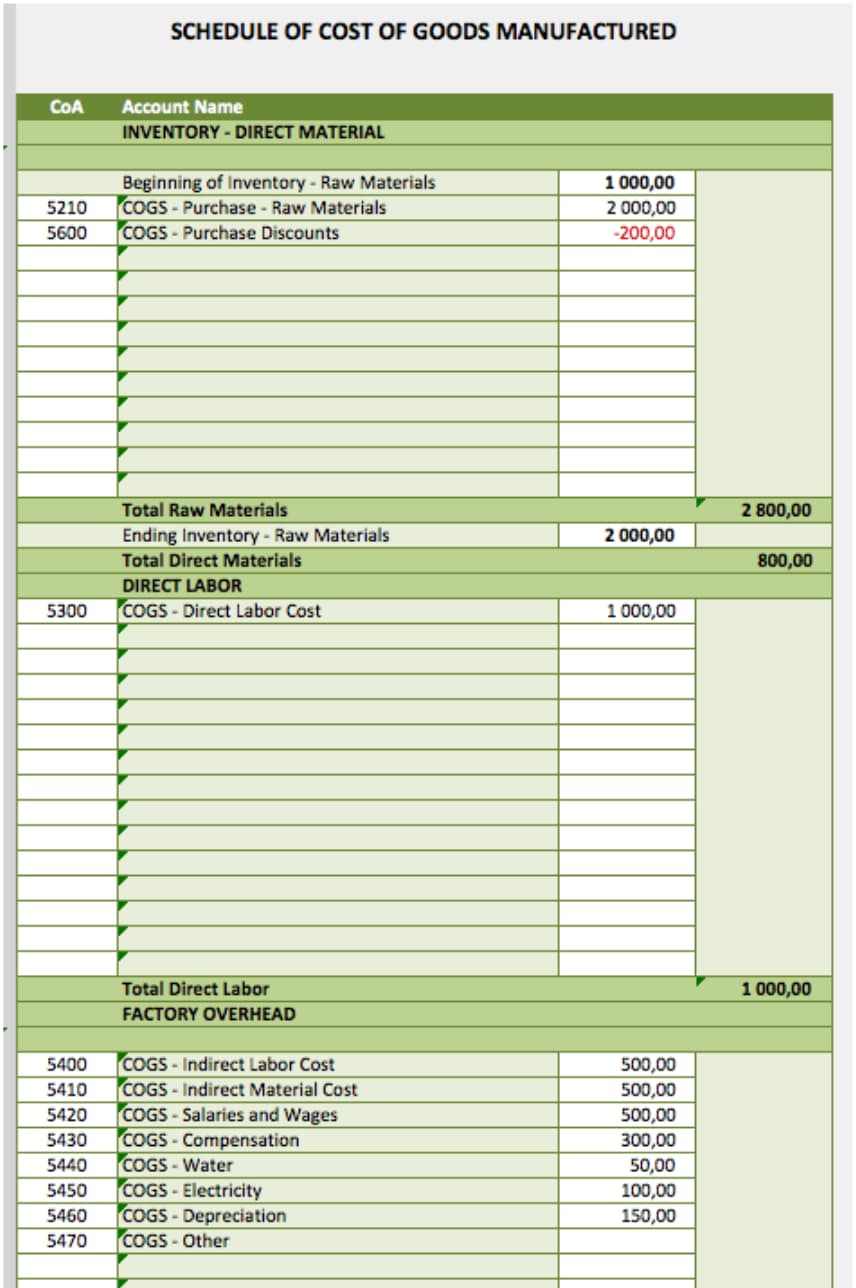
Key elements of the schedule include:
- Direct Costs: Total expenses for direct materials and direct labor.
- Manufacturing Overheads: Indirect costs like utilities and equipment maintenance.
- Inventory Adjustments: Beginning and ending balances of work-in-process inventory.
- Production Period Totals: The final calculation of goods completed during the period.
How to Calculate Costs of Goods Manufactured: Step-by-Step
When calculating the cost of goods manufactured (COGM), you’ll have to consider many factors that raise production costs.
At each step, a different production cost adds up, giving you a complete picture in the form of COGM. But it’s a step-by-step process, and you need practical actions to reach precise COGM confidently.
Let’s unfold these steps.
Step 1. Calculate your Direct Materials Cost
This step involves figuring out the cost of all the raw materials that go directly into your products.
Direct Materials Cost = Beginning Raw Materials Inventory + Raw Materials Purchases – Ending Raw Materials Inventory
Think of it as taking inventory of all the ingredients in your manufacturing recipe.
Here’s how to break it down:
- Start with your beginning raw materials inventory: This is the value of all the raw materials you had on hand at the beginning of the period.
- Add your raw materials purchases: This includes all the raw materials you acquired during the period.
- Subtract your ending raw materials inventory: This is the value of any unused raw materials you have left at the end of the period.
Step 2. Accurately Calculate Direct Labor Costs
This includes the wages, salaries, and benefits of those employees who work directly on the production line or in the workshop.
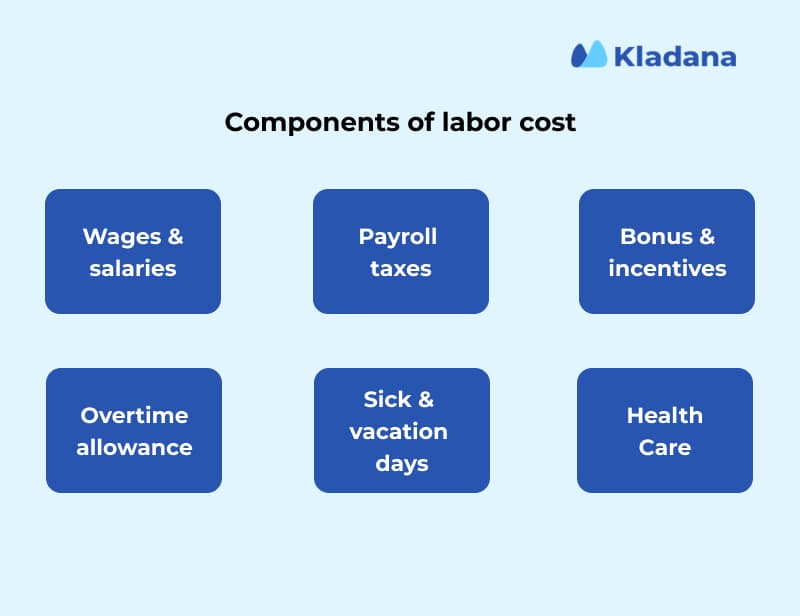
Accurately tracking these costs ensures your calculations reflect the actual cost of labor.
Here’s how you can calculate direct labor:
- Track Hours Worked: Record the actual hours employees spend on production tasks.
- Multiply by Hourly Rates: Apply the wages or salaries for each worker, factoring in any overtime pay.
- Include Additional Costs: Add employee benefits, payroll taxes, and bonuses specific to the production workforce.
- Gather payroll data: Collect information on wages, salaries, overtime pay, and any benefits directly tied to these employees.
- Allocate labor costs: If employees work on multiple products, you’ll need to allocate their time and associated costs accordingly.
Step 3. Consider the Manufacturing Overheads
Manufacturing overheads represent indirect costs that are necessary to support production, but they can be tricky to track.
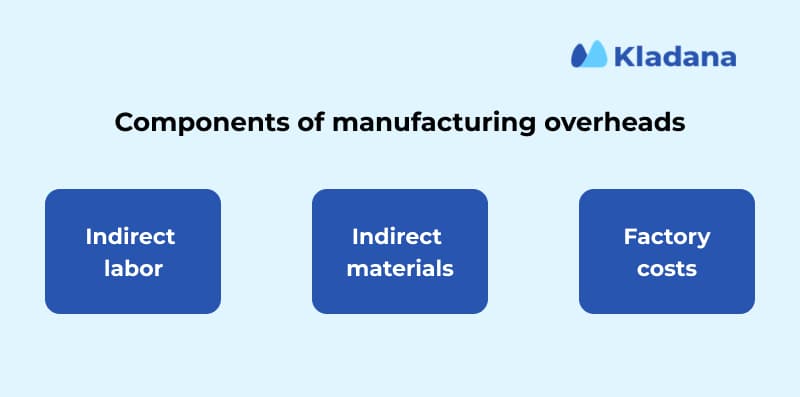
A few standard manufacturing overheads are:
- The cost of renting your production facility.
- Utility expenses related to electricity, gas, and water used in the factory.
- Depreciation — a value that decreases in the value of your factory equipment and machinery over time.
- Factory supplies like cleaning supplies, lubricants, and small tools that you’d use in your factory.
To allocate overheads, you can:
- List All Overheads: Identify all indirect costs linked to production, such as rent, power, and factory supplies.
- Use Allocation Bases: Assign costs using a logical base like labor hours, machine hours, or production volume. For example, if electricity powers specific machines, allocate those costs accordingly.
- Review and Adjust Regularly: Overhead costs can fluctuate, so ensure periodic reviews to keep allocations accurate.
Step 4. Prepare the Schedule of Cost of Goods Manufactured
The schedule of cost of goods manufactured is a valuable document that includes all the production-related costs in one place. It gives you a complete picture of what went into manufacturing during a specific period.
Tips for Creating an Accurate Schedule
The tips below should help you prepare an accurate and actionable schedule. It’s not just about calculating COGM; it’s about preparing a concise, clear document that provides valuable insights to drive your manufacturing business forward.
Organize Your Data
- Gather all cost-related data before you start, ensuring accuracy from the outset.
- Inventory management tools are used to streamline production tracking for raw materials and WIP.
Standardize the Process
- Follow a consistent format to prepare the schedule for every reporting period.
- Include clear line items for each component (e.g., direct materials, labor).
Validate Your Numbers
- Cross-check totals at each step of the calculation to avoid errors.
- Compare your final schedule with past reports to spot discrepancies or trends.
Leverage Automation
- Use accounting or ERP software to generate the schedule, reducing manual errors.
- Automate recurring cost calculations, such as overhead allocation, for efficiency.
Analyze the Results
- Review the schedule regularly to identify areas where costs can be optimized.
- Share insights with your team to address inefficiencies in production.
Example of Costs of Goods Manufactured Calculation
We’ve already explored the formula and critical components of COGM, but let’s consider the practical example as well.
This will provide you with much-needed clarity that helps internalize the calculation process. Let’s consider a simplified scenario of a manufacturing company.
In this example, we’ll break down each component of the COGM calculation to give a clear, step-by-step understanding of how to arrive at the total manufacturing cost in USD ($).
Direct Materials Used Calculation
Company A starts the year with $500,000 worth of raw materials in inventory. During the year, the company purchases an additional $2,500,000 in raw materials. At the end of the year, the remaining inventory totals $600,000.
Calculation:
- Beginning Inventory: $500,000
- Purchases during the year: $2,500,000
- Ending Inventory: $600,000
Formula Application:
Direct Materials Used = $500,000 + $2,500,000 – $600,000 = $2,400,000
This figure represents the total cost of raw materials that were actually converted into products during the year.
Direct Labor Costs Calculation
Company A employs 30 factory workers whose total salaries for the year amount to $1,800,000.
Calculation:
- Total Direct Labor Costs: $1,800,000
This amount highlights the wages that Company A paid to employees directly involved in the production process.
Manufacturing Overheads Calculation
Company A’s manufacturing overheads include
- Equipment depreciation ($200,000)
- Factory rent ($400,000)
- Utilities ($300,000)
- Maintenance ($100,000)
Formula Application
Total Overheads = $200,000 + $400,000 + $300,000 + $100,000 = $1,000,000
These are the indirect costs necessary to support the manufacturing process but are not directly tied to the production of specific goods.
Work-in-Process Inventory Adjustment
At the start of the year, the work-in-process inventory was $150,000, and it increased to $250,000 by year-end.
Calculation:
- Beginning WIP Inventory: $150,000
- Ending WIP Inventory: $250,000
Formula Application:
WIP Inventory Adjustment = $250,000 – $150,000 = $100,000
This adjustment accounts for the change in the value of goods that are still in the production process and still need to be completed.
Total COGM Calculation
Below is the final COGM calculation based on all the above-calculated figures.
Total COGM = Direct Materials Used + Direct Labor + Manufacturing Overheads + WIP Inventory Adjustment
This means,
Total COGM = $2,400,000 + $1,800,000 + $1,000,000 + $100,000 = $5,300,000
This final figure represents the total cost of goods that were completed during the year and ready for sale.
Calculate COGM Using Cloud ERP Software: Kladana
Manually tracking production costs can be overwhelming, mainly when your business depends on accurate numbers for planning and growth.
That’s where Kladana, a cloud-based ERP software for manufacturing, steps in to automate the calculation of the cost of goods manufactured (COGM). Kladana also makes it easier to keep your production costs accurate, organized, and ready when you need them.
Check our video tutorial on how you can calculate COGM with Kladana
1. Unifying All Production Costs in One System
Instead of working with disconnected tools, Kladana centralizes all your manufacturing data, from materials and labor to overheads and inventory. This ensures every cost is accounted for in one place.
How Kladana Helps:
- Provides a live view of material costs and usage across production stages.
- Tracks labor costs automatically, linking wages to tasks performed.
- Keeps an accurate log of overhead expenses, such as utility bills and equipment wear and tear.
By using a single platform, you reduce the risk of missed or duplicated costs.
2. Automating Work-in-Process Adjustments
Work-in-process (WIP) inventory calculations can often cause errors, but Kladana eliminates this issue by automating the tracking and adjustment process.
What Kladana Does:
- Monitors WIP levels as items move through production stages.
- Automatically calculates starting and ending WIP inventories.
- Ensures only completed goods are included in the COGM.
This automation ensures your calculations are consistent and free from human errors.
3. Generating COGM Reports in Minutes
Kladana lets you create a professional schedule of the cost of goods manufactured without the hassle of manual data entry. All your production cost details are compiled into clear, structured reports.
Features You Can Rely On:
- Generates accurate schedules tailored to your reporting needs.
- Offers options for internal analysis or external audits.
- Highlights trends in production costs, helping you make better decisions.
You’ll save time while ensuring your reports are always audit-ready.
4. Turning Data into Valuable Insights
Kladana doesn’t stop at calculating your COGM — it provides actionable insights from the data it gathers.
These insights can help you refine operations, plan budgets, and even negotiate better supplier deals.
How You Benefit:
- Spot inefficiencies in your production process by analyzing cost patterns.
- Use real-time data to optimize raw material usage.
- Forecast future expenses with greater accuracy based on historical trends.
Why Calculating COGM is Important for Production?
The cost of Goods Manufactured (COGM) helps you understand exactly how much it costs to make your products. It breaks down all your expenses — materials, labor, and other production costs — so you know where your money is going.
With this information, it’s easier to make intelligent decisions about your business. You can better plan budgets, find areas to save money, and improve the way things run in your factory.
These are the five reasons why calculating COGM is vital for your production process:
- Gain Full Visibility of Costs: COGM lays out every detail of your production costs, ensuring nothing goes unnoticed.
- Create Pricing That Works: By understanding your expenses, you can price your products to balance competitiveness and profit.
- Streamline Your Production Process: Reviewing COGM highlights areas where processes can be refined and costs reduced.
- Build Better Financial Plans: Accurate COGM figures give you the foundation to plan budgets and forecast expenses with confidence.
- Enhance Financial Reporting: A precise COGM calculation ensures your financial reports are reliable and transparent, supporting better decision-making.
Cost of Goods Sold vs Cost of Goods Manufactured
Understanding the difference between the Cost of Goods Sold (COGS) and the Cost of Goods Manufactured (COGM) is critical to managing your production and overall financial planning.
While both focus on production-related costs, they serve different purposes and include distinct components.
The table below highlights the primary differences:
Aspect | Cost of Goods Manufactured (COGM) | Cost of Goods Sold (COGS |
Definition |
Total cost of producing goods during a specific period. |
Cost of goods that were sold during a specific period. |
Purpose |
Tracks costs involved in manufacturing finished goods. |
Measures the cost of products sold to calculate gross profit. |
Includes |
Direct materials, direct labor, manufacturing overhead, and WIP adjustments. |
COGM, plus adjustments for finished goods inventory. |
Focus |
Production costs for goods completed. |
Selling costs for goods delivered to customers. |
Inventory Adjustment |
Adjusts for beginning and ending WIP inventory. |
Adjusts for beginning and ending finished goods inventory. |
Stage in Process |
Tracks cost up to the completion of manufacturing. |
Accounts for costs from manufacturing to the point of sale. |
Frequently Asked Questions of Cost of Goods Manufactured
What is the Cost of Goods Manufactured (COGM)?
COGM is the total cost of producing goods during a specific period, including direct materials, direct labor, and manufacturing overheads.
How is COGM different from COGS?
COGM calculates the cost of completed goods, while COGS includes costs for goods sold and adjusts for finished goods inventory.
What are the main components of COGM?
Direct materials, direct labor, manufacturing overhead, and adjustments for work-in-process (WIP) inventory.
Why is calculating COGM important?
It helps manufacturers track production costs, set pricing strategies, and identify inefficiencies in their operations.
What is the formula for COGM?
COGM = Direct Materials Used + Direct Labor + Manufacturing Overhead + Beginning WIP – Ending WIP.
Can COGM help with budgeting?
Yes, COGM provides detailed cost insights, making it easier to create accurate budgets and forecasts.
How does cloud ERP software like Kladana help calculate COGM?
Kladana automates data tracking and calculations, reducing errors and saving time.
What is the difference between the direct and indirect costs of COGM?
Direct costs (materials and labor) are tied to specific products, while indirect costs (overheads) support overall production.
Does COGM include all inventory costs?
No, it only includes costs for goods completed. Unfinished goods remain in WIP inventory, and finished goods are accounted for in COGS.
How can I reduce my COGM?
Review production processes, reduce waste, negotiate better rates with suppliers, and leverage automation tools like ERP software.