Today SMEs are under constant pressure to do more with less. Lean manufacturing offers a solution by focusing on waste reduction and efficiency improvements, enabling companies to streamline their production processes and remain agile. But for many businesses, lean principles may seem complex or suited only for large-scale enterprises. The truth is, lean manufacturing tools are highly adaptable, offering practical benefits to businesses of any size.
This article will explore the most effective lean manufacturing tools for SMBs, showcasing how these methods can transform your operations, boost productivity, and deliver long-term value. Whether you’re just starting or looking to scale, integrating these lean techniques can provide a sustainable path to higher efficiency.
- Why Lean Manufacturing Tools Matter for SMBs
- Essential Lean Manufacturing Tools for Small and Medium-Sized Businesses
- Advanced Lean Tools for Scaling SMBs
- Choosing the Right Lean Manufacturing Tools for Your Business
- Common Challenges in Implementing Lean Tools and How to Overcome Them
- Frequently Asked Questions on Lean Manufacturing
Why Lean Manufacturing Tools Matter for SMBs
Lean manufacturing tools are crucial for small and medium-sized businesses (SMBs) that want to stay competitive in a fast-paced market. By focusing on the elimination of waste and continuous improvement, these tools enable companies to refine their production processes and improve operational efficiency.
For SMBs, lean tools aren’t just about reducing costs — they also play a significant role in improving product quality, meeting customer demands more effectively, and fostering a culture of innovation. Adopting lean manufacturing techniques can help businesses become more agile, allowing them to respond quickly to market changes without sacrificing profitability. In industries where resources are often constrained, lean tools provide a structured approach to maximizing output without unnecessary complexity.
Benefits of Lean Manufacturing Tools
Implementing lean manufacturing tools offers a wide range of benefits that extend beyond simple cost-cutting. These tools enable SMBs to optimize their operations and create a more efficient production environment. Key benefits include:
Waste reduction: Lean tools focus on eliminating unnecessary steps and materials, reducing costs while improving output quality.
Improved productivity: Streamlined processes allow businesses to operate more efficiently, increasing throughput without requiring additional resources.
Enhanced customer satisfaction: Faster production times and consistent product quality lead to higher customer retention and better market positioning.
Operational flexibility: Lean practices promote adaptability, helping SMBs respond quickly to changes in demand or market conditions.
Sustainable growth: By standardizing operations and reducing inefficiencies, businesses create a scalable model that supports long-term expansion.
Better resource allocation: Lean tools help businesses use their workforce, equipment, and materials more effectively, ensuring resources are not wasted.
Manufacturing Management in Kladana
Take full control of your production process—from planning orders and managing inventory to monitoring supply and employee performance. Easily track unit production costs and sell goods directly to customers.
Streamline your entire manufacturing workflow with a single browser-based app, removing the hassle of juggling Excel sheets and paper documents.
Essential Lean Manufacturing Tools for Small and Medium-Sized Businesses
For small and medium-sized businesses, lean manufacturing tools provide practical ways to improve efficiency, reduce waste, and create a more streamlined production process. Each tool targets specific areas of improvement, from organizing workspaces to managing workflows and reducing defects. Below are some of the most impactful lean tools that SMBs can implement to enhance their operations.
5S Methodology
The 5S methodology is a foundational lean tool that helps businesses create organized, efficient, and safe work environments. It consists of five phases: Sort, Set in Order, Shine, Standardize, and Sustain. By following these steps, businesses can declutter workspaces, organize tools and materials for easy access, and ensure that cleanliness and order are maintained over time. For SMBs, the 5S methodology is a cost-effective way to improve workplace efficiency and boost employee morale by creating a more structured and productive environment.
Value Stream Mapping (VSM)
Value Stream Mapping (VSM) is a visual tool that helps businesses map out every step in their production process. By visually representing the flow of materials and information, VSM makes it easier to identify bottlenecks, redundancies, and waste. For SMBs, VSM is particularly valuable because it provides a clear roadmap for process improvement, enabling businesses to make data-driven decisions that enhance productivity and reduce lead times.
Kaizen (Continuous Improvement)
Kaizen, which translates to «continuous improvement,» is a core lean philosophy that encourages incremental improvements in processes, products, and workflows. Instead of making drastic changes, Kaizen emphasizes small, ongoing adjustments that lead to significant long-term benefits. For SMBs, the Kaizen approach fosters a culture of innovation and collaboration, where every employee is empowered to suggest improvements. This steady evolution not only enhances operational efficiency but also engages teams in the pursuit of excellence.
Kanban
Kanban is a visual workflow management tool that helps teams track and manage tasks in real-time. By using visual boards with columns representing different stages of work, businesses can easily monitor progress and identify where tasks are piling up. For SMBs, Kanban offers a simple, flexible system to optimize workflows, reduce bottlenecks, and ensure that resources are allocated efficiently.
Just-In-Time (JIT) Production
Just-In-Time (JIT) production focuses on producing only what is needed, when it is needed. This lean manufacturing tool helps SMBs minimize excess inventory, reduce storage costs, and respond quickly to customer demand. By aligning production schedules closely with demand, JIT enables businesses to operate more efficiently, reducing waste and maximizing profitability.
Poka-Yoke (Mistake-Proofing)
Poka-Yoke is a lean tool designed to prevent mistakes in production by eliminating the potential for human error. Through simple devices or mechanisms, Poka-Yoke ensures that defects are caught early in the process, reducing the need for costly rework or scrap. For SMBs, implementing Poka-Yoke can significantly improve product quality while minimizing wasted time and resources.
Total Productive Maintenance (TPM)
Total Productive Maintenance (TPM) is a proactive approach to maintaining equipment and machinery. Instead of waiting for equipment to break down, TPM emphasizes regular maintenance to prevent unplanned downtime. For SMBs, TPM ensures that machinery runs smoothly, reducing interruptions in production and extending the lifespan of valuable equipment.
Six Sigma
Six Sigma is a data-driven methodology focused on reducing variability and defects in production processes. By analyzing and controlling variations, businesses can achieve higher levels of quality and consistency. For SMBs, adopting Six Sigma practices leads to more predictable outcomes, which helps in maintaining customer satisfaction and reducing operational costs.
Gemba Walk
The Gemba Walk is a management practice where leaders observe the actual work being done on the production floor. By walking through the workplace, managers can identify inefficiencies, engage with employees, and gain a deeper understanding of the production process. For SMBs, Gemba Walks provide valuable insights that can inform strategic decisions and drive continuous improvement efforts.
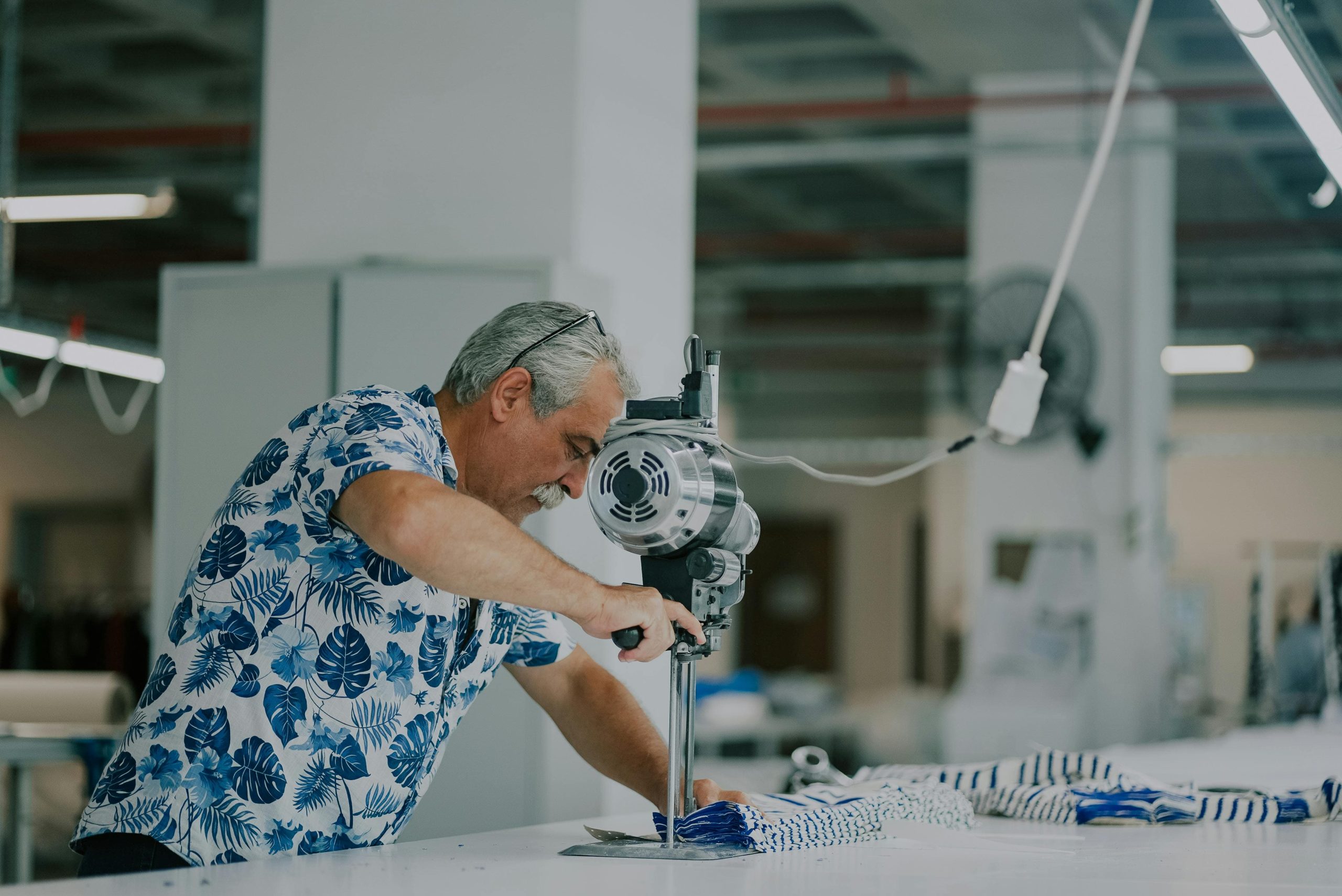
Advanced Lean Tools for Scaling SMBs
As small and medium-sized businesses grow, the complexity of their operations increases. Advanced lean manufacturing tools provide the strategic framework necessary to scale efficiently while maintaining lean principles. By adopting these tools, businesses can further optimize their processes, align their long-term goals, and ensure consistent production flow.
Heijunka (Leveling Production)
Heijunka is a production leveling technique designed to smooth out fluctuations in demand and avoid bottlenecks. By distributing work more evenly over time, Heijunka helps businesses maintain a steady production flow, even when orders vary in size and frequency.
For SMBs, implementing Heijunka can prevent the stop-and-start nature of production that often leads to inefficiencies and excessive inventory. This tool ensures that resources, including labor and materials, are utilized more consistently, which leads to a more predictable and balanced operation as the business scales.
Hoshin Kanri (Strategic Planning)
Hoshin Kanri is a strategic planning method that ensures alignment between a company’s long-term vision and its day-to-day operations. It creates a framework where high-level goals are translated into actionable tasks, with clear accountability and performance metrics.
For SMBs looking to scale, Hoshin Kanri is invaluable because it ensures that every department is working toward common objectives. By focusing on key priorities and regularly reviewing progress, businesses can stay agile and responsive while ensuring that their strategic goals are achieved.
Andon System
The Andon system is a visual tool used to alert workers to issues on the production line in real-time. When a problem arises — whether it’s a defect, equipment failure, or resource shortage — the Andon system signals an immediate response.
For scaling SMBs, the Andon system is crucial because it empowers employees to identify and address problems before they escalate, reducing downtime and maintaining the flow of production. This not only improves efficiency but also enhances the quality of output by catching potential defects early in the process. As businesses grow, the Andon system fosters a culture of accountability and rapid problem-solving.
Read‑alikes
Business Process Automation: Guide with 10 Benefits
Managing Production in a Small Manufacturing Company: Planning, Control, and Profit Calculation
Barcoding for Manufacturing: Importance, 8 Paramount Benefits, and Step‑by‑Step Implementation Guide
Choosing the Right Lean Manufacturing Tools for Your Business
Selecting the right lean manufacturing tools is crucial for small and medium-sized businesses aiming to streamline their operations and enhance efficiency. Not all lean tools will suit every business, as factors like company size, production complexity, and unique operational needs play a significant role in determining which tools will have the greatest impact. Understanding your business’s specific goals and challenges can help guide the selection process.
Factors to Consider When Selecting Tools
When evaluating lean tools, SMBs should consider the following key factors to ensure they make informed decisions:
Company Size: Smaller operations might prioritize simplicity and flexibility, while larger ones may benefit from more structured tools like Six Sigma or Heijunka.
Production Type: Whether your business deals with discrete or process manufacturing will influence the choice of tools. For example, Just-In-Time is particularly suited for businesses handling high-value, low-volume goods.
Operational Goals: Lean tools should align with your objectives. If reducing waste is a priority, Value Stream Mapping and 5S might be most effective. For businesses focused on continuous improvement, Kaizen or Gemba Walks could be key.
Resource Availability: Some lean tools require more time, training, and technology to implement. SMBs must assess their capacity for adopting new methodologies.
Customizing Lean Tools for SMBs
One of the strengths of lean manufacturing is its adaptability. SMBs can modify and scale lean tools to fit their workflows without compromising effectiveness. Here’s how customization can enhance results:
Adapting 5S: For SMBs, implementing the 5S methodology can be more gradual and involve fewer steps compared to larger companies. Starting with simple workspace organization may already lead to noticeable improvements.
Simplifying Kanban: While traditional Kanban systems are highly structured, SMBs can use digital boards or basic visual cues to track workflow and optimize production. This approach keeps the system lean and manageable.
Phased Introduction of Lean Tools: SMBs don’t need to adopt all tools simultaneously. A phased approach allows businesses to focus on one or two tools initially, building momentum and expertise before expanding.
By carefully considering these factors and customizing lean tools to meet their specific needs, SMBs can effectively implement lean manufacturing and drive operational success.
Common Challenges in Implementing Lean Tools and How to Overcome Them
Implementing lean manufacturing tools can transform a small or medium-sized business, but challenges often arise during adoption. Understanding and addressing these hurdles is key to ensuring a smooth transition and long-term success.
Employee Resistance
One of the most common challenges is resistance to change. Employees may feel uncertain or uncomfortable with new methods that disrupt established routines.
Solution: Engage employees early in the process by explaining the benefits of lean tools and involving them in decision-making. Regular training and open communication foster buy-in, making the transition smoother.
Lack of Resources
SMBs often face resource constraints, whether in terms of time, budget, or manpower, which can make the implementation of lean tools seem overwhelming.
Solution: Start small by implementing lean tools that require minimal investment, such as 5S or Value Stream Mapping. Prioritize tools that offer quick wins and visible results, which can build momentum for future investments.
Maintaining Momentum
Sustaining lean practices over time can be difficult, especially as initial enthusiasm wanes or when other business pressures arise.
Solution: Schedule regular reviews and Gemba Walks to assess progress. Set clear, achievable goals, and celebrate small wins to keep teams motivated. Continuous improvement must become part of the company culture to avoid stagnation.
Frequently Asked Questions on Lean Manufacturing
Lean manufacturing tools can drive significant improvements for small and medium-sized businesses, but they come with questions. Below are answers to some common inquiries from business owners and managers about applying lean tools in their operations.
What are the key lean manufacturing tools for small businesses?
Lean tools like 5S, Kanban, and Just-in-Time are ideal for SMBs. These tools are straightforward, cost-effective, and have a tangible impact on productivity and waste reduction.
How do lean tools help reduce waste in production?
Lean tools streamline processes by eliminating inefficiencies. By producing only what is necessary and optimizing workflows, businesses can significantly cut down on waste, whether in time, materials, or effort.
Is lean manufacturing only for large enterprises?
No, lean manufacturing is scalable and can be tailored to fit businesses of all sizes. SMBs can start with simpler tools like 5S or Kanban and gradually adopt more complex practices as they grow.
What is the difference between 5S and Kaizen?
5S focuses on organizing the workspace to increase efficiency, while Kaizen emphasizes continuous, small improvements across all areas of the business.
How difficult is it to implement lean tools in an SMB?
With proper planning and active employee participation, lean tools can be easily integrated into SMB operations. Starting small and gradually expanding the use of lean tools helps ensure smoother adoption.
What is the most important lean tool for a manufacturing startup?
Startups often find the 5S methodology and Kanban systems most valuable as they help establish efficient, organized workflows from the outset.
How can lean tools improve customer satisfaction?
By reducing production errors and optimizing processes, lean tools enable businesses to deliver higher-quality products more quickly, leading to improved customer satisfaction.
Can lean tools help with inventory management?
Yes, lean tools like Kanban and JIT are specifically designed to optimize inventory management by aligning production with demand and minimizing excess stock.
How much training is required to implement lean tools?
The amount of training depends on the tool. Some, like 5S, require minimal training, while others, such as Six Sigma, may need more in-depth learning and application.
How do I measure the success of lean manufacturing tools?
Success can be tracked using metrics like reduced waste, higher productivity, improved process flow, and enhanced customer satisfaction.