The future is here! The Wall Street Journal’s article can blow any mind. Humanoid robots are getting their first real jobs. Recent advancements have led to the integration of humanoid robots in manufacturing settings, performing typically “human” tasks.
In fact, here we have something to think about: according to the Engineering Institute of Technology, the global industrial automation market is projected to grow by 9.3% annually, reaching $307.7 billion by 2030. In the meantime, McKinsey Global Institute states that around 60% of occupations have at least one-third of their tasks that could be automated.
But we can’t give up and wait for robots to replace us all. Let’s look at the main trends in automation in production. The best way to survive the “revolution” is to take part in it.
- The Role of Automation in Modern Manufacturing
- Types of Automation in Manufacturing
- Key Technologies in Automated Manufacturing
- Implementing Automation in Small and Medium-Sized Businesses (SMBs)
- Future Trends in Manufacturing Automation
- Frequently Asked Questions on Automation in Manufacturing
- List of Resources
The Role of Automation in Modern Manufacturing
Automation plays a vital role in modern manufacturing, enabling businesses to increase efficiency, productivity, and accuracy in their production processes. By leveraging automation technologies, manufacturers can streamline their operations, reduce costs, and improve product quality. Automated systems help in minimizing human errors, speeding up production, and maintaining consistent quality, which is crucial for staying competitive in today’s fast-paced market.
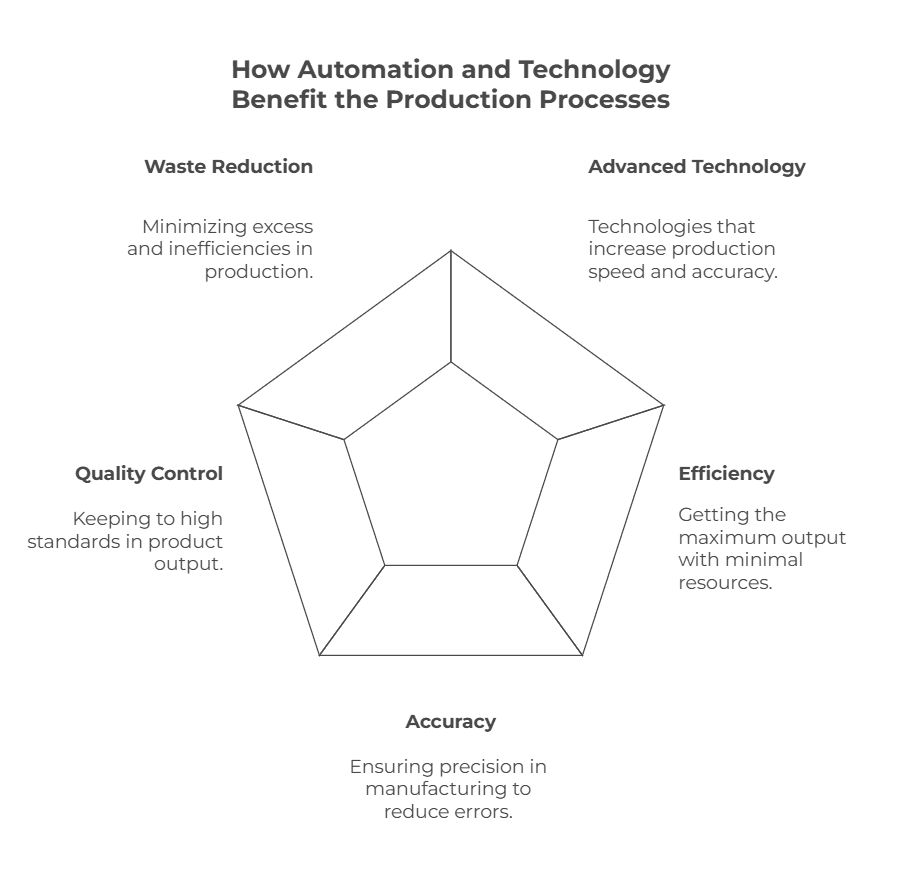
What Is Automation in Manufacturing?
Automation in manufacturing refers to the use of technology and machinery to perform specific tasks without human intervention. This can include equipment, software programs, production floor robots, or overall systems used to create smoother, more data-driven strategies for the production line. The overarching goal of automation is to drive efficiency, reduce costs, and increase production capacity. By automating repetitive or tedious tasks, manufacturers can focus human labor on more complex and value-added activities, thereby enhancing overall productivity.
Evolution of Manufacturing Automation
Manufacturing automation has evolved significantly over the years, from the early use of mechanized systems to the current adoption of advanced technologies like artificial intelligence, robotics, and the Internet of Things (IoT). Initially, automation began with simple mechanized tools during the Industrial Revolution, which replaced manual labor with machines. As technology advanced, programmable automation emerged, allowing for more flexibility and customization in production processes. Today, modern factories utilize smart systems that integrate AI, IoT, and data analytics to not only automate tasks but also to monitor and optimize the entire production process in real-time. This evolution has made manufacturing more efficient, adaptable, and capable of meeting the demands of a dynamic market.
Kladana’s ERP solution helps you automate your business operations. Make your processes more streamlined and efficient.
Types of Automation in Manufacturing
There are several types of automation used in manufacturing, each with its own advantages and disadvantages. The main types of automation include fixed automation, programmable automation, and flexible automation.
Fixed Automation or Hard Automation
Fixed automation, also known as hard automation, is a type of automation system that is designed to perform a specific task or set of tasks without the ability to adapt to changes in the production process. This type of automation is often used in high-volume production of a single product, where the equipment is custom-designed for a specific manufacturing process. Fixed automation is typically used for tasks that require high precision and speed, such as assembly lines, transfer lines, and dedicated production equipment.
Fixed automation is most effective for high-volume production of products that have a long lifecycle and a stable demand. However, it can be difficult to switch production styles once a machine is set, making it less flexible than other types of automation. Examples of fixed automation include high-speed packaging machines, automated bottling lines, and continuous casting machines.
Key Technologies in Automated Manufacturing
Automation is changing the way products are made, making manufacturing faster, more precise, and less reliant on human labor. Advanced robotics and industrial robots play a significant role in enhancing efficiency and flexibility across production processes. Technologies like robotics, artificial intelligence, and smart machines help businesses produce goods with fewer errors and at lower costs. For small and medium-sized manufacturers, using these technologies is key to staying competitive in a fast-changing industry.
Robotics and Automated Machinery
Robots and automated machines handle repetitive tasks with high accuracy, reducing human errors and increasing production speed. These systems perform tasks that are dangerous, hazardous, or repetitive with greater efficiency than human workers. These systems include:
- Robotic arms — Used in assembly lines to place, move, or weld parts.
- Conveyor systems — Transport materials efficiently, reducing manual labor.
- Automated material handling — Moves products between different stages of production.
The assembly line method, popularized by Henry Ford, set the foundation for modern automated manufacturing processes.
✅ Benefits for manufacturers:
✔ Faster production
✔ Improved precision
✔ Lower labor costs
Artificial Intelligence (AI) and Machine Learning
AI helps factories operate smarter by analyzing data and making real-time improvements. Machine learning systems detect patterns and optimize processes without human input.
- Predictive maintenance — AI identifies equipment issues before they cause breakdowns, reducing downtime.
- Process optimization — AI suggests better workflows to reduce waste and improve efficiency.
These technologies contribute to increased productivity by optimizing workflows and reducing downtime.
✅ Why it matters:
✔ Less machine downtime
✔ More efficient production
✔ Lower operational costs
Internet of Things (IoT) in Manufacturing
IoT connects machines and devices, allowing manufacturers to track and control production remotely. Sensors collect valuable data and real-time data on:
📊 Production metrics — Tracks how efficiently machines are working.
⚙ Equipment health — Detects potential failures early.
🌡 Environmental conditions — Monitors temperature, humidity, and other factors.
Advanced sensors play a crucial role in connecting smart devices and improving safety and functionality in collaborative robots.
✅ Impact on businesses:
✔ Improved decision-making
✔ Reduced errors and delays
✔ Cost savings through better resource management
Computer Numerical Control (CNC) Systems
CNC machines use programmed instructions to cut, drill, and shape materials with extreme accuracy. The introduction of machine tools during the Industrial Revolution marked a pivotal shift in manufacturing practices. These machines are widely used for making metal and plastic parts.
🔧 Key features:
- Precision cutting — Ensures uniformity in every piece.
- Automated operation — Reduces the need for manual work.
- Custom production — Allows small batches without high costs.
✅ Why it’s useful for manufacturers:
✔ Consistent quality
✔ Faster production cycles
✔ Lower material waste We implemented Kladana at the factory, and things started to work.
Gain full control over your production process — from planning and stock management to raw material transfers, packaging, and final sales.
✅ Convert sales orders into production orders to ensure timely manufacturing
✅ Accurately calculate finished goods costs
✅ Set the right sale price
✅ Track raw material usage
✅ Monitor each production stage
✅ Ensure sufficient raw materials for every order
Implementing Automation in Small and Medium-Sized Businesses (SMBs)
For SMBs, adopting automation can seem daunting due to perceived financial and operational risks. While the high initial investment may seem daunting, the long-term benefits can justify the expense. However, with a strategic approach, these businesses can integrate automation in ways that enhance efficiency without disrupting daily operations or overwhelming budgets or human employees.
Assessing Automation Needs
Before implementing automation, SMBs must first identify where it will deliver the greatest value.
- Evaluate current workflows: Map out key processes to pinpoint bottlenecks and repetitive tasks. Monitoring overall equipment effectiveness (OEE) can help identify areas for improvement.
- Focus on high-impact areas: Prioritize areas that directly affect production speed, quality, or resource allocation and equipment effectiveness.
- Set clear goals: Determine whether your primary objectives are cost reduction, improved output, or enhanced accuracy.
Choosing the Right Automation Technologies
Selecting the most suitable automation solutions is critical to success.
- Align with business scale: Choose technologies and automation software that can scale with your business as it grows, without requiring complete overhauls.
- Consider budget: Automation doesn’t have to be prohibitively expensive — start with smaller, incremental automation tools before investing in larger systems.
- Compatibility: Ensure that new automation systems can integrate seamlessly with your existing technologies.
Software systems like MRP and ERP are essential for managing and controlling inventory, tracking parts throughout the supply chain, and integrating various processes.
Challenges in Adopting Automation
While automation offers numerous benefits, SMBs may encounter some challenges during the transition.
- Cost concerns: Initial setup costs can be high, especially for businesses with limited budgets.
- Employee resistance: Workers may fear job displacement or feel uneasy about adapting to new systems.
- System integration: Legacy systems may not be easily compatible with newer automation technologies.
- Despite the reduction in human supervision, a skilled human workforce is still essential for managing and maintaining automated systems.
Solutions for Overcoming Automation Challenges
SMBs can navigate these hurdles by adopting a phased approach and providing necessary support.
- Gradual implementation: Start small, automating a single process before expanding. Automation enables continuous improvement by optimizing production processes and reducing waste.
- Employee training: Offer comprehensive training to help employees adapt and find new roles within the automated environment, leading to increased efficiency.
- Flexible, scalable solutions: Opt for automation systems that allow easy upgrades as your business evolves.
Future Trends in Manufacturing Automation
The future of manufacturing is poised for significant transformation as automation technologies continue to evolve. Smart manufacturing integrates advanced automation technologies, data analytics, and digital tools to enhance efficiency and real-time insights. For businesses, understanding and adopting these trends is crucial for staying competitive in the manufacturing industry and driving innovation.
Smart Factories and Industry 4.0
Smart factories represent a shift toward fully interconnected and data-driven manufacturing environments.
- Autonomous systems: Machines, sensors, and devices in smart factories communicate in real-time to optimize production without human intervention. The industrial internet plays a crucial role in connecting machines and devices, enabling data sharing and real-time optimization.
- Data-driven insights: Industry 4.0 technologies harness vast amounts of data to predict and prevent production issues, improve maintenance schedules, and enhance decision-making.
- Integration: Seamless integration of IoT, AI, and robotics enables data sharing, higher productivity, quality, and flexibility in manufacturing processes.
3D Printing and Additive Manufacturing
3D printing is revolutionizing production by offering faster, more cost-effective solutions for creating complex parts and prototypes.
- Prototyping automation: Rapid prototyping through 3D printing allows businesses to test designs more quickly and refine products without lengthy production cycles. 3D printing allows manufacturers to produce products with complex geometries and customized features.
- Customization: Additive manufacturing enables cost-effective customization, allowing companies to produce tailored electronic components and products in smaller batches without retooling.
- Reduction in waste: As a form of additive manufacturing, 3D printing uses only the material required for each item, contributing to more sustainable practices.
Sustainability and Green Manufacturing
Automation plays a crucial role in advancing sustainability in manufacturing.
- Energy optimization: Automated systems help monitor and reduce energy consumption, ensuring processes run efficiently with minimal waste. Automation also helps improve worker safety by reducing the need for human labor in dangerous tasks.
- Waste reduction: Advanced machinery and AI can minimize material waste through precision and optimized resource use in dangerous tasks.
- Eco-friendly production: Automation supports greener production methods by enabling the efficient implementation of renewable energy sources and recycling processes in manufacturing.
Frequently Asked Questions on Automation in Manufacturing
Automation is reshaping manufacturing, and small and medium-sized businesses need to understand its potential. Here are answers to frequently asked questions that address common concerns about automation.
What is automated manufacturing?
Automated manufacturing uses technology, such as machinery, software, and robotics, to carry out production tasks and automated processes with minimal human intervention. Automation technology enhances precision, productivity, and error reduction in manufacturing processes. This improves efficiency, precision, and consistency, allowing businesses to reduce their dependence on manual labor while speeding up production processes.
How does automation affect manufacturing costs?
Automation helps reduce manufacturing costs and reduced costs by cutting labor expenses and minimizing material waste. While there may be a high initial investment, the long-term savings and efficiency gains can justify the expense. Additionally, it improves accuracy and decreases errors, which means fewer costly mistakes and optimized resource usage. These factors lead to higher profitability and greater financial control over operations.
What types of manufacturing processes can be automated?
Automation can be applied to a wide range of manufacturing processes and production systems. Automation can handle various manufacturing tasks, from assembly to quality control, enhancing efficiency and consistency. Assembly lines can be streamlined by automating repetitive tasks, while packaging processes become faster and more precise with automated systems. Cutting and machining tasks benefit from improved accuracy, and automated quality control systems help detect defects early, ensuring products meet consistent standards.
Is automation suitable for small and medium-sized businesses?
Automation is not just for large-scale manufacturers. Automation can significantly benefit a manufacturing business by improving efficiency and accuracy in inventory management and production forecasting. Many SMBs can benefit from affordable and scalable automation solutions. With flexible, cloud-based technologies and modular systems, businesses can start small and gradually implement automation across the entire supply chain as they grow, without needing large upfront investments.
What is the difference between robotics and automation?
Robotics is a specific branch of automation that focuses on machines performing physical tasks, such as welding or assembling components. Industrial robots are commonly used for repetitive tasks, while programmable logic controllers (PLCs) control machine and device tasks. In contrast, automation is a broader concept that encompasses both physical tasks performed by robots and digital processes like workflow automation and software-driven optimization.
How does automation improve product quality?
Automation enhances product quality by ensuring precision and consistency in production processes. Automated quality control systems help detect defects early, ensuring consistent standards. Since automated systems reduce human error, products are manufactured to consistent standards, which results in fewer defects and improved customer satisfaction.
What are the initial steps in implementing automation?
The first steps in implementing automation involve assessing current processes to identify inefficiencies and bottlenecks. Monitoring overall equipment effectiveness (OEE) can help identify areas for improvement. Afterward, businesses should choose technologies that match their needs and scale, ensuring that new systems can be integrated smoothly with existing operations.
How can SMBs overcome the challenges of automation?
SMBs can successfully overcome challenges in automation by starting with small-scale implementations in key areas, training employees to work with new systems, and selecting scalable solutions that allow for future growth. Automation enables continuous improvement by optimizing production processes and reducing waste. These strategies help minimize disruptions and maximize the return on investment.
Additionally, SMBs should adopt increased efficiency by leveraging automated equipment that can outperform human workers in speed and accuracy. This optimization of production processes and reduction of human error collectively enhance productivity and resource utilization, giving manufacturers a competitive edge.
What are the potential risks of automating production?
While automation offers many benefits, there are risks involved, including high upfront costs, potential integration challenges, and the possibility of technical failures. The high initial investment can be a significant barrier for some businesses. However, with proper planning, maintenance, and a phased approach involving human employees, businesses can mitigate these risks and enjoy long-term advantages.
How will automation evolve in the future?
Automation is expected to evolve by incorporating more advanced technologies like artificial intelligence (AI), the Internet of Things (IoT), and sustainable practices. Smart manufacturing integrates advanced automation technologies, data analytics, and digital tools to enhance efficiency and real-time insights. These advancements will make manufacturing more efficient, adaptable, and environmentally friendly, helping businesses stay competitive in a rapidly changing manufacturing industry.
List of Resources
- The Wall Street Journal — Humanoid Robots Finally Get Real Jobs
- The Engineering Institute of Technology — Global industrial automation market expected to reach $307.7B in 2030
- McKinsey Global Institute — Jobs lost, jobs gained: What the future of work will mean for jobs, skills, and wages