In manufacturing, controlling and planning processes directly impacts the quality, efficiency, and overall success of production. A manufacturing control plan serves as a foundational tool, helping businesses establish process parameters, quality checks, and resource allocations that keep production consistent and reliable. Meanwhile, effective manufacturing planning ensures the right materials, equipment, and personnel are in place at the right time, reducing bottlenecks and minimizing waste.
Together, these strategies empower small and medium-sized businesses to respond to market demands, optimize resources, and maintain high-quality standards. By implementing a control plan tailored to their manufacturing process, companies can streamline operations, improve production schedules, and ultimately support business growth while keeping quality intact at every stage.
- Understanding Manufacturing Control and Planning
- Key Elements of a Manufacturing Control Plan
- Building an Effective Manufacturing Planning Strategy
- Tools and Technologies for Manufacturing Control and Planning
- Creating a Customizable Control Plan for Manufacturing
- Benefits of a Well-Structured Control and Planning System
- Frequently Asked Questions on Manufacturing Control Plan and Manufacturing Planning
Understanding Manufacturing Control and Planning
Efficient manufacturing hinges on two core components: control and planning. While manufacturing control ensures processes stay on track to produce consistent, high-quality results, manufacturing planning lays the groundwork by organizing resources and setting production timelines. Together, these elements shape a well-coordinated system that meets quality, cost, and scheduling demands.
Definition of Manufacturing Control
Manufacturing control is the process of monitoring and regulating production activities to maintain consistent product quality, optimize costs, and reduce errors. By establishing specific parameters for each phase of production, a manufacturing control plan helps businesses ensure that every product meets set standards while minimizing variations. Control plans in manufacturing are designed to address potential risks by setting checkpoints, conducting regular inspections, and employing preventive actions that keep operations within optimal limits. This approach not only supports efficient production but also provides a proactive way to manage quality and reduce costs tied to rework or defect management.
The Importance of Manufacturing Planning in Production
Manufacturing planning is essential to aligning resources, schedules, and processes with production targets, acting as the backbone of efficient production management. A well-structured manufacturing planning process includes forecasting demand, setting achievable production goals, and organizing workforce and materials to ensure steady output. Planning also helps businesses respond to fluctuations in demand or resource availability by building flexibility into their production workflows. For small and medium-sized businesses, manufacturing planning is a critical strategy to optimize resources, minimize waste, and maintain reliable delivery schedules that can adapt as market conditions change.
How Control and Planning Work Together
Manufacturing control and planning are interconnected processes that reinforce each other to ensure stable, high-quality production. While manufacturing planning outlines the necessary resources, timelines, and capacities, manufacturing control ensures that each aspect of production stays within these established parameters. Together, they create a system where production flows smoothly, quality standards are consistently met, and any deviations can be quickly identified and corrected. This harmony between control and planning not only enhances productivity but also supports a company’s ability to deliver reliable, high-quality products that align with market demands, positioning it for long-term success.
Key Elements of a Manufacturing Control Plan
To create a robust manufacturing control plan, businesses must identify and manage several critical elements. These include setting quality benchmarks, defining process controls, establishing thorough documentation, and conducting regular inspections. Each element works to support stable production and high-quality outcomes, essential for competing in a demanding market.
Setting Up Quality Standards
Setting measurable quality standards forms the backbone of consistent production, defining clear expectations for product performance and reliability. Quality standards should be specific to the business, taking into account industry regulations, customer needs, and internal goals. By establishing these standards, businesses can avoid production errors, reduce variability, and build a strong reputation for delivering reliable products.
Key considerations when defining quality standards include:
- Product specifications such as dimensions, strength, or material composition.
- Compliance requirements related to safety, environmental impact, or industry certifications.
- Customer expectations for quality, durability, and functionality.
These benchmarks help create a consistent framework for production and ensure each product aligns with both market and regulatory expectations.
Defining Process Parameters and Controls
Defining process parameters is essential for managing the production environment and ensuring high-quality outputs. Process parameters include any operating condition — temperature, pressure, speed, or timing — that influences product quality. By identifying and setting up controls for these variables, companies can detect and address deviations early, preventing small issues from becoming costly problems.
Key parameters to monitor include:
- Environmental factors like humidity or temperature that may impact material properties.
- Equipment settings that affect production speed, pressure, or precision.
- Material flow rates to ensure efficient use of resources and maintain consistent outputs.
These checkpoints serve as safeguards, allowing for quick adjustments that preserve quality throughout production.
Developing Documentation and Data Collection Methods
Documentation and data collection are crucial for tracking production performance and enabling continuous improvement. By maintaining clear, accurate records — whether through digital logs or inspection forms — businesses can analyze data over time to identify trends, optimize processes, and improve compliance.
Effective documentation methods may include:
- Production logs to record time, materials, and batch specifics.
- Inspection records for tracking quality control checks and outcomes.
- Digital data capture systems that automate and centralize data for easy access and analysis.
Such documentation not only supports regulatory requirements but also provides insights into production inefficiencies or recurring quality issues, guiding targeted improvements.
Implementing Regular Inspections and Audits
Regular inspections and audits play a vital role in maintaining production quality and ensuring processes align with defined standards. Inspections focus on specific factors, such as equipment performance or raw material quality, while audits offer a comprehensive review of the manufacturing system. These practices allow businesses to proactively manage issues before they escalate, fostering a culture of continuous quality management.
Regular inspections and audits deliver multiple benefits, including:
- Early detection of potential issues before they impact production.
- Validation of process compliance with quality standards and regulatory requirements.
- Opportunities for ongoing improvement through detailed review and feedback.
Together, these elements strengthen the overall manufacturing control plan, creating a production system that is both reliable and adaptable to market demands.
Building an Effective Manufacturing Planning Strategy
Developing a strong manufacturing planning strategy enables businesses to make optimal use of resources, streamline production, and adapt quickly to changing demands. A well-structured approach to planning keeps production running smoothly and ensures timely, high-quality output.
Assessing Resource Availability and Requirements
The first step in manufacturing planning is to assess resource availability, including workforce, equipment, and raw materials. Without a clear understanding of available resources, production goals may fall short, leading to inefficiencies or delays. Resource assessment should cover:
- Workforce capacity — ensuring the right number of skilled employees are available to handle production needs.
- Equipment readiness — verifying that machinery is properly maintained and can handle the workload.
- Material sourcing — confirming adequate supply of raw materials to avoid bottlenecks.
Regular assessments allow manufacturers to identify gaps, make necessary adjustments, and allocate resources effectively, setting the foundation for a reliable production plan.
Establishing Production Schedules and Timelines
Creating a production schedule that aligns with demand forecasts is essential for maintaining productivity. Schedules define when, how, and where production activities take place, allowing companies to optimize output while minimizing idle time. Key aspects of production scheduling include:
- Task prioritization — sequencing tasks to ensure critical production stages are completed on time.
- Timeline development — setting realistic start and end times for each task to maintain consistent workflow.
- Bottleneck management — identifying and addressing areas prone to delays to improve overall efficiency.
Effective scheduling streamlines workflows, making it possible to meet production goals without unnecessary downtime or cost increases.
Balancing Demand Forecasting with Production Capacity
Demand forecasting helps businesses anticipate market needs, but it’s equally important to balance forecasts with actual production capacity. Overproduction leads to wasted resources, while underproduction risks unfulfilled orders. A balanced approach considers:
- Historical data analysis to predict likely demand.
- Capacity evaluation to determine realistic production limits.
- Adjustment plans for scaling production up or down as necessary.
Balancing demand and capacity prevents strain on resources and supports a sustainable, cost-effective production environment.
Monitoring Workflow and Adjusting for Continuous Improvement
Continuous monitoring of workflows allows manufacturers to identify inefficiencies and adapt processes for better performance. Workflow adjustments, whether in task timing, sequencing, or resource allocation, help improve flexibility and responsiveness. Regular monitoring promotes:
- Quick adaptation to unforeseen issues, such as equipment malfunctions.
- Increased productivity through the elimination of redundant steps.
- Ongoing process refinement for optimized resource usage.
This cycle of monitoring and adjustment not only drives productivity but also enables manufacturers to adapt their planning strategies in response to evolving market conditions.
Tools and Technologies for Manufacturing Control and Planning
Leveraging the right tools and technologies for manufacturing control and planning helps streamline production processes, enhance efficiency, and ensure quality standards. Modern software solutions enable real-time tracking, data collection, and smart scheduling to keep production on course.
Manufacturing Control Systems
Manufacturing control systems are designed to automate critical aspects of production oversight, from data collection to compliance tracking. These systems gather data directly from machines and workflows, providing real-time insights into production status, equipment performance, and quality metrics. Through continuous monitoring and automated alerts, control systems make it easier to detect deviations, correct errors, and maintain consistent quality standards. By replacing manual checks with automated controls, these systems significantly reduce errors and help manufacturers stay compliant with industry regulations.
Manufacturing Planning Software Solutions
Manufacturing planning software is essential for managing resource allocation, scheduling, and demand forecasting. By integrating planning software into daily operations, manufacturers can automate resource distribution based on demand projections and inventory levels, which minimizes downtime and maximizes output. Key benefits include:
- Efficient resource management — software allocates materials and labor where they’re needed most.
- Dynamic demand forecasting — algorithms analyze historical and real-time data to predict demand fluctuations.
- Improved decision-making — centralized data provides managers with actionable insights to optimize production planning.
Planning software brings agility to production, allowing businesses to adapt to shifting demands and resource availability with minimal disruption.
Production Scheduling Software and Its Advantages
Production scheduling software focuses on creating optimized timelines and managing task priorities to reduce delays and downtime. This software allows manufacturers to plan task sequences, set production targets, and allocate resources efficiently. Key advantages of using scheduling software include:
- Enhanced timeline management — automated scheduling creates accurate, achievable timelines.
- Bottleneck reduction — schedules are optimized to identify and alleviate potential production bottlenecks.
- Improved task prioritization — critical production tasks are managed in sequence, improving workflow stability.
By automating scheduling, manufacturers can ensure a smooth production flow, minimize delays, and boost overall productivity, making it a valuable investment for process efficiency and resource optimization.
Read‑alikes
Bill Of Materials (BOM): Definition, Examples, Format and Free Template
Managing Production in a Small Manufacturing Company: Planning, Control, and Profit Calculation
Full Guide to MRP Solutions: Core Features, Advantages and Pitfalls
Creating a Customizable Control Plan for Manufacturing
A well-defined control plan ensures manufacturing processes meet quality standards, minimize defects, and maximize efficiency. However, to address the unique challenges of different manufacturing environments, a customizable control plan is essential. By tailoring a control plan to specific production needs, manufacturers can improve consistency and reduce variability across operations.
Steps to Draft a Control Plan
- Identify key processes — Start by determining the critical production steps that directly affect product quality.
- Set measurable standards — Establish clear, quantifiable quality standards for each process.
- Define process parameters — Specify key variables (e.g., temperature, pressure, speed) that need monitoring.
- Assign responsibility — Assign team members to oversee specific parameters and ensure compliance.
- Set control limits — Determine acceptable ranges for each parameter, outlining the actions to take if deviations occur.
- Create documentation — Document all procedures, inspections, and corrective actions to ensure consistency.
A well-structured control plan enables manufacturers to proactively address issues before they become problems, ensuring consistent output and quality.
Adapting the Control Plan for Different Manufacturing Processes
Different manufacturing processes require different approaches to control planning. Whether dealing with batch production, assembly lines, or custom orders, each process will have unique quality and efficiency requirements. Customizing the control plan involves:
✅ Adjusting parameters for specific workflows — Tailor control methods to suit the specific machinery, tools, or technologies in use.
✅ Aligning with product type — Products with varying complexity may require different control methods, such as more frequent checks for high-precision items.
✅ Incorporating regulatory standards — Customize controls based on industry-specific regulations, ensuring compliance without unnecessary overhead.
Customizable control plans allow manufacturers to address the nuances of their operations, delivering improved control and stability.
Ensuring Continuous Review and Updates to the Control Plan
As production processes evolve, so too must the control plan. Regular reviews are essential to ensure the plan remains relevant and effective. Consider these steps:
✅ Monitor performance — Continuously track production data to identify opportunities for improvement.
✅ Update for new standards — As industry regulations and best practices evolve, adjust the control plan to stay compliant.
✅ Integrate feedback — Collect input from production teams to refine processes and address emerging challenges.
Continuous updates ensure the control plan remains aligned with evolving production needs, quality expectations, and regulatory standards, enhancing long-term manufacturing success.
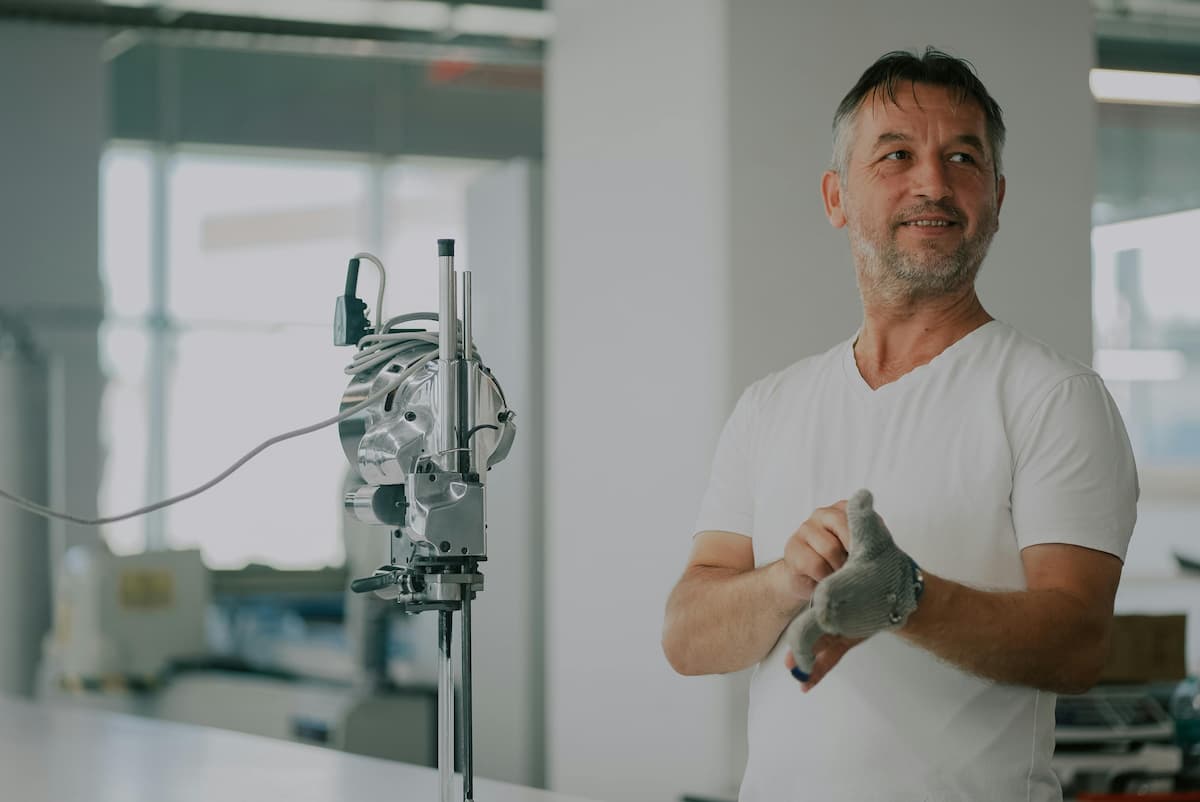
Benefits of a Well-Structured Control and Planning System
Implementing a robust control and planning system in manufacturing has far-reaching effects. From consistent product quality to improved resource management, the benefits are both immediate and long-term. A well-structured system helps organizations adapt to changing demands while maintaining operational excellence.
Enhanced Quality Assurance
Effective control and planning systems directly impact product quality. By establishing measurable quality standards and clear process parameters, manufacturers can minimize errors, reduce variability, and ensure consistent output. This approach allows for:
- Reduced defects — Proactive control limits prevent deviations that lead to quality issues.
- Standardized processes — Repeating best practices across the production line ensures uniformity.
- Early issue detection — Real-time monitoring allows quick identification of problems before they escalate.
Such systems enable manufacturers to meet both customer expectations and regulatory requirements, building long-term trust and reputation.
Cost Savings and Efficiency Gains
A well-structured control and planning system reduces costs across various aspects of production. By minimizing rework, material waste, and operational downtime, manufacturers can significantly boost their bottom line. The benefits include:
- Lower material waste — Precision in resource allocation reduces excess and unused materials.
- Fewer reworks and recalls — Preventing errors at early stages reduces costly corrections later.
- Optimized resource use — Effective planning ensures that workforce and machinery are utilized efficiently, cutting unnecessary overhead.
Such efficiency gains contribute to greater profitability, as manufacturers can produce more at a lower cost, thereby improving their competitive edge.
Increased Flexibility and Responsiveness
A dynamic control and planning system enhances flexibility, enabling manufacturers to swiftly adapt to changing market conditions. Key benefits include:
- Quick response to demand shifts — Adjust production schedules in real-time to accommodate customer demands.
- Efficient resource allocation — React to shortages or excess inventory without major disruptions.
- Customization capabilities — Tailor processes for short-term or one-off production runs, improving responsiveness to customer needs.
This adaptability positions manufacturers to thrive in volatile markets, meeting demand without sacrificing quality or efficiency.
Greater Compliance and Risk Mitigation
Manufacturers operating in regulated industries must adhere to stringent standards. A structured control and planning system supports compliance and minimizes operational risks by:
- Ensuring regulatory adherence — Built-in compliance tracking ensures processes meet industry regulations.
- Risk management — Early detection of potential process failures reduces the likelihood of costly operational disruptions.
- Documenting controls and audits — Detailed records support audits and verification, ensuring transparency and traceability.
A reliable control and planning system not only helps avoid penalties but also safeguards against costly disruptions and legal liabilities, enhancing overall risk management.
Frequently Asked Questions on Manufacturing Control Plan and Manufacturing Planning
In this section, we address the most commonly asked questions about manufacturing control and planning. These insights aim to clarify key concepts, guide decision-making, and offer actionable advice for businesses looking to enhance their production processes.
What is a manufacturing control plan?
A manufacturing control plan is a comprehensive document that outlines the procedures, standards, and parameters for managing production processes. It serves as a blueprint for ensuring product consistency, quality, and efficiency throughout the manufacturing lifecycle. Key components typically include quality standards for each stage of production, process parameters to define acceptable ranges for critical factors, inspection points for ensuring compliance and quality control, and data collection methods to track performance and identify areas for improvement. A well-crafted control plan acts as both a reference and a guide to ensure systematic, high-quality production.
How does a manufacturing control plan improve production quality?
By detailing every step of the manufacturing process, control plans reduce the risk of defects and ensure consistency. The plan helps to standardize operations, which ensures that quality remains stable across multiple production runs. The control plan minimizes process variations that could lead to defects, standardizes inspections to maintain consistent product quality, and provides clear benchmarks for measuring success and identifying issues early. These structured approaches directly impact product reliability, reducing waste and improving customer satisfaction.
What software is best for manufacturing planning?
Choosing the right manufacturing planning software depends on the scale and specific needs of your business. For smaller businesses, solutions like Kladana ERP or Zoho ERP provide a comprehensive, affordable way to manage production schedules, resources, and inventory. For larger operations, more robust platforms like SAP or Oracle ERP offer advanced features for complex manufacturing environments. When selecting software, it’s essential to consider integration capabilities with existing tools, scalability as your business grows, and the availability of detailed analytics and reporting features to support continuous improvement.
Can small businesses benefit from a control and planning system?
Yes, small businesses can gain significant advantages from a control and planning system. Even at a smaller scale, manufacturing control plans streamline workflows, improve resource utilization, and enhance product quality. The key benefits include cost savings from reduced waste and rework, improved production scheduling to meet demand efficiently, and enhanced process control to maintain consistent output without overextending resources. Adopting structured control systems early in business growth ensures scalability and smoother transitions as the company expands.
How frequently should a control plan be updated?
Control plans should be regularly reviewed and updated to reflect changes in production processes, new product designs, or changes in regulations. A common practice is to update the plan annually to incorporate any major process changes, after every significant product or process change, and when new quality standards or industry regulations are introduced. Frequent updates ensure the plan remains relevant and continues to support operational goals.
What is the difference between manufacturing control and quality control?
While both manufacturing control and quality control are aimed at improving product quality, they focus on different aspects. Manufacturing control encompasses the entire process, from resource allocation to production scheduling, ensuring that all parts of the operation run efficiently. Quality control, on the other hand, is focused specifically on monitoring and maintaining the standards of the finished product, detecting defects, and ensuring compliance with product specifications. While the two are interconnected, manufacturing control ensures processes run smoothly, while quality control ensures the final output meets standards.
How can a control plan help in resource management?
A manufacturing control plan helps optimize resource utilization by ensuring that machinery, workforce, and materials are allocated effectively. It provides a framework for accurate demand forecasting, so resources are not under or over-utilized. The control plan also helps identify bottlenecks or resource shortages early, allowing corrective actions to be taken promptly. Additionally, it ensures proper machine maintenance and workforce scheduling to prevent downtime and maximize efficiency.
What factors affect production scheduling?
Several variables can impact production scheduling, including demand fluctuations, which require adjustments to meet customer needs, lead times for raw materials, which affect how far in advance production can be planned, and resource availability, ensuring that equipment and labor are available when needed. Production bottlenecks may also require adjustments in workflows to minimize delays. A good control and planning system allows businesses to adjust their schedules dynamically based on these factors.
How do manufacturing control systems support compliance?
Manufacturing control systems automate many tasks involved in regulatory compliance, such as tracking material certifications and other required documentation, automating data collection for easier audit trails, and providing real-time monitoring to ensure adherence to health, safety, and environmental standards. These systems help companies meet industry standards while reducing the risk of non-compliance.
What are the key benefits of using a control plan PDF template?
Control plan templates streamline the creation of new plans by providing a structured framework that can be customized. The benefits include consistency in how control plans are developed and documented, ease of use by offering a pre-designed format, reducing the time spent on planning, standardization, ensuring all teams follow the same protocols and guidelines, and documented history that simplifies audits and updates. Templates save time and reduce the chance of errors, making them an efficient tool for maintaining control and planning consistency across operations.