Efficient operations management is the backbone of any successful manufacturing business. At the heart of this efficiency lies Material Requirements Planning (MRP), a system that not only optimizes inventory management but also drives production scheduling and demand forecasting. For small and medium-sized businesses, juggling material availability, production timing, and customer demands can be daunting. That’s where MRP steps in, transforming complex processes into manageable workflows, reducing waste, and boosting productivity.
As automation in production and operations management becomes critical, understanding how MRP systems work is crucial for maintaining a competitive edge. Let’s explore how MRP can unlock new efficiencies for your manufacturing operations and help you stay agile in an ever-evolving market.
- What is MRP in Operations Management?
- Core Objectives of MRP in Operations Management
- The Role of MRP in Inventory Management
- How MRP Automates Production Systems and Operations Management
- Benefits of MRP in Operations Management
- The Future of MRP in Operations Management
- Frequently Asked Questions on MRP in Operations Management
What is MRP in Operations Management?
Material Requirements Planning (MRP) is an essential tool in modern operations management, designed to optimize the way manufacturers plan, schedule, and manage their inventory. For businesses where production is heavily reliant on the availability of raw materials and precise timing, MRP offers a structured approach to ensure everything aligns perfectly — from material supply to finished goods delivery. But beyond being just a planning tool, MRP acts as a powerful driver of efficiency, automating complex tasks that, if handled manually, would lead to costly errors and delays.
Defining MRP in Operations Management
At its core, MRP is a system built to coordinate production activities. It breaks down a business’s production process into digestible components, calculating the materials needed for each stage of production. By analyzing demand forecasts, production timelines, and inventory levels, MRP helps businesses determine what materials to order, when to order them, and how much is required. This ensures there is no overstocking or stockouts, two common problems in inventory management that can hurt production schedules and increase costs. More than just managing resources, MRP contributes to the overall health of a company’s supply chain, aligning it more closely with real-world customer demands.
Historical Development of MRP Systems
MRP has its roots in the 1960s when manufacturers first began adopting computerized systems to cope with the growing complexity of production processes. Initially designed to solve basic inventory issues, early MRP systems were rudimentary, focusing on ordering materials at the right time. Over the decades, MRP has evolved significantly, integrating more advanced algorithms, real-time data analysis, and automation features. Today, MRP is often incorporated into broader Enterprise Resource Planning (ERP) systems, creating a seamless link between production, inventory, sales, and accounting, marking its transition from a manual tool to an indispensable software solution in operations management.
Core Objectives of MRP in Operations Management
The implementation of an MRP system in operations management goes far beyond simply tracking inventory or automating production schedules. It’s about transforming the way businesses handle their resources, aligning production with actual demand, and ultimately, driving efficiency at every level. MRP helps businesses move from reactive to proactive management, where planning is data-driven and every decision — whether it’s ordering materials or scheduling production — is optimized for maximum output with minimum waste.
Improving Inventory Management
One of the core objectives of MRP is improving how businesses manage their inventory. Traditional inventory systems often struggle with either overstocking, which ties up capital and space, or understocking, which halts production and disappoints customers. MRP solves this by ensuring materials are ordered exactly when needed, based on real-time demand forecasts and production schedules. By offering better visibility into what’s in stock and what’s required for future orders, MRP reduces both the likelihood of excess inventory and costly stockouts. This keeps operations running smoothly while reducing inventory holding costs — an important balance for small and medium-sized businesses.
Enhancing Production Planning and Scheduling
MRP’s ability to seamlessly align production schedules with actual demand is another game-changer. By analyzing current orders, inventory levels, and production capacity, MRP provides a clear roadmap for what needs to be produced and when. This allows businesses to minimize lead times and eliminate bottlenecks that can slow down production. MRP’s scheduling capabilities also ensure that each component is ready precisely when needed, helping avoid costly delays in the manufacturing process.
Reducing Waste and Costs
MRP systems are designed with cost-efficiency in mind. By optimizing inventory levels and production schedules, MRP helps reduce excess material waste. When inventory is carefully managed and production flows without interruption, businesses experience lower operational costs, fewer last-minute purchases, and less wasted material. This streamlined approach is crucial for businesses looking to remain competitive while improving their bottom line.
The Role of MRP in Inventory Management
For small and medium-sized businesses, inventory management can often feel like walking a tightrope — one wrong step, and either stockouts or overstocking can throw everything off balance. This is where Material Requirements Planning (MRP) shines. By leveraging precise data and automation, MRP enables businesses to manage inventory more effectively, minimizing risks and ensuring that the right materials are always available at the right time. For SMBs, this translates to improved cash flow, less waste, and a more efficient production process that is better equipped to meet customer demands.
Real-Time Inventory Tracking
MRP offers businesses the advantage of real-time inventory tracking, a feature that improves visibility across the entire supply chain. By constantly monitoring stock levels, MRP can provide up-to-the-minute data on what’s available, what’s in production, and what needs to be ordered. This level of visibility helps reduce errors that often result from manual stock tracking, such as double-ordering or failing to reorder in time. Real-time tracking also ensures that decision-makers can react quickly to fluctuations in demand, maintaining agility in operations.
Just-in-Time Inventory
The Just-in-Time (JIT) approach is a popular strategy for minimizing excess inventory, and MRP plays a crucial role in supporting it. MRP systems can forecast material requirements based on actual demand and production schedules, allowing businesses to receive materials just as they are needed in the production process. This not only reduces the need for large storage spaces but also cuts down on the capital tied up in unsold inventory. By syncing material orders with production demand, MRP ensures that businesses can run leaner, more efficient operations.
Avoiding Stockouts and Overstocking
One of the biggest challenges in inventory management is balancing supply with demand. Overstocking leads to wasted resources, while stockouts can halt production and damage customer relationships. MRP mitigates both issues by using accurate demand forecasts and production timelines to order materials only when needed. With MRP, businesses can ensure they have enough stock to meet customer orders without overburdening themselves with excess inventory. This equilibrium keeps production flowing smoothly, improves customer satisfaction, and reduces the financial strain associated with poor inventory management.
Learn How to Automate Your Business with Kladana ERP
- End-to-end ERP — manage inventory, production & sales
- Smooth onboarding — 1–3 sessions
- Quick support response — 5–15 minutes
- Flexible solution — unlimited API and seamless integrations
- Dependable infrastructure — fully-managed and secure cloud-based software
How MRP Automates Production Systems and Operations Management
As businesses scale, manual processes become inefficient and prone to errors. MRP helps by automating key functions, transforming operations from reactive to proactive planning. This automation enhances accuracy and efficiency, especially for small and medium-sized businesses, leading to better productivity, fewer mistakes, and a more streamlined production process. Let’s dive into how MRP automates production planning, integrates with other systems, and improves supply chain management.
Automating Production Planning and Scheduling
Production planning and scheduling involve managing various elements like materials, workforce, and machinery. MRP automates these complex tasks by using real-time data to generate precise production schedules, eliminating manual errors and overlaps. Key benefits include:
- Real-time adjustments to schedules based on current demand
- Reduced downtime and maximized resource use
- Fewer manual errors and scheduling conflicts
Integrating with Other Systems (ERP, CRM, Accounting)
One of MRP’s biggest strengths is its ability to integrate with other systems like ERP, CRM, and accounting software. This creates a unified platform where data flows seamlessly between different departments. For example:
- CRM systems feed customer orders into MRP, adjusting production schedules
- Accounting software informs MRP of cash flow constraints, optimizing procurement
- ERP systems ensure all departments operate in sync with real-time data
Streamlining Supply Chain Operations
MRP automates and optimizes the supply chain by syncing production needs with supplier deliveries. This ensures that materials arrive exactly when needed, improving overall efficiency. Key impacts include:
- Timely procurement to avoid production delays
- Reduced excess inventory through precise material ordering
- Stronger supplier relationships with clear and timely orders
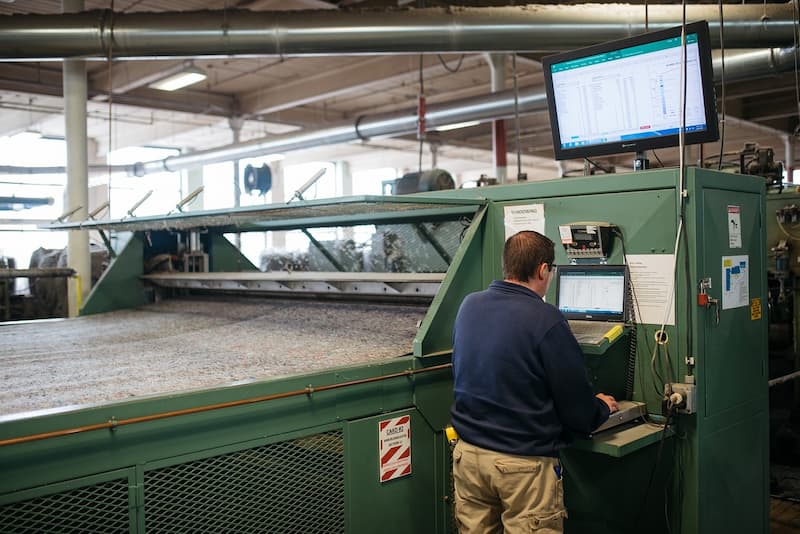
Benefits of MRP in Operations Management
Implementing an MRP system brings transformative benefits to operations management, allowing businesses to shift from reactive strategies to proactive, data-driven decisions. MRP is designed to streamline complex processes, reduce inefficiencies, and maximize resource use. For small and medium-sized businesses (SMBs), this means enhanced productivity, lower costs, and a more agile response to changing market conditions. Let’s explore the key benefits that MRP systems offer for operational efficiency.
Increased Efficiency and Productivity
MRP drives efficiency by automating tasks that would otherwise consume valuable time and resources. These automated processes include:
- Inventory tracking: No more manual stock counting or error-prone spreadsheets.
- Production scheduling: MRP ensures that materials and labor are allocated where needed, precisely when needed.
By reducing the need for constant human intervention, MRP frees up valuable time, enabling teams to focus on higher-value activities such as strategic planning and innovation. This automation results in fewer production delays, faster lead times, and overall higher output.
Cost Savings and Improved ROI
One of the most immediate benefits of MRP is its impact on reducing operational costs. Key areas where businesses experience savings include:
- Reduced inventory carrying costs: MRP ensures that businesses hold only the necessary stock levels, lowering storage expenses.
- Minimized material waste: With MRP optimizing material orders, over-purchasing and waste are dramatically reduced.
These cost reductions lead to a faster return on investment (ROI) for businesses, especially for those looking to scale efficiently without inflating overhead.
Better Decision-Making Through Data-Driven Insights
MRP systems provide managers with real-time, accurate data on inventory levels, production status, and supplier performance. This data enables better, faster decision-making. For instance:
- Accurate forecasting: Businesses can anticipate demand more accurately and adjust production plans accordingly.
- Proactive problem-solving: MRP alerts managers to potential supply chain disruptions or production delays before they become costly issues.
This level of insight helps SMBs stay ahead of operational challenges, ensuring long-term growth and stability.
Read‑alikes
ERP Software for Manufacturing: 15 Best Systems
Full Guide to MRP Solutions: Core Features, Advantages and Pitfalls
The Future of MRP in Operations Management
As technology continues to evolve, Material Requirements Planning (MRP) systems are poised to undergo significant transformations. The future of MRP lies in its integration with advanced technologies like artificial intelligence (AI) and machine learning, as well as its migration to cloud-based platforms. These advancements will not only enhance the core functions of MRP but also make these systems more accessible and valuable to small and medium-sized businesses (SMBs). Let’s explore these key trends shaping the future of MRP in operations management.
Advancements in AI and Machine Learning Integration
Artificial intelligence and machine learning are set to revolutionize MRP systems by offering predictive insights and smarter automation. Current MRP systems are reactive — they rely on historical data to optimize inventory and production schedules. However, with AI and machine learning, MRP can:
- Predict future demand with greater accuracy by analyzing historical data, market trends, and customer behavior.
- Optimize production schedules dynamically, adjusting in real-time based on machine performance, workforce availability, and material flow.
- Identify inefficiencies faster by learning from past production cycles, helping businesses eliminate bottlenecks and reduce downtime.
These advancements allow businesses to make more informed decisions and respond proactively to potential disruptions, providing a competitive advantage in increasingly volatile markets.
Cloud-Based MRP Solutions for SMBs
Cloud-based MRP systems are becoming the preferred choice for SMBs due to their scalability, affordability, and accessibility. Traditional MRP systems often required significant upfront investment in hardware and IT infrastructure, but cloud solutions eliminate these barriers. Key benefits of cloud-based MRP include:
- Lower implementation costs as businesses only pay for what they use, avoiding the need for expensive on-premise servers.
- Greater flexibility with the ability to scale up or down as needed, making it ideal for growing businesses.
- Remote accessibility, allowing teams to access real-time data from anywhere, enhancing collaboration across departments and locations.
As more SMBs adopt cloud-based MRP, they can leverage the same powerful tools as larger enterprises, leveling the playing field in today’s competitive landscape.
Frequently Asked Questions on MRP in Operations Management
Understanding how Material Requirements Planning (MRP) fits into operations management can help businesses make informed decisions about their production and inventory strategies. Here, we answer some of the most frequently asked questions about MRP systems to provide clarity for those considering implementation.
What is MRP in operations management?
MRP is a system designed to streamline production planning, inventory control, and scheduling. By analyzing demand, production capabilities, and material availability, MRP ensures that manufacturers can meet production deadlines without overstocking or running out of materials.
How does MRP help in inventory management?
MRP optimizes inventory management by ensuring that materials are ordered and available exactly when needed. This prevents both stockouts, which can halt production, and overstocking, which ties up capital and space unnecessarily.
Can MRP systems integrate with other business tools?
Yes, modern MRP systems can seamlessly integrate with ERP, CRM, and accounting tools. This integration enables businesses to manage production alongside other critical functions, like sales and financial reporting, ensuring a comprehensive approach to operations management.
What are the challenges of implementing MRP?
Some common challenges include ensuring data accuracy, integrating MRP with existing systems, and managing employee resistance to change. These issues can be mitigated with careful planning, proper training, and a focus on change management strategies.
How is MRP different from ERP?
While MRP focuses specifically on manufacturing operations — such as production planning and material management — ERP (Enterprise Resource Planning) covers broader business functions, including finance, HR, and sales. MRP is often a key component within a larger ERP system.
What businesses benefit most from MRP?
Manufacturing businesses, particularly those with complex inventory and production needs, benefit the most from MRP. Companies producing goods based on fluctuating demand or working with extensive supply chains find MRP especially valuable.
Is MRP suitable for small businesses?
Absolutely. Modern MRP systems, especially those that are cloud-based, are designed to be scalable and accessible to small and medium-sized businesses. They offer the same efficiency and control benefits as larger systems but at a lower cost.
How does MRP reduce costs in manufacturing?
MRP reduces costs by optimizing the use of resources, minimizing waste, and improving production scheduling. This leads to more efficient operations, less excess inventory, and fewer last-minute material purchases, all of which contribute to lower operational costs.
What is the future of MRP systems?
The future of MRP lies in the integration of artificial intelligence (AI) and machine learning, as well as the growing trend of cloud-based solutions. These advancements will allow MRP systems to become more predictive, flexible, and accessible to businesses of all sizes.
How long does it take to implement an MRP system?
The implementation timeline varies depending on the size and complexity of the business. For smaller businesses, it could take a few weeks, while larger operations may require several months. Proper planning and employee training are key to a smooth and efficient implementation process.