Tracking production is essential for manufacturers looking to improve efficiency and keep processes running smoothly. For small and medium-sized businesses, real-time monitoring provides clear insights into the production flow, helping to identify and resolve issues before they become costly. Manufacturing tracking software offers a direct way to manage resources, reduce delays, and enhance productivity across the shop floor. By using real-time data, businesses can react quickly to changes, ensure quality control, and make informed decisions that drive efficiency. This approach not only streamlines daily operations but also sets the foundation for future growth by ensuring that all production activities are transparent and fully optimized.
- What is Production Tracking?
- The Role of Real-Time Tracking in Manufacturing
- Types of Manufacturing Tracking Systems
- Benefits of Using Manufacturing Tracking Software
- Key Features to Look for in Manufacturing Tracking Software
- How to Implement a Production Tracking System
- Frequently Asked Questions on Production Tracking for Manufacturing
Use Kladana to streamline your manufacturing tracking, minimize downtime, and reduce costs.
What is Production Tracking?
Production tracking is the process of monitoring the progress of manufacturing tasks in real-time to improve overall operational efficiency. By keeping a close eye on every step, manufacturers can identify bottlenecks, ensure deadlines are met, and streamline workflows. This practice involves capturing data from various stages of production and using it to make adjustments that can increase output, minimize downtime, and reduce errors. With the help of modern manufacturing tracking systems, this once-complex task has become more accessible, offering a clearer view of the entire production cycle.
The Basics of Production Tracking
At its core, production tracking revolves around transparency and efficiency. It allows manufacturers to monitor workflows, track resources, and ensure that every process is functioning as intended. The goal is to create a seamless production line where delays are minimized, and tasks are completed in a timely manner. By capturing real-time data, businesses gain valuable insights into how operations are running. This transparency helps to address inefficiencies, allocate resources properly, and ensure that each step in the production chain is operating at its optimal capacity. Production tracking also provides the flexibility to adjust plans when needed, allowing manufacturers to adapt quickly to changing demands.
Why Is Production Tracking Crucial for Manufacturers?
For manufacturers, production tracking is essential for staying competitive. It directly impacts productivity, ensuring that resources are used effectively and that deadlines are consistently met. Tracking also plays a vital role in reducing waste by identifying areas where improvements can be made, whether through better resource allocation or faster response times to issues. Without a clear system in place, manufacturers risk delays, bottlenecks, and resource mismanagement, all of which can lead to higher costs and missed opportunities. By monitoring production closely, businesses not only ensure smoother operations but also position themselves for long-term growth and success.
The Role of Real-Time Tracking in Manufacturing
Real-time production tracking equips manufacturers with immediate insights into their operational status, enabling more effective management of the production process. This capability not only enhances productivity but also empowers decision-makers to respond swiftly to emerging challenges.
What Is Real-Time Production Tracking?
Real-time production tracking refers to the continuous monitoring of manufacturing processes, providing up-to-the-minute updates on production activities. This system captures data from various stages of production and presents it in a user-friendly format, ensuring that manufacturers always have a clear picture of their operations. By implementing real-time tracking, businesses can access information regarding workflow status, resource usage, and overall production efficiency instantly. This visibility allows manufacturers to make timely adjustments and maintain optimal operational flow.
How Real-Time Tracking Transforms Manufacturing Operations
Real-time tracking fundamentally transforms manufacturing operations by identifying inefficiencies and potential bottlenecks before they escalate. With immediate data access, manufacturers can analyze production metrics and assess where adjustments are necessary. Key benefits include:
- Proactive Issue Resolution: Quickly identify underperforming machines or delayed production stages.
- Informed Decision-Making: Analyze production metrics to implement timely adjustments.
- Accurate Forecasting: Improve the ability to predict production timelines, enhancing overall productivity.
This proactive approach facilitates informed decision-making, enabling managers to implement solutions promptly. Additionally, real-time insights help in forecasting production timelines more accurately, ultimately leading to enhanced productivity and reduced operational costs.
The Power of Shop Floor Apps for Real-Time Tracking
Shop Floor Apps represent a significant advancement in real-time production tracking, seamlessly integrating with existing manufacturing tracking systems. These tools empower manufacturers to monitor production tasks, resource allocation, and equipment performance directly from the production floor. Key features of Shop Floor Apps include:
- Instant Data Input: Workers can input data and receive updates in real time.
- Enhanced Communication: Ensure alignment among teams regarding current production statuses.
- Improved Accountability: Foster a culture where team members engage directly with the tracking system.
By utilizing mobile applications, teams can ensure that everyone is aligned with current production statuses. This integration fosters a culture of accountability and responsiveness on the shop floor, contributing to a more streamlined and efficient manufacturing environment. Shop Floor Apps not only enhance the tracking process but also empower manufacturers to harness the full potential of real-time data in their operations.
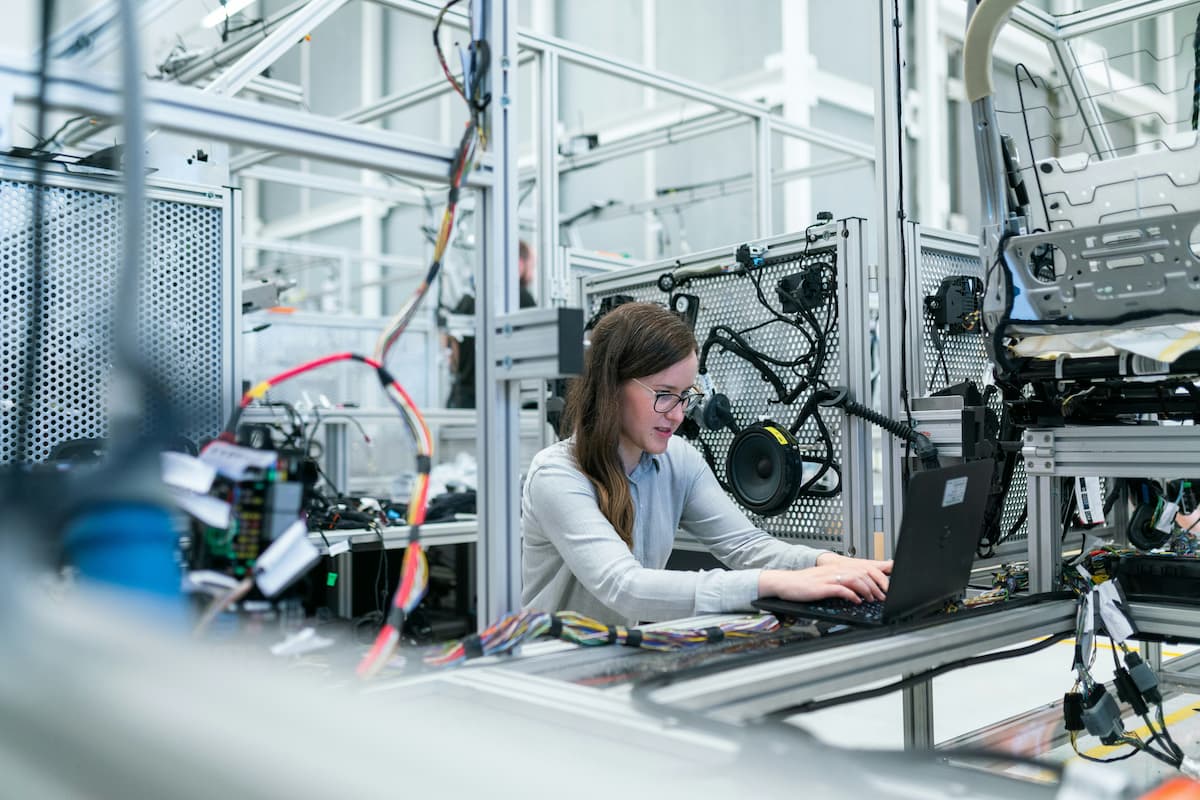
Types of Manufacturing Tracking Systems
Manufacturing tracking systems come in various forms, tailored to meet the distinct needs of businesses based on their size and complexity. Understanding these systems is vital for optimizing operations and enhancing productivity.
Manual vs. Automated Production Tracking
Manual production tracking relies on paper logs and spreadsheets, demanding significant human effort for data entry and management. While this approach can work for smaller operations, it often leads to inaccuracies and delays. In contrast, automated production tracking systems leverage technology to streamline processes, offering numerous benefits:
- Increased Accuracy: Automation minimizes human error, ensuring data integrity.
- Real-Time Updates: Instant data collection and reporting enhance decision-making.
- Resource Efficiency: Free up personnel for higher-level tasks, reducing labor costs.
Adopting automation not only boosts accuracy and efficiency but also positions businesses to scale operations effectively.
Key Components of a Manufacturing Tracking System
A robust manufacturing tracking system comprises several critical components that work together to ensure seamless operations. These elements include:
- Software: Centralized platforms that aggregate data from various sources and provide insights.
- Sensors: Devices that monitor machinery performance and track production metrics.
- Data Integration Tools: Applications that consolidate information from different systems, including Shop Floor Apps.
These components play a pivotal role in delivering comprehensive visibility into production activities, allowing manufacturers to identify trends, predict outcomes, and make informed decisions.
Choosing the Right Manufacturing Tracking System for Your Business
Selecting an appropriate manufacturing tracking system is crucial for small and medium-sized businesses aiming to enhance efficiency and support growth. Consider the following factors:
- Operational Needs: Assess specific requirements, such as production volume and complexity.
- Integration Capabilities: Ensure compatibility with existing systems to facilitate smooth data flow.
- Scalability: Choose a system that can grow alongside your business, accommodating future needs.
A well-chosen manufacturing tracking system empowers businesses to streamline operations, improve productivity, and position themselves for success in a competitive landscape. By carefully evaluating options and aligning them with operational goals, manufacturers can unlock the full potential of their production processes.
Read‑alikes
ERP Software for Manufacturing: 15 Best Systems
Managing Production in a Small Manufacturing Company: Planning, Control, and Profit Calculation
Benefits of Using Manufacturing Tracking Software
Implementing manufacturing tracking software offers significant advantages that can transform operational effectiveness and enhance productivity.
Enhanced Workflow Efficiency
Manufacturing tracking software streamlines workflows by providing transparent, real-time data that helps teams maintain optimal production flows. With clear visibility into each stage of the process, errors can be significantly reduced. This clarity allows workers to focus on their tasks, minimizing the time spent on troubleshooting and corrections, ultimately leading to a more efficient operation. By utilizing such systems, manufacturers can maintain a steady pace and enhance overall workflow efficiency.
Real-Time Data for Better Decision-Making
Access to real-time data empowers decision-makers to react swiftly to changes occurring on the production floor. Immediate insights into production metrics allow managers to identify issues as they arise, whether it’s a machinery malfunction or a sudden spike in demand. This agility enables timely adjustments, fostering a proactive approach to management that can mitigate disruptions and enhance operational stability.
Reduction in Downtime and Bottlenecks
Manufacturing tracking systems are instrumental in pinpointing potential bottlenecks and sources of downtime. By continuously monitoring operations, these systems help manufacturers identify inefficiencies in their workflows. Addressing these issues promptly ensures that production lines operate smoothly, reducing the likelihood of delays that can impact overall output.
Cost Savings Through Resource Optimization
By optimizing labor and material usage, manufacturing tracking software contributes significantly to cost savings. Efficient tracking helps identify areas where resources may be overutilized or wasted, enabling manufacturers to adjust their practices. This optimization not only reduces operational costs but also enhances profitability, making every aspect of the production process more economical.
Shop Floor Apps: A Game-Changer for Efficiency
Shop Floor Apps revolutionize the connection between management and the factory floor. By providing real-time monitoring of equipment, workers, and output, these apps enhance visibility into daily operations. Managers can quickly address issues, improve worker allocation, and ensure that production targets are met. The immediate access to data from Shop Floor Apps contributes significantly to reducing downtime and improving overall efficiency, making them an invaluable tool in modern manufacturing.
Key Features to Look for in Manufacturing Tracking Software
Selecting the right manufacturing tracking software is crucial for achieving operational excellence. Certain features can significantly enhance productivity and streamline processes.
Customizable Dashboards
Customizable dashboards are essential for effective manufacturing tracking. They allow manufacturers to visualize key performance indicators (KPIs) aligned with specific production goals. By tailoring the interface to highlight relevant metrics, such as cycle times, output rates, and equipment utilization, users can quickly assess performance and make informed decisions. This personalized approach ensures that teams remain focused on their objectives, enhancing overall efficiency and productivity on the shop floor.
Real-Time Alerts and Notifications
Real-time alerts are a vital component of manufacturing tracking software. These notifications enable manufacturers to identify and address potential production issues before they escalate into significant problems. For example, alerts can be set for deviations in production rates or equipment performance. By promptly addressing these alerts, manufacturers can minimize downtime, maintain workflow continuity, and ensure that production schedules are met. This proactive approach fosters a culture of responsiveness and enhances operational reliability.
Integration with Shop Floor Apps and Other Business Systems
Seamless integration with Shop Floor Apps, ERP, and CRM systems is paramount for comprehensive operational visibility. When manufacturing tracking software can communicate effectively with existing business systems, it ensures a smooth flow of data across all departments. This integration facilitates better coordination between production, inventory management, and sales, leading to informed decision-making and optimized resource allocation. Enhanced visibility into the entire manufacturing process empowers managers to identify trends, forecast demands, and streamline operations, ultimately driving business success.
How to Implement a Production Tracking System
Implementing a production tracking system is a strategic move that can greatly enhance operational efficiency. This process requires a thorough understanding of the business’s needs and the intended outcomes of the tracking system.
Assessing Your Manufacturing Needs
A comprehensive evaluation of current production processes is essential before implementing a tracking system. Begin by mapping out existing workflows and identifying specific areas where inefficiencies or gaps exist. Engage team members across departments to gain insights into their challenges and pain points. This collaborative approach not only uncovers valuable information but also fosters buy-in for the upcoming changes. By recognizing the unique requirements of your manufacturing environment, you can ensure that the tracking system selected will effectively address those needs.
Step-by-Step Process of System Implementation
Deploying a manufacturing tracking system involves several critical steps:
- Software Selection: Research and choose a tracking software that aligns with your operational goals and integrates well with existing systems.
- Planning: Develop a clear implementation timeline and allocate necessary resources, including budget and personnel.
- Data Migration: Ensure that historical data is transferred seamlessly to the new system to maintain continuity.
- Training: Provide comprehensive training for staff to ensure they are comfortable using the new system and can leverage its features effectively.
Following this structured approach can streamline the implementation process and minimize disruptions to daily operations.
Overcoming Common Challenges During Implementation
Resistance to change is a common hurdle when implementing a new system. To address this, foster open communication and involve employees in the process from the outset. Providing training sessions and demonstrating the benefits of the new system can help alleviate concerns. Additionally, technical integration challenges may arise; working closely with IT specialists and software vendors can ensure a smoother transition. By proactively addressing these challenges, manufacturers can enhance the likelihood of a successful implementation and drive lasting improvements in production efficiency.
Frequently Asked Questions on Production Tracking for Manufacturing
In this section, we address common questions that decision-makers may have regarding production tracking systems and the integration of Shop Floor Apps in the manufacturing landscape.
What is production tracking in manufacturing?
Production tracking refers to the process of monitoring and analyzing manufacturing workflows in real time. This system allows manufacturers to ensure optimal workflow efficiency, helping them to increase productivity and maintain high-quality standards by quickly addressing issues as they arise.
How does real-time tracking improve manufacturing efficiency?
Real-time tracking significantly enhances manufacturing efficiency by providing instantaneous updates on production status. This capability enables manufacturers to identify and address bottlenecks immediately, leading to smoother operations and reduced idle time. The immediacy of information empowers teams to make quicker decisions, adapting workflows dynamically to meet production demands.
What are Shop Floor Apps, and how do they help in production tracking?
Shop Floor Apps are innovative tools designed to give manufacturers real-time insights directly from the factory floor. These applications allow for tracking various production tasks, resource utilization, and equipment performance. By facilitating immediate data access, Shop Floor Apps enhance communication between the production team and management, ultimately leading to improved operational efficiency.
Can small businesses benefit from manufacturing tracking systems?
Absolutely. Manufacturing tracking systems are not exclusive to large enterprises; they are equally beneficial for small businesses. These systems can help small manufacturers reduce waste, optimize resource allocation, and enhance workflow efficiency. By leveraging tracking technologies, smaller operations can compete more effectively and improve their overall productivity.
What are the critical features of a good production tracking system?
A robust production tracking system should encompass several essential features:
- Real-time data monitoring: Provides immediate updates on production processes.
- Customizable dashboards: Allows manufacturers to tailor views according to specific operational goals.
- Real-time alerts: Notifies users of potential issues before they escalate.
- Integration capabilities: Seamlessly connects with existing systems such as ERP and Shop Floor Apps.
How do I choose the right tracking system for my manufacturing business?
Selecting the right tracking system involves a thorough assessment of your production scale, operational requirements, and long-term growth objectives. Evaluate systems based on how well they can be tailored to meet your specific needs and their ability to scale as your business expands.
Are manual tracking methods still relevant today?
While manual tracking methods are still employed in some settings, they are increasingly considered less efficient due to their susceptibility to errors. Automated tracking systems provide a more reliable and accurate means of monitoring production.
Can real-time tracking systems reduce production costs?
Yes, implementing real-time tracking systems can lead to significant cost reductions. By optimizing resource usage, minimizing downtime, and identifying inefficiencies early on, manufacturers can streamline their operations and cut unnecessary expenses.
What are the benefits of integrating tracking systems with Shop Floor Apps?
The integration of tracking systems with Shop Floor Apps offers numerous advantages, including enhanced real-time monitoring and improved workflow visibility. This synergy allows manufacturers to respond rapidly to operational changes, facilitating quicker decision-making and fostering a proactive manufacturing environment.
What are the future trends in production tracking?
The future of production tracking is poised to embrace deeper integration with Internet of Things (IoT) technology, artificial intelligence (AI)-driven analytics, and further automation. These advancements will enable manufacturers to achieve even greater operational insights and efficiencies, paving the way for smarter and more agile production environments.