The MRP system is like a conductor orchestrating a symphony of raw materials, machinery, and skilled labor. It has the power to transform fragmented processes into harmonious and smooth ones. In this article, we embark on a journey into the essence of MRP solutions, unravel their workings, explore their historical evolution, and shed light on the impact it has had on different industries. Explore responses to frequently asked questions about MRPs, insights from the Kladana expert, and user reviews.
According to Business Research Insights, the global MRP solutions market is growing steadily with a compound annual growth rate of 7.68% and is predicted to reach almost USD 8.29 billion by 2028.
Lots of business owners follow the trend and trust MRPs when it comes to the planning of materials requirements. But still many are not ready to trust their processes to the single software and opt for the alternative methods of planning. Let’s clear things up in this article.
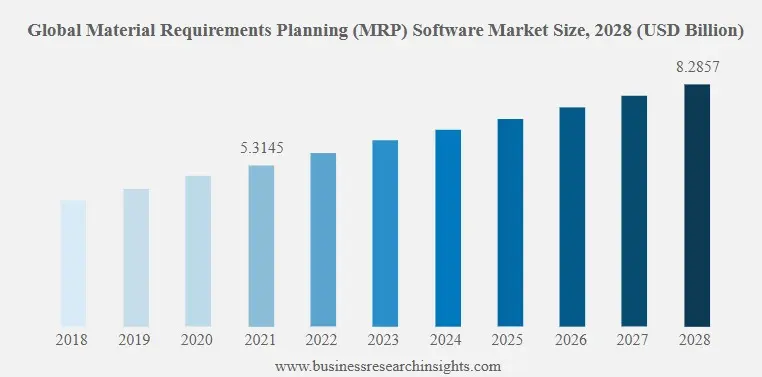
- How Does MRP Work?
- What Are the Core Inputs and Outputs of MRP?
- What are the Benefits of MRP?
- What are the Disadvantages of MRP?
- How to Choose between MRP and ERP?
- How to Launch an MRP System?
- Who Can Use MRP?
- What Are the Types of MRP Solutions?
- What Is the History of MRP?
- Which Technologies Are Applicable to MRP?
- Examples of MRP Solutions
- Frequently Asked Questions on MRP Solutions
💻 Free Webinar Recording Available!
Recently, we hosted the webinar Automation for Manufacturing Companies: Where to Begin, featuring Aleksandra Brovchuk, Kladana’s Director in India, and Uday Sharma, Senior Customer Support Executive.
They shared the insights on efficiently managing inventory, warehousing, sales, and production — all within a single app, without requiring expensive implementations or specialized skills.
Key topics covered included:
- 6 common production management challenges and solutions
- 5 steps to seamlessly implement manufacturing software
- How Kladana ERP can benefit manufacturing companies
Receive webinar recording, presentation slides, a promo code for an extended 30‑day trial, and additional content via email for free.
How Does MRP Work?
Material Requirements Planning (MRP) is a computerized inventory management system specifically crafted to aid businesses in making production schedules and planning orders for demanded items: raw materials, components, etc.
MRP process can be divided into the following key stages:
Determining Requirements to Fulfill Demand
In the initial phase of the MRP process, the primary objective is to identify customer demand and the necessary requisites to satisfy it. This stage starts with introducing customer orders and sales forecasts into the system.Deconstructing Demand with Bill of Materials
MRP proceeds to disassemble the overall demand using the bill of materials required for production. It segregates demand into its individual components and raw materials, accounting for any essential sub-assemblies in the process.Inventory Assessment and Resource Allocation
MRP helps to thoroughly examine demand versus inventory and allocate resources accordingly. This provides insights into the current inventory status and its whereabouts, which is particularly crucial when dealing with inventory spread across multiple locations.It also allows tracking the status of items, including those already earmarked for other builds and those in transit or on order. MRP facilitates the relocation of inventory to the appropriate storage locations and triggers recommendations for reordering when necessary.
Production Scheduling
The next step involves scheduling production activities. Here the system calculates the required time and labor for each step of the production process, ensuring timely execution. The production schedule also identifies the machinery and workstations necessary for each step, generating relevant work orders, purchase orders, and transfer orders. If the production involves subassemblies, the system factors in the time required for each subassembly and schedules them accordingly.Issue Identification and Recommendations
In the concluding stage, MRP serves to link raw materials with work orders and customer orders. It can autonomously notify employees about delays and propose recommendations for existing orders. This includes automatic adjustments to production schedules, the execution of «what-if» scenario analyses, and the creation of exception plans to ensure the completion of required builds.
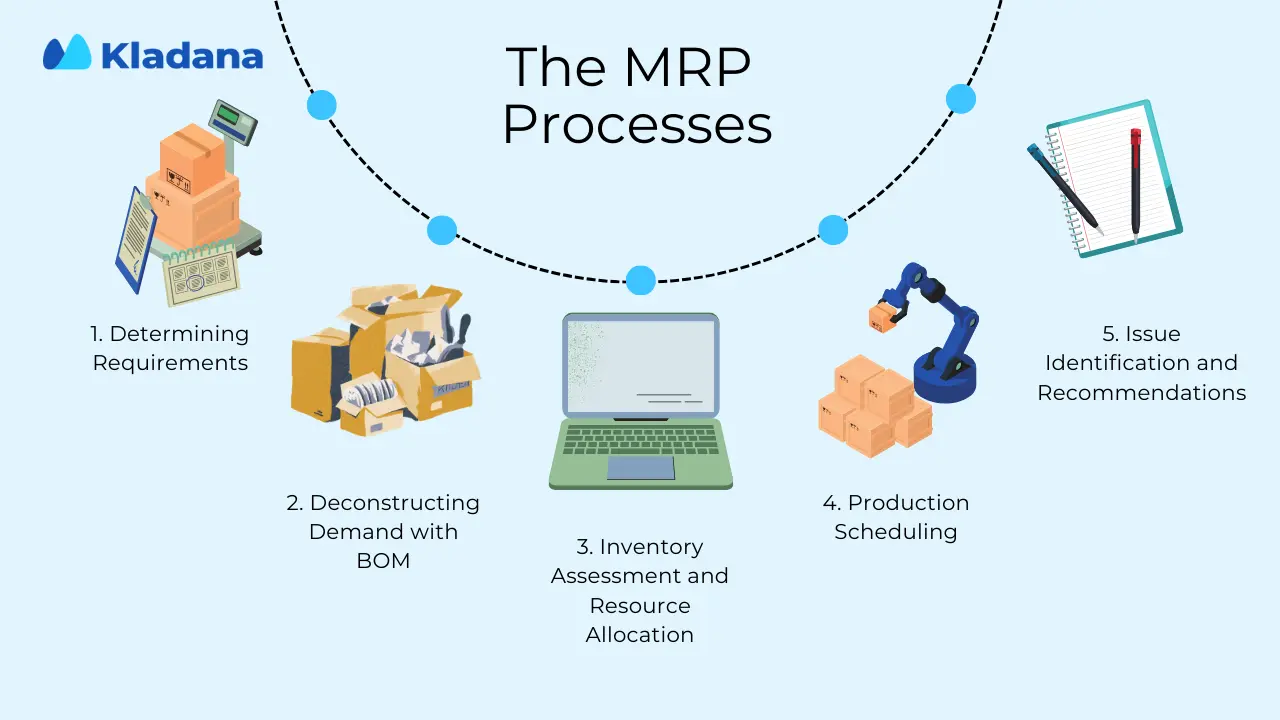
In trading, process management is relatively simple: businesses buy and sell goods, calculate profits and losses, and make corresponding records. Production is a complex process, extended over time. Various resources enter the production cycle at separate times. Work in progress is a common situation here.
You use raw materials and other resources, but you don’t get finished products. You need to monitor the production flow, costs, wear and tear, availability of raw materials, the required number of employees, equipment, warehouses, etc.
All this needs to be considered, that’s why you need special software. And the simpler the solution is, the easier it is to use. We are for simplicity.
What Are the Core Inputs and Outputs of MRP?
Understanding MRP begins with grasping its fundamental elements. An MRP system relies on several key components or inputs: the master production schedule, bill of materials (BOM), and inventory records file.
Master Production Schedule:
The master production schedule outlines the materials required for production, specifying quantities and timing. It is constructed based on the BOM, which provides intricate information about all components essential for creating the final product.
Bill of Materials (BOM):
The BOM comprises a comprehensive inventory of all necessary items for the final product assembly. This list may include descriptions, part numbers, lead times, quantities per assembly, quantities per end item, and details of the next higher assembly.
Inventory Records:
The inventory records file displays the current status of raw materials and finished products in inventory, including those already ordered or in the production pipeline. This record-keeping is vital for managing the supply chain effectively.
With the help of provided inputs, the MRP system precisely determines the necessary raw materials, components, and subassemblies required for each manufacturing process. This information is documented in primary and secondary reports:
Primary Reports:
Planned Order Schedules: These reports detail the quantity and timing of future orders.
Order Releases: These reports signify the approval for the creation of orders.
Changes to Planned Orders: These reports encompass order cancellations or revisions to quantities and timeframes.
Secondary Reports:
Performance Control Reports: These reports are employed to monitor issues such as missed delivery dates and stock shortages, aiding in the evaluation of system performance.
Planning Reports: These reports serve to predict future inventory requirements.
Exception Reports: These reports are designed to highlight significant problems, such as late orders or excessive scrap rates.
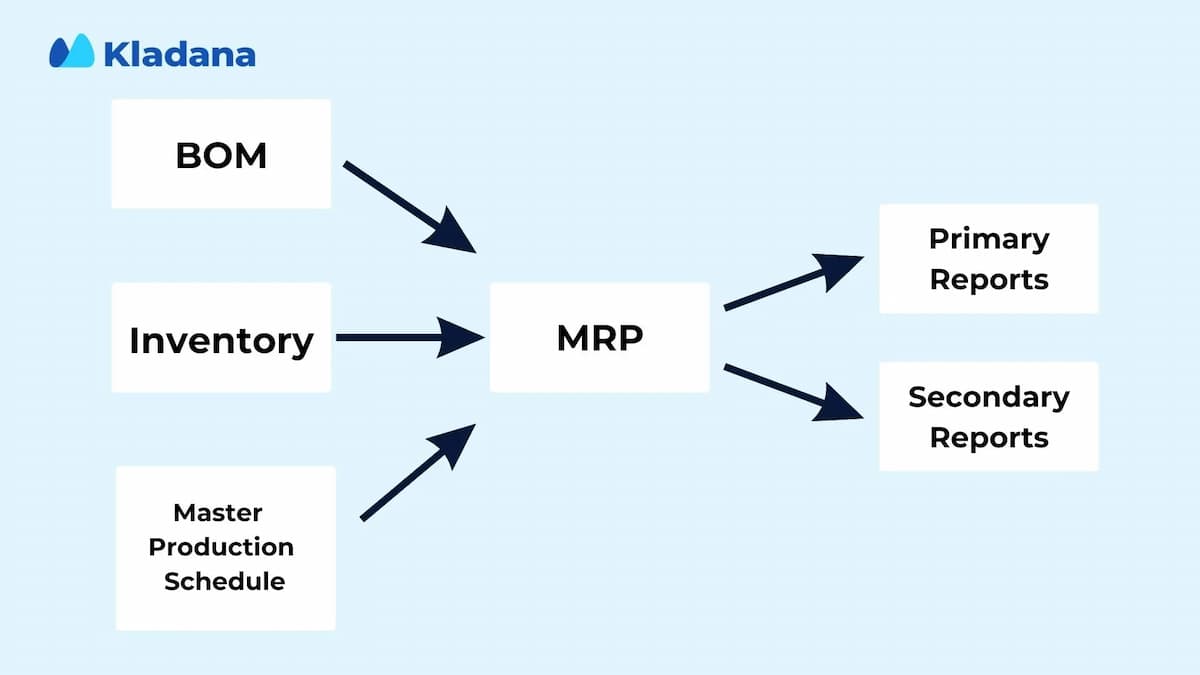
Read‑alikes
Managing Production in a Small Manufacturing Company: Planning, Control, and Profit Calculation
Unicorn Natural Products Manufacturing: a Journey from Spreadsheets to ERP
Cura Pharmaceuticals Manufacturing: Increased Data Accuracy & Business Workflows in 6 Months
What are the Benefits of MRP?
MRP solution is aimed at ensuring the timely availability of materials and components for the production process and maintaining a smooth manufacturing schedule. MRP offers several additional advantages, such as:
➕ Increased labor productivity.
➕ Efficient inventory management and optimization. Businesses can acquire or produce the right quantity and type of inventory, minimizing the risk of stock-outs and their influence on customer satisfaction, sales, and profit, all while avoiding unnecessary inventory expenses.
➕ Enhanced customer satisfaction through reduced lead times.
➕ Lower costs of inventory.
➕ Improved manufacturing efficiency achieved by precise production planning and scheduling, leading to optimal utilization of labor and equipment.
➕ Enhanced competitiveness through more attractive product pricing.
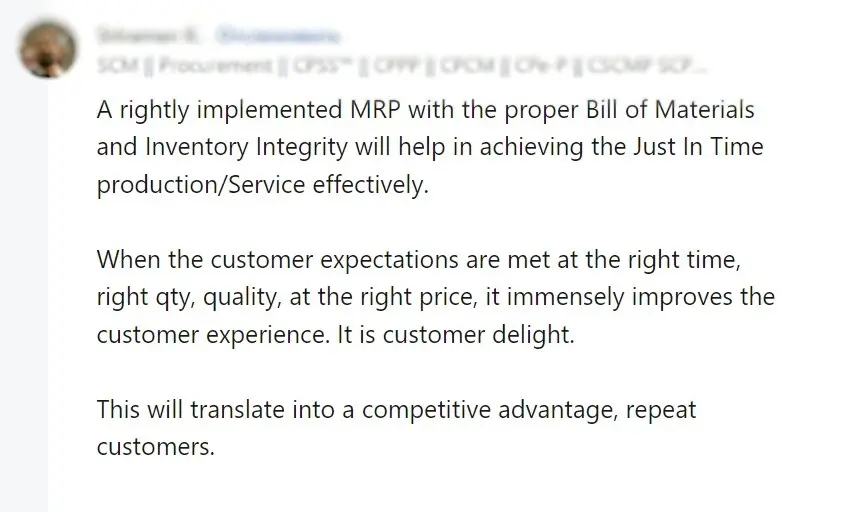
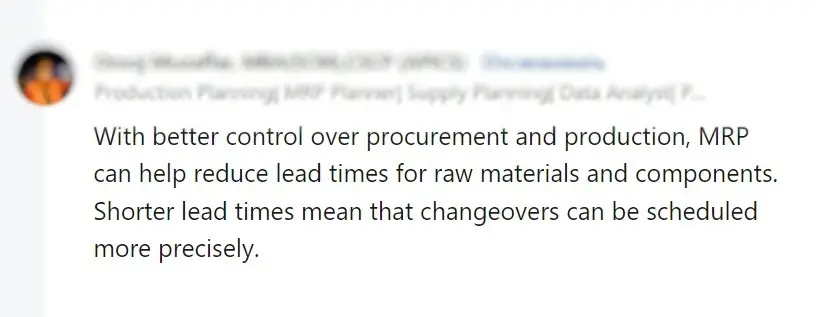
We were searching for software to manage raw materials and finished goods at ease. We tried several solutions but they mainly offered inventory management for those who buy and resell. Kladana turned out to be one of a few software companies that offered necessary features.
Kladana is quite customizable, easy to manage and understand. We can set all the processes up as we like in order to follow our protocols & to simplify the daily routine.
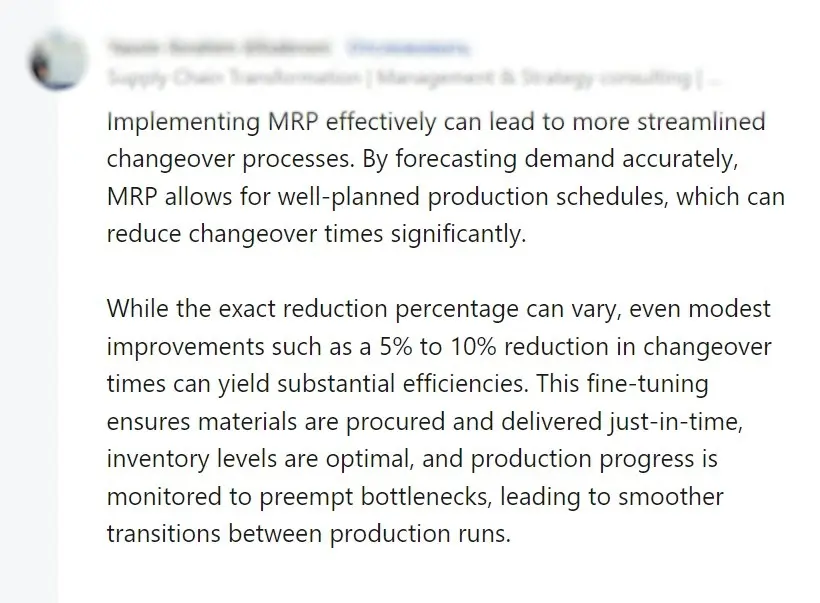
What are the Disadvantages of MRP?
The drawbacks associated with implementing a material requirement planning inventory system are as follows:
➖ Dependency on accurate data input. Any inaccuracies in the data can lead to scheduling delays, incorrect order quantities, and ineffective tracking.
➖ Extensive maintenance of strong databases. Maintaining the system requires the establishment and upkeep of comprehensive databases, which can be a resource-intensive task.
➖ Extended training. Effective utilization of the system demands adequate training for the personnel involved.
➖ Substantial initial costs.
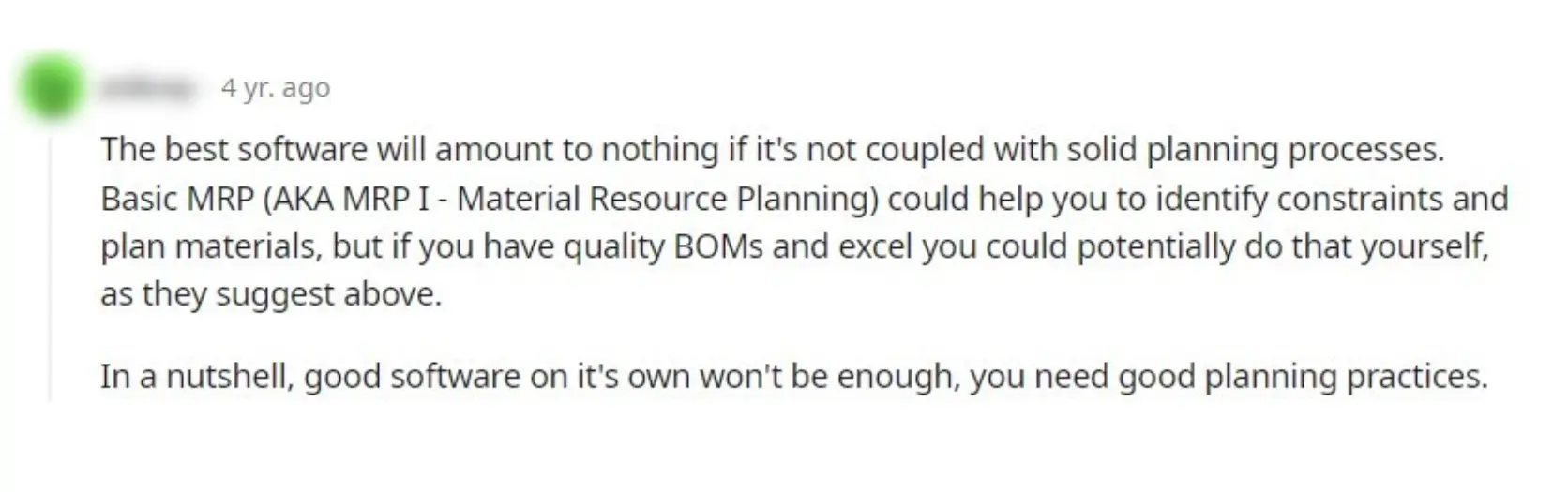
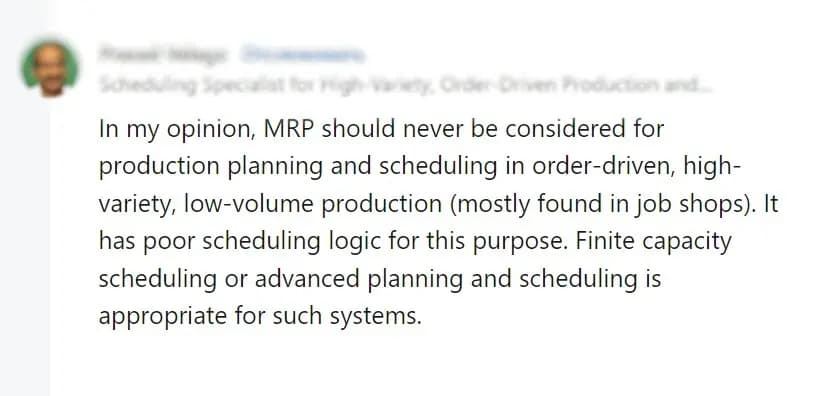
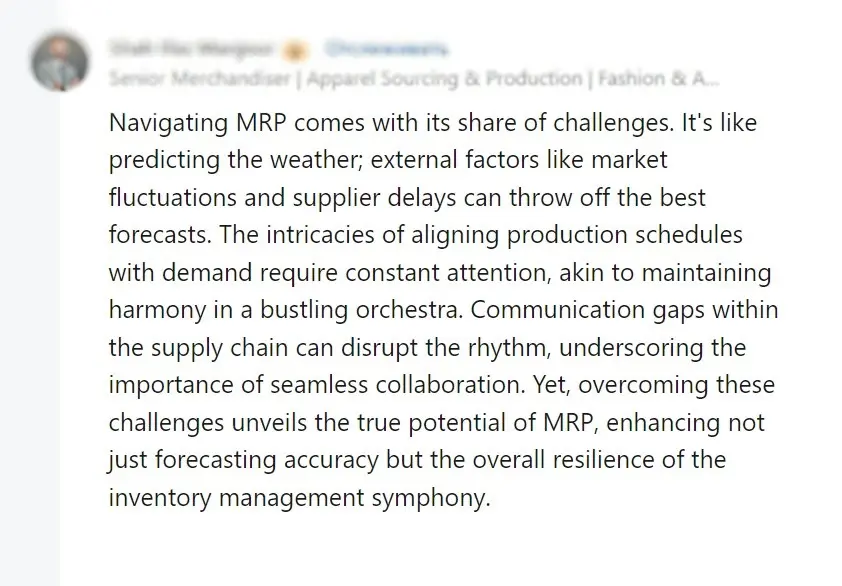
How to Choose between MRP and ERP?
When it comes to production, ERP and MRP systems stand out as the most prevalent inventory management methods. Both of them have their distinctive features. Let’s map out the main differences in the table:
Feature | MRP | ERP |
Functionality |
MRP system is tailored to enhance inventory efficiency by managing manufacturing, scheduling, and procurement |
ERP system consolidates finance, manufacturing, supply chain, procurement, sales, and planning into a unified platform |
Structure |
Operates as a standalone system, focusing intensely on a few specific functions |
An integrated solution, offering a multitude of functions within a single entity |
Integration Possibilities |
Easily integrable with other inventory software |
Not so flexible as MRP, needs complex adjustments |
Check out our article about the ERP systems. Learn about the difficulties and possibilities of their integration with other software, their prices, and prospects.
How to Launch an MRP System?
To successfully start working with the MRP system, you need only several manufacturing indicators. Let’s group them into a table for convenience:
Indicator | Description |
BOM |
MRP system won’t operate without detailed information about components and materials used in manufacturing |
Quantity |
To meet the demand plans and schedules the software needs a precise quantity of products |
Inventory Information |
Everything connected with available materials, work in progress, and finished products should carefully be entered into the system |
Planning Records |
The solution needs all standards and directions connected with labor, techniques, machine use, commands, etc |
Shelf Life |
The time the product can stay at the warehouse is important for planning components of the software |
End Item |
MRP system necessitates that the user defines both the nature of the product being manufactured and its precise level of demand. |
Begin your journey into automated manufacturing management with Kladana: master your inventory and resource allocation, make efficient production plans, and increase your overall profit.
Who Can Use MRP?
It can be surprising, but the term «manufacturer» includes a wide range of organizations. MRP doesn’t just apply to traditional manufacturers but also to any organization that purchases anything that is later transformed into goods or services sold to the customers. Here are some examples:
- Food service companies that use MRPs to manage inventory and supply of ingredients
- Service providers that gather documents, stock and sell devices, consumables, or other items for their customers
- Warehouses that gather different products to be sold as a single set
- Managers of government & office buildings, hospitals, schools, etc, who stock equipment and supplies for future usage
- Warehouses that tailor orders and make personalized order variants, stock primary and supplementary components, and subsequently assemble the final product for shipment.
Now is the period when approximately the same goods at the same prices are sold in one place. It is very complicated to compete in this kind of market environment. Correctly built processes can become an additional competitive advantage.
It’s hard to compete with similar products on the market, but if you optimize processes, you can save on purchases and increase productivity, optimize some costs, monitor the deviations, and analyze, eliminate, and expand bottlenecks. Due to this, you can reduce prices and fight for market share.
What Are the Types of MRP Solutions?
Legacy MRP systems and modern MRP systems are representatives of different technological generations. To put it briefly, modern MRP systems use technological advancements to provide more efficient solutions for managing materials and resources. But let’s take a closer look at the main differences:
Feature | Legacy MRPs | Modern MRPs |
Data Management |
Limited data integration and visibility across different departments |
Seamlessly integrate with other systems (ERP, CRM, etc.) for real-time data |
Interface |
Complex, text-based interfaces that require training to use and to understand them |
Intuitive, user-friendly interfaces with simple graphical dashboards and simple data presentation |
Technology |
Usually use on-premise deployment and store data on hard disks |
Use cloud-based, web-based, or mobile platforms for flexibility |
Operation Speed |
Search for all necessary records on the disk and then start processing the data. That’s why all the processes take a long time and consume a great deal of computing resources |
Process the data very quickly, and can run multiple operations throughout the day |
Inventory Management |
Basic inventory control with possible overstock or stockouts |
Advanced inventory management, reducing costs, and improving order accuracy |
Real-Time Updates |
Lack of real-time data, resulting in outdated information |
Provide real-time updates on inventory, demand, and production statuses |
What Is the History of MRP?
In the early 20th century, MRP began to take shape with new approaches to streamline manufacturing. In 1913, an American production engineer named Ford Whitman Harris created a formula called economic order quantity. It helped minimize the costs of ordering and storing goods. Around the same time, Henry Ford introduced a mass-production system demonstrating the importance of strict control over material flow on assembly lines.
In the 1950s humanity welcomed a new era: the appearance of mainframe computers made it possible to develop custom software. Companies started to create the first software to handle inventory, production, bills of materials, planning, and scheduling.
First MRPs emerged in 1964 as a response to the need for more efficient production and inventory management. Initially, MRP systems were simple, using basic calculations to determine how much material was needed and when.
The next generation of MRP developed in 1980 and known as MRP II, goes beyond just manufacturing planning. It encompasses marketing, finance, accounting, engineering, and human resources.
MRP has evolved from a simple calculation to a comprehensive decision-support system. It provides efficient planning and management for organizations that turn components into products to meet customer demands.
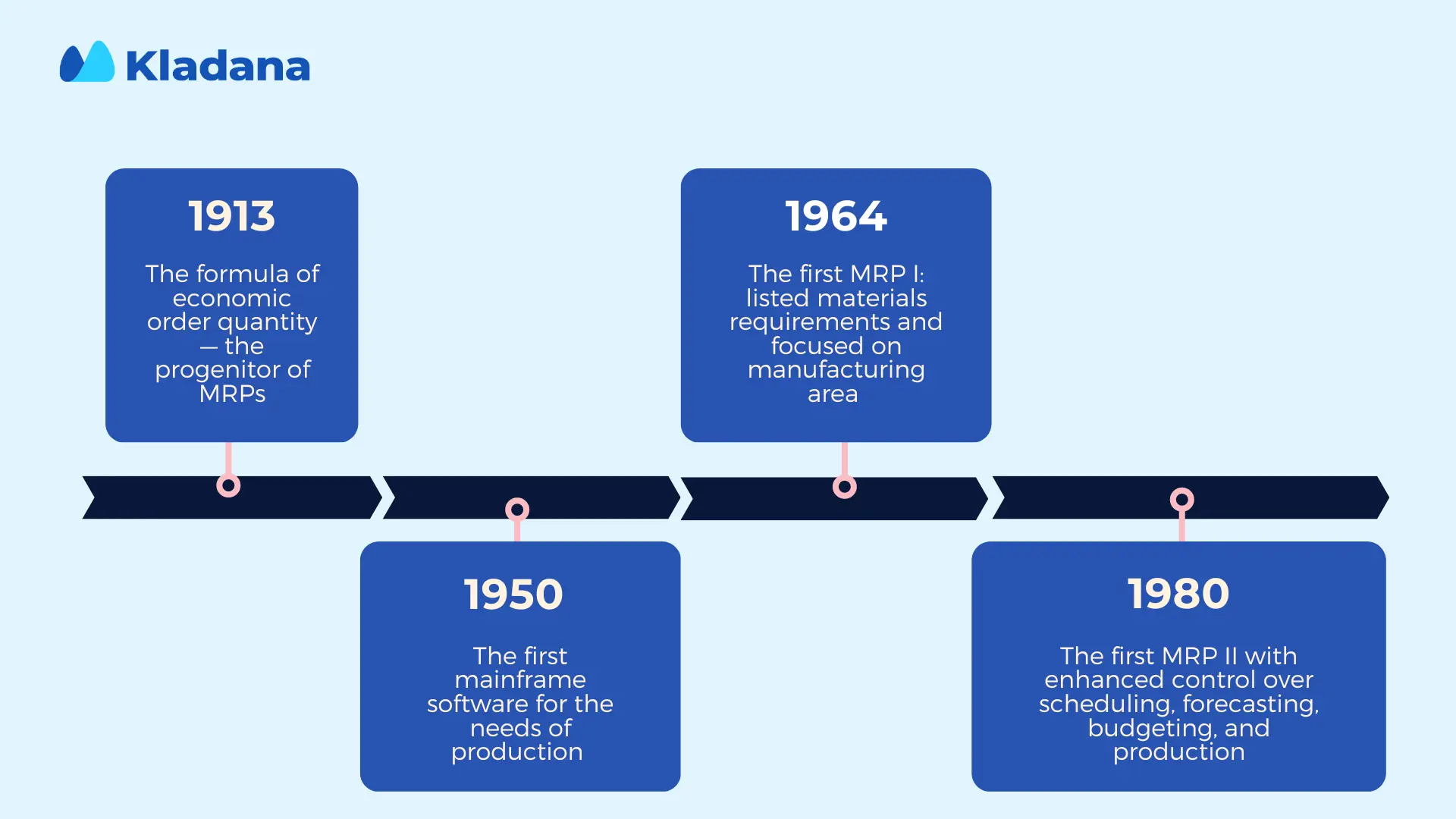
Which Technologies Are Applicable to MRP?
Software engineers never stop improving their MRP solutions to meet the demands of their clients. The use of new technologies is a must today in case you want to keep your product competitive and up-to-date.
Artificial intelligence and machine learning are actively used now to increase planning processes’ accuracy and efficiency. Due to machine learning, the software is capable of tracking the processes and conditions creating more exact models, and giving better recommendations.
In the world of advanced technology, we have a significant innovation called the Industrial Internet of Things (IIoT), also known as Industry 4.0. It refers to the widespread use of various non-household devices, equipment, sensors, and automated process control systems that can monitor and control many aspects all through the whole supply chain. This technology brings a large amount of data into the planning systems that support AI and machine learning.
MRP systems continue to develop new capabilities via cloud deployment. It introduces features like collaboration tools that align with modern work styles. Cloud provides enhanced availability and better security. The systems are now more sustainable due to secure processes of disaster recovery and backup. MRP solutions with cloud deployment now offer faster response time that leads to better performance speed.
Examples of MRP Solutions
Ok, in this paragraph you’ll find brief descriptions of the most popular MRP software vendors. We hope it will help you make the best choice for the efficient management of your production process.
Kladana presents a comprehensive cloud-based ERP solution with a manufacturing module, tailor-made for small and medium-sized enterprises (SMEs). This user-friendly platform helps businesses go digital and automate their operations within a single, unified application.
A 14-day trial period is offered to choose carefully and try the necessary features before buying. For those who have simpler requirements, to begin with, Kladana has a free pricing plan.
New users can master the basics of the application in just 15 minutes. Each client has 1–3 onboarding sessions depending on the plan. The support team responds to inquiries and concerns within 5–15 minutes.
MRP easy has a convenient interface and all the features necessary for a manufacturer: from tracking stock availability to reporting, planning, and forecasting. The solution fits the needs of small manufacturers. However, a few users complained about the worsening of the customer service a couple of months after the registration.
ERPAG is a cloud-based solution suitable either for small or big enterprises. It’s easy to use yet very powerful. It can also work with popular tools like Shopify, QuickBooks, Xero, and WooCommerce. ERPAG also has integrated CRM and sales modules.
Acumatica is a cloud-based MRP solution for SMEs that helps to satisfy the needs of the enterprise by offering features like financial management, reporting, business analytics, and more. Most of the users mark it as a scalable solution with a reasonable price.
Katana MRP offers smart features to enhance control over business processes: automated resource distribution, automatic inventory adjustments, etc. Users are satisfied with the excellent work of the customer support team and mention that sometimes Katana accepts and introduces the development suggested by clients.
Epicor Software is known as one of the most flexible solutions tailored to coping with complex manufacturing tasks. It is good at predicting demand parameters and managing distribution and fulfillment processes. Some users complain about high prices and long educational stages.
Genius ERP is a complex solution with a strong MRP module with a long history: it was established over 25 years ago. It offers powerful features good for SMEs. It can convert CAD designs into BOMS. Sometimes users notice that the software is slow in operation.
Oracle NetSuite is a complex MRP solution with an abundance of features the manufacturer can successfully use and adjust to his own needs. It operates with strong intelligence tools, manages and controls inventories and production with automatic status updates, and has convenient forecasting features. The only drawback constantly mentioned by the users is the solution’s price.
DelmiaWorks, earlier known as IQMS, is an affordable yet rather scalable cloud-based solution that grows together with the enterprise. It offers a variety of business intelligence tools and informative graphic reports. The solution is also famous for its constant innovations based on the requirements of the users.
JobBOSS is remarkable for its flexibility. It is an affordable and manageable MRP cloud-based or on-premise software good for SMEs’ manufacturing needs. Has strong accounting features and helps to predict the results of «what if» scenarios.
If you want to get acquainted with popular production management software, read our compilation article with examples of the 23 best solutions, and a description of their functions, advantages, and disadvantages.
Frequently Asked Questions on MRP Solutions
Below, we describe the elements, methods, and challenges of MRP. Additionally, we explain the differences between MRP and ERP, as well as MRP and BoM.
What does MRP mean?
MRP stands for Material Requirements Planning, a system used by businesses to ensure they have the right materials and products in the right quantity at the right time, minimizing inventory levels and production costs.
What are the MRP elements?
The key elements of MRP include the Bill of Materials (BOM), inventory status records, and the master production schedule (MPS). These elements work together to provide a comprehensive plan for material procurement and production scheduling.
What are the 3 basic steps of MRP?
- Identifying the requirements: Determining what materials are needed and in what quantities;
- Scheduling production: Planning when and in what order parts should be produced or purchased;
- Managing inventory levels: Keeping inventory at optimal levels to meet production schedules while minimizing holding costs.
What are the methods of MRP?
The methods of MRP typically involve demand‑based planning, where production and purchase orders are driven by forecasted or actual customer demand, and time‑phased order planning, which schedules orders based on the lead times for production and delivery.
What are the challenges of MRP?
Challenges of MRP include accurate demand forecasting, maintaining up‑to‑date and accurate inventory records, managing changes in production schedules, and ensuring the Bill of Materials is current and accurate. Additionally, integrating MRP systems with other business processes can be complex.
What is MRP vs ERP?
MRP focuses specifically on the planning and management of materials and inventory for manufacturing, while ERP encompasses a broader range of business processes, including finance, HR, sales, and more, integrating them into a single unified system.
What is the difference between BOM and MRP?
The Bill of Materials (BOM) is a detailed list of parts, items, assemblies, and other materials required to create a product, along with instructions for how to assemble the product. MRP, on the other hand, is a planning system that uses information from the BOM, along with inventory data and the master production schedule, to calculate materials requirements and plan production and purchasing activities.