ERP for Chemical Manufacturing
Control the entire chemical production cycle — from formulation management to finished goods shipment
- BOMs with custom processes and formulation & recipe management for chemical production
- Batch tracking and shelf‑life monitoring for raw materials & finished goods, including FIFO & FEFO inventory methods
- By‑products, reusable items, and production waste (e.g., evaporation, spills, equipment cleaning) tracking for better cost control
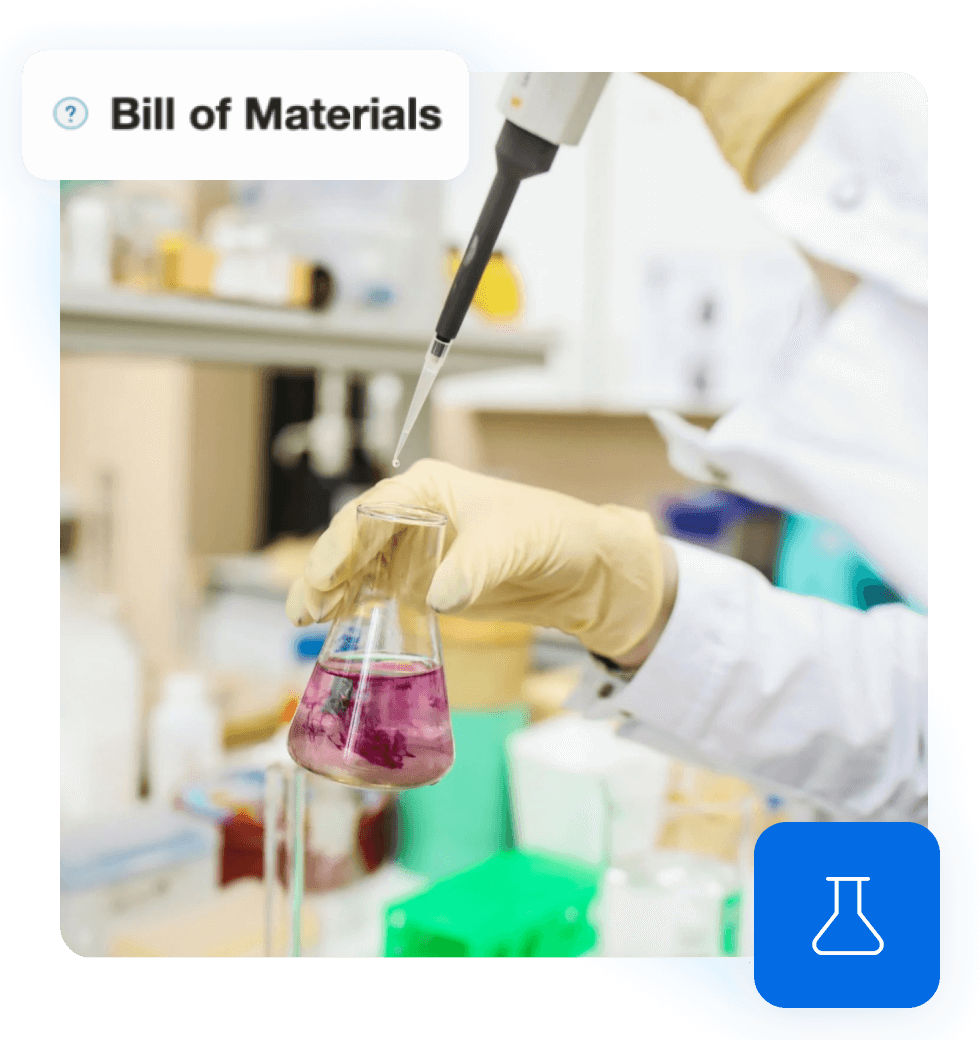
Chemical Manufacturing ERP for Production Planning
- Create BOMs with flexible formulation & recipe management, and set up custom routing sequences for paints, fertilizers, and cleaning agents:
Mixing & Blending → Milling/Dispersion → Quality Control & Lab Testing → Packaging - Use ultra‑small unit measurements in BOMs for precise formulations
- Estimate production costs based on BOMs before production scheduling
- Raw materials sourcing (e.g. pigments, resins, solvents, additives, fillers) — stock materials or purchase for specific production orders
- Supports MTO (Make‑to‑Order) & MTS (Make‑to‑Stock) manufacturing methods
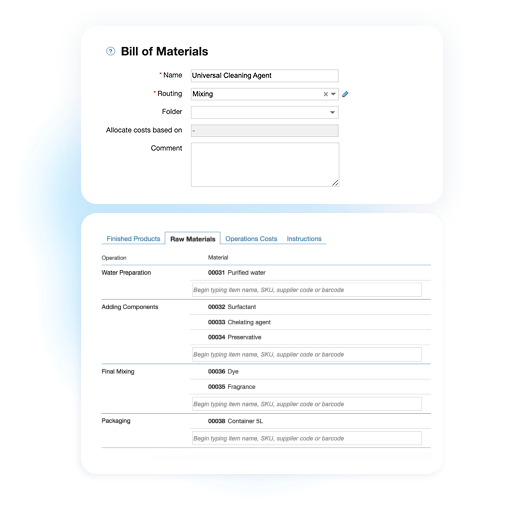
ERP for Chemical Industry with Production Execution
- Step‑by‑step operation tracking: mixing, filling, blending, dispersion, etc.
- Job task assignments and in‑house production tracking
- Special instructions for each manufacturing stage available for shop floor workers
- Assign subcontractors as stage performers and track reconciliations
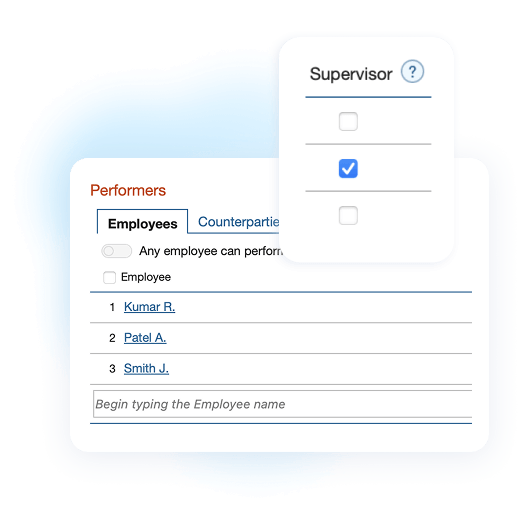
Inventory Management in Chemical ERP
- Batch tracking and expiry date control with shelf‑life monitoring
- Organize inventory using different packaging formats: containers, drums, bags, tanks
- Set reorder point alerts for raw materials & finished goods
- Safety stock management available

Sales & CRM for Chemical Manufacturers
- Order processing & fulfillment with support for packaging formats and labeling
- FEFO/FIFO‑based dispatch logic to ensure proper stock rotation
- Link sales orders with specific production orders for accurate batch tracking
- CRM integrations (HubSpot, Salesforce) for customer follow‑ups
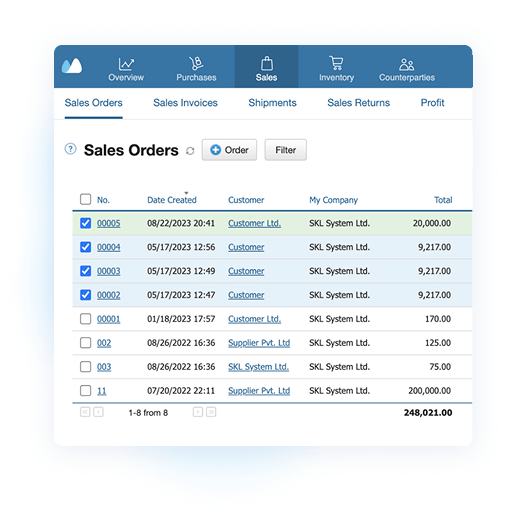
Cost Tracking & Financial Reporting in ERP for Chemical Industry
- Estimate costs before production scheduling and calculate unit costs after production completion
- Track waste, evaporation, and scrap costs
- Allocate costs for by‑products and co‑products
- Generate financial reports on revenue, losses, and employee performance
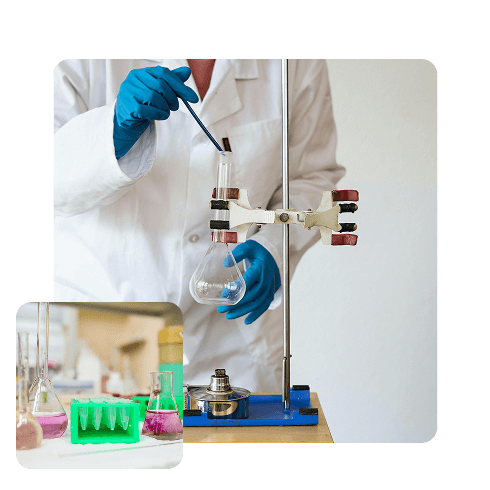
Chemical ERP with Manufacturing & Business Reports
- Monitor stock movements with batch tracking and expiry dates alerts
- Monitor production progress by operation (e.g., milling, blending) and finished goods output
- Conduct plan-fact analysis for materials, WIP, and costs

Comprehensive ERP for the Chemical Industry
14‑day trial, free plan available, $60/year for basic features, and $563/year for the plan with the manufacturing module. Monthly payments accepted
Integrations with third‑party CRM, e‑commerce, accounting, and delivery platforms such as Shopify, Zoho Books, HubSpot, and more, plus an API for custom integrations
1–3 onboarding sessions and free support with response times of 5–15 minutes. Help Center articles and YouTube tutorials for self‑guided learning
Cloud hosting, data encryption & backup, and customizable access permissions for different user roles
Success Stories from Chemical Manufacturers
FAQ on ERP for Chemical Industry
A chemical manufacturing ERP is a software solution designed to manage production planning, inventory tracking, quality control, and cost management. It helps manufacturers streamline formulation management, batch tracking, and order processing.
Chemical ERP systems provide BOMs with formulation management, allowing businesses to create and store custom formulas and recipes. Users can adjust ingredient proportions, track revisions, and ensure consistency across batches.
Yes, batch tracking is a core feature. The system monitors raw materials and finished goods using FIFO (First‑In, First‑Out) and FEFO (First‑Expired, First‑Out) methods, ensuring products are used or sold before expiry.
Yes, the system records scrap, waste, evaporation losses, and by‑products at different production stages. By‑product and co‑product cost allocation features help in financial tracking.
The ERP allows cost estimation before production scheduling and tracks actual costs per batch, including raw materials, labour, waste, and packaging. Financial reports provide insights into profitability, operational efficiency, and cost variances.
The ERP enables batch‑based inventory tracking, allowing businesses to organize stock by containers, drums, tanks, or bags. It also provides real‑time stock updates, reorder alerts, and safety stock management.
Yes, Kladana Chemical ERP integrates with CRM tools like HubSpot and Salesforce to manage customer interactions, sales orders, and follow‑ups. It also links sales orders to production batches for accurate tracking.
Yes, subcontractors can be assigned to specific production stages, with cost tracking and reconciliations for outsourced processes like blending, filling, or packaging.
The system analyzes historical sales and production data to predict future demand, ensuring optimal stock levels, raw material procurement planning, and reduced stockouts or overproduction.
Learn how to arrange business routines for manufacturing, wholesale, retail & e‑commerce