Using Kladana, we managed to streamline the manufacturing management in whole: production operations became smoother, raw materials planning & purchasing became much easier. Now, a purchasing manager can look at one screen In Kladana, access sales estimates, figure out how many raw materials need to be bought for different items, and make purchase orders straightaway.
Food ERP for Small Manufacturers
ERP Software for Food Industry
- Track inventory: ingredients, finished products, and WIP in one system
- Streamline production: schedule orders and monitor progress
- Determine unit costs for spices, dairy, pulses, and more
- Get alerts for perishable items and prevent product expiration
- Sync all sales channels: manage wholesale, retail, and e‑commerce orders in real time
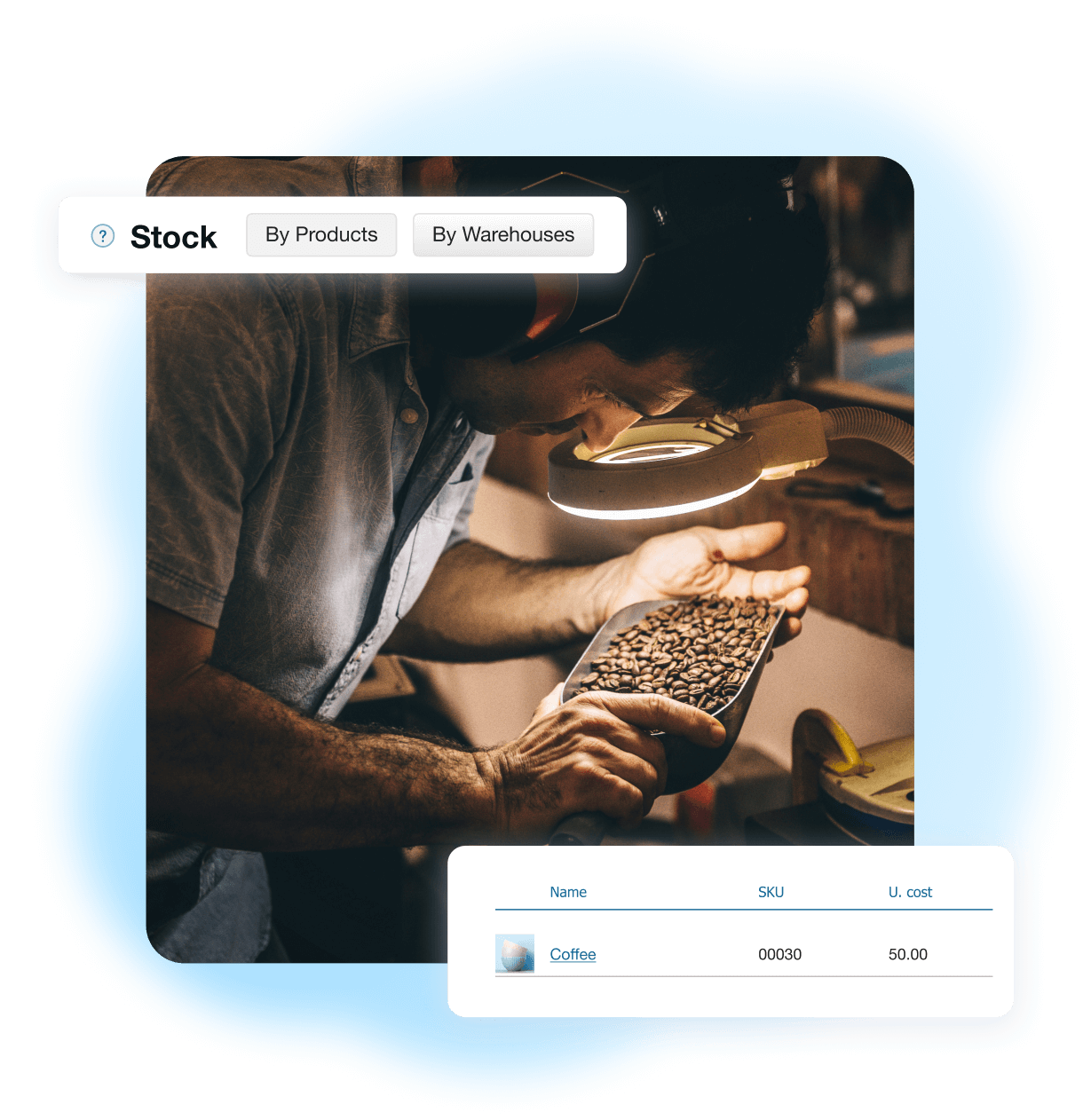
Food ERP for Inventory and Purchasing
- Track Ingredients & Finished Goods
Manage perishable inventory with batch processing and lot tracking. Set up variants for shapes, types, and flavours with flexible pricing - Reorder Alerts & Stock Management
Define minimum stock levels and receive low‑stock alerts before running out - Supplier Management & Purchasing
Inspect raw material quality upon receiving. Track ingredient sourcing, supplier performance, and price fluctuations - Shelf‑Life & Expiry Management
Monitor expiration dates to schedule timely write‑offs and reduce waste
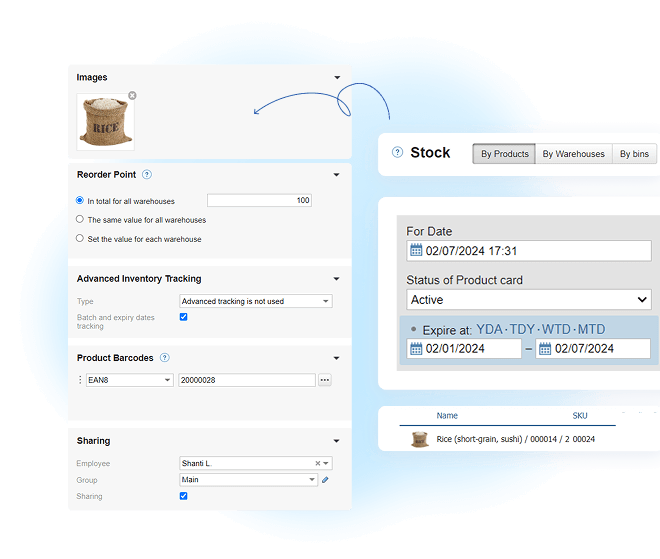
Efficient Food & Beverage Production with ERP
- Multi‑Level BOM Management
Standardize ingredients, portions, and operation & labor costs for food manufacturing - Production Planning and Scheduling
Plan batch processing and partial production, monitor quality control, and optimize workflows - Food Waste Reduction & Cost Control
Track scrap, by‑products (husk, peel), and process efficiency to minimize waste - Shop Floor Control
Workers mark tasks as complete using the Shop Floor App. Managers can assign tasks and track total earnings in real time - Finished Products Pricing
Use the unit cost calculator to determine wholesale and retail prices for finished goods
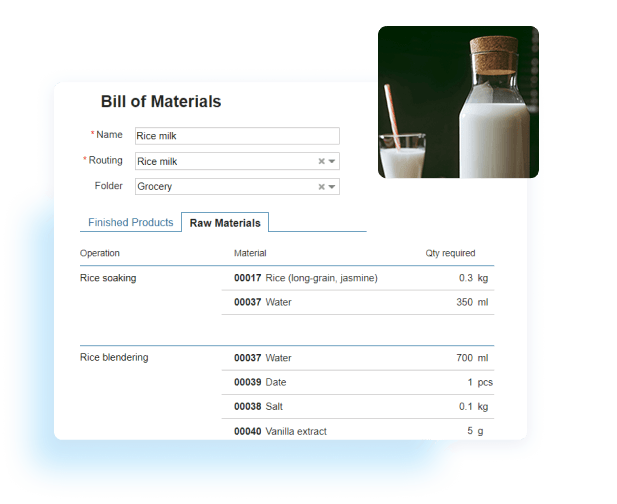
Talk to our Expert
and answer your questions
Food ERP for Sales & Order Processing
- Multi‑Channel Sales Management
Handle orders from wholesale and retail customers in one system - E‑commerce Integrations
Sync stock and orders with Shopify, WooCommerce, or other platforms - Manage Order Fulfillment
Track shipments, returns, and overdue invoices with real‑time updates - Dynamic Pricing & Discounts
Offer bulk order discounts, and custom pricing for key customers - Sell Manufactured Products directly to Customers
Use Online Order App to send customers online catalogues with tailored pricing, receive new orders directly in Kladana, and manage sales reps and track their performance
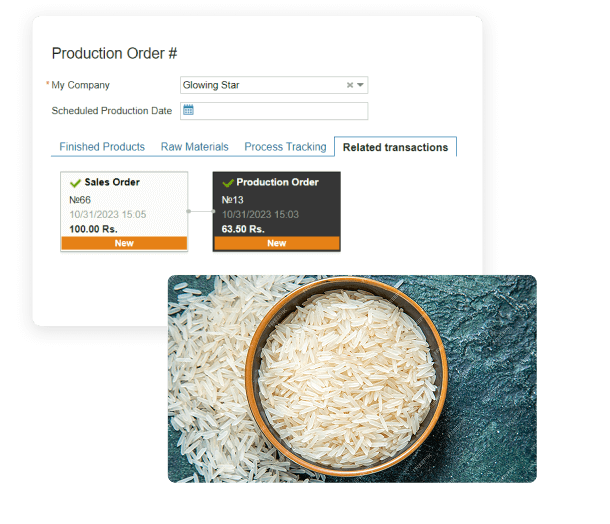
Food ERP with Advanced Analytics & Reporting
- Real‑Time Profitability Insights
Track profit margins, revenue, and average check values for better financial control - Demand Forecasting
Identify best‑selling products and optimize purchasing based on sales order trends - Employee Performance
Reward top‑performing employees who drive profits or boost production efficiency
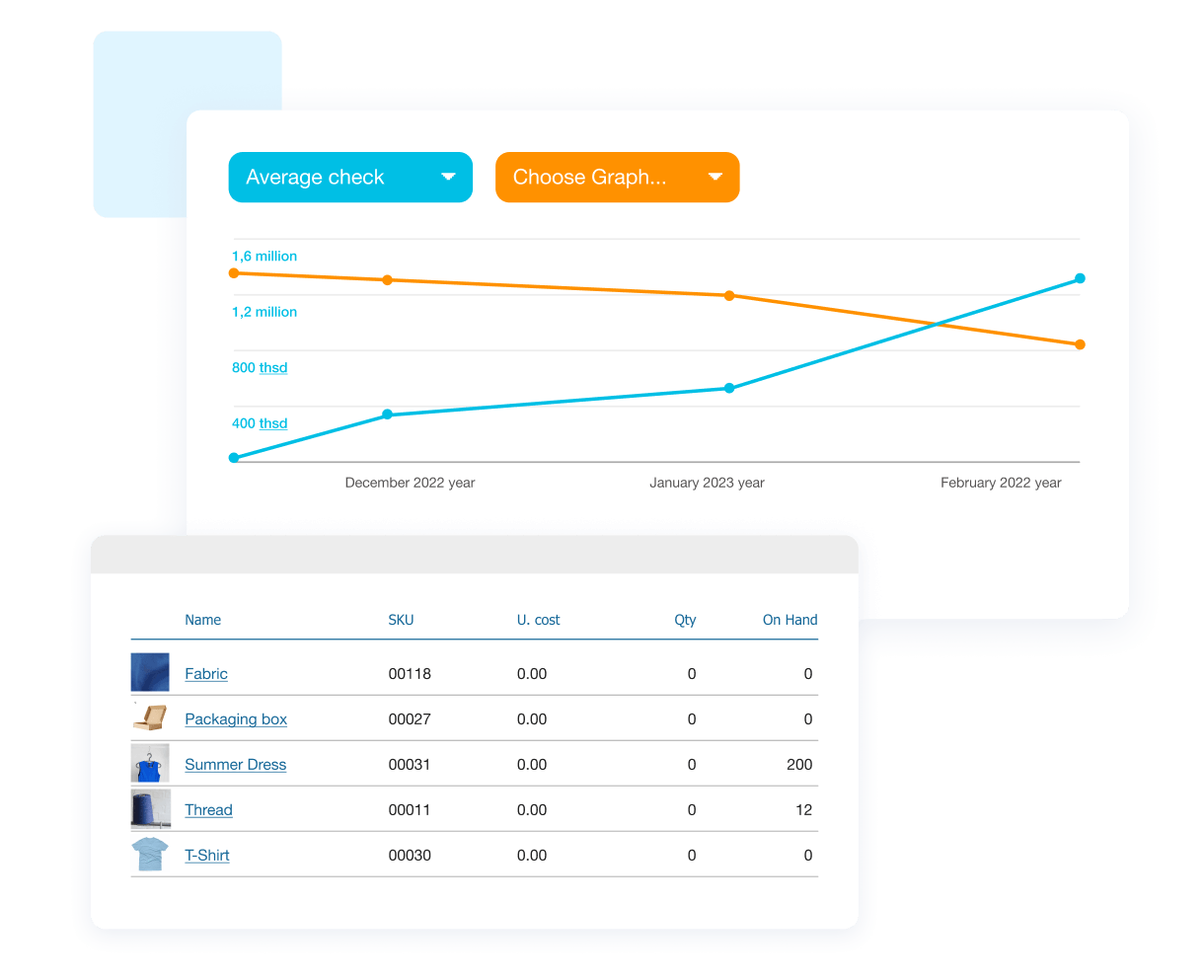
Automate your Small Business with
Kladana Food and Beverage ERP
Get Your 14‑Day Free Trial
Food ERP Success Stories: How Manufacturers
Transformed Their Businesses
Before Kladana, we were doing everything in Excel. All the stock and production records were maintained in spreadsheets. We weren’t able to arrange timely updates for the information about warehouse stocks: the materials we were receiving, the goods we were shipping.
In Kladana, we found the functionality we were looking for. In combination with affordability, it worked as a decisive factor. Another important area is tracking the amount of yield our company is getting. In this respect Kladana is suitable to our requirements, and we are going to start using the Financials module of the solution.
In Kladana we process sales orders, make sales invoices in pdf, and manage shipments. All bills of materials are stored in the software. All production stages are reflected in Kladana.
We have three warehouses: one for raw materials, one for production, and one for finished goods. We add the purchased materials to Inventory in Kladana, and the raw materials are transferred to production. In production, they are processed in a production order. Then the finished goods appear in another warehouse. Thus, 1,500 bottles are moved from one warehouse to another in a couple of clicks.
User‑Friendly Food and Beverage
ERP Software
Our expert will onboard you within 1–3 sessions, help to adjust all the important settings, and answer your questions
Get help within 5–15 minutes from our support team
Access our Help Center articles and YouTube tutorials
FAQ on ERP for the Food & Beverage Industry
Let’s review the most relevant user queries.
General Questions about Food ERP
Questions about Inventory Management and Purchasing in Food ERP
Easily manage product variations in food ERP:
- Open the product card → Click +Variant → Add the attribute (flavour).
- You can also add other attributes like shape or type to customize product details.
Questions about Production Planning & Execution in Food Manufacturing ERP
Yes! Here’s how:
- Create a product card for a ground coffee pack with different variants (grind levels).
- Set up a BOM for the coffee pack.
- When starting a production order, specify how many packs of each grind level will be produced in the Variance column.
Unfortunately, Kladana doesn’t have a dedicated menu planning feature. However:
- When creating & scheduling a production order, you can attach a file (e.g., PDF menu plan)
- Add notes in the «Add some notes» field for reference.
Questions about Food ERP Software for Sales, Payroll & Cost Management
The food production management software automatically calculates:
- Raw material costs (ingredients, packaging, waste)
- Production costs (equipment, labour, utilities)
- Distribution & logistics costs (storage, transport, fulfillment)
- Create product cards for finished goods and all raw materials.
- Input purchase prices for each material.
- Set up a BOM for the finished item, including operation and labour costs.
- When you create a production order, the system automatically calculates total and unit costs.
Yes! Our food ERP software supports:
- Bulk discounts — offer special rates for large orders.
- Customer‑segmented pricing — Assign different price levels for wholesale and retail clients.
- Bulk price updates — Easily adjust multiple prices at once.
Learn how to arrange business routines for manufacturing, wholesale, retail & e‑commerce