Using Kladana, we managed to streamline the manufacturing management in whole: production operations became smoother, raw materials planning & purchasing became much easier. Now, a purchasing manager can look at one screen In Kladana, access sales estimates, figure out how many raw materials need to be bought for different items, and make purchase orders straightaway.
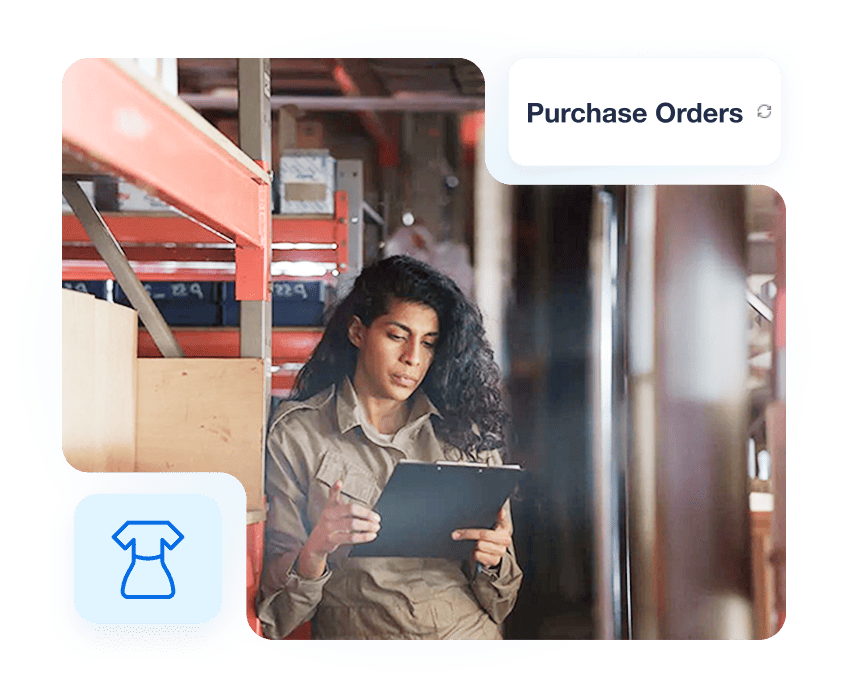
Avoid Overstocking
Order only the required quantity of products and raw materials by leveraging sales analytics and demand forecasting
Prevent Stockouts
Receive notifications when stock levels are low and reach the reorder point
Track Stock Movements
Monitor all stages: expected delivery, available in the warehouse, reserved for an order, and shipped
Manage Purchasing Seamlessly
Record operations, assign tasks, and enable cross-divisional collaboration
Flexible Purchasing Workflows
First, define your products, quantities, timing, and suppliers, then set up purchasing rules and operations. Kladana supports multiple procurement scenarios
Purchases Based on Sales or Production Orders
- Track the statuses of purchase orders linked to relevant sales or production orders
- Assign corresponding tasks to employees
Purchases When Stock Levels Reach the Minimum Threshold
- Set up reorder points to receive notifications when stock levels are low
- Use the purchasing management report to identify how many days items typically stay in stock and determine the optimal order quantity
- Create internal orders for cross-divisional collaboration and manage transfers for moving stock between warehouses
Regular Purchases with a Certain Frequency
- Replenish particular product range, schedule orders on Mondays, or on 15th day of each month according to contract terms with a supplier
- Implement workflows to automate the creation of documents and task assignments
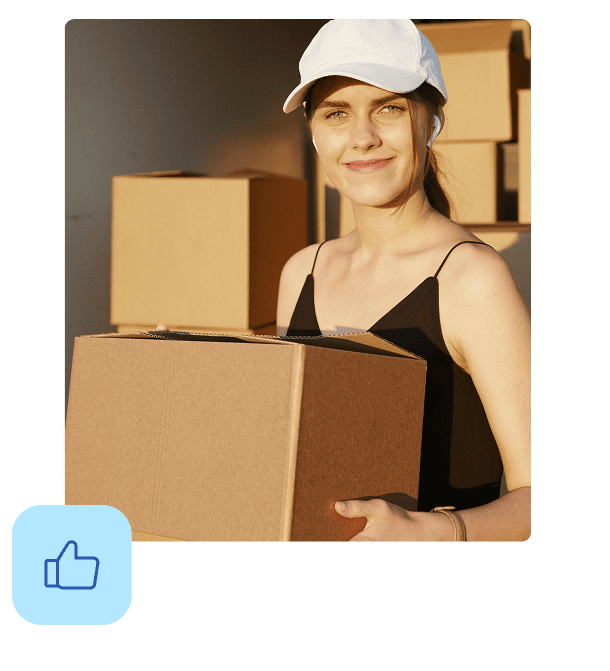
Use Purchase Management
Module Efficiently
Manage Purchase Orders and Operations
- Run purchase orders and track their statuses: Monitor orders through stages such as new, expected, received, and canceled
- Manage financials: Handle supplier invoices, incoming payments, overdue invoices, and purchase returns
- Manage receivings: Conduct quantity and quality checking
- Manage warehousing: Use storage bins and batch tracking
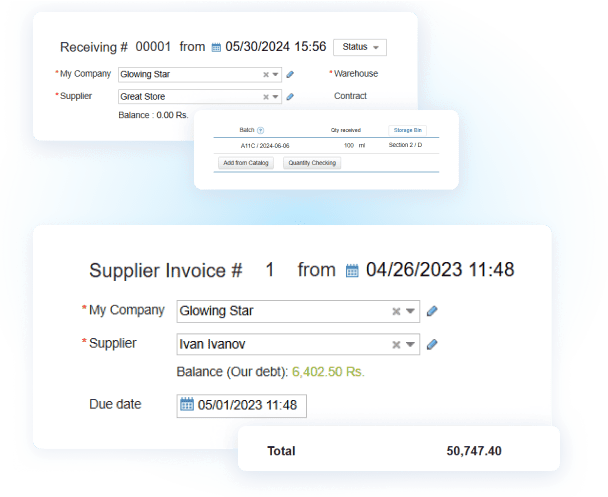
Analyze Sales and Purchasing
- Use Purchasing Management report: Control purchases by sales, and by raw material consumption
- Analyze sales: Monitor daily, weekly, or monthly volumes, and overall profit and loss
- Use demand forecasting: Consider average sales and best‑selling items to anticipate needs
- Monitor stock levels: Keep track of in‑transit stock, reserved stock, and stockpile
- Use stock and stock movement reports: Monitor all transactions and ensure timely stock replenishment
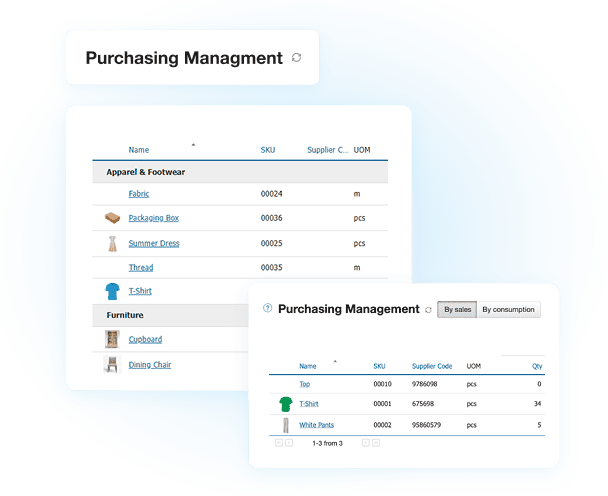
Automate and Customize Purchasing
- Set up access rights and approval processes: Ensure smooth management and data protection
- Create internal orders: Facilitate stock replenishment efficiently
- Configure workflows: Automate actions triggered by specific events, such as automatically allocating stock when a purchase order is created
- Link purchase orders with relevant employee tasks and documents, such as supplier invoices or outgoing payments
- Connect purchase orders with relevant production orders, internal orders, or warehouse operations such as receiving
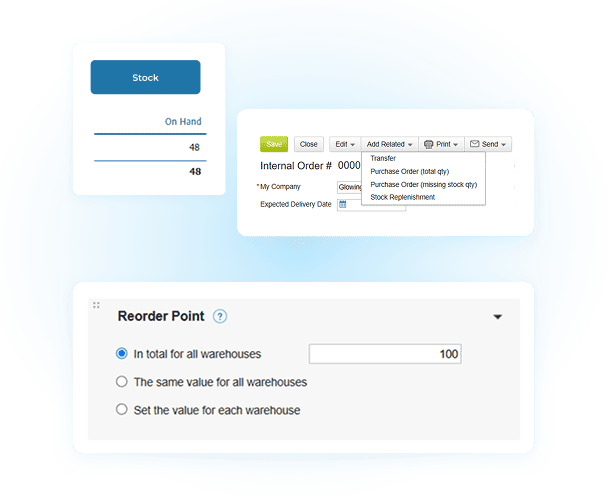
Efficient Supplier Management
- Maintain supplier profiles, including shipping information, contact persons, and provided discounts
- Categorize suppliers into groups, such as regulars and new ones
- Analyze interactions with suppliers: transactions, profitability, and relevant tasks
- Select preferred suppliers
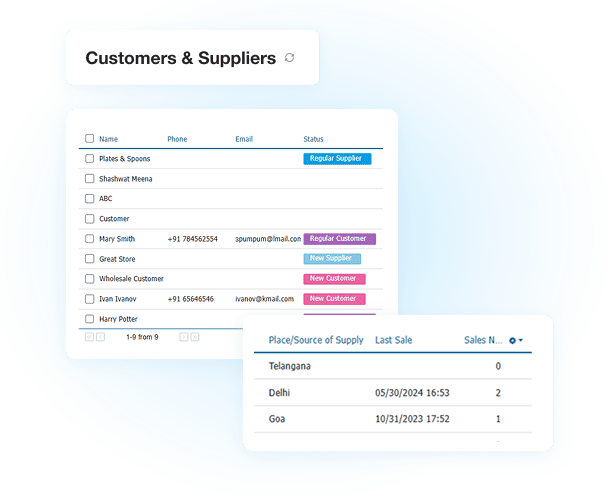
ERP with the Purchase Module
Designed for SMEs
- Control current stock levels, including stock on hand, committed, and in transit
- Manage supplier workflow: delivery lead times, payment conditions, and
minimum purchase order quantities - Link purchase orders with receivings
- Analyze the profitability and turnover of each item to purchase the most cost-effective ones
- Use advanced sales analytics to forecast demand and ensure timely supplies
- Receive alerts when stock levels are low
- Manage purchase orders to ensure sufficient raw materials for new production orders
- Use the purchase management report to plan purchase orders based on sales, and raw material consumption
- Automatically create purchase orders based on production orders and track their statuses
- Create stock replenishment directly from sales orders
Kladana ERP for Your E‑Commerce & D2C Business
14-day trial, free plan available, $60/year for basic features, and $563/year for the plan with the manufacturing module
Integrations with third-party platforms like WooCommerce & Shopify, Kladana Online Order App for direct sales without a website, and API available
1–3 onboarding sessions based on the selected plan, with free support via live chat, email, or form submission for all paid plans, responding in 5–15 minutes
Fashion, food, cosmetics, electronics, plastics, furniture, and more
Manage sales in one app: control stock levels, transfer goods to marketplaces, update prices and product variants, and synchronize orders seamlessly
Monitor actual profit per order, sales channel, and overall company performance. Get precise information on earnings, expenses, and restocking needs
Case Studies
Using Kladana’s Purchase module, we monitor raw material stock levels and plan purchases based on available and reserved stock. Planning starts two months in advance: in October, we order raw materials for December. This timeframe is typical for our business — suppliers need time to prepare shipments, while we are to produce goods and send them to marketplaces.
In Kladana, we manage sales, production, inventory, and purchasing. Previously, we guessed stock levels and often faced situations where we needed to ship a product, but didn’t have it in stock. Now, we always see up-to-date data in the marketplace warehouses.
Using the Purchase module, it’s convenient to monitor the stock levels of raw materials and components, plan purchases, and create purchase orders directly from production orders.
In Kladana ERP, we create BOMs and manage production orders. We record the actual quantity of finished products and assign batch numbers.We also create purchase orders for suppliers very quickly. Previously, it took 15–20 minutes, now it takes just a minute. The required amount of raw materials is calculated based on the process sheets. We can also see the status of orders: which ones have arrived and which haven’t. We sell our products on marketplaces. Using Kladana, we control the actual stock levels.
FAQ on Purchase Management
Purchase Module in Kladana ERP
Purchase Orders and Stock Control
Payments and Warehousing
Learn how to arrange business routines for manufacturing, wholesale, retail & e‑commerce